The skill is in the detail
Written by
01 September 2019
•
6 min read
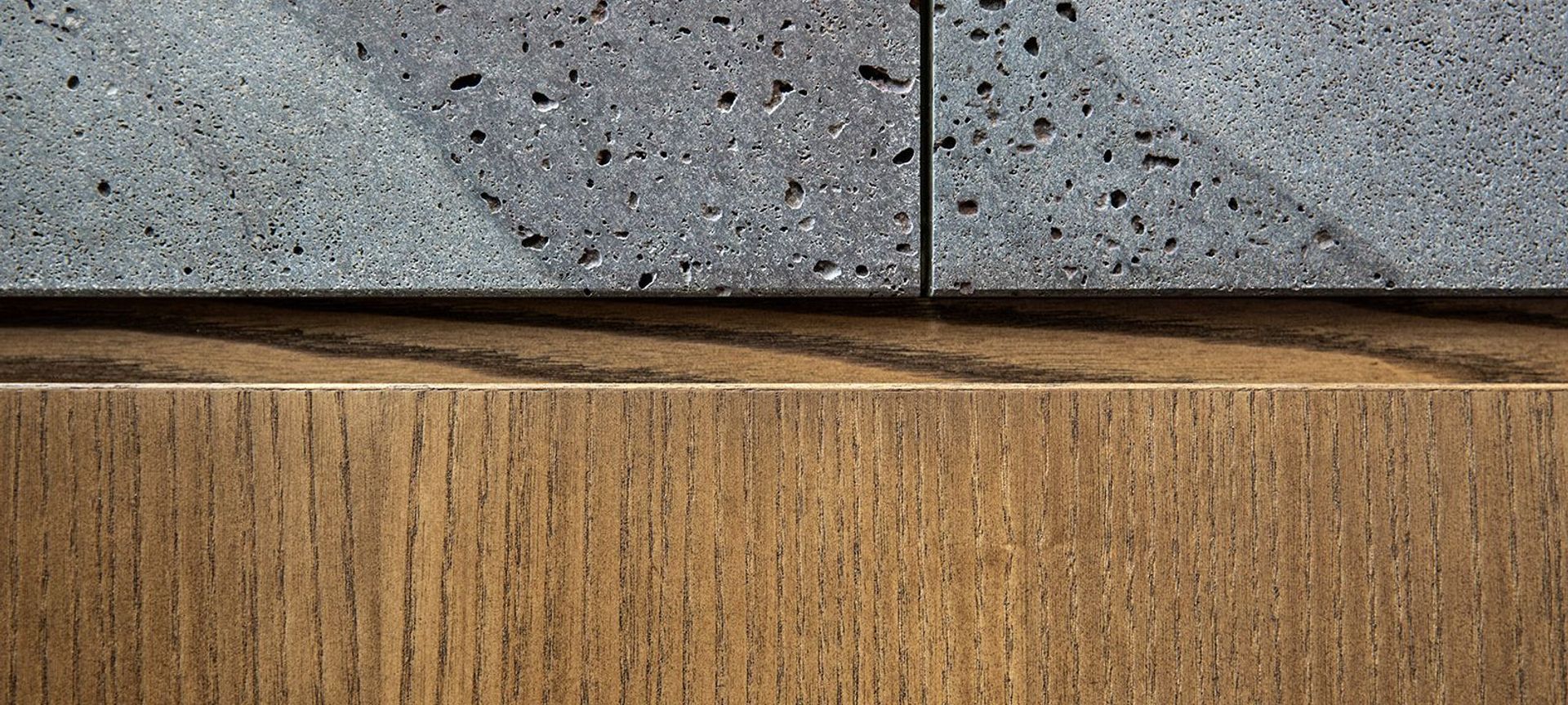
Arranged around a series of micro-landscapes, our Project of the Month, Volcano House, is a courtyard home that celebrates its local mountain, as well as materials from around New Zealand. It is a story of clever details and serious craftsmanship by the team at WG de Gruchy Construction. Justine Harvey spoke with owner William de Gruchy, AKA Willie, about what it takes to create a home that’s also a work of art.
