Avoid concrete floor disasters – 5 key concepts for designers & specifiers
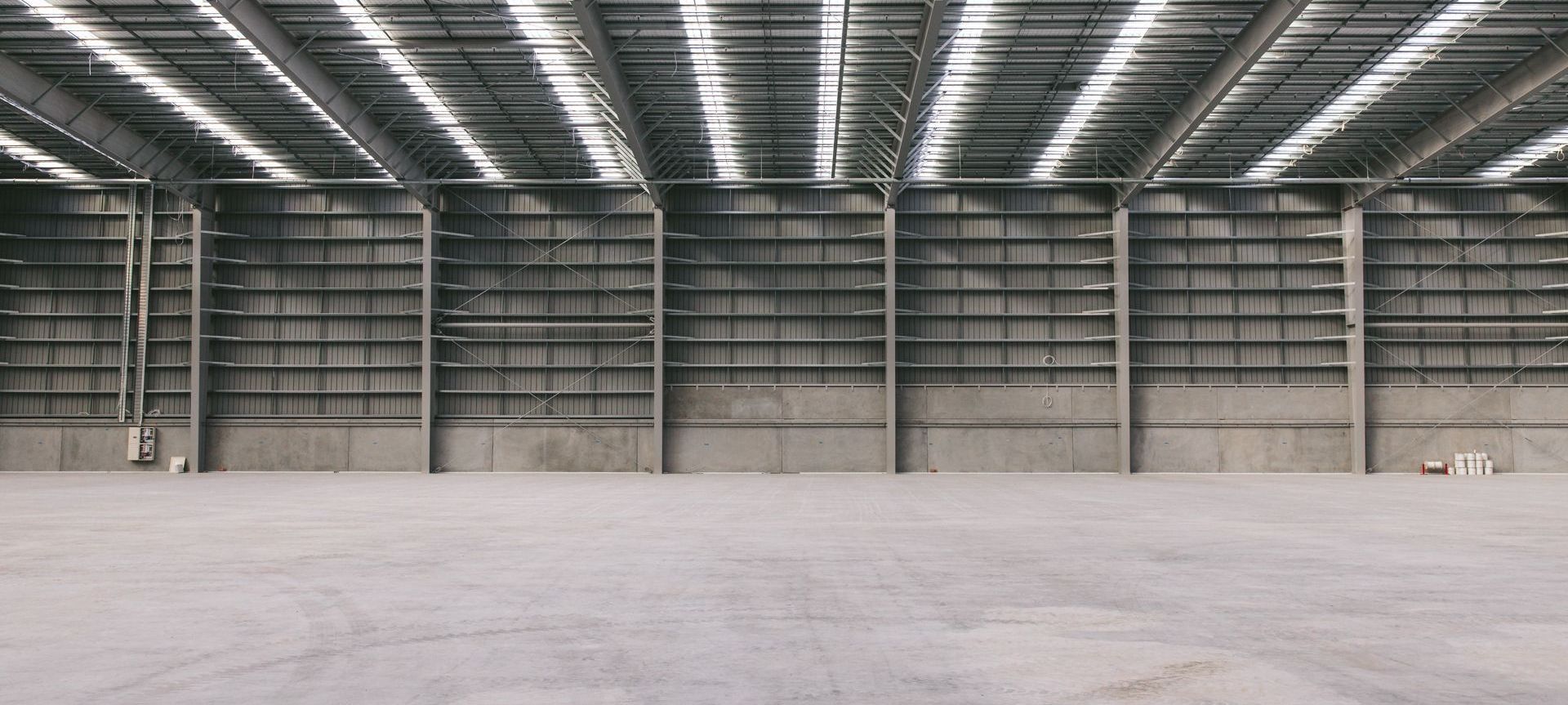
The concrete floor is one of the most important components of a modern warehouse. The floor is the working surface on which pallets are stacked, forklifts are operated and racks are installed. A favourite saying in the industry is “if we have a good floor and the roof doesn’t leak then the project will be a success”. Unfortunately, time and time again clients are being let down when it comes to their floor – delamination, cracking, flatness issues, soft and dusty surfaces – the list goes on and on. The following list is a cheat sheet for designers & specifiers to consider for their next industrial flooring project.
