A gorgeous spiral staircase with a bent glass balustrade shines in luxury French fashion house fit-out
Written by
24 September 2024
•
4 min read
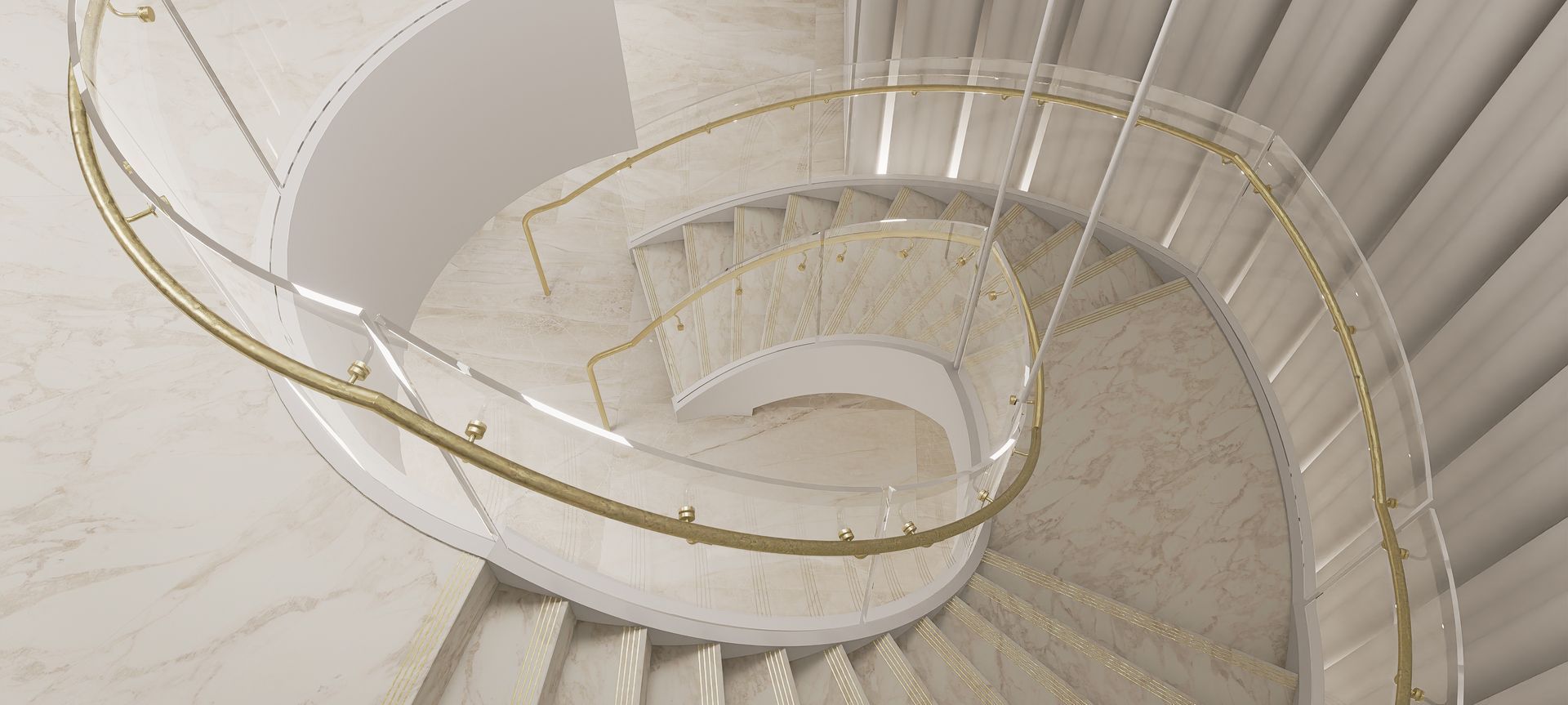
When designing the new Australian headquarters for a luxury French fashion house, every detail — from the flooring to the balustrades — needed to be perfect. Engaged to deliver an elegant, bent glass balustrade for the office’s grand spiral staircase, Active Metal contacted Glasshape, their trusted supplier for high-end glass.
“The brief called for quality, toughened and laminated bent glass balustrades to be delivered in a timely manner for a high-end office fitout,” says Brendan Forrest of Glasshape. “Active Metal reached out to us because we have a proven record of delivering glass pieces where both quality and timing are crucial to the project’s success.”
