The future is now
Written by
25 February 2021
•
4 min read
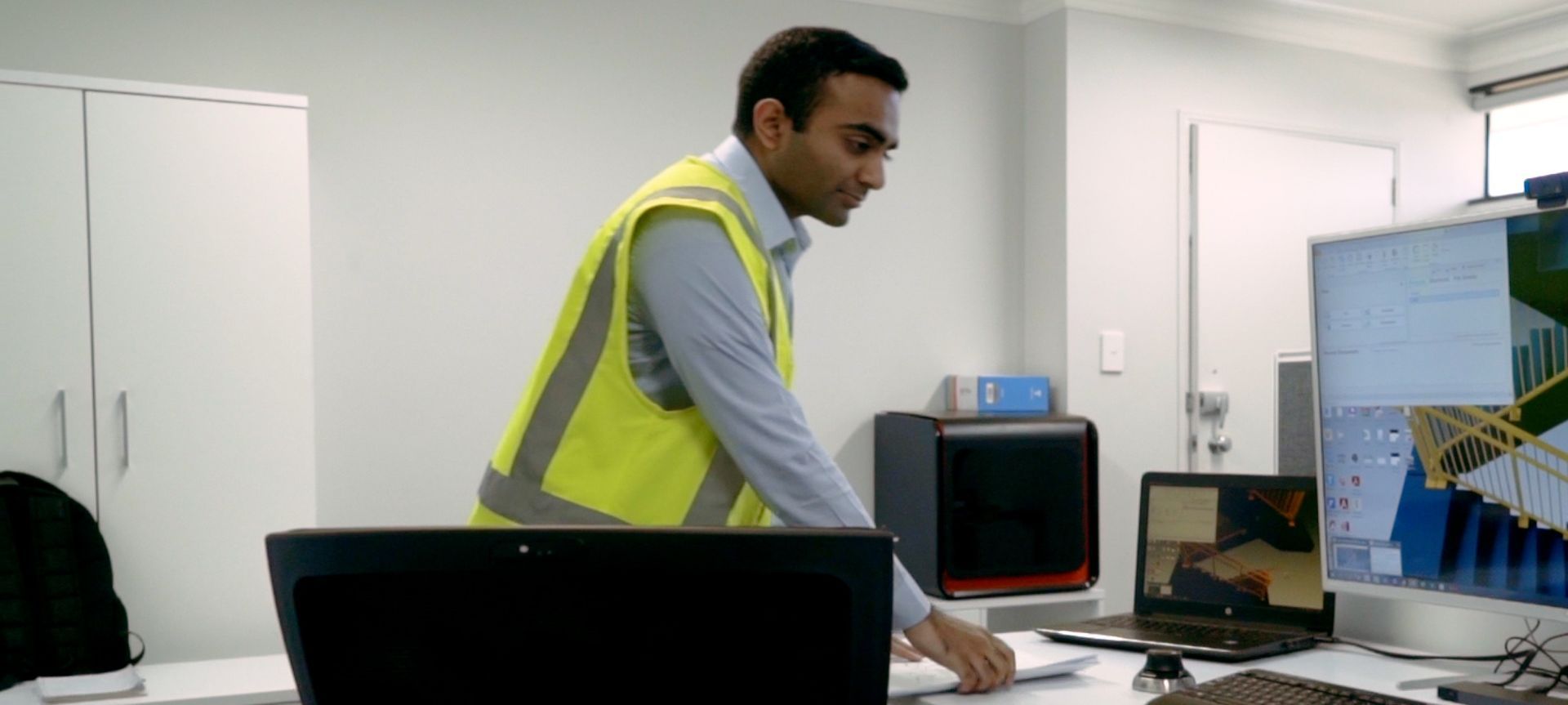
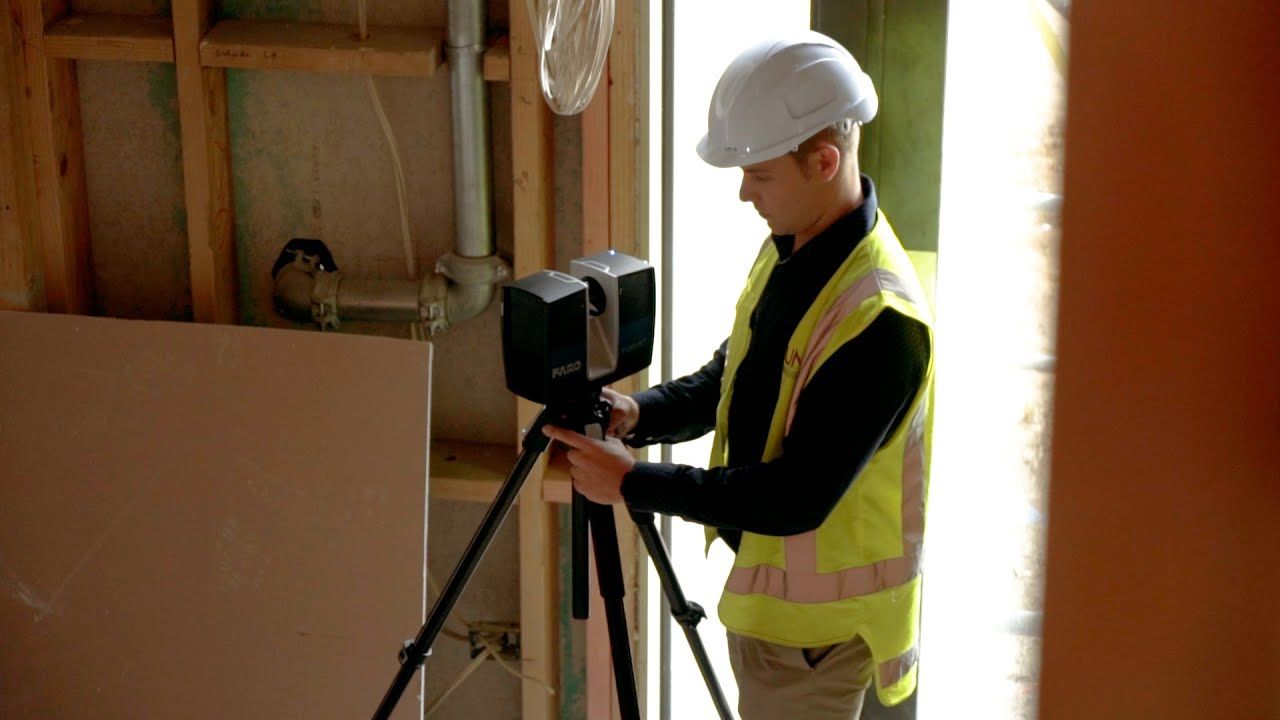
In 1917, everyone’s favourite theoretical physicist, Albert Einstein, established the theoretical foundations for the laser but it would be another four decades before American engineer and physicist, Theodore Maiman, successfully demonstrated the first functioning laser.
In the sixty years since, laser technology has been adapted into just about every facet of society from the humble barcode scanner through to tactical high-energy weapons. One area in which laser technology has produced wide-ranging benefits, is in 3D object scanning, especially in the construction sector.
“Spatial scanning in this manner is a game-changer,” says Kevin Degutis, Sales and Marketing Manager for Unex. “3D scanning has allowed us to greatly increase our offering to clients, as well as pass on a number of efficiencies to them.”
