You know something is amiss when Joseph Lyth is feeling the cold.
As a Yorkshire lad, he grew up in a 300 year old farmhouse with ice on the windows, yet is still shocked at the state of some New Zealand houses. “We’ve got an issue of performance here,” he says.
After a stint in London, Joseph and his wife Sarah visited Auckland in 2016 and liked it so much they stayed. The houses they lived in, however, were another story.
“We were renting a room in an old villa in Grey Lynn and it was the kind of house that had a vent in the ceiling that you could see glow worms through in winter, it was that cold and wet. Then we moved into a little granny flat in Murray’s Bay: single-glazed, barely insulated.”
When they started a family, this became a problem.
“Our first child, Lily, was coughing every winter – asthma, inhalers, all sorts of issues – and we were hating it. And then we had our second child, Emily, and the same thing was happening. We just couldn't do it any more.”
Luckily, Joseph is an architect at Respond Architects, and at the time was a newly certified Passive House designer. Together he and Sarah made the decision to build.
“What is the priority? It is a healthy envelope. So if we're going to do it, let’s do it properly. Let’s design a Passive House.”
Bolstered by a small inheritance from Joseph’s grandmother Joyce after she passed, the pair spent a year looking for a site that was affordable with plenty of space. When they found just the spot, 1.4ha in a rural area on Auckland’s North Shore with expansive valley views, it was time to start designing.
So what is a Passive House? There are five basic principles: site-specific insulation, high-performance glazing, airtightness, mechanical ventilation with heat exchange, and minimal thermal bridges.
“I’d first learned about it in university back in London,” says Joseph. “Interestingly, I do remember thinking, why would you? It’s basically a thermos flask with a ventilation system stuck on it. But once you dive deeper down the rabbit hole and learn why, it all makes sense.”

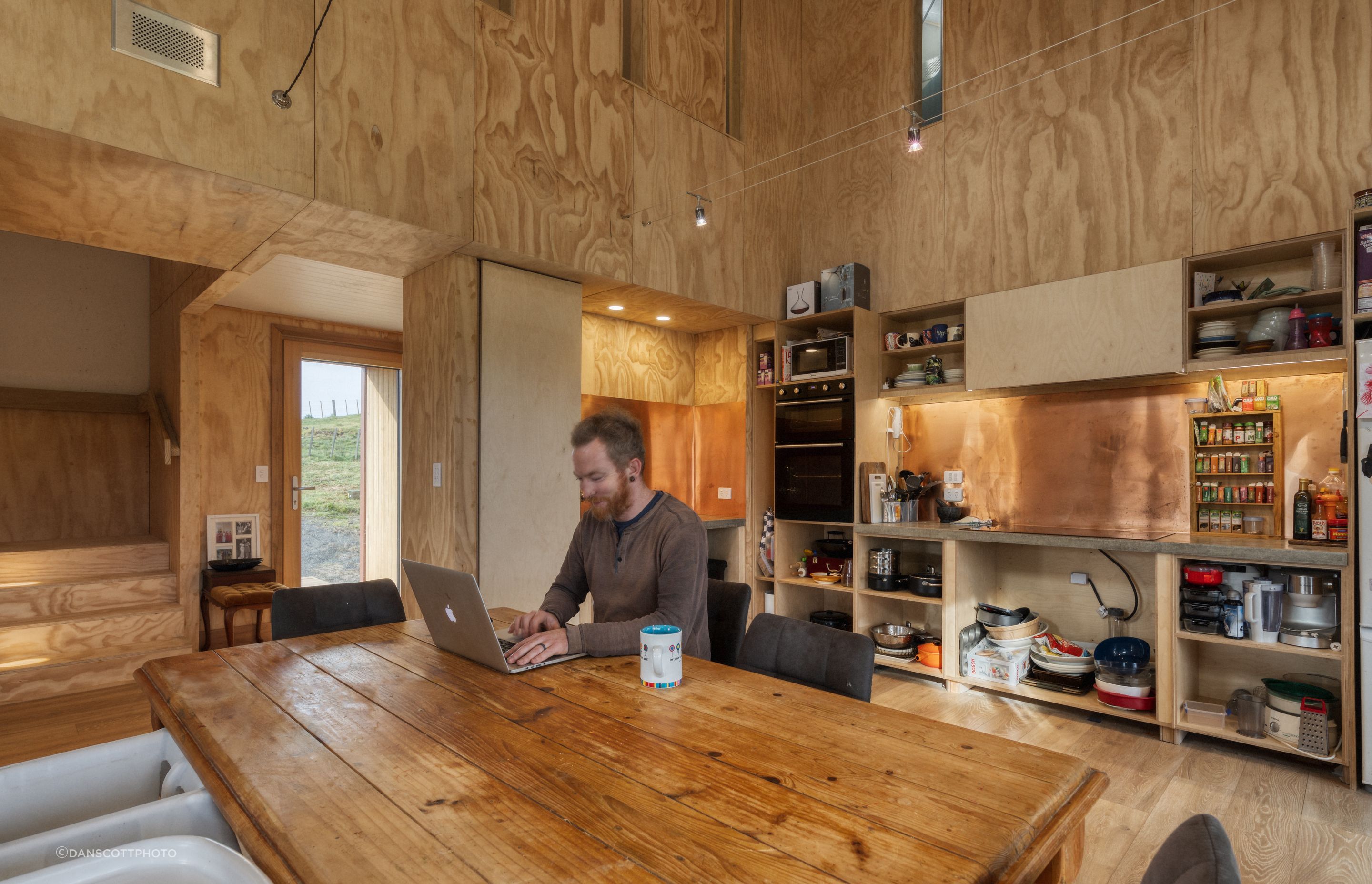
Unfortunately the builder’s quote on the initial design was twice as much as expected. Plus, to satisfy the bank’s mortgage requirements, the house had to be larger than envisaged to increase its value. For the sake of the budget, this meant paring back to the essentials.
