Blum: think globally, act locally
Written by
07 August 2020
•
4 min read
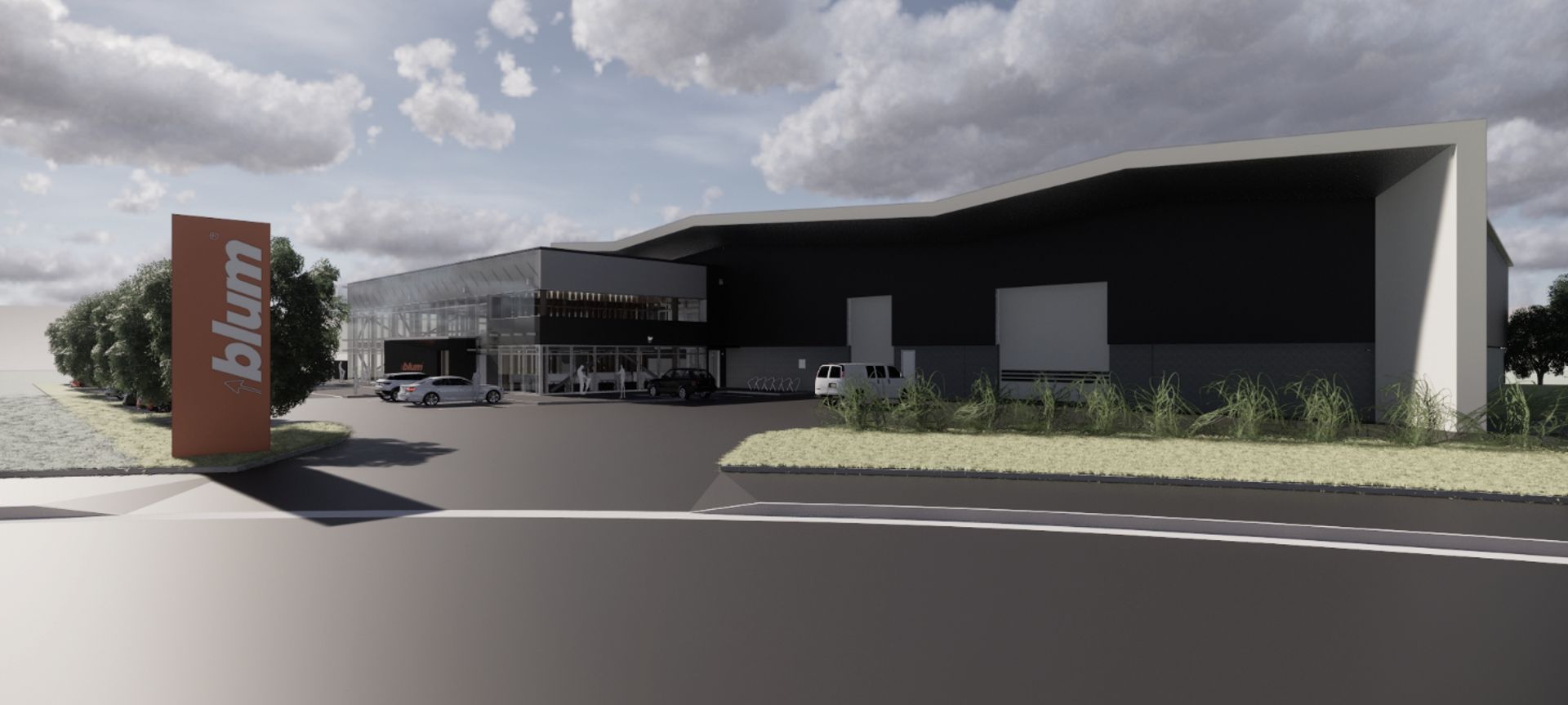
Established by blacksmith Julius Blum in the Austrian municipality of Hӧchst in 1952, Blum has gone from supplying horse shoe studs and furniture hinges to the local inhabitants to being one of the largest global manufacturers of cabinetry hardware, with 11 production facilities and 31 subsidiaries around the world, including New Zealand.
“With a focus on kitchen systems primarily, Blum is well known within the industry to have innovative products built to the highest quality and exports a range of hinge, lift and pull-out products to more than 120 countries,” says Michael Hawkins, Managing Director of Blum New Zealand.
“It’s because of this reputation and a growing customer base that we sought to design and build a new showroom/factory in Christchurch. We had outgrown our existing facility and we really wanted to create something that exemplified the Blum ideal of ‘think globally, act locally’.
Designed by Warren & Mahoney Architects, the new facility comprises warehousing, showroom and offices for 11 full-time staff.
“At 3150m<sup>2</sup>, the new facility fits into our 20-year expansion plan with the warehouse space (2500m<sup>2</sup>) being around 50 per cent larger than current requirements. Additionally, the site, within the old Wigram Air Base, allows for further development, thus future-proofing the facility for the foreseeable future,” says Michael.
“The New Zealand market differs slightly to most other Blum subsidiaries in that we incorporate actual showrooms into our locations rather than solely being warehousing and distribution. To that end, we really wanted a facility that reflected the high-quality of the product and also served to inspire and motivate.