Entrusted with the task of delivering an element so crucial to the office fit-out, Glasshape got to work doing what they do best: crafting beautiful bent glass features.
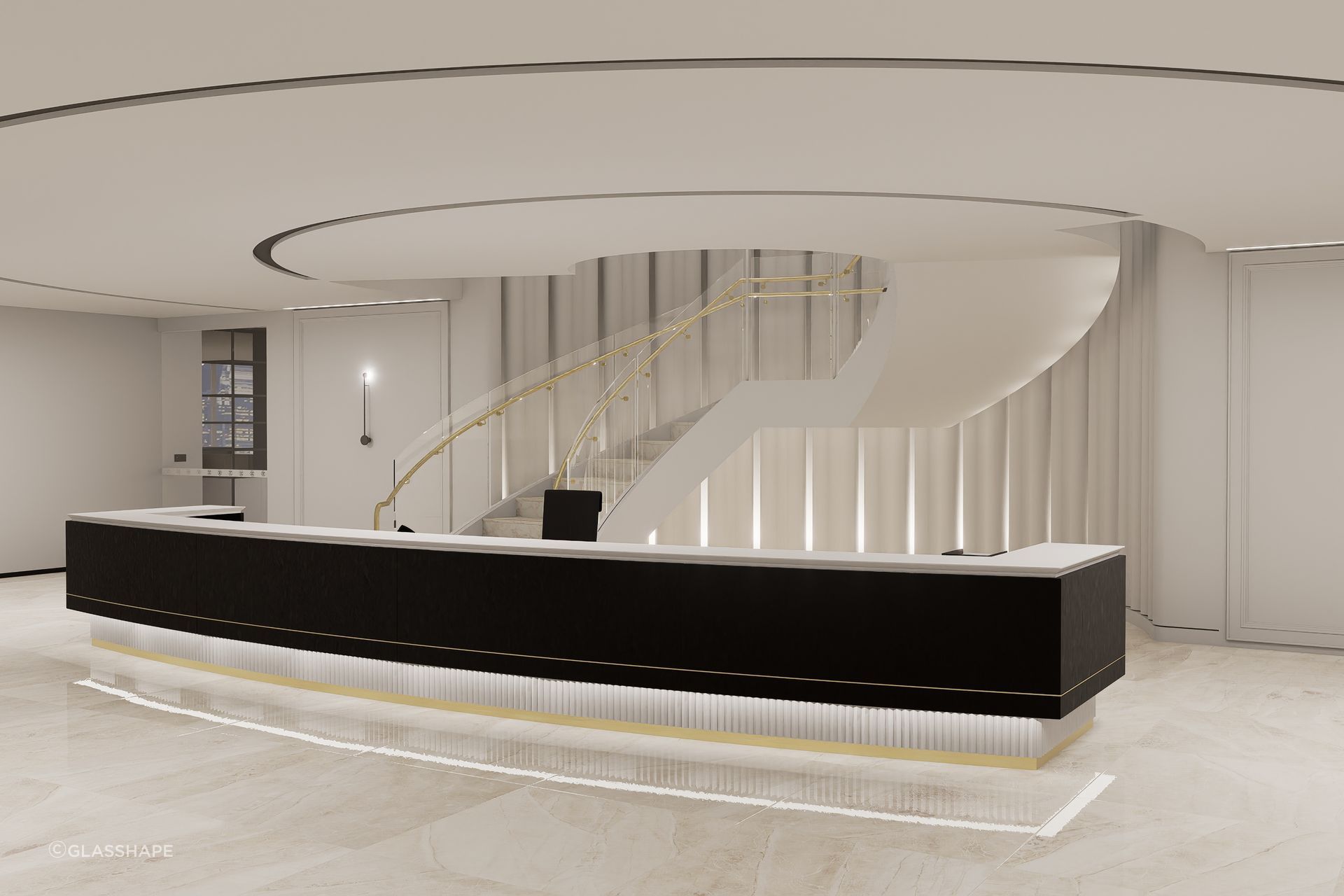
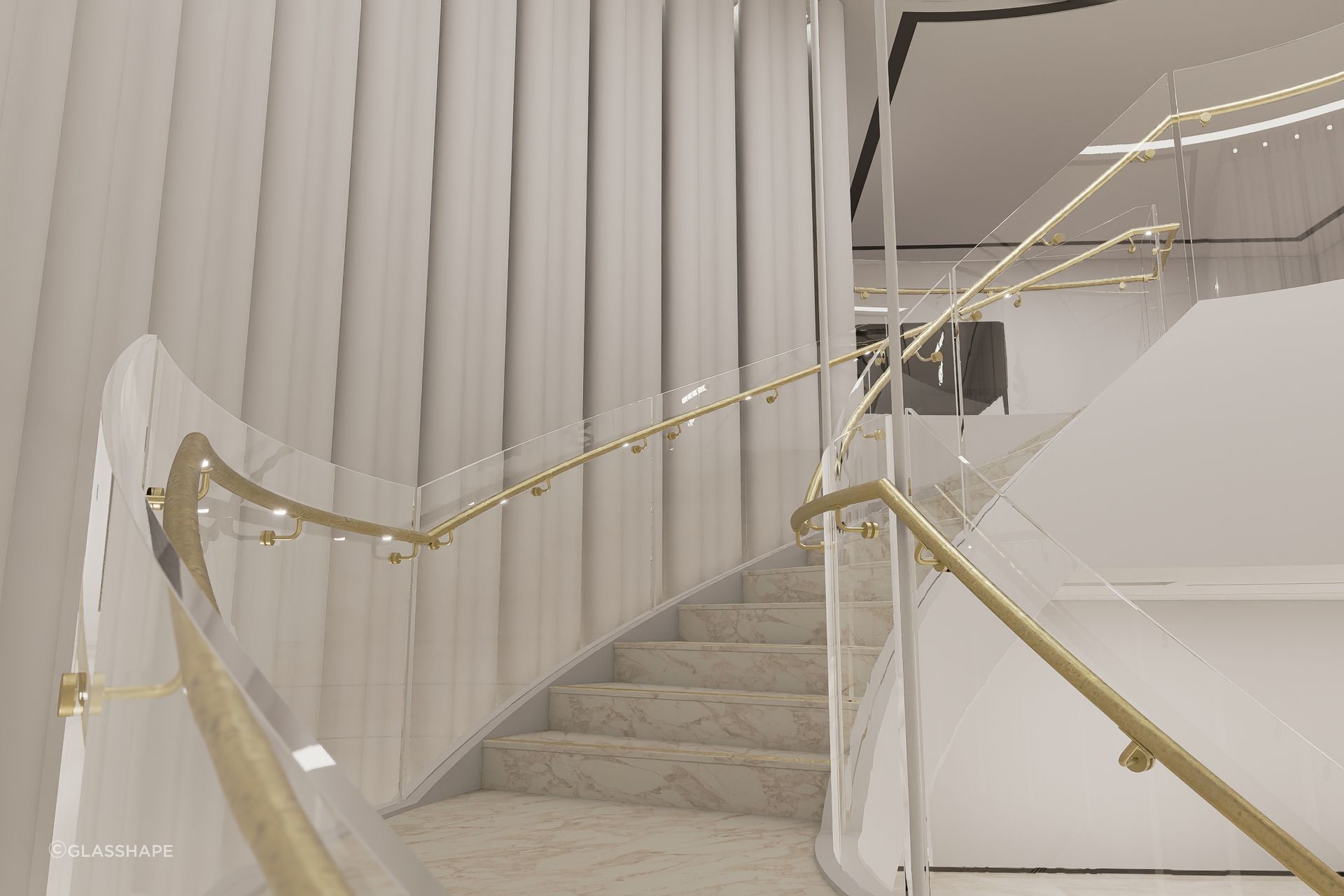
Bending the balustrades
Once the brief had been accepted, Active Metal sent the Glasshape team a series of shop drawings detailing the specifics of the balustrades.
Typically, to ensure the glass fits the stair structure, the client or a member of the Glasshape team will usually visit the site to measure the stair structure in place, and determine the required glass sizes and fixing positions within the glass panes.
“Glasshape’s digital site measure service is very popular as we take full responsibility for the site measurements digitally, removing the risk and hassle for the client having to make and rely on physical templates. In this particular case, the client provided Glasshape with the pre-measured sizes and it was a matter of Glasshape preparing machine files for the various production processes,” Forrest explains.
The first step of the glass production process requires the glass panels to be cut out of stock sheets with a CNC machine. Once the panels are cut, their edges are polished and holes for fixings and handrails are drilled in. The glass panels are then processed through the toughening and CNC bending furnace to produce the desired shape. Finally, the glass panels are matched with their partners and laminated.
