Achieving an authentic aesthetic with traditional stonework
Written by
10 June 2024
•
5 min read
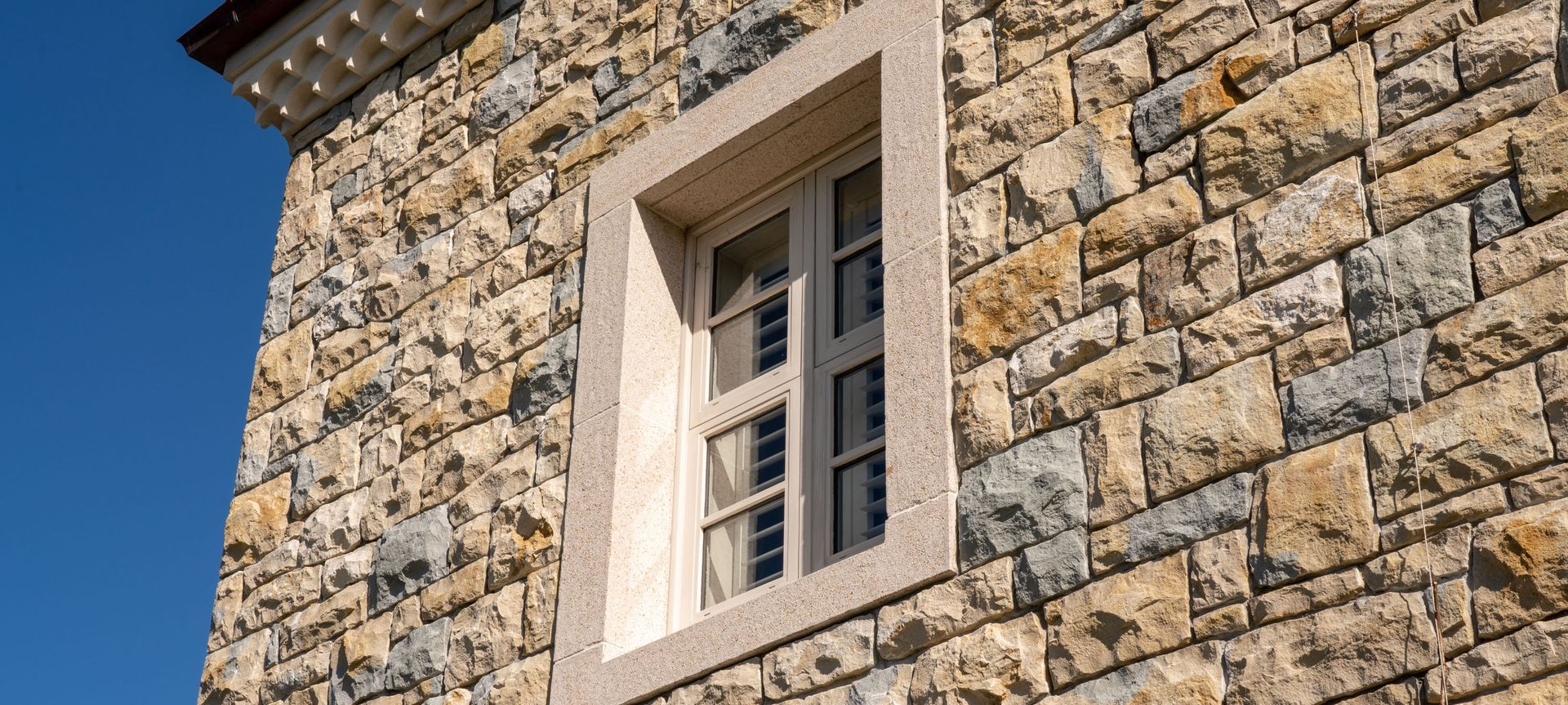
Experts in structural stonework and masters in their field, Auckland Stonemasons has built its expertise from decades of iconic projects, from Auckland’s Tamaki Drive sea walls built in the late 1920s to Cornwall Park and many other residential and public buildings, monuments and walls throughout the country.