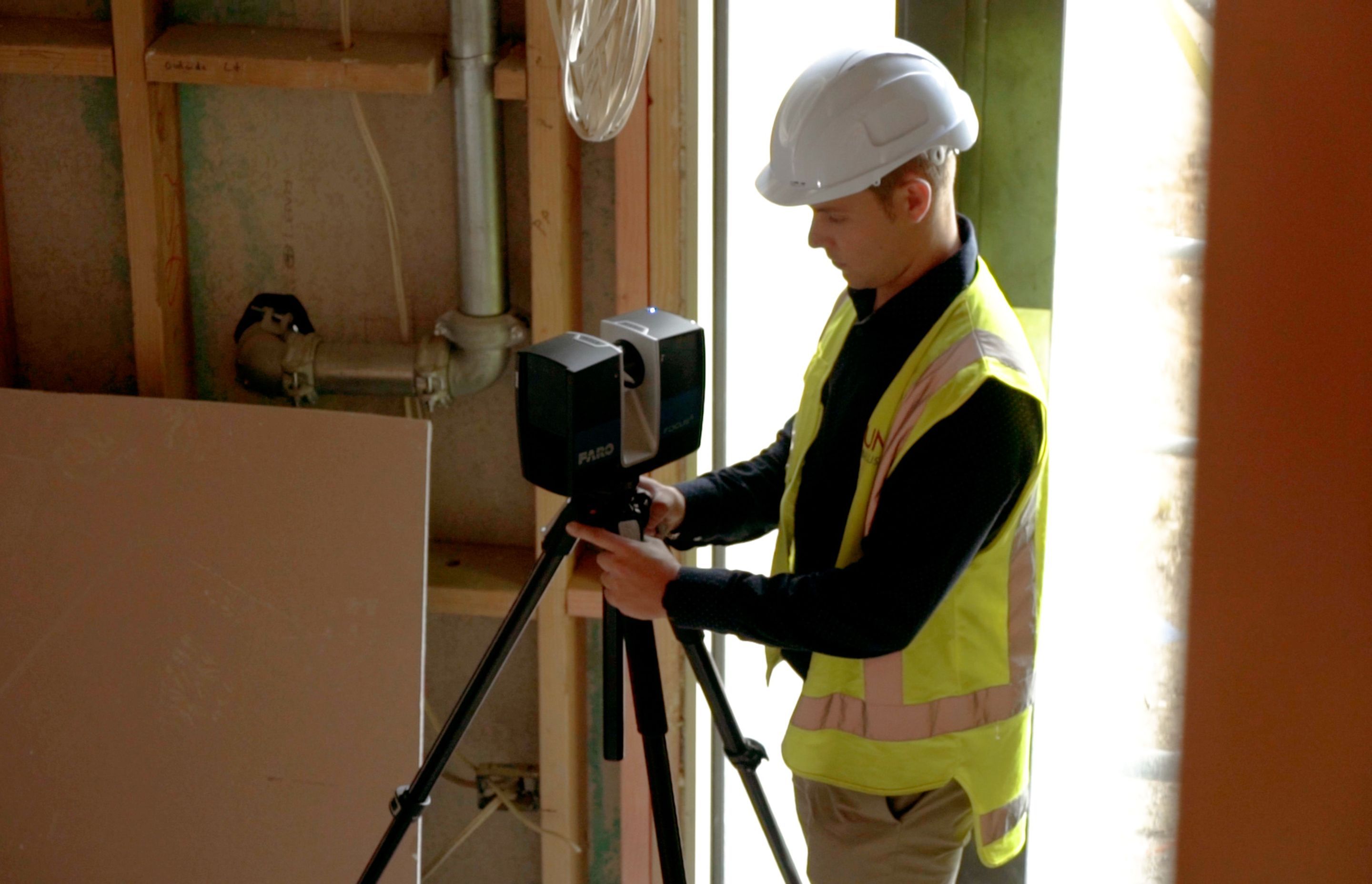
3D scanning: focused on the future
Kevin says Unex utilised 3D scanning technology on the Nixon Central building in Kingsland, Auckland, scanning the building’s stairwells and balconies in order to provide balustrading.
“We purchased our own Focus S 70 laser scanner from Faro last year after having leased one for a little over a year—we have been offering a 3D scanning service in conjunction with our product range since mid-2019. The beauty of having our own machine means we can offer our clients an expedited service without being tied to someone else's schedule. Also, there were additional costs that came from leasing that we had to pass on; now we don't have to do that.
“The scanning unit, which is about twice the size of a school lunch box, has a 360-degree rotating laser and bounces a laser beam off a series of orbs, which have been set up throughout the building at strategic points, creating an outline matrix. From this, we’re able to build a 3D digital blueprint that can be used for further reference.
“3D scanning typically takes between half a day to a full day versus a week-plus for manual measuring. The Nixon Central apartment building included a 10-flight staircase and the system scanned the entire structure with an extremely accurate tolerance of plus-or-minus 1mm over 10m.”
As well as being an expeditious way of measuring buildings for balustrading, Kevin says another of the system’s benefits is its relatively small size and portability.
“Comprising a series of small, separate units, the system is simple to set up; is less intrusive—meaning other trades can continue carrying out their responsibilities at the same time; produces no noise, allowing the actual scanning to be carried out at any time, day or night; requires only 1–2 people to operate; and, can be easily transported from site to site around the country.”