“Our design and production teams worked closely together to produce superior quality glass that matched the shop drawings. While the balustrades were under construction, our dispatch team worked closely with the freight forwarder and shipping lines to ensure the shipping schedules would align with the production timeline. This collaboration was key as it would ensure that the client would receive the glass with enough time to install before the project deadline,” Forrest says.
Before the glass leaves Glasshape’s factory, it is securely packaged into custom wooden export crates. It is then taken to the freight forwarder’s yard where the crates are loaded into a shipping container, or delivered to the airport where it is air-freighted to the destination port.
“Once the glass clears customs, our freight forwarder will arrange collection of the crates from the port and deliver according to the customers’ requirements. This could mean delivery to their store or a hiab delivery directly to the building site.”
When the glass arrives on site it is installed by professional glaziers. For this project, the glass was grout fixed onto a custom channel and then attached to the stair stringer. The installation process takes place towards the end of the project — once the stair structure is in place and other finishes have been installed —to protect the glass from any damage.
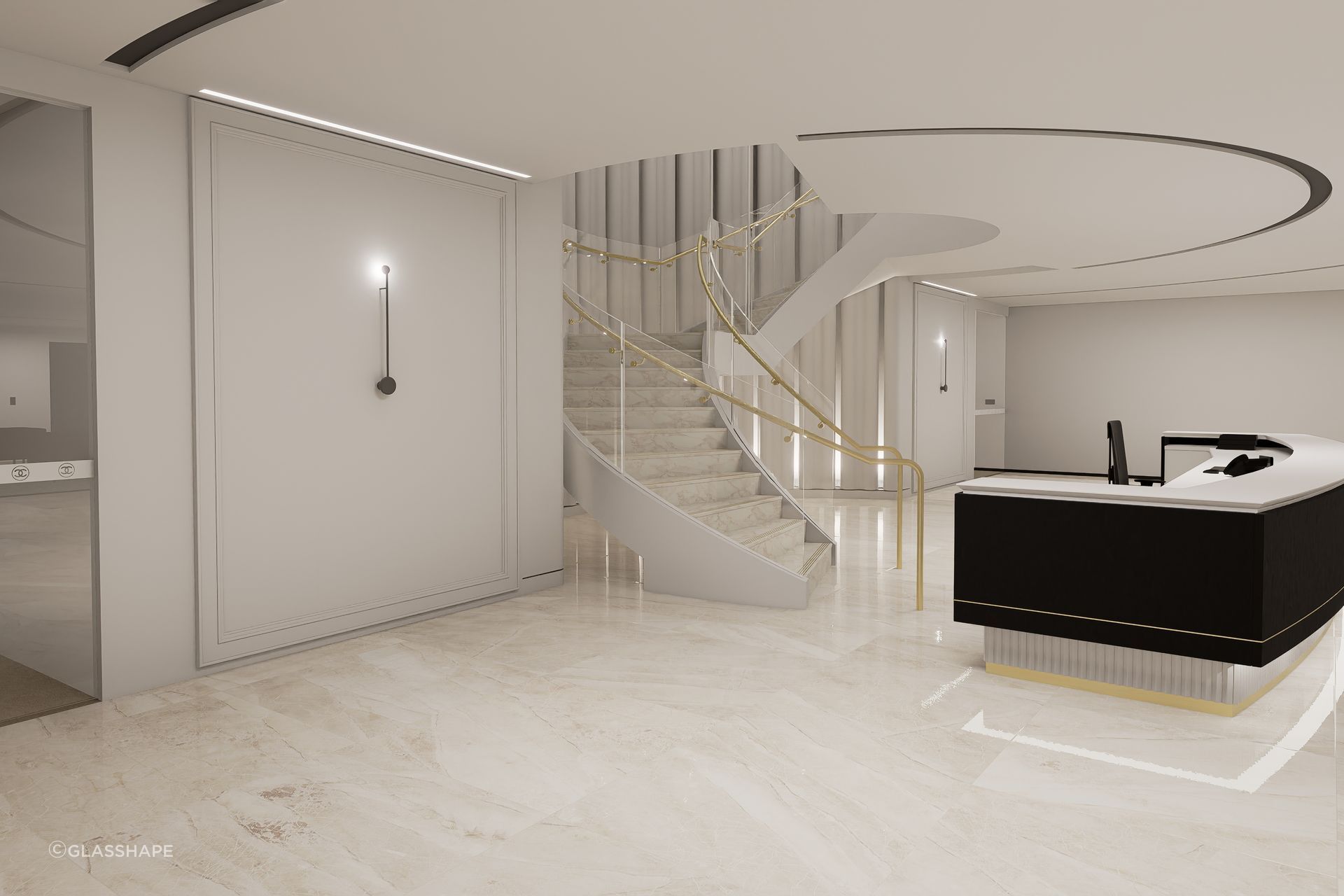