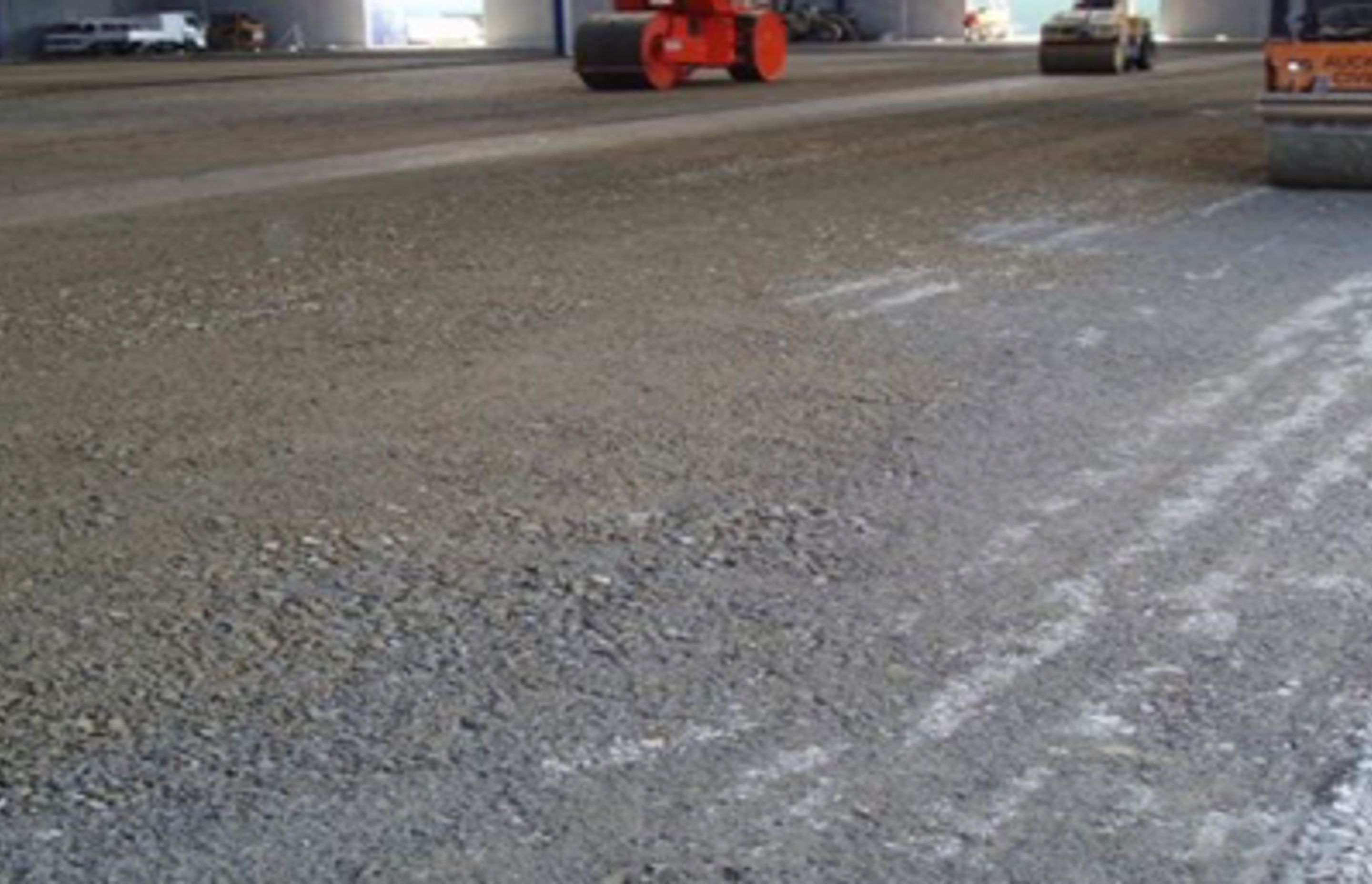
1. Understand your ground Conditions
This one might seem like a no-brainer but very often I get asked to visit a floor that has “sunk” – sometimes by over a metre. Why? Because no one took the time to understand or address the geotechnical conditions on the site. There are two options for supporting a concrete floor – if you have good soil conditions and won’t have consolidation or subsidence the floor can be ground supported. This may require some ground improvement work and you should always install a sub-base to act as a working platform. But what if you don’t have good ground conditions? You need to pile support your floor. Sometimes this can come as a nasty surprise to the developer because it will more than double construction costs. But the alternative is ploughing money into an asset that will likely need replacement within 3 years – it’s not a gamble worth taking. Get a geotechnical investigation underway as soon as possible so that you can get your design right and avoid nasty surprises.