“It was a real exercise. How can we mitigate the upfront costs, what can we do later or do ourselves? We basically put our money into the things that really count.”
They switched from concrete water tanks to plastic, and deleted the varnishing of the ply walls from the builder’s contract.
“I took every day of annual leave I had and came on site to help bring down the labour costs. If I'm being honest, it probably didn't help that much with the budget but it did give me valuable experience from the builders’ perspective and I learned a lot.”
The house is built using SIPs, structural insulated panels, from Formance. It’s basically a sandwich, says Joseph: expanded polystyrene between two layers of strandboard.
“It’s your insulation, it’s your structure, it’s your interior lining if you want, and it’s your air barrier as well. So while the product itself costs more, it does several jobs. It's also much quicker: our walls went up in two days.”
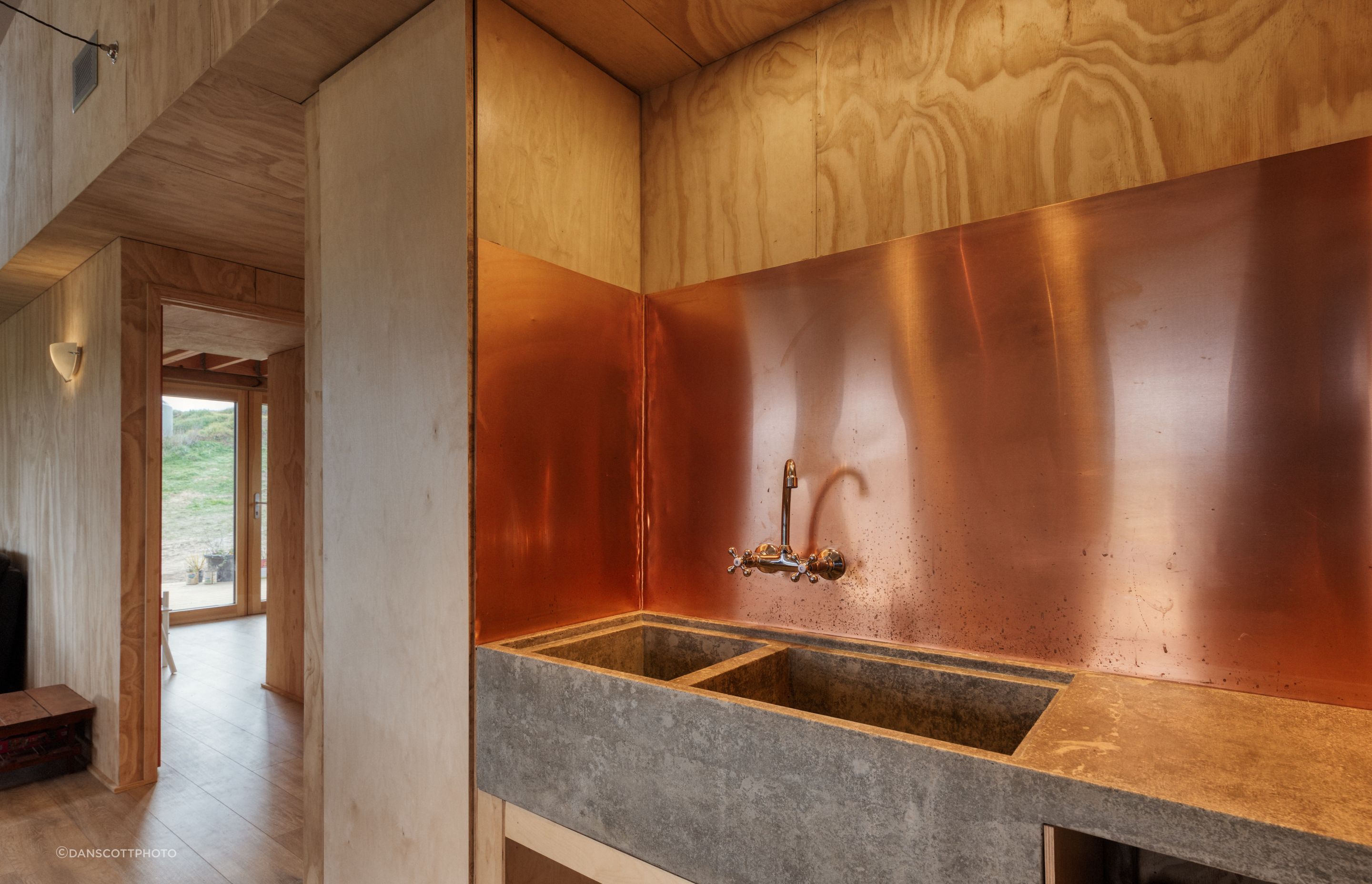
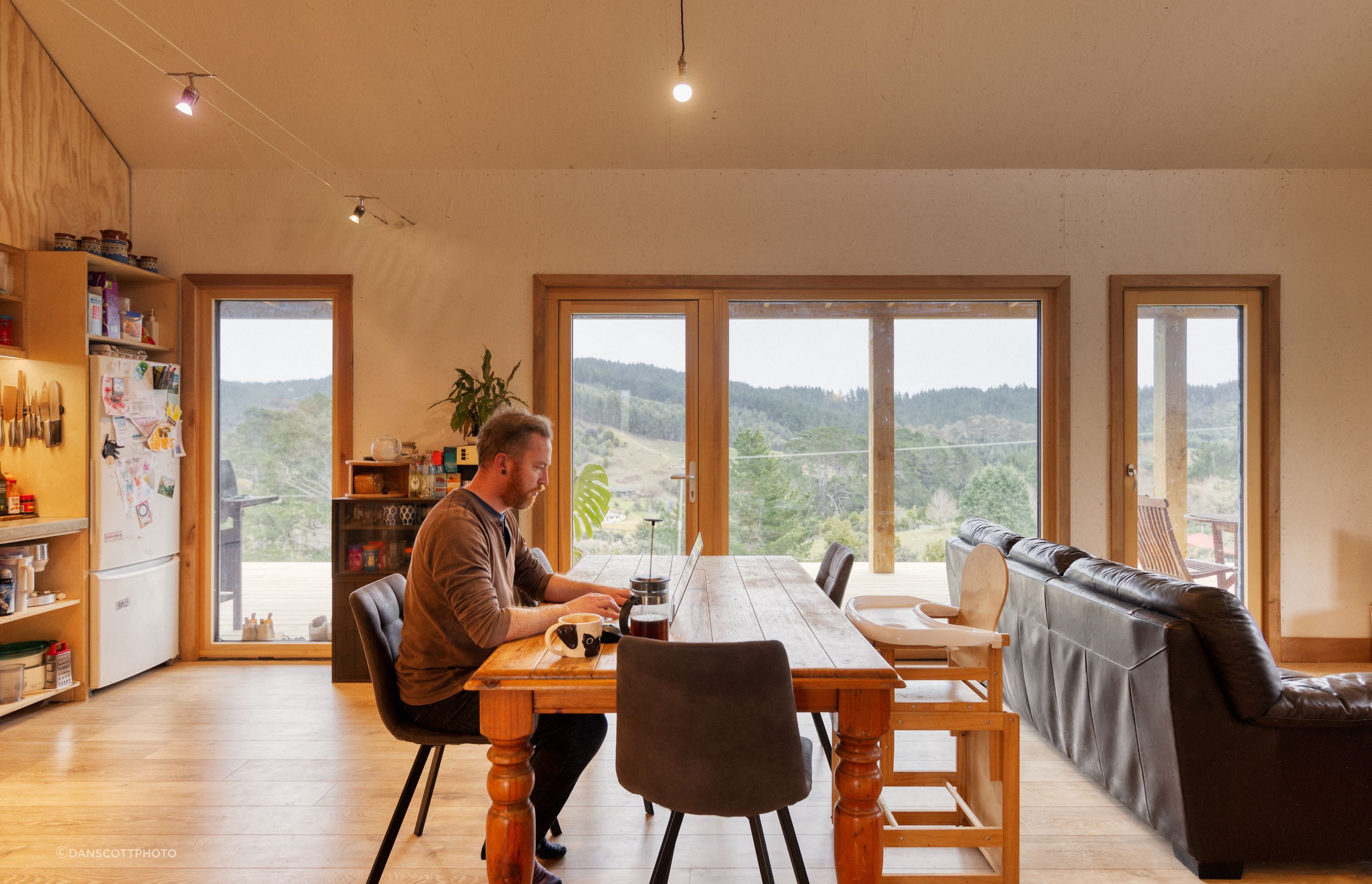
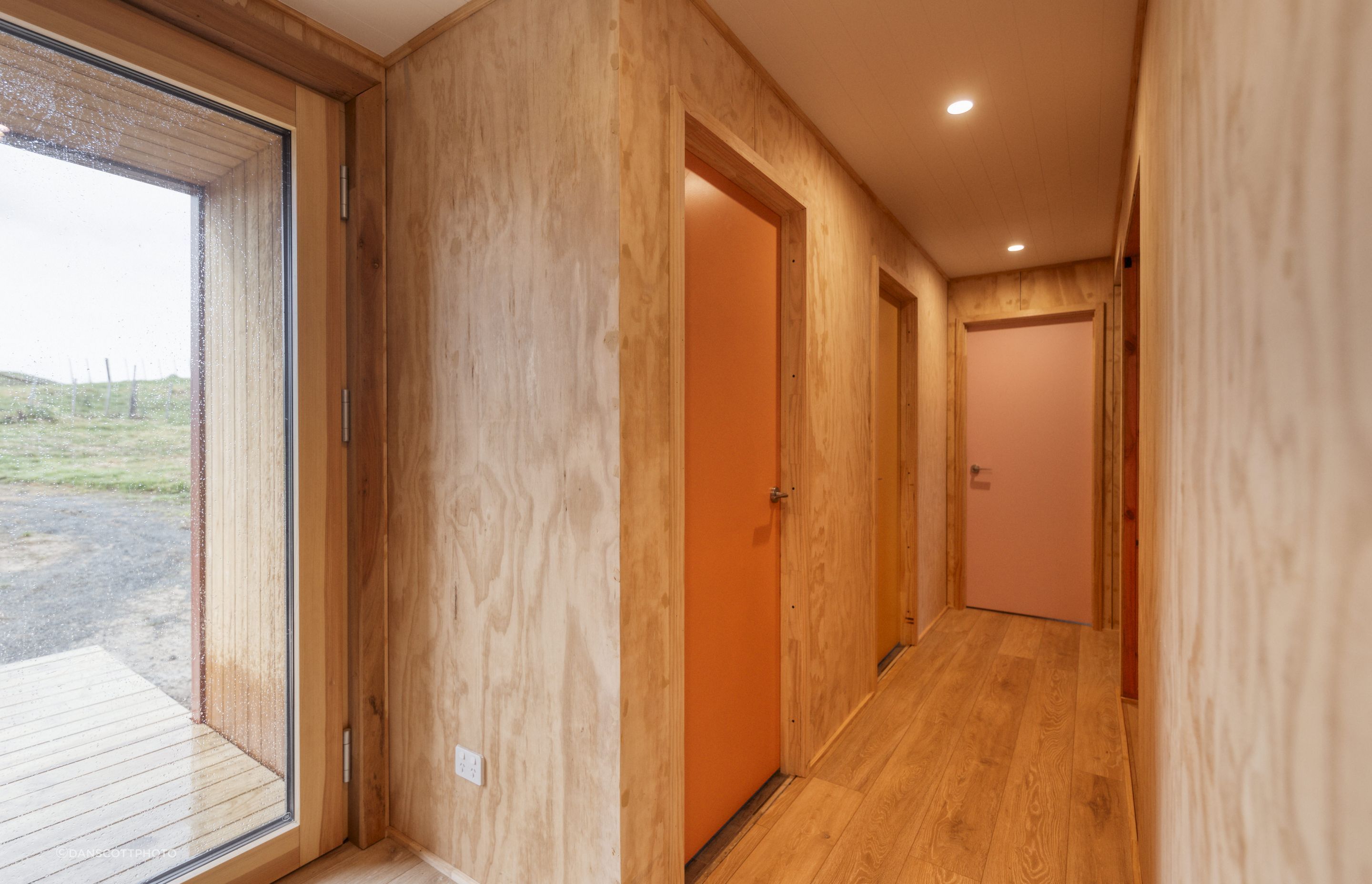
Functionality doesn’t trump the form: the house has been designed in a classic barn style.
