Associated with the winner of a gold medal in the Registered Master Builders Awards, an exemplary kitchen project in a high-end home overlooking Lake Pupuke in the Auckland suburb of Takapuna, illustrates the kind of quality that sets DBJ’s cabinetry work apart.
DBJ’s Paul Walkinton says the owners of the clean-lined Understated Elegance new build project designed by Mark Wilson (MDS) and built by Henry Dunham Building had very exacting standards.
“They wanted their home to be beautiful, luxurious and to stand the test of time. That meant a kitchen that would have longevity well beyond the norm. We create cabinetry that stays looking good for many years,” explains Paul.
Instead of lasting five to eight years, DBJ kitchens and bathrooms look great for at least 20 years because they use products such as MR E0, a highly moisture-resistant, environmentally friendly substrate MDF board. DBJ integrates solid timber into their cabinetry to reduce water ingress, which causes bubbling and water damage.
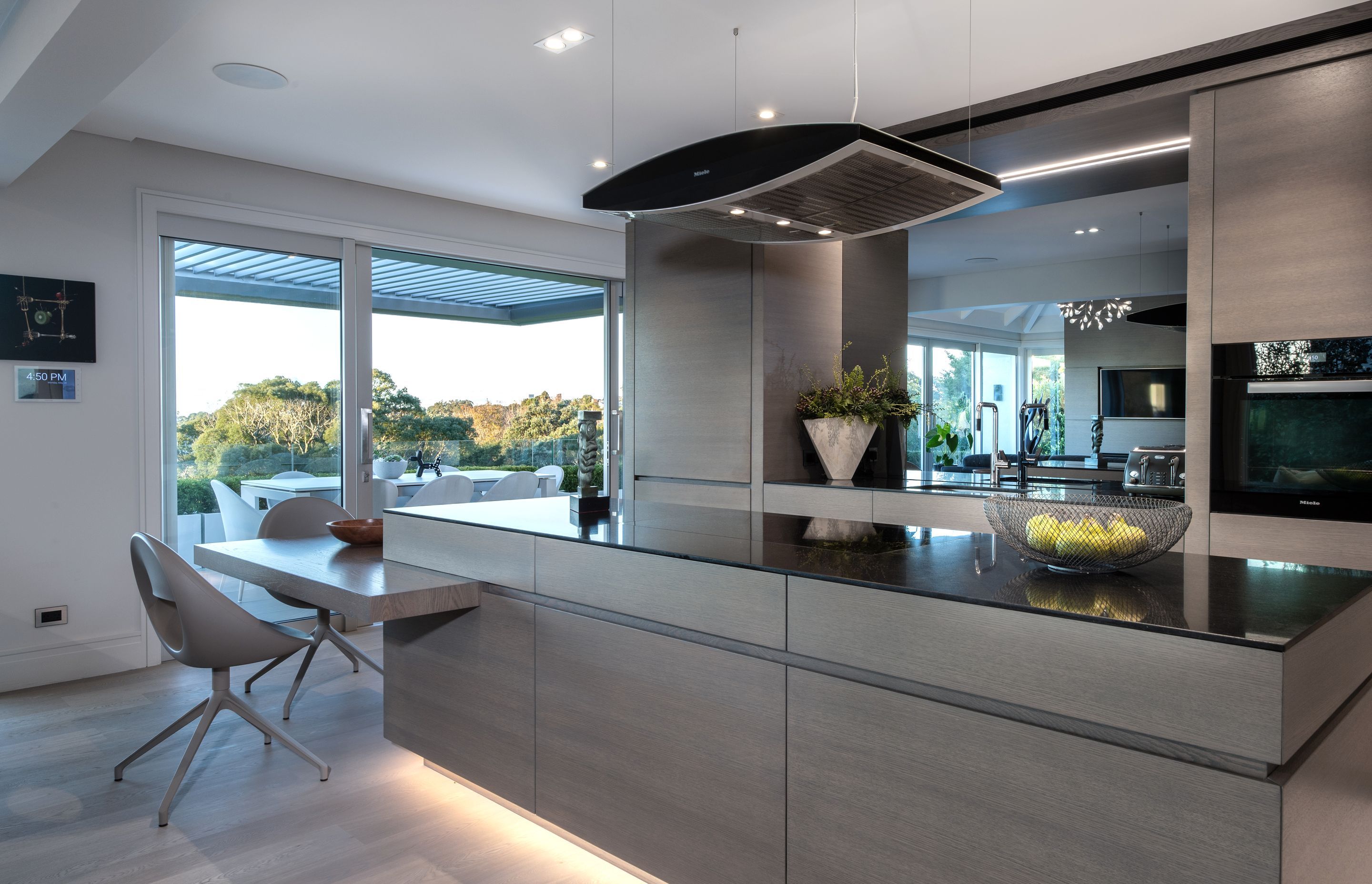
DBJ: building on a solid foundation
“Our high-quality construction methods differ from other cabinetmakers and that was the main reason behind the client’s decision in selecting us to create their kitchen, scullery and full house lot.”
“Choosing superior products also reduces the impact on the environment. We’re not building throwaway items that are going to start deteriorating within three years.”