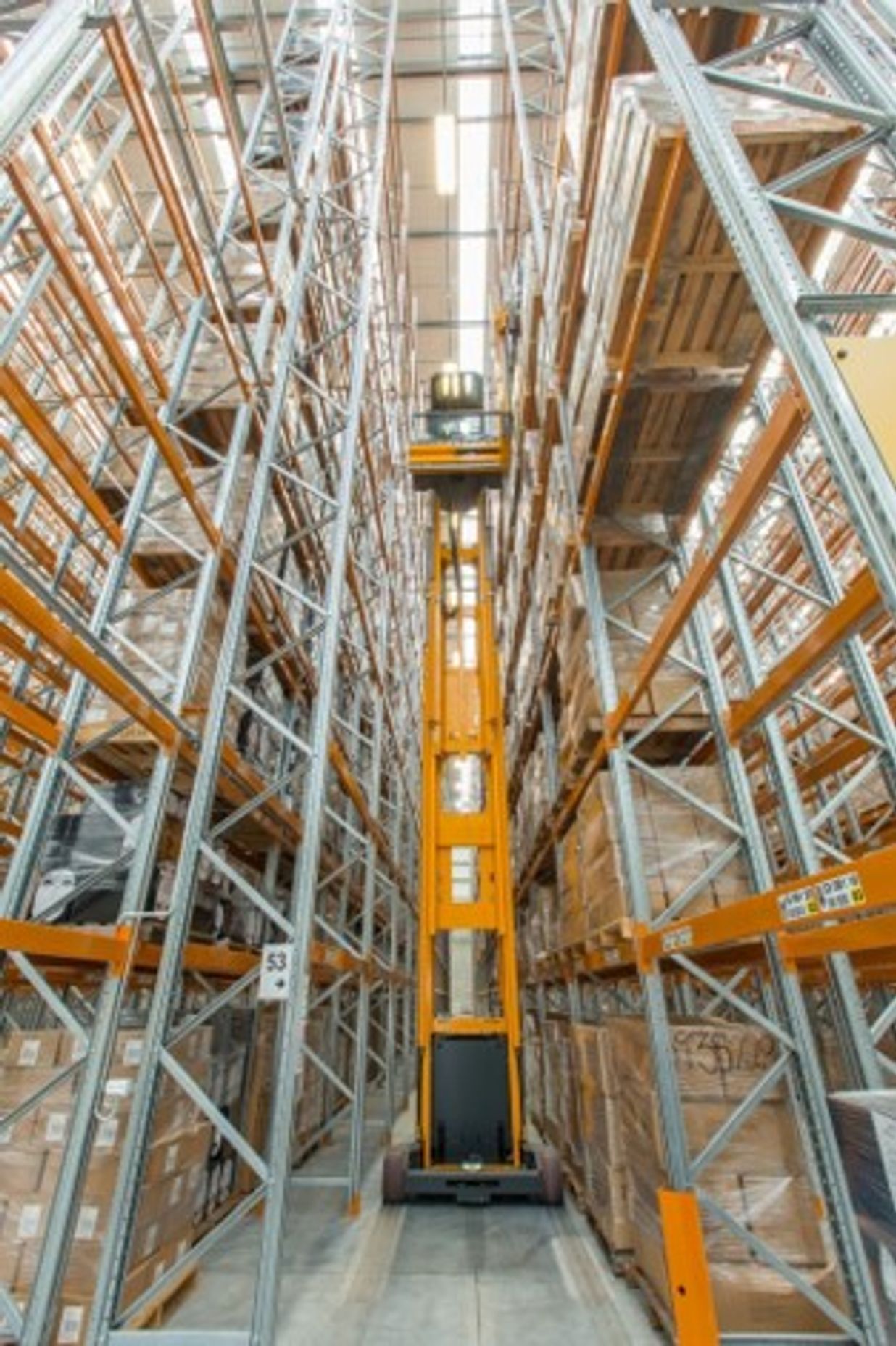
2. Co-ordinate with the tenant project team
This might seem like another no-brainer but time and time again we see a lack of collaboration between property and construction people and the the tenant project team – forklift and racking suppliers in particular. The floor is the key working surface that all of the expensive forklifts and racks will work on. It’s crucial to get the right information because if you don’t you can be left with a big headache. The logistics systems being used in the building will define the loading criteria – if you get this wrong the floor might be under designed. But just as importantly they define the surface regularity requirements – what people commonly call "floor flatness". Maybe back in the days of low level pallet racking or bulk storage this wasn’t such a consideration. But we live in a world where a 12 m high SPR system is considered blasé and more and more facilities are adopting semi-automated Very Narrow Ailes (VNA) systems and fully automated ASRS. This places big demands on the floor flatness – a difference in level of more than 2-3 mm across the aisle can cause the system to fail. To put that in to context that's 5 to 10 times the thickness of a business card being the different between success and failure.