“You think of shelter, you think simplicity, you think robustness,” says Joseph. “And because it’s a rural location, we didn't want something massively modern. I can literally see another red barn across the valley so it sits into its context really nicely.”
The home is full of texture with the exposed strandboard of the SIPs and the ply-lined interior walls.
“My preference is for materials that have got character,” says Joseph. So much so, he has added even more. He built the forms and cast the concrete sinks himself, and installed the sheet copper splashbacks.
“We were concerned that we might have gone a bit overboard with the texture, but I think they all complement each other, and we love seeing the developing patina on the copper and concrete.”
All that texture inside meant colour was tricky to add. “My oldest said she wanted a pink door for her bedroom. It was a good idea but we didn’t want every door pink, so we went to Resene and worked with one of their colour experts to come up with a palette that adds to the journey through the house. It makes me happy when I see the doors, I do love a bit of colour.”
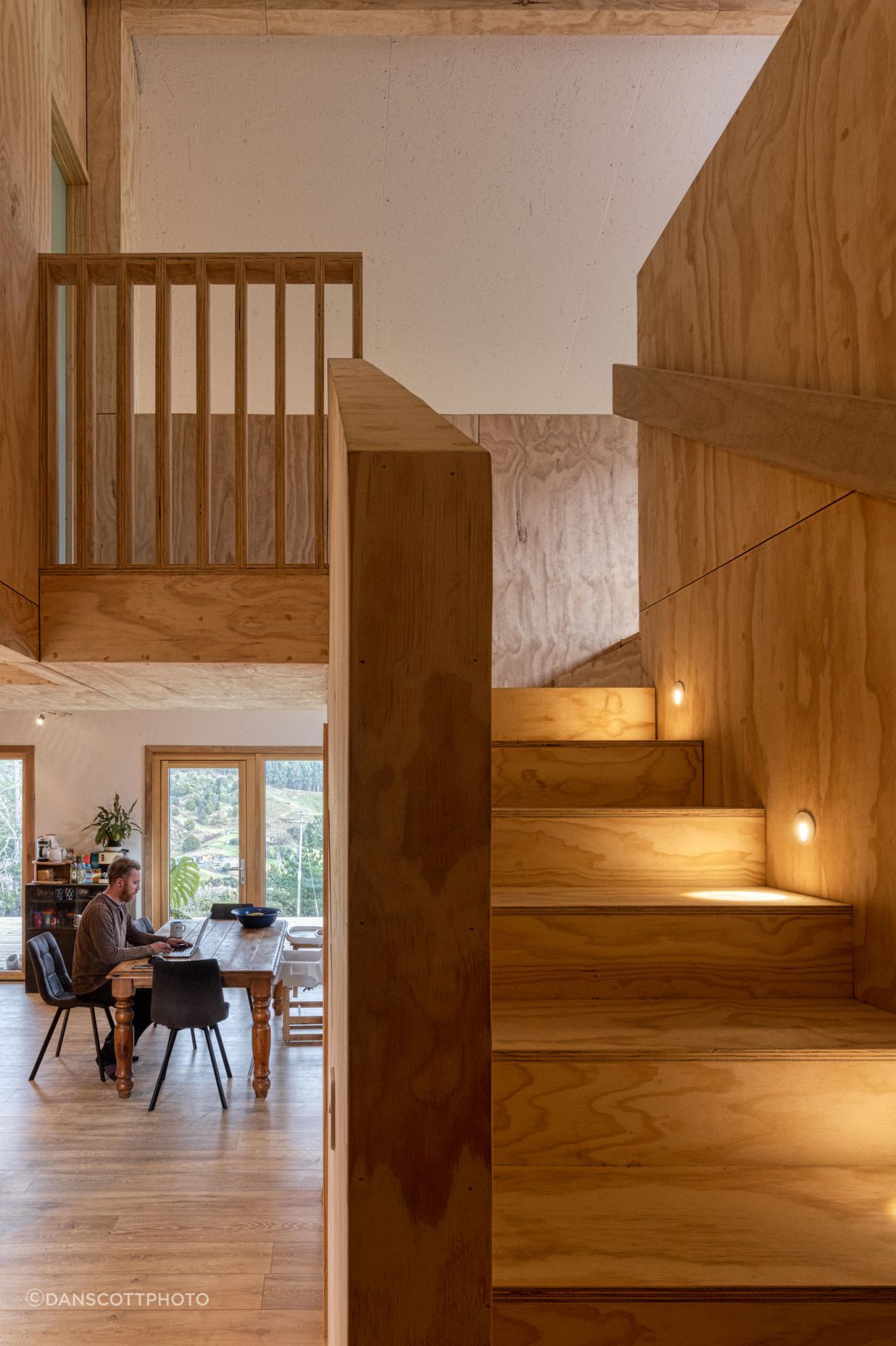
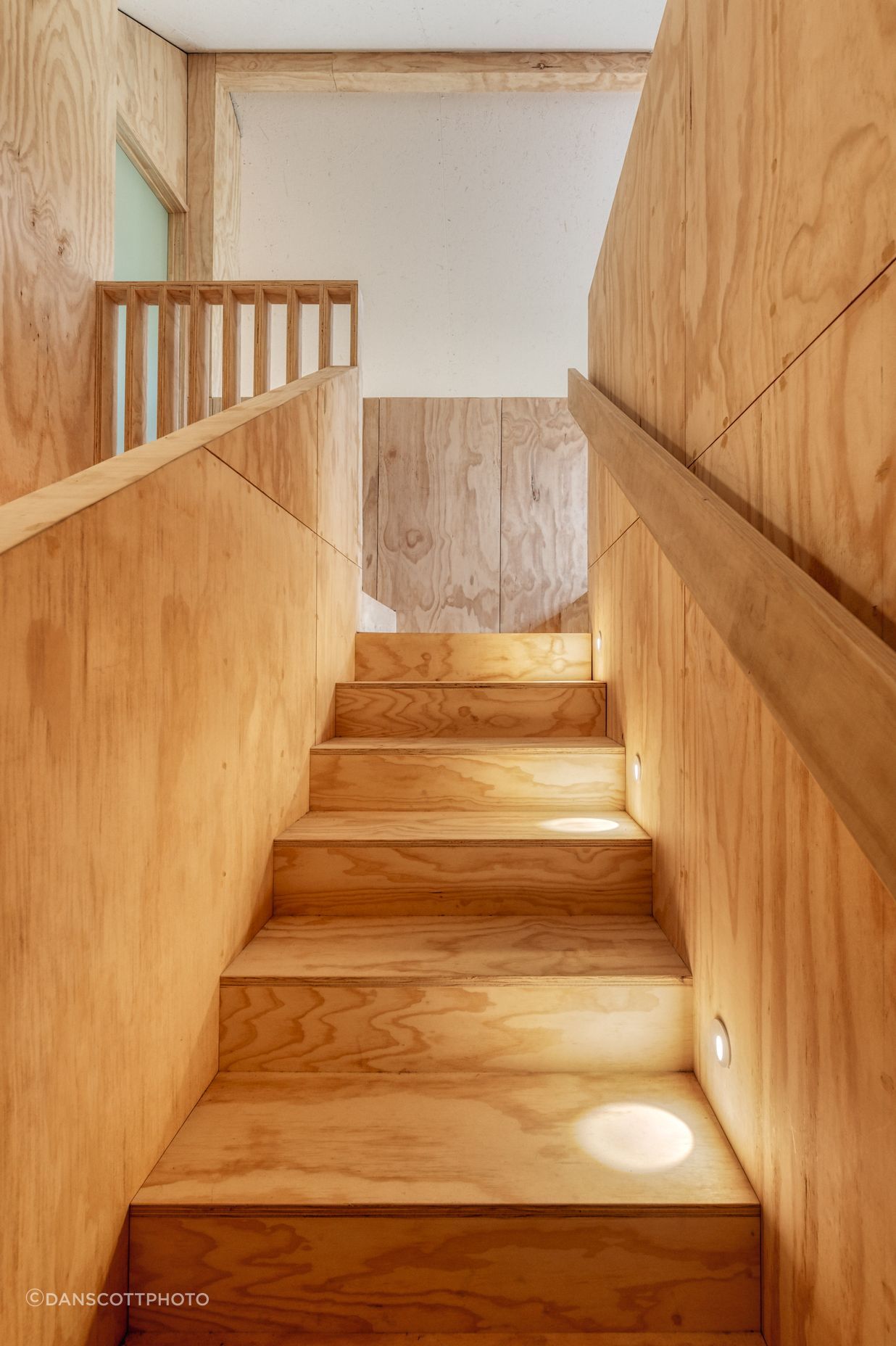
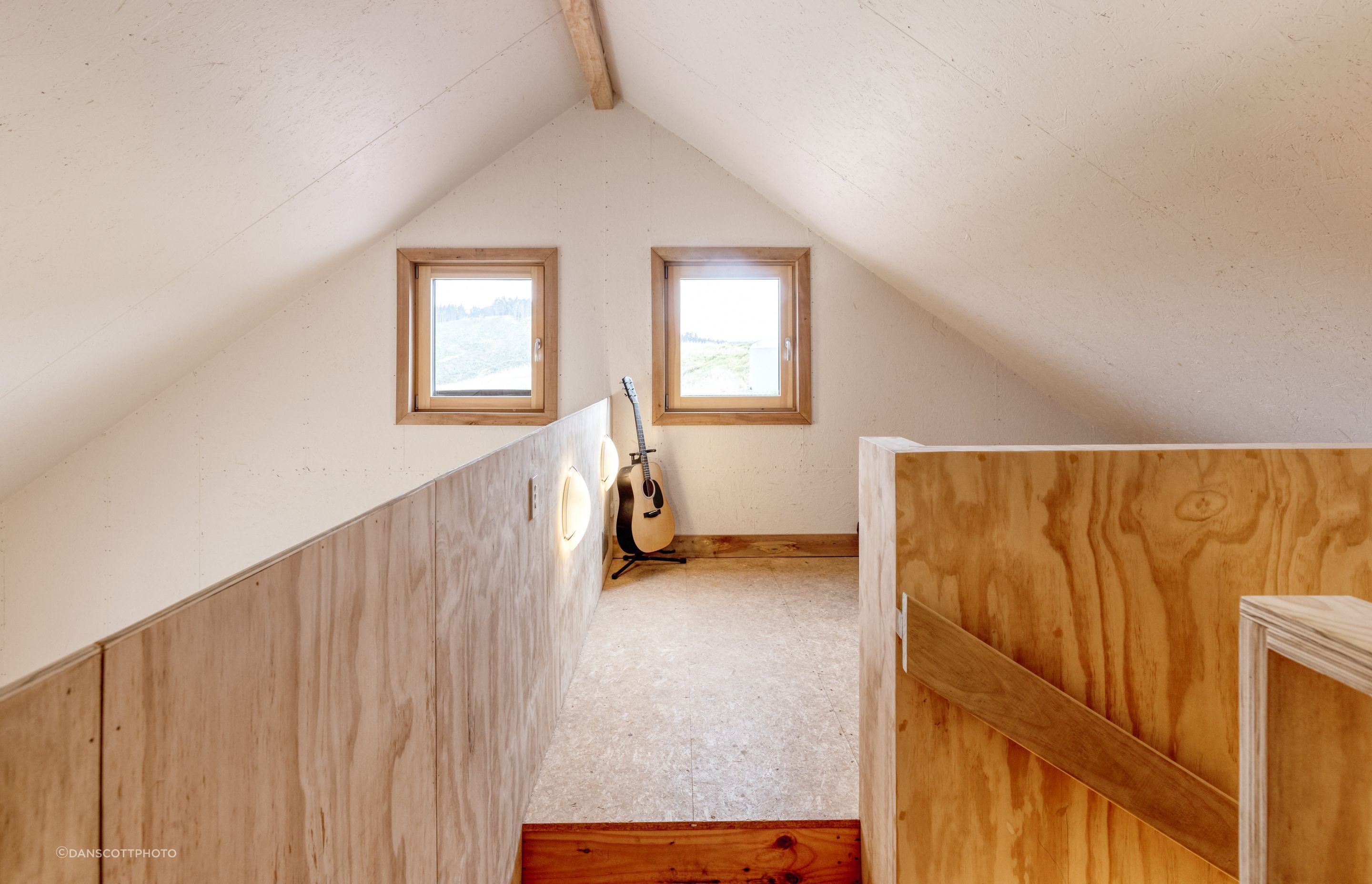
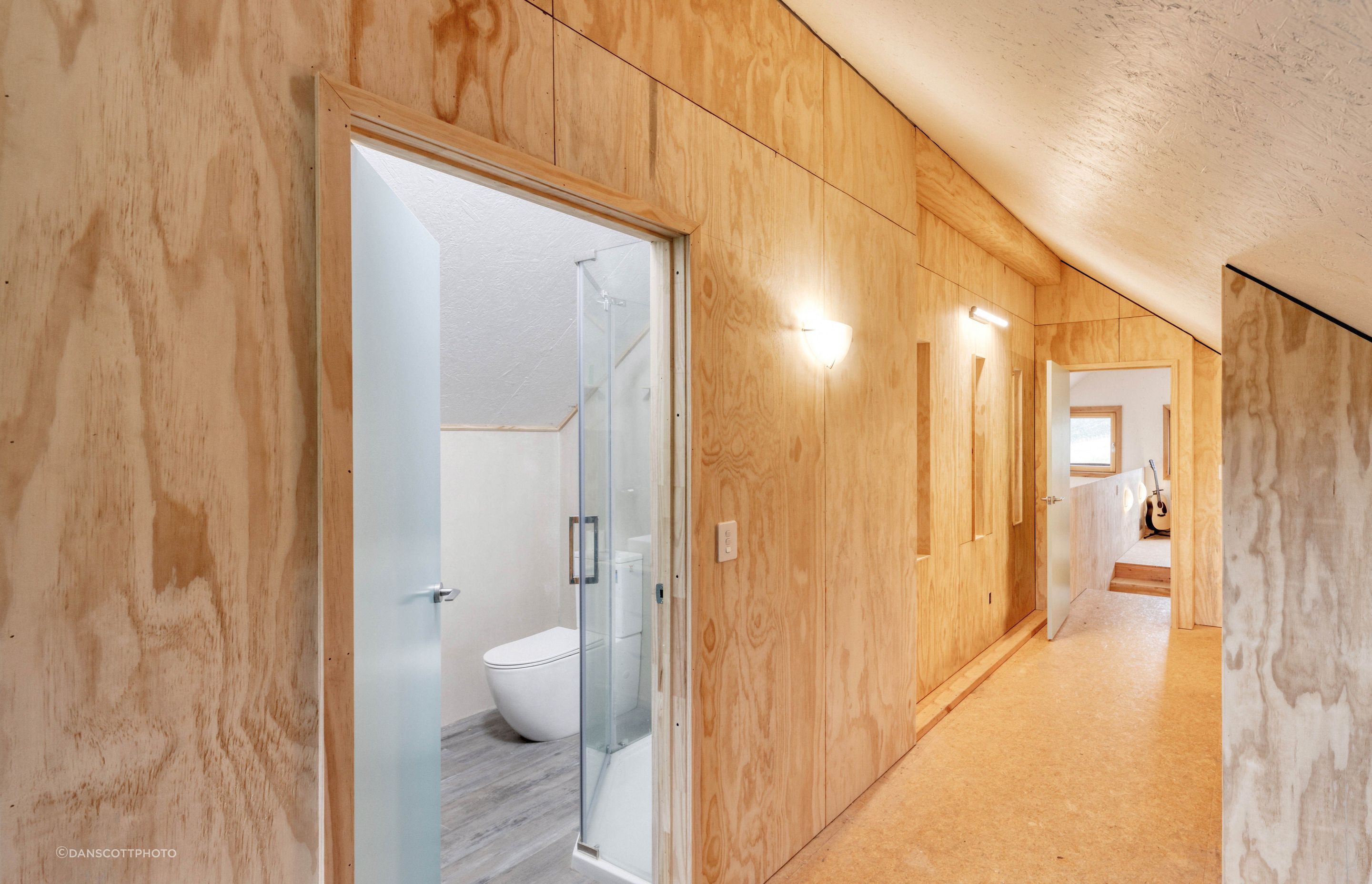
Also pleasing is the performance of the Passive House: the environment inside the home is monitored by Tether sensors so the family can keep an eye on carbon dioxide levels, temperature and humidity.
Now with three children including baby William, all health issues are resolved. “Emily was just hacking for the month before we moved in and within a week she was fine.”
Joseph says this was the first certified Passive House he designed. “It’s great to use yourself as a guinea pig.”
A fully certified Passive House is a vigorous process, and needs to be considered right from the concept stage. But Respond Architects can still apply the principles to any degree to create a higher performing home that is warmer, dryer and more energy efficient.