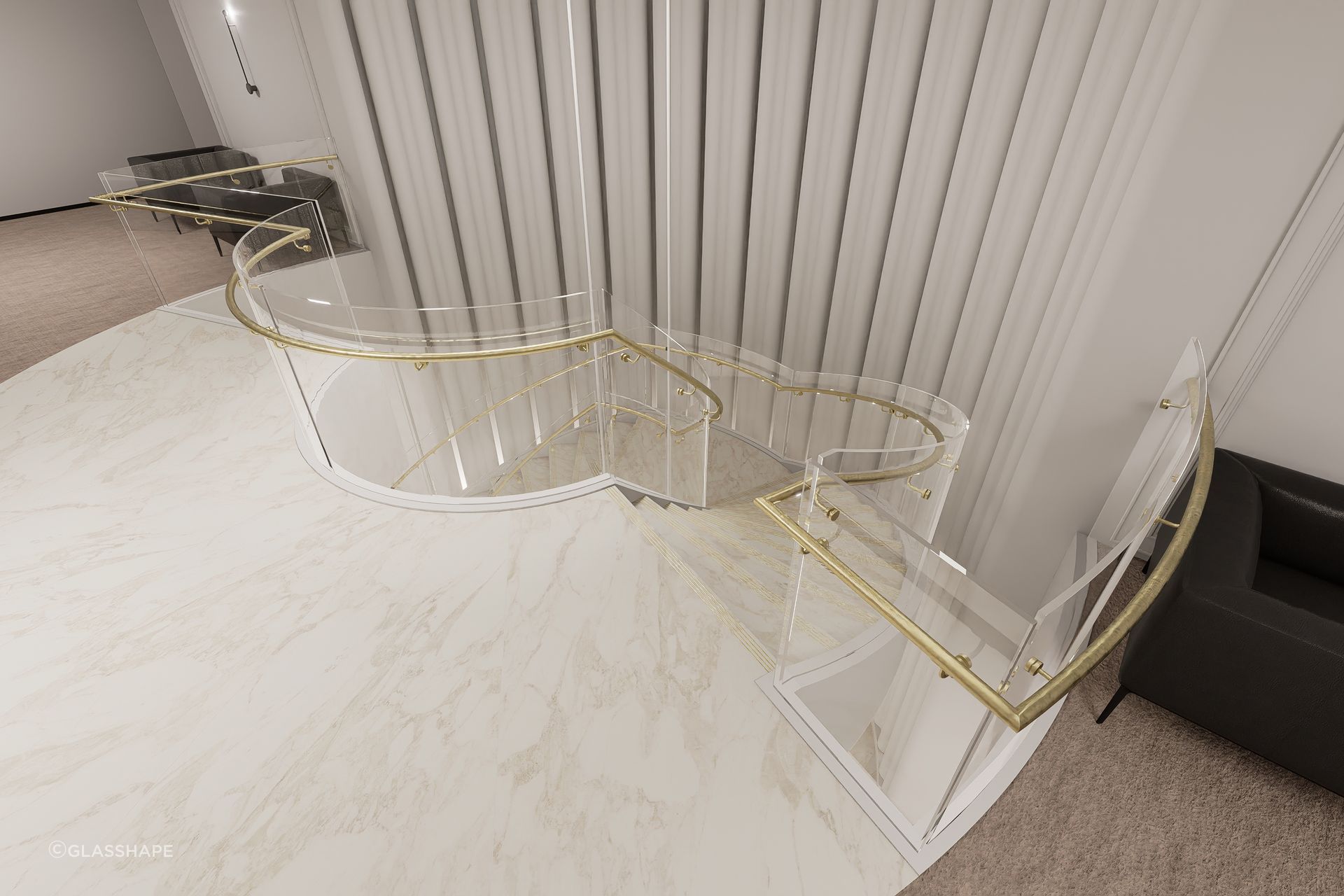
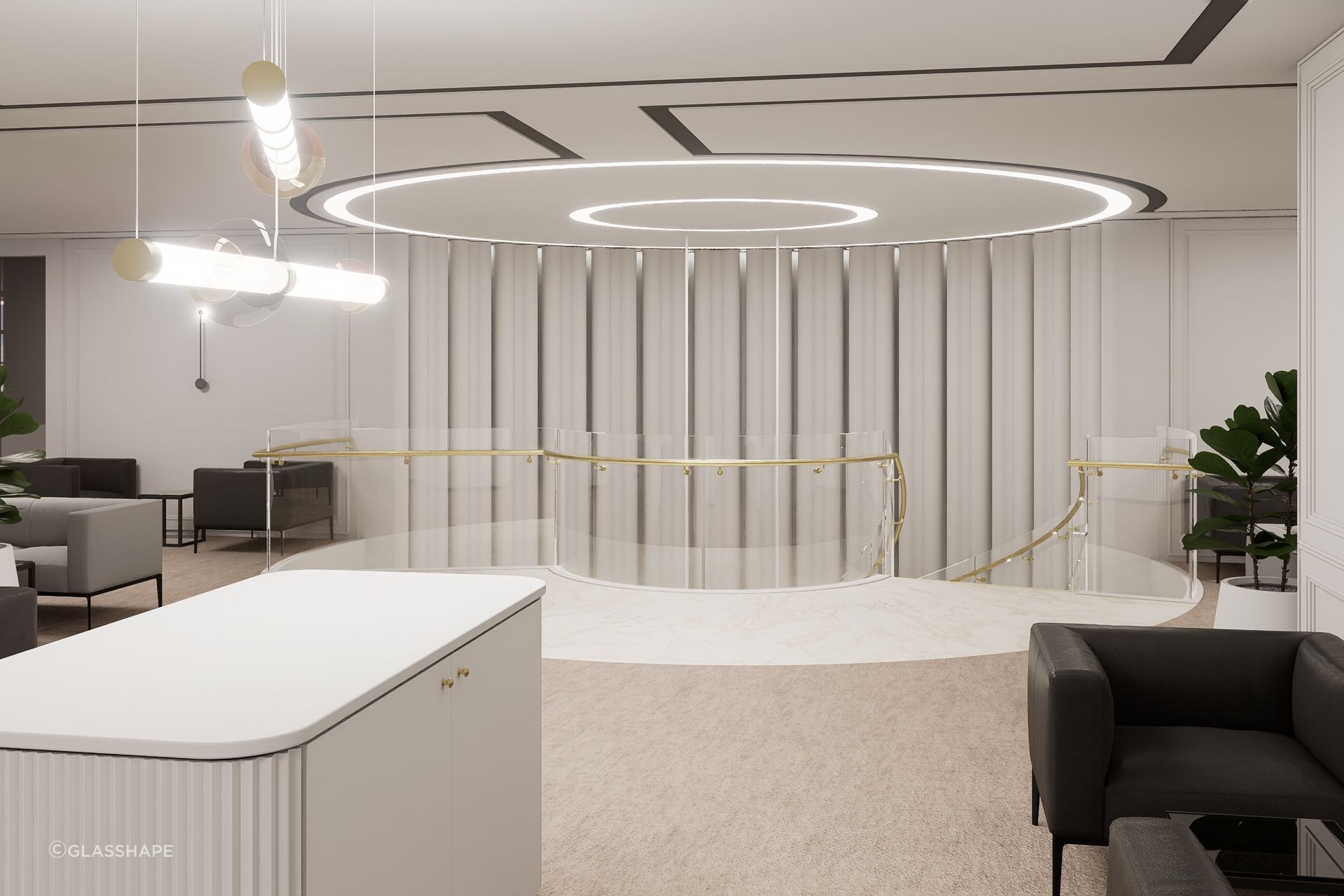
Navigating challenges with ease
“This project was a breeze as it's exactly the type of high-end project Glasshape is set up to deliver,” Forrest says. “The most challenging part of these kinds of fast turnaround projects is always the part we have little or no control over: the shipping. We are bound by shipping schedules or the number of flights to the destination, which can be tricky.”
To ensure the delivery runs smoothly, the Glasshape team maintains close relationships with multiple freight forwarding companies so that, regardless of the brief, they always have a variety of transport options to choose from.