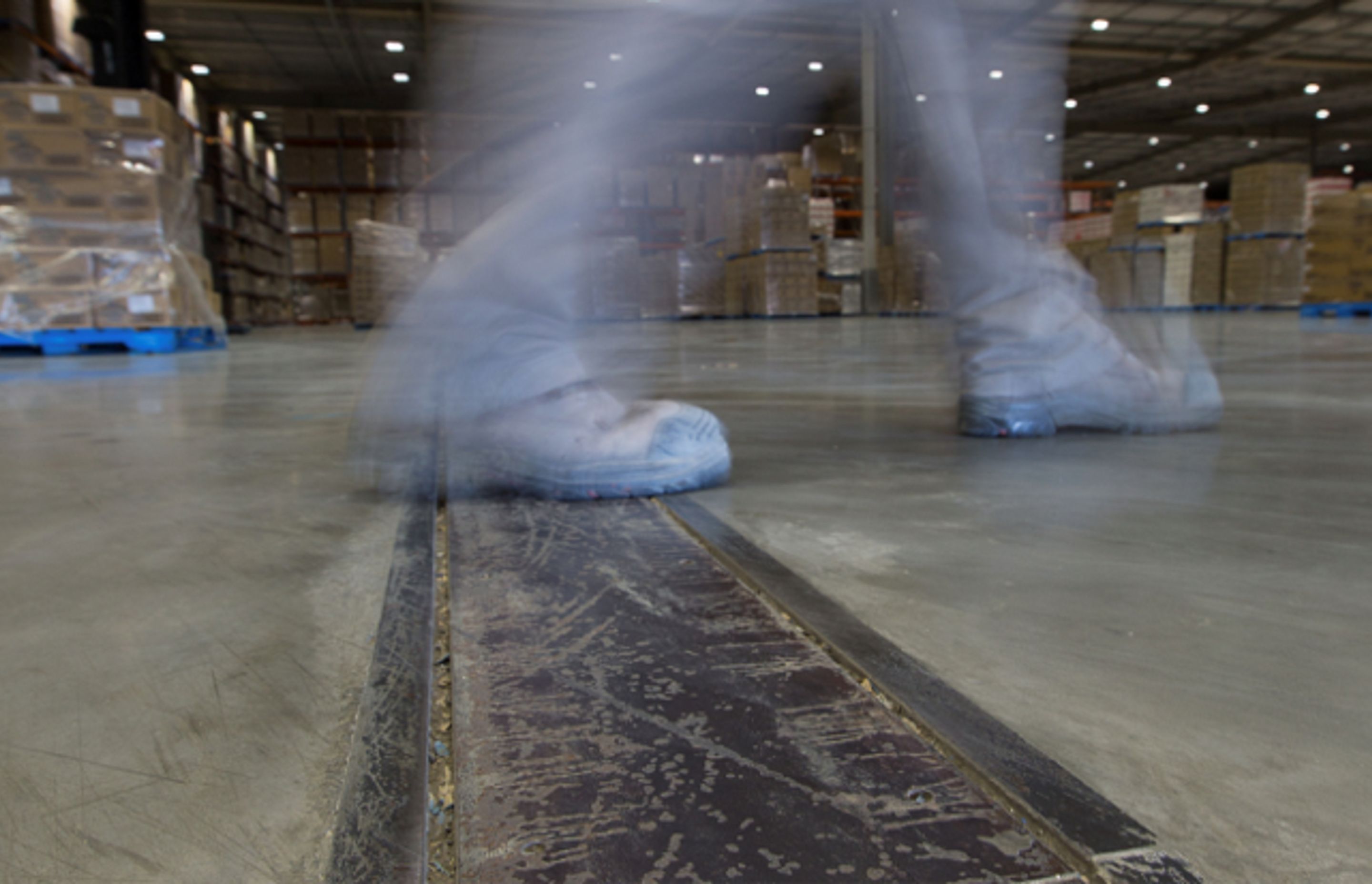
3. Design for long term serviceability
Did you nod your head when I mentioned that the floor is one of most important part of a logistics facility? The working platform for material handling? Well unfortunately floors are often designed by structural engineers using the same serviceability criteria they would use for foundations. Foundations that no one will ever see and that will not have hundreds of thousands of forklift movements across them. Floors should be designed to remain in a good serviceable condition throughout their life provided they aren’t overloaded or abused. That means focusing on minimizing and eliminating cracking, making sure joints don’t spall and having a hardwearing and abrasion resistant surface. If you get these items right you avoid 99% of the maintenance problems that will occur over the floors life and give the owner a floor that will be cost effective to maintain and will attract blue chip tenants. This means designers need to undergo a shift in mind-set. Generally speaking you should be minimizing and eliminating restraint - not using the floor for lateral loads and isolating it from the rest of the structure like pile caps or columns. The floor should probably be thicker than you would have designed otherwise because you want additional stiffness to reduce the chance of surface cracking from deflection and rotation. It means ensuring a good accurate sub-base to cast the floor on. It means steel edge armour joints to prevent joint spalling. And it means you should be looking at using modern design methods like post-tensioning and steel fibre reinforced concrete to allow large joint free and crack free panels.
4. Don’t get too clever with your concrete mix design
Concrete is the 2nd most used material on earth after water. It’s the critical material in a concrete floor and you need to get it right if you want your floor to be a success. But there is a very very high probability that you are not an expert concrete technologist. So please don’t be too prescriptive when it comes to the mix design for your floor. It might seem like a great idea to limit the w/c ratio to 0.40, or the slump to 60-80 mm, or to prescribe a low drying shrinkage limit. But taking this sort