It’s a trade that has been honed by the team over many decades, achieving beautiful results – and Len Lavas, managing director at Auckland Stonemans, encourages all architects and design professionals to consider how authentic, solid stonework can be incorporated in residential and commercial projects.
“We build structural stonework that is not reliant on glue or any special products. It holds itself up and even though it’s normally tied to a concrete building, it’s structural within its own right,” says Lavas.
An example is the sprawling French provincial home in Riverhead where architect Peter Diprose engaged the Auckland Stonemasons team.
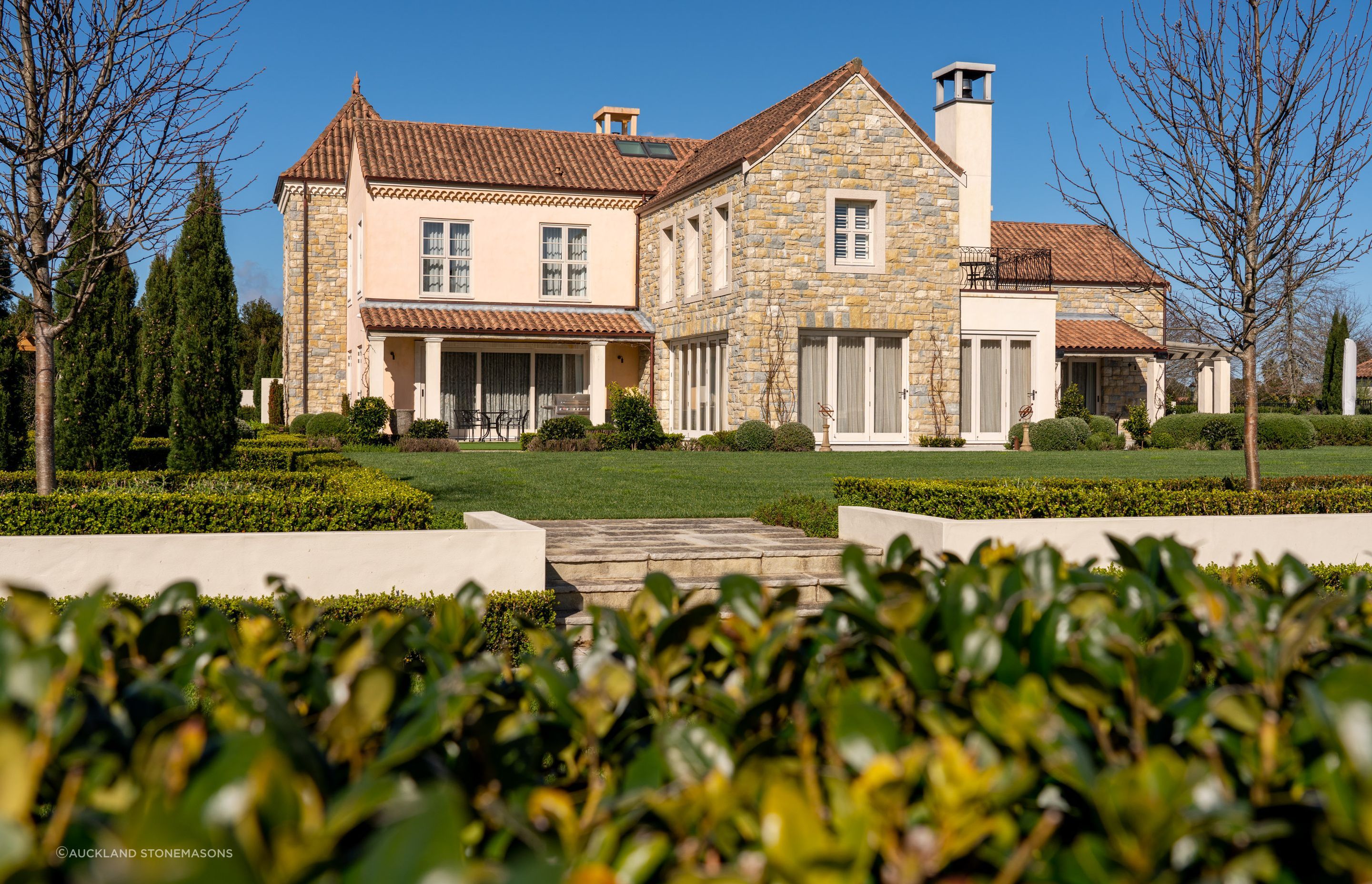
Engaged a year before construction commenced, Auckland Stonemasons ensured the right look and feel would be achieved.