“Our shipping and delivery conversations usually begin before commencing the glass production so we can ensure the production schedule meets the cut-off for the very best shipping options available.”
Glasshape is extremely proud of its reputation as a manufacturer of high-end bent glass.
“It’s an immense privilege being selected by contractors and fabricators as the trusted partner for very high-end projects such as this. It goes to show we really do live and breathe our motto: delivering bent and specialist glass with excellence.”
Learn more about Glasshape.
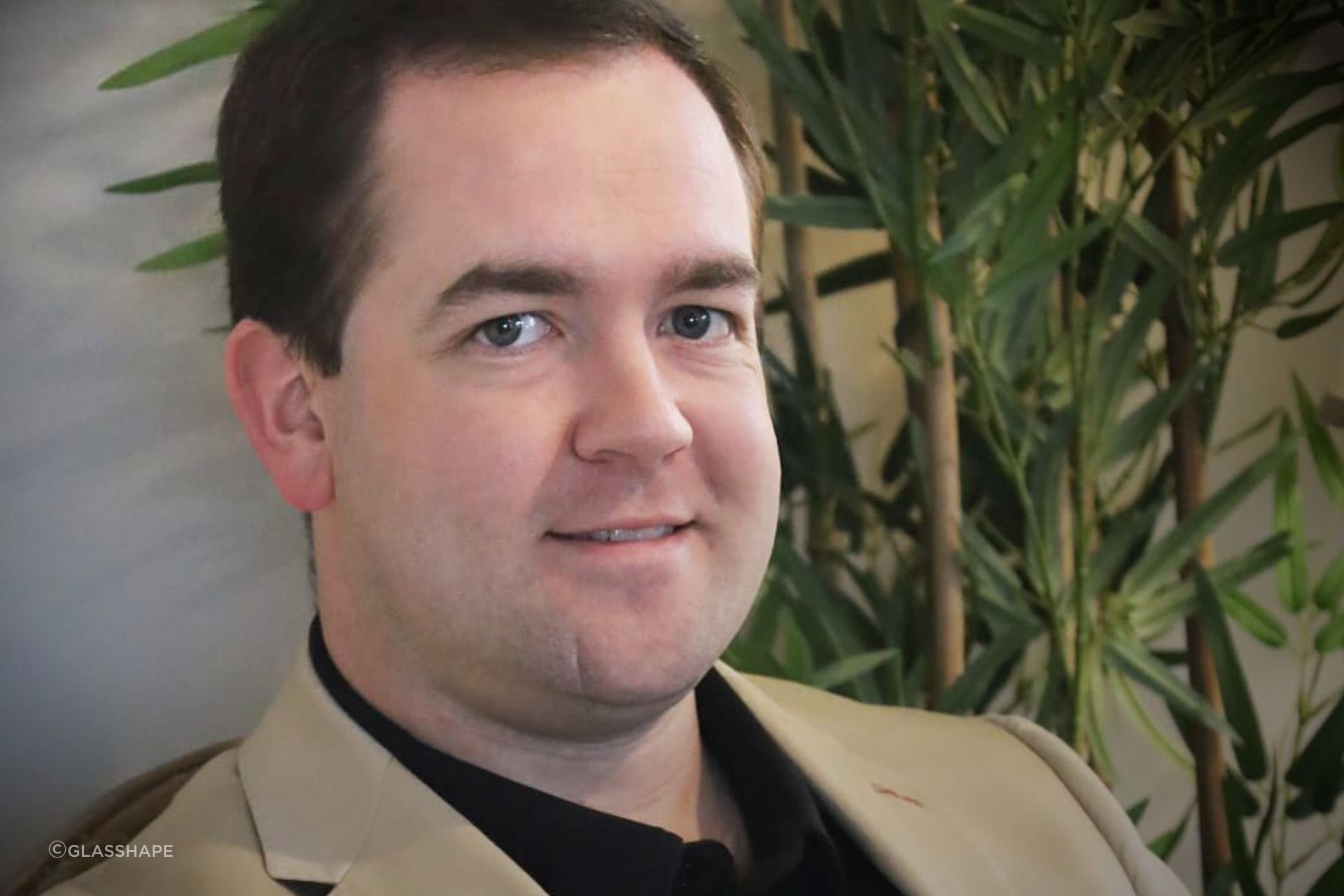