5 Tips for Applying Microcement with Rockcote MicroStone
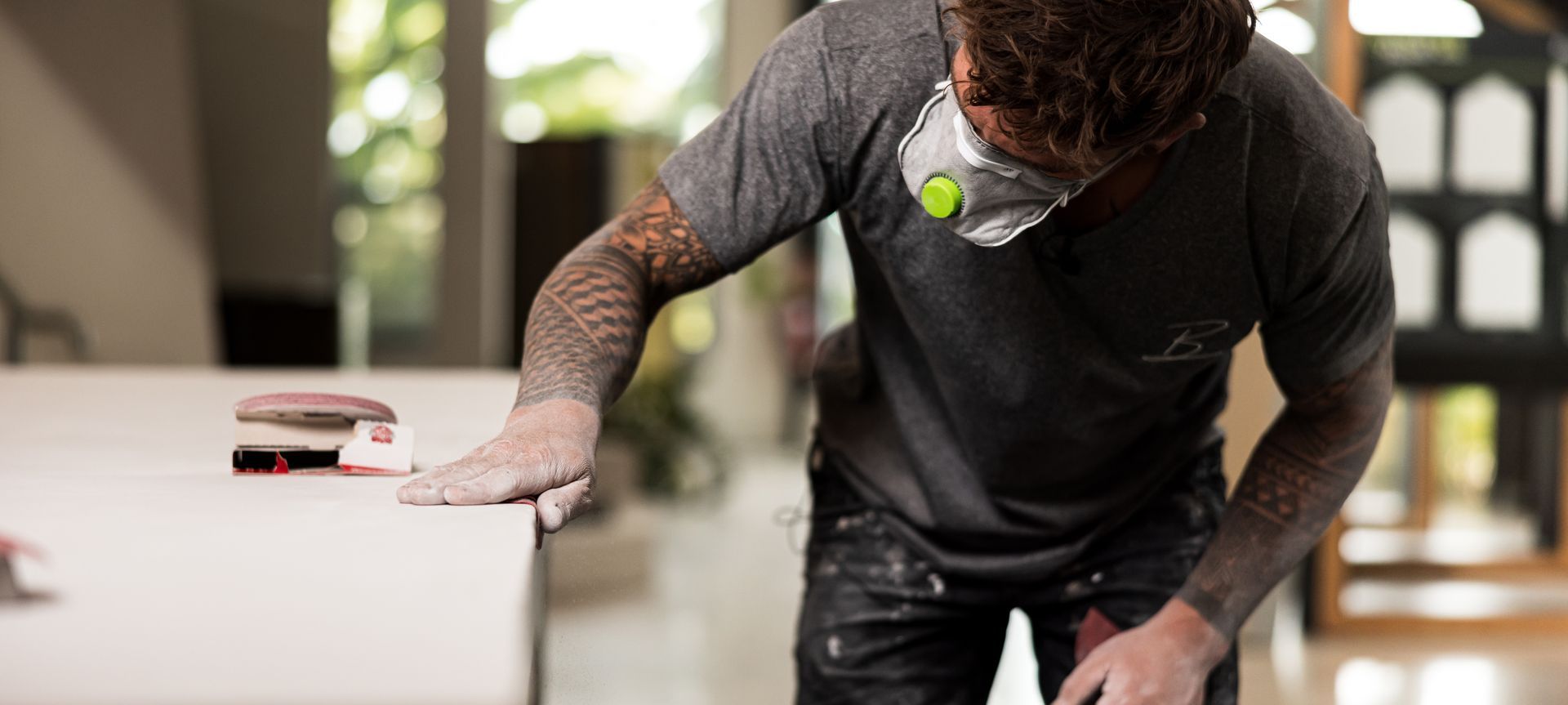
Rockcote, a leading Australian-owned brand known for its commitment to quality and service, is proud to introduce its MicroStone range. This innovative product line is designed to offer a natural microcement finish that exudes elegance and durability. In the following blog, we will share five expert tips for applying MicroStone to ensure a flawless and long-lasting finish!