“In a first for Blum, the new showroom has a ‘home-style’ layout with multiple dedicated spaces. This allowed us to focus on the interior design component to really showcase how Blum products can be incorporated throughout the home. We’ve designed the showroom as a relaxed environment for industry professionals—cabinet makers, designers and architects—to bring their clients in to chat about plans over coffee and we highly encourage them to come in and explore and make use of the spaces.”
Michael says they also had a number of requirements governed by the site itself as well as the previously built Auckland showroom.
“We were lucky with the site in that it has views towards the mountains so we really wanted to capitalise on that and the architects responded by giving us high ceilings and lots of glazing. One of the lessons we had learned through the process of building the Auckland showroom a few years back was the importance of keeping the showroom and warehousing capabilities together and, again, Warren & Mahoney really came to the fore with the design.
“They provided us with a lot of choice when it came to materials, which gave us the ability to choose environmentally sustainable options as creating a facility with the smallest environmental footprint possible was one of our clear ambitions.”
The new building features solar panels, a water recovery and recirculation system, geothermal heat recovery, smart ventilation, high-spec insulation and underfloor heating. The sustainability aspect also features internally with engineered oak flooring and terrazzo being specified for the showroom.
“We were conscious of not including any materials containing VOCs and choosing materials that, at the end of their life-cycle, could be recycled,” says Michael. “Similarly, materials were chosen for their acoustic and thermal properties.”
“With the glazing, because there is so much of it, we went with a low-emissivity option from Hagley Windows & Doors for the thermal and environmental benefits. To further aid with solar gain, a fritted pattern was printed onto the glass.”
Externally, the site backs onto a natural swale so the landscaping was designed around using water-tolerant natives. A 40,000-litre tank provides non-potable water for watering the gardens and also for flushing the toilets.
“All-in-all we stayed fairly true to the original design concept,” says Michael. “It was a challenging design and we’re really happy with the outcome. Aside from the delay in getting the showroom open, due to the Covid-19 shutdown, the end result is definitely the one we set out to achieve and we look forward to seeing how the new building is received by the public and our industry partners.”
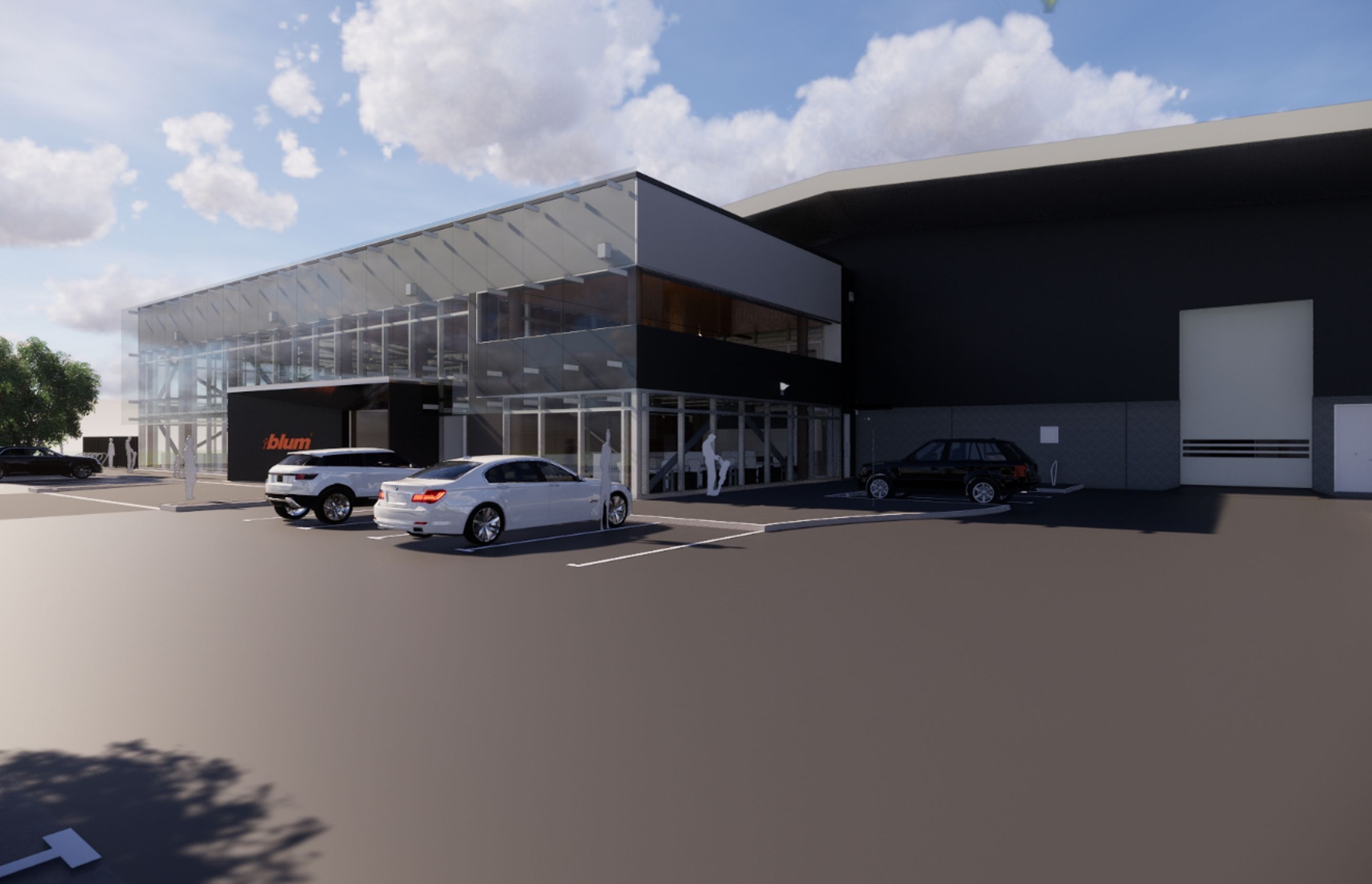
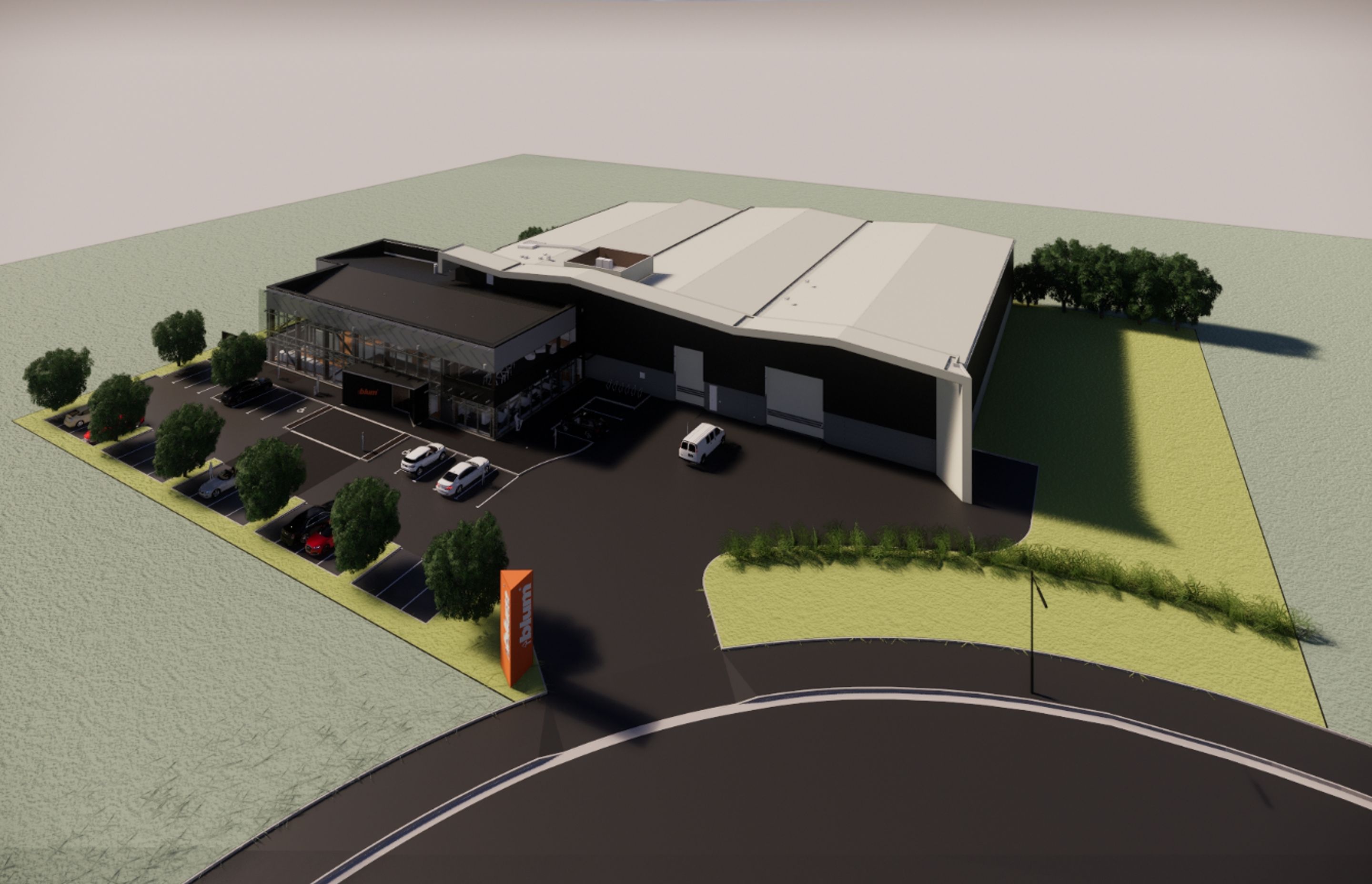