Justine: Volcano House draws inspiration from local mountain Maungauika (North Head) and the neighbouring Cheltenham Beach, but what was special about the materials you worked with on the project?
Willie: We had the chance to work with unique natural materials, whether it be the Timaru bluestone on the walls or the totara and rimu riverwood on the floors and ceiling. These timbers were pulled out of the rivers up north and had been under water for around 100 years.
Then, just the level of detail required to get everything to come together, whether it be the bluestone meeting up with the brushed ash veneer cabinetry, and all the negative details. There is no hiding anywhere on a project like this so, to achieve that level of detail, you have to work very hard early on to understand the final vision.
We needed to have a vision at the very start for what you can see now. When we were putting the structural steel up, we knew that every millimetre we lost would come back to haunt us at a later stage. When we were doing the finishing lines, we pushed really hard to make things as perfect as possible so, when we put the timber sarking up, we spent a lot of time doing it. We ensure that our team understands that they have a chance to put their stamp on something pretty unique.
How did you achieve the beautiful timber ceilings and floors? All of the timber boards for the ceilings were laid on the floor first to try and get the colour variations working. We wouldn’t just put the boards up in a random fashion because, then, you’d be left with a bit of a patchwork quilt. We laid all the colours out to get a bit of a flow going and to try and tell a bit of a story, before we put the boards up on the ceiling.
The result is that you can see all of the boards roll right through the whole house in the same line, whether it be up on the top level or the bottom levels, the board set-out is exactly the same. They work their way out from a set point and all the way out to the ends of the house to the soffit so, when you’re in the bedrooms, you look out through the window and the glazing goes right up to the soffit and the boards look like they’re going right out through the glass.
Creating this effect takes a lot of time and effort, but we haven’t got a lot of time to do a job like this and we have a budget to stick to, so we still have to keep pushing.
How did you achieve such accurate details that all line up perfectly? We had to understand the architect Tom (Rowe from RB Studio) and the client’s visions very early on, so you can set yourself up to produce this result when it all comes together at the end. There are certain datums around the house – in the stone modules, for example, that follow through onto all of the joinery. Although there is a slightly different finish on the internal stone than on the external stone cladding, and a slightly different methodology in the installation, it’s still in the same datum and the same module that follows through to the door heads, the cabinetry heights and the art recesses.
What do you do to ensure your team members are producing high-quality workmanship? We’re very lucky that we have a very good team of professional employees who have done this work year after year, and they deliver day after day to the very highest standards. We finish one job and. roll onto the next and the boys just go, ‘Here we go. Let’s saddle up again and do what we know best’.
I spend a lot of time pushing as hard as possible to challenge ourselves with the best techniques and we are constantly trying to learn and become better craftsmen and tradesmen. We’ll take things the joiners are doing and see if we can adapt that to the carpentry. Often, we take little bits from other professions, whether that be boatbuilding or surveying, to see if we can apply it to what we do. We’re constantly learning and growing and it seems to work really well. It challenges the guys and they are constantly learning new skills.
For instance, there are a lot of 5mm negative details around everything – every light and every speaker, so the boys became really good with their routers and gigs. When you’re putting 5mm negative details around all the different shapes in the ceiling and the air conditioning grills, then you have to have a repertoire for different gigs for your router to work off, which took a lot of time to do. This is definitely a step above the standard work.
What is your favourite part of the project and why?
Being lucky enough to have another opportunity to work with such beautiful natural materials was the big highlight and, after working so hard to ensure we set ourselves up to execute the finer details of these materials throughout the build process, to see them start to come together in the final finished product. It was a massive team effort; from the clients and design team through to the suppliers, subs and, of course, our team of professional employees that is working towards that ultimate end goal from the day they start banging in pegs for boxing up the slab. A result like this is incredibly satisfying and why I do what I do.