of approach will not help you get a better floor - in fact it will probably make the floor worse. The key concept to understand is that every concrete plant you visit in every corner of the globe is a unique operation relying on the locally available materials. In order to produce a good floor we need to manage the characteristic strength, workability, initial and final set times, bleed rate, and have a suitable grading to get the paste required for finishing. Putting arbitrary limits on workability, water cement ratio or shrinkage can make this difficult or impossible – leave the specifics of the mix design to an expert so they can make the best of the local materials that they encounter.

5. Engage a specialist contractor
You’ve worked out your ground conditions and made the right choice between a pile supported or ground supported floor. You’ve got detailed information from the tenant and have the design loads locked in. You’ve specified the right flatness standard based on a world leading document like ConcreteNZ TS01:2021. The design considers long term serviceability and you are confident you’ll minimize cracking and avoid issues at joints. And maybe you even involved an expert in concrete technology to optimize the concrete mix design. What could possibly go wrong?
Everything.
Even with best practice in design, specification and planning if you have a bunch of unskilled labor show up to prep, cast and finish your floor it will still be a disaster. If you want to produce a high performance floor you should use a professional contractor. They should have a lot of experience in the type of system you are using and evidence of having achieved the flatness results and abrasion resistance you want. And they should have modern equipment like Somero Laser Screeds.
If you found this post interesting I’d recommend you pick up a copy of the UK Concrete Society TR34 – Concrete Industrial Ground Floors. It provides a proven template to design, detail and construct high quality floors and is a great starting point for anyone struggling to get the results they want. And feel free to contact the Conslab team if you have an industrial flooring project or query you'd like to discuss in detail.
Article by Tim Walker - General Manager Conslab Ltd