“We had a lot of time with the architect going over the plan with the stone, and it was decided that the stones shouldn’t be too straight or too tight. We wanted it to look imperfect, a little bit rustic, because it adds a lot more character,” says Lavas. “The architect wanted a creamy limestone for that Mediterranean, sun-drenched look.”
A stone from the Te Kuiti lime quarry was selected, a great choice for exterior cladding and retaining walls.

The same approach was taken for Auckland Stonemasons’ recently completed Beachlands project.
The brief called for a modern mix of Te Kuiti limestone cladding for the ground level and timber cladding for the upper level. This combination provided a stunning juxtaposition and an opportunity for the Auckland-based company to show their expertise in working with stone while pairing it with materials outside their specialty.
There was also the matter of ensuring the limestone integrated with the aluminium flashings and the louvre system on the deck. This was relatively straightforward with the stonemasons needing to install flashings that extended through the stone back to the steel frame. “This ensured that when the louvre was eventually installed, there would be no issues. Again, this would have become a huge problem if we hadn’t consulted with the architect first,” says Lavas.
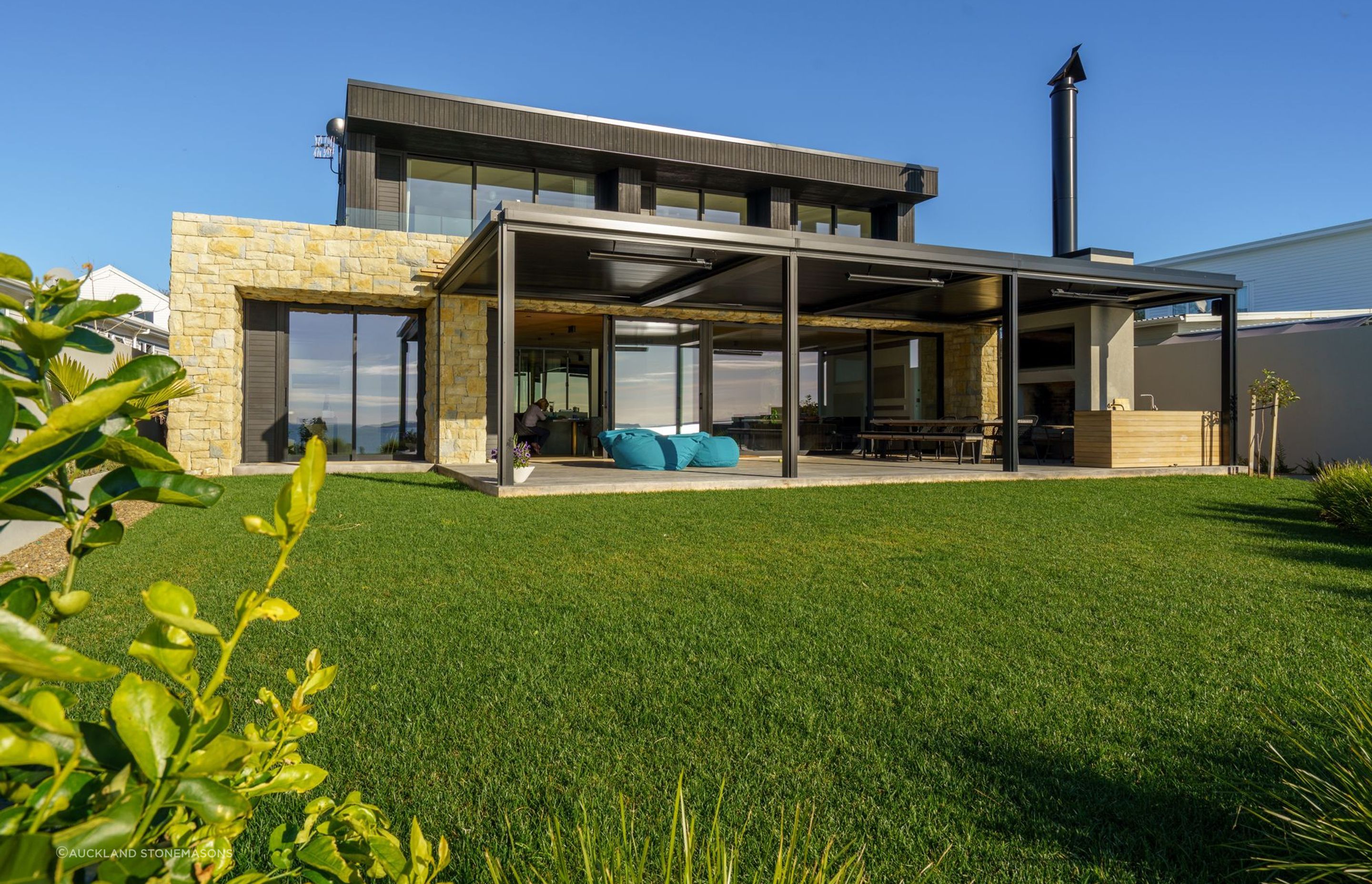
What is the difference between structural stone cladding and stone veneer?