Preparing the Surface
Proper surface preparation is the foundation of any successful microcement application. A well-prepared surface ensures strong adhesion and a smooth, flawless finish.
1. Clean the Surface:
Ensure the surface is dust-free, grease-free, and completely dry. Any moisture can hinder the adhesion of the microcement. Sand, grind, or acid etch any existing paint, coatings, or debris as required. This step is crucial to ensure the new layer adheres well.
For surfaces requiring regularisation, such as tiled walls or rough cement, apply a primer to improve bonding. Rockcote’s Keycote or High Adhesion Primer is ideal for this purpose. For more information on primers and additives, visit Rockcote’s Patching, Priming, and Additives.
2. Regularisation:
- Irregular surfaces need a regularisation procedure to create a smooth, level base for the microcement. This is essential for surfaces like walls with tiles or uneven cement.
- Apply a base coat to create a smooth, level surface. Use a trowel to spread the base coat evenly and allow it to dry completely. The base coat acts as a foundation, ensuring proper adhesion of the microcement. It is critical to follow the manufacturer’s instructions for mixing and application to achieve the best results.
Mixing and Application Techniques
Achieving the right consistency in your microcement mixture is crucial for a smooth and even application.
3. Mixing Microcement:
- Follow the manufacturer’s instructions precisely for mixing Part A (10L) and Part B (5L) of the MicroStone. Accurate proportions are essential for the mixture’s performance.
- Use a mechanical mixer to achieve a uniform, lump-free consistency. Mixing by hand can result in inconsistencies and lumps, which can affect the final finish.
- Ensure that the mixed product is used within the recommended timeframe to maintain its optimal properties.
4. Application Techniques:
- Apply the first coat of microcement with a trowel or spatula, ensuring an even spread. This coat will create a smooth base for the subsequent layers.
- Allow the first coat to dry completely before applying the second coat.
- The second coat should provide the desired texture and colour. Spread the microcement evenly, achieving the desired thickness, and smooth out the surface using a steel trowel or a finishing trowel.
- Additional coats may be required to enhance durability for floors. Each coat should be applied thinly and allowed to dry completely before the next application. Rockcote’s MicroStone can be used to achieve various textures, so experiment with different techniques to find the best finish for your project.
Finishing Touches
The final appearance of your microcement render can be significantly enhanced with careful finishing touches.
5. Sanding and Sealing:
- After the final coat of microcement has dried, gently sand the surface with fine-grit sandpaper to achieve a smooth, even finish. This step helps to remove any imperfections and create a uniform surface.
- Remove all sanding dust with a vacuum cleaner or damp cloth. It’s important to ensure the surface is completely clean before proceeding to the sealing stage.
- Apply a coat of sealer using a short-haired roller or brush. This step is crucial for protecting the microcement from stains, water damage, and wear. The sealer also helps to enhance the final appearance by bringing out the colour and texture of the microcement.
- Multiple coats of sealer may be applied to achieve the desired level of protection and enhance the final appearance. Follow the manufacturer’s instructions for drying times between coats.
- Finally, apply a finishing varnish to ensure complete water resistance and durability. Depending on the application area, choose between shiny, matte, or satin finishes. Shiny finishes are typically recommended for floors, while matte or satin finishes are preferred for walls. The finishing varnish provides an additional protection layer and enhances the microcement’s visual appeal.
Common Mistakes to Avoid
To ensure a flawless application, it’s important to be aware of common mistakes and how to avoid them.
1. Inadequate Surface Preparation:
- Skipping surface cleaning or regularisation can lead to poor adhesion and an uneven finish. Always ensure the surface is thoroughly prepared. Neglecting this step can result in the microcement peeling or cracking over time.
2. Incorrect Mixing:
- Inconsistent mixing can cause lumps and affect the application. Use a mechanical mixer and follow the manufacturer’s instructions precisely. Incorrect mixing can lead to variations in colour and texture, compromising the overall appearance.