One of the most striking aspects of this particular kitchen is the evenness of the vertical and horizontal lines between all the cupboards and the sleek negative detail that creates the unobtrusive handles. There is a certain skill required to keep these lines perfect, neat and symmetrical.
DBJ uses increasingly high levels of technology to achieve perfection. For example a new
5-axis CNC (computerised numerical control) machine ensures all panels and carcasses are perfectly square. Doing it by hand simply can’t compete.
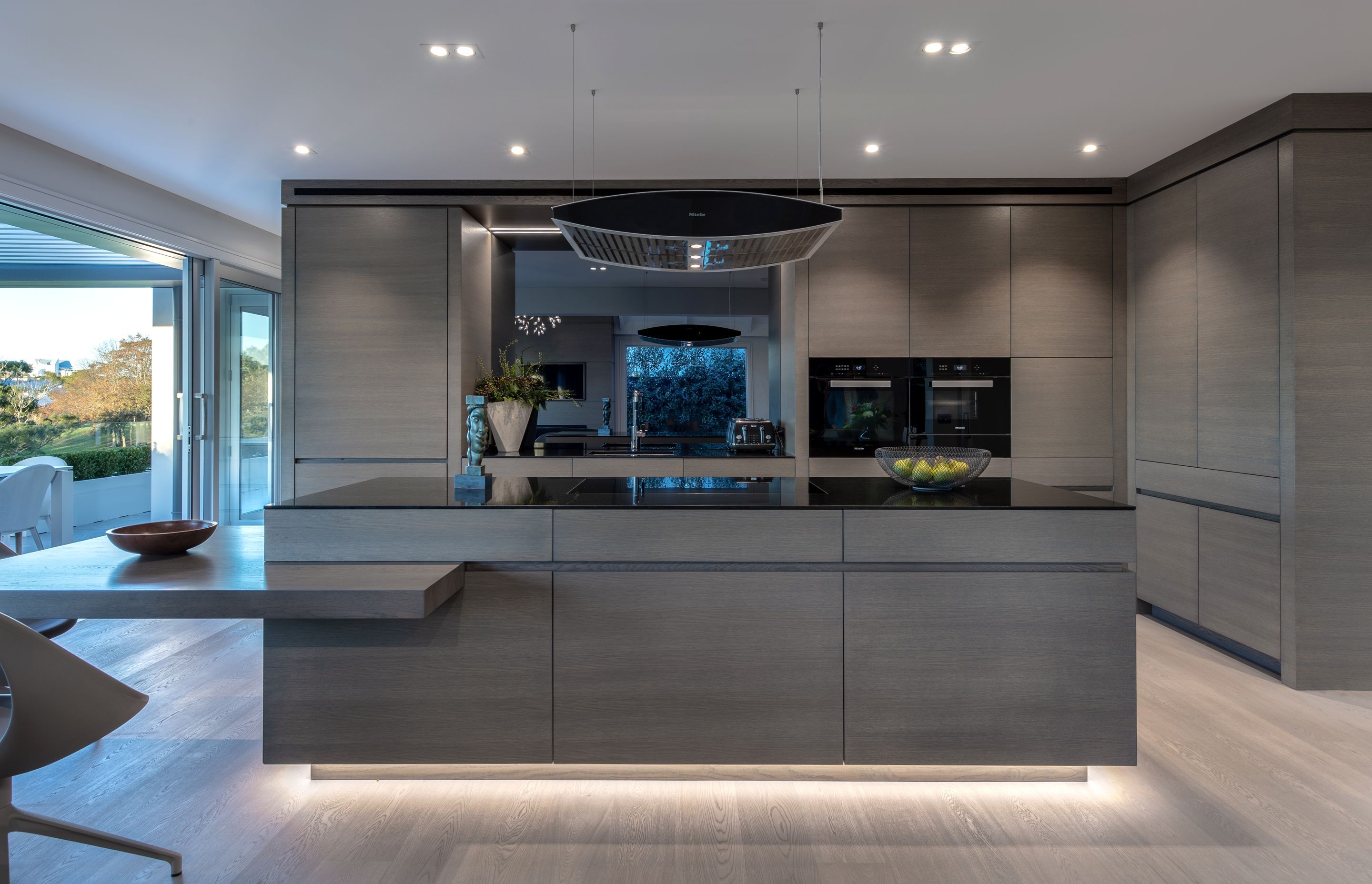
DBJ: an eye for detail
DBJ also uses metals, solid timber and other materials to protect the prone edges in and around the negative handle details, drawer leading edges and toe kick areas.
The techniques used to make the cabinetry are not obvious to look at. But it’s the finished result that tells all.
Paul adds: “We incorporate other clever details in areas like bathrooms too. We have a special technique for fitting mirrored cabinets into tiled areas creating the neatest tile line.“
The final aspect is the finishing product applied to all cabinetry to provide many years of protection. DBJ primarily uses a two-pack polyurethane, which is the most durable and hard-drying finish available. It comes in either a water-based or acrylic product and gives a hard, non-yellowing finish so the cabinetry always looks fresh. This kitchen is American white oak veneer stained and finished in the two-pack polyurethane.
Learn more about custom made kitchens and quality cabinetry for all rooms of your house.