Veneer is manufactured in factories where stone is cut down to approximately 40–50mm thick. “You have to glue it onto the wall. The problem with this is once you saw cut the stone you can’t cut it with a hammer and chisel anymore otherwise it falls to pieces. Instead, you’ve got to cut it with a grinder which creates dust everywhere which can lead to silicosis,” says Lavas.
Traditional in their approach, Lavas and the stonemasons under his employ at Auckland Stonemasons use a hammer and chisel, instead of mechanical grinders, to cut stone down to the right size – not only for its increased precision but also its efficiency.
“It’s very easy to cut too much off with a mechanical grinder, and this happens all too often if stonemasons and architects aren’t aligned on how stone exteriors will factor into the wider design of residential projects.”
The solution to this is simple: engaging knowledgeable stonemasons before the design process begins.
“The main problem I see is people coming to us to work on a stone house, but it’s already been designed and consented and we can’t do it because the architect hasn’t consulted with us,” says Lavas.
This can often lead to issues such as not being able to put in cavities.
“Cavities in New Zealand are very important, and you can’t put in a cavity with stone veneer – you need to glue it to the concrete blocks or concrete house and water pressurises. If there’s any failure whatsoever in the waterproofing, the house will leak. Whereas if you’ve got a cavity, the water runs faster and it can breathe.”