3. Uneven Application:
- Applying microcement too thickly or unevenly can result in an inconsistent texture. Use a trowel to spread the material evenly in thin layers. Applying too much material at once can cause it to crack or not adhere properly.
4. Insufficient Drying Time:
- Rushing the drying process can compromise the finish. Allow each coat to dry completely before proceeding to the next step. Skipping this step can lead to a weak bond between layers, affecting the durability of the finish.
5. Neglecting Sealing and Finishing:
- Skipping the sealing process can leave the microcement vulnerable to damage. Always apply the recommended sealer and finishing varnish. Proper sealing protects the surface from stains, water damage, and wear, ensuring the longevity of the finish.
FAQs About MicroStone
Can MicroStone be applied to both walls and floors?
Yes, MicroStone is versatile enough for use on walls, floors, wet areas, benchtops, and furniture. For more details, please contact your local BDM or Customer Service team.
Is MicroStone easy to maintain?
Yes, it is low-maintenance, requiring only water, neutral soap, and a cloth for cleaning, making it an excellent choice for high-traffic areas.
Is MicroStone suitable for commercial flooring applications?
Yes, please seek advice from your local BDM to understand the slip rating requirements.
Is MicroStone prone to cracking?
No, MicroStone is durable and resists cracking when applied and maintained correctly, ensuring a long-lasting smooth finish.
Does MicroStone remain flexible under temperature changes?
Yes, thanks to its polymer mix, MicroStone remains flexible and does not crack with temperature fluctuations.
How does the top sealer impact the colour of MicroStone?
The type of sealer and finish applied can influence the colour of MicroStone, potentially altering the final appearance.
Can MicroStone be used in walk-in showers?
Yes, MicroStone is ideal for wet areas, providing a seamless finish. However, it is crucial to wait seven days after the final sealer application before using the shower.
How long does MicroStone typically last?
With proper care and maintenance, MicroStone is exceptionally durable and can last for decades.
Which primer should be used on ceramic tiles?
MicroBase is designed explicitly for coating challenging and low-suction surfaces like ceramic tiles, negating the need for material removal.
Can a matte sealer be used with MicroStone?
Absolutely. For a matte finish, we recommend using Rockcote MicroFinish IV Hydrophobic Sealer.
When is mesh necessary with MicroStone?
To enhance durability, mesh is recommended to be incorporated into Rockcote’s MicroBase in all applications.
What colour options are available for MicroStone?
Rockcote MicroStone can be tinted to the range of colours offered. Liquid tints and Oxides can be used to achieve a variety of colours.
Will MicroStone’s final finish vary with different applicators?
MicroStone is designed to allow for various finished styles. Skilled applicators can achieve specific styles, though subtle differences unique to each space may occur. Typical finishes will be smooth, exposed stone or textured.
Is MicroStone suitable for outdoor use?
Yes, when sealed with polyurethane or hydrophobic sealers, MicroStone is highly durable and can withstand outdoor conditions.
For more information on Rockcote’s products, visit the Rockcote Product Page.
Rockcote’s MicroStone range offers a versatile and elegant solution for various surfaces. By following these expert tips, applicators and tradies can achieve a flawless microcement finish that stands the test of time. Proper surface preparation, precise mixing, careful application, and thorough finishing are key to unlocking the full potential of Rockcote’s MicroStone. Embrace these techniques to deliver superior results and elevate your craftsmanship with Rockcote’s innovative products.
Rockcote, with its dedication to quality and service, provides products that meet and exceed industry standards. Their MicroStone range exemplifies excellence, offering a natural stone finish with minimal shrinkage and ensuring a flawless result every time. Whether you’re working on a residential or commercial project, Rockcote’s MicroStone is the perfect choice for creating elegant, durable surfaces. Discover the true essence of luxury and performance with Rockcote MicroStone, and take your application skills to the next level. For more information, visit the Rockcote MicroStone page.