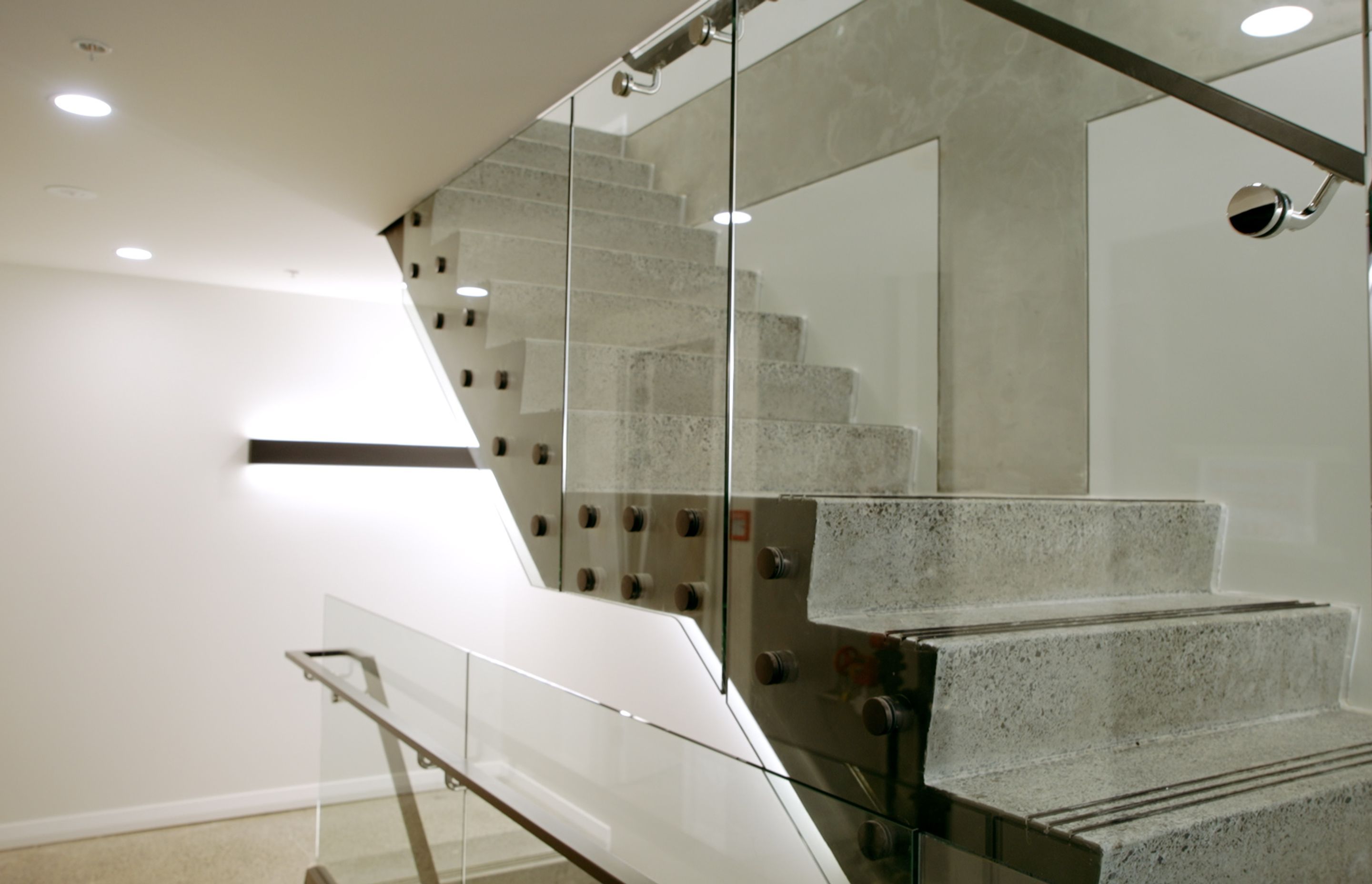
From 3D scan to fabrication
Once completed, Kevin says it takes around two hours to process the scan and produce the 3D blueprint, at which point the Unex team can begin the design process before moving the specs on for fabrication of the chosen balustrades.
“One of the advantages for us with the system, is that it is incredibly versatile in that it allows us to tailor the scanned measurements to any of our balustrading styles. By simply adjusting the measurements to the individual specifications of each style we can digitally measure how much material is needed, making it a cost-effective solution.
“At Unex we’re always looking at ways of reducing wastage, even when using fully recyclable materials such as aluminium, and this system results in very little materials wastage; generally below 10 per cent and as low as two per cent on some jobs.”
Similarly, the minute accuracy of 3D scanning means most, if not all, of the usual onsite installation adjustments are a thing of the past, says Kevin. “Minor refinements can be made onsite if needed, however, installation is usually the only onsite requirement, greatly speeding up this process. Clients can reap the rewards of gains in efficiencies through accurate fabrication and reduced installation times/costs.
“We would love to be talking with architects and architectural designers at the specification stage, 3D scanning is a great service for architects/designers to pitch to their clients as a means of speeding up the construction process. It’s also ideal for use by quantity surveyors as it is very cost effective, while project managers stand to gain with accuracy of install.”
Learn more about how your next project can benefit from greater efficiencies through utilising 3D scanning technology.