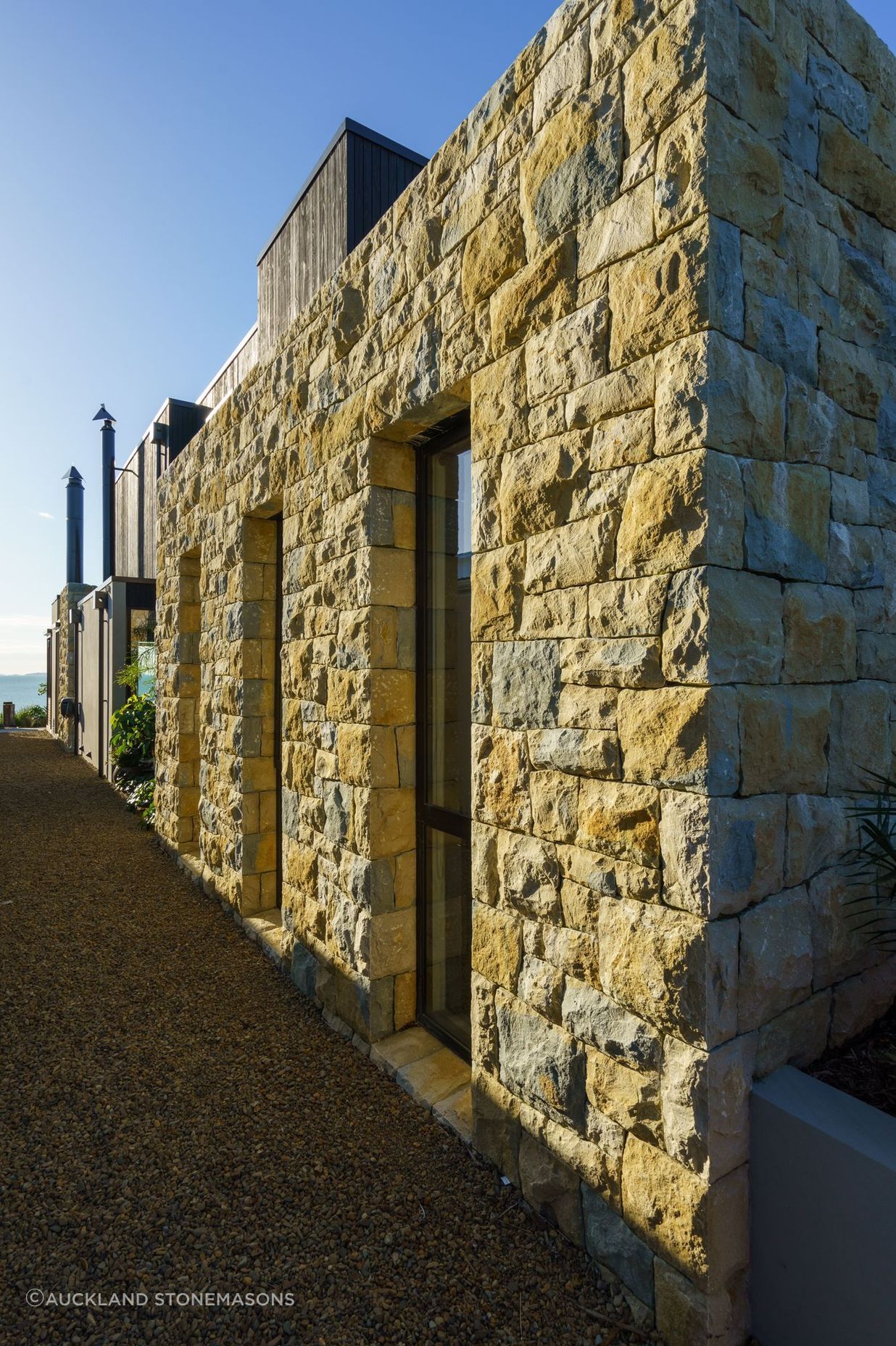
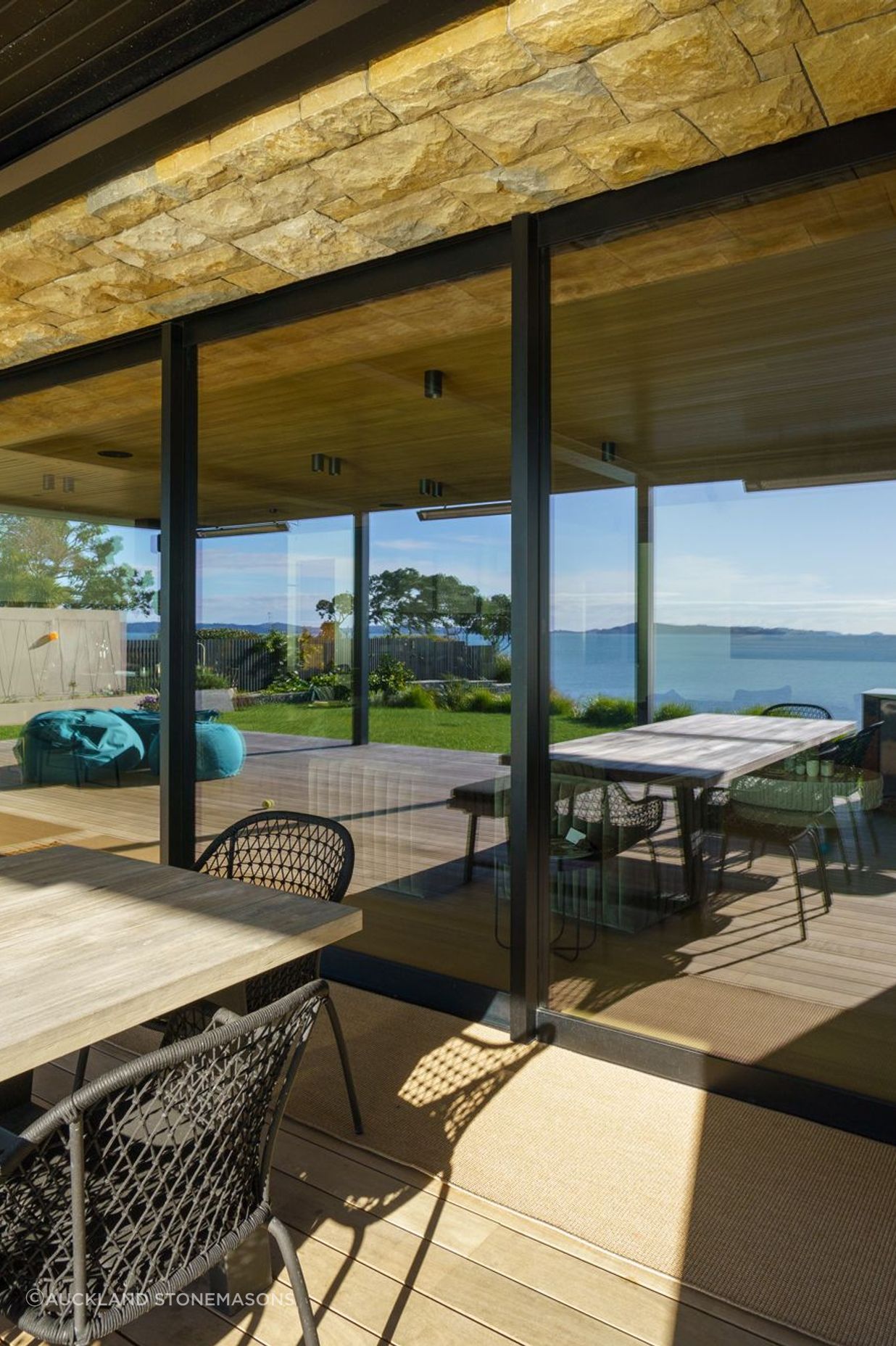
Another common misconception is the price associated with specifying solid stone, says Lavas.
“The only difference is you need good foundations for proper stone. Labour is also reduced as a lot of the old ways of cutting stone are actually faster. It gives you more precision – but equally important is the fact that if my stonemasons use the grinder all the time, they’ll lose their trade and they won’t be effective stonemasons anymore.”
Before you embark on your next project design, get in touch with Lavas and the team at Auckland Stonemasons to learn more about traditional stonework.