“We're not purists. As a practice, we completely understand that not every single project can be fully Certified Passive House. But we want to improve every project because every little step is a good step as far as we're concerned.”
Images: Dan Scott Photo

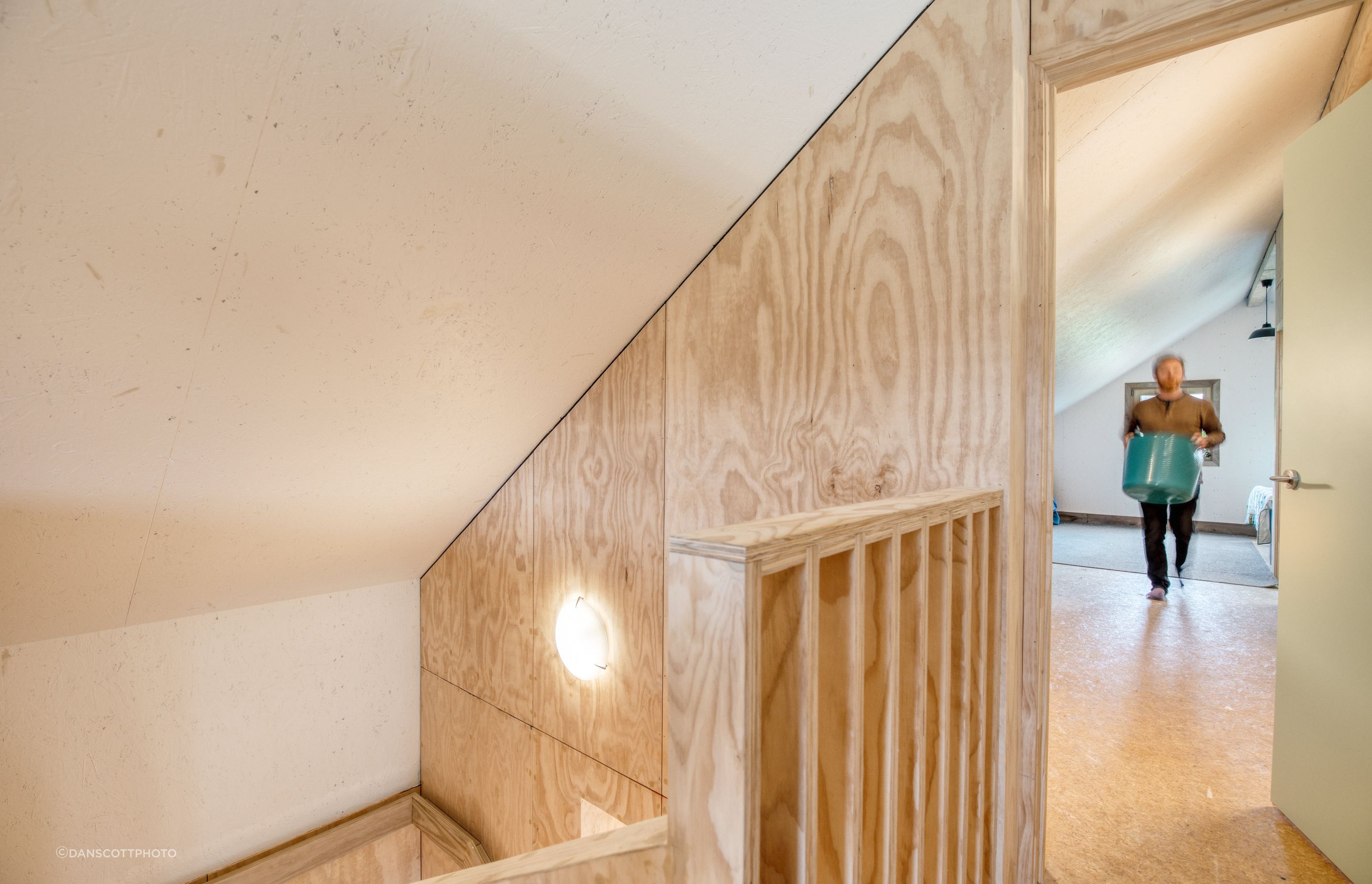
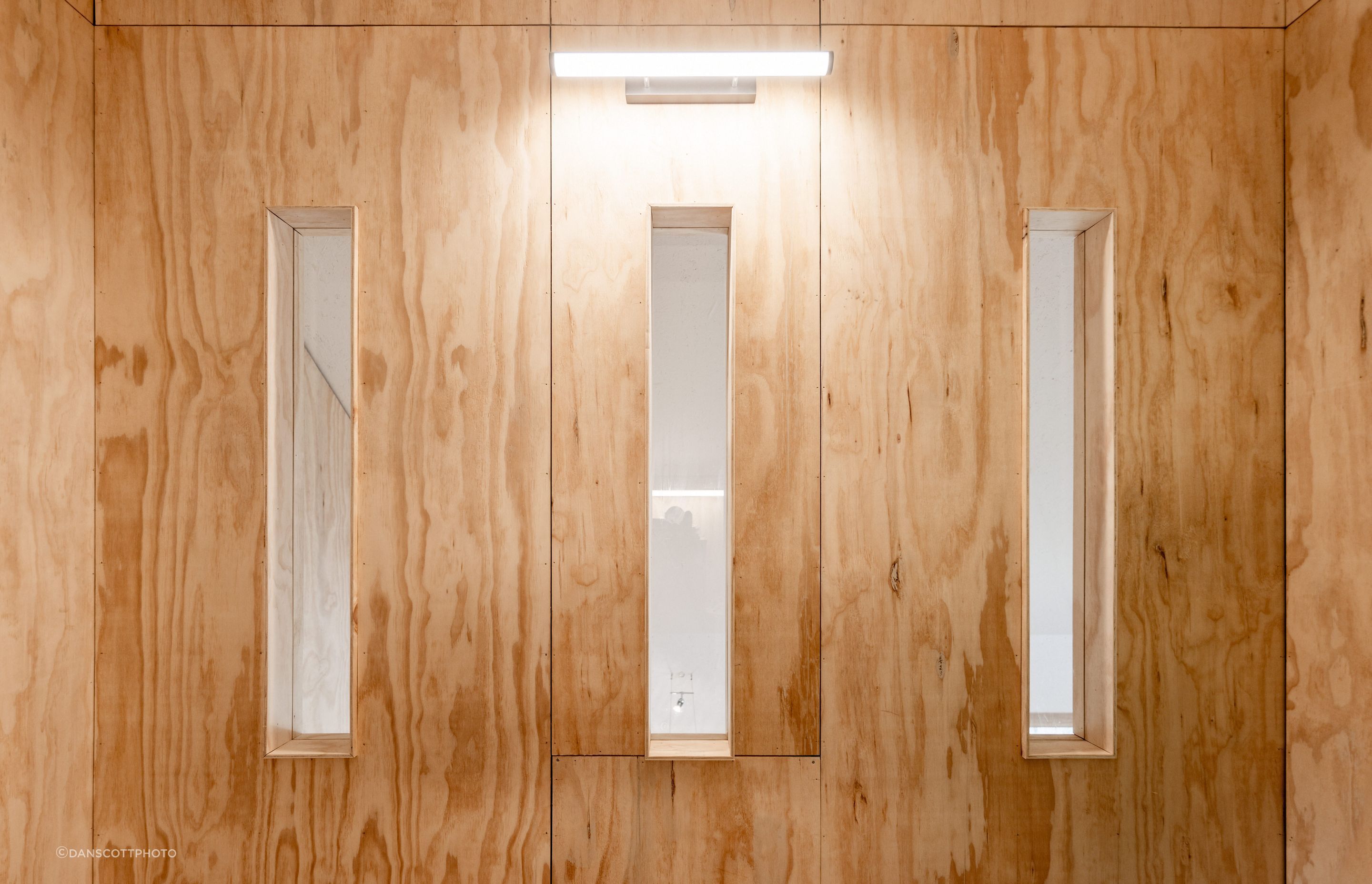
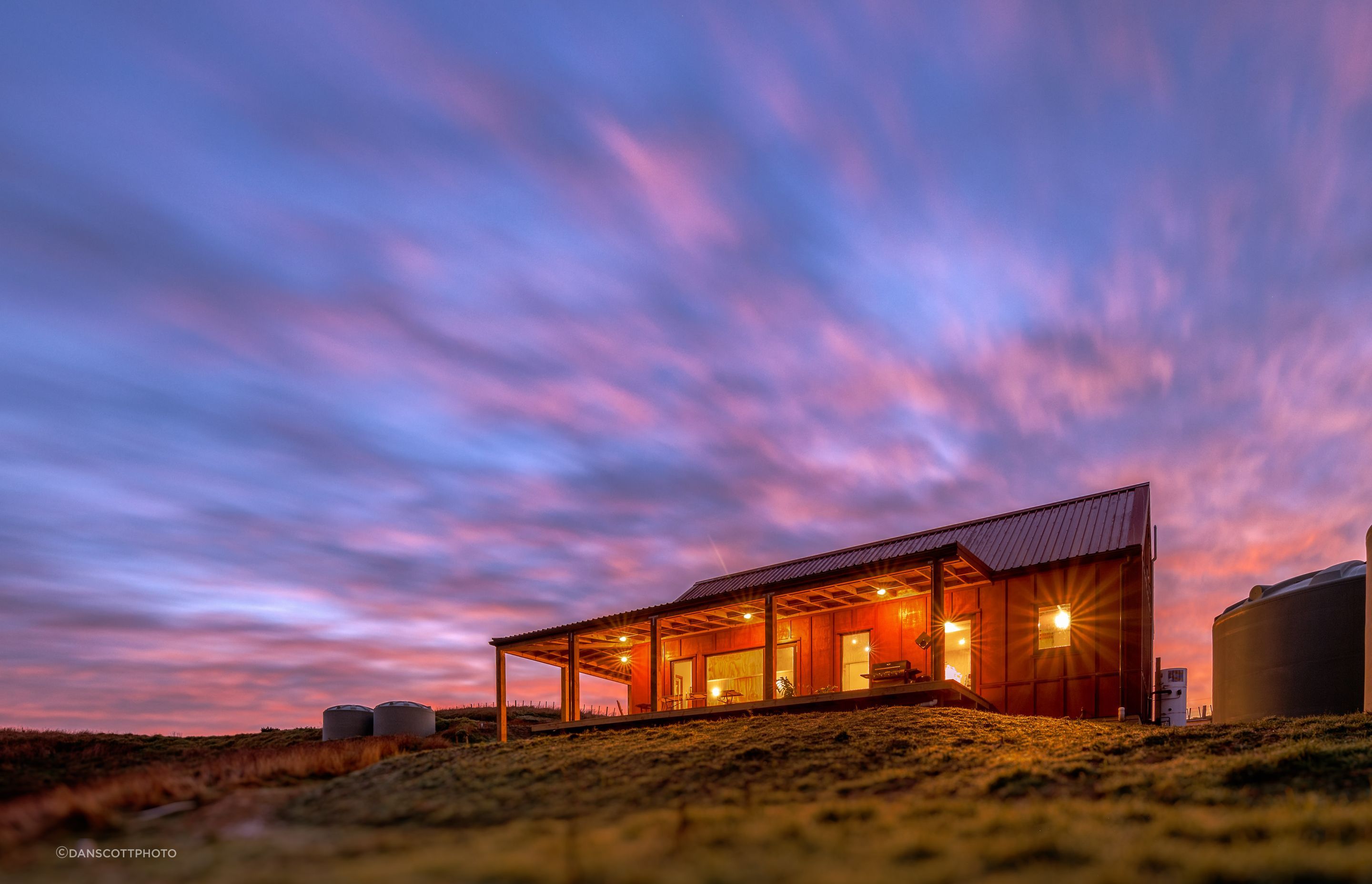