In 2023, New Zealand’s Building Code overhauled the H1 clause, introducing new climate zones and higher insulation standards. However, subsequent to this change, concerns were raised about overheating and higher moisture levels in homes with increased insulation, and a disproportionate increase in the cost to build relative to the performance. This prompted a review by the MBIE, which found these concerns to be a result of poor design – including building orientation, ventilation, window shading, and heat absorption properties of building materials – rather than increased insulation.
“The proposed changes now are focusing on simplifying the way we insulate our homes and overall, reducing costs,” says Cameron Brooks, Special Project Manager at EXPOL.
EXPOL manufactures and distributes solid insulation and lightweight polystyrene construction solutions to keep buildings warm, dry, and comfortable. With the potential changes to the H1 code for insulation, EXPOL has been reviewing its offering to help builders, architects and homeowners make informed decisions.
The current H1 energy efficiency settings for new builds segment the country into six climate zones with R-values based on cooler and warmer climates. The schedule method is also one of the three allowable methods of establishing the insulation requirements for a project. However, MBIE is proposing the removal of the prescriptive schedule method and adjusting the minimum R-values for roof, wall, and floor insulation.
“At EXPOL, we’ve done two things. The first has been getting on board and getting involved in the consultation process to provide the MBIE with our feedback. The other has been looking at the calculation method and how we can help people achieve the same desired result while also finding ways to reduce the cost to build, which is one of the desired outcomes of the proposed changes,” says Cameron.
According to the MBIE, “the calculation and modelling methods enable a designer to better consider the building as a whole, rather than as a series of individual components, and have been shown to reduce up-front costs as much as $15,000.”
After some modelling and looking at different levels of insulation, EXPOL concluded that it’s difficult to make changes around wall insulation, but there are potentially significant cost-savings available by shifting insulation from one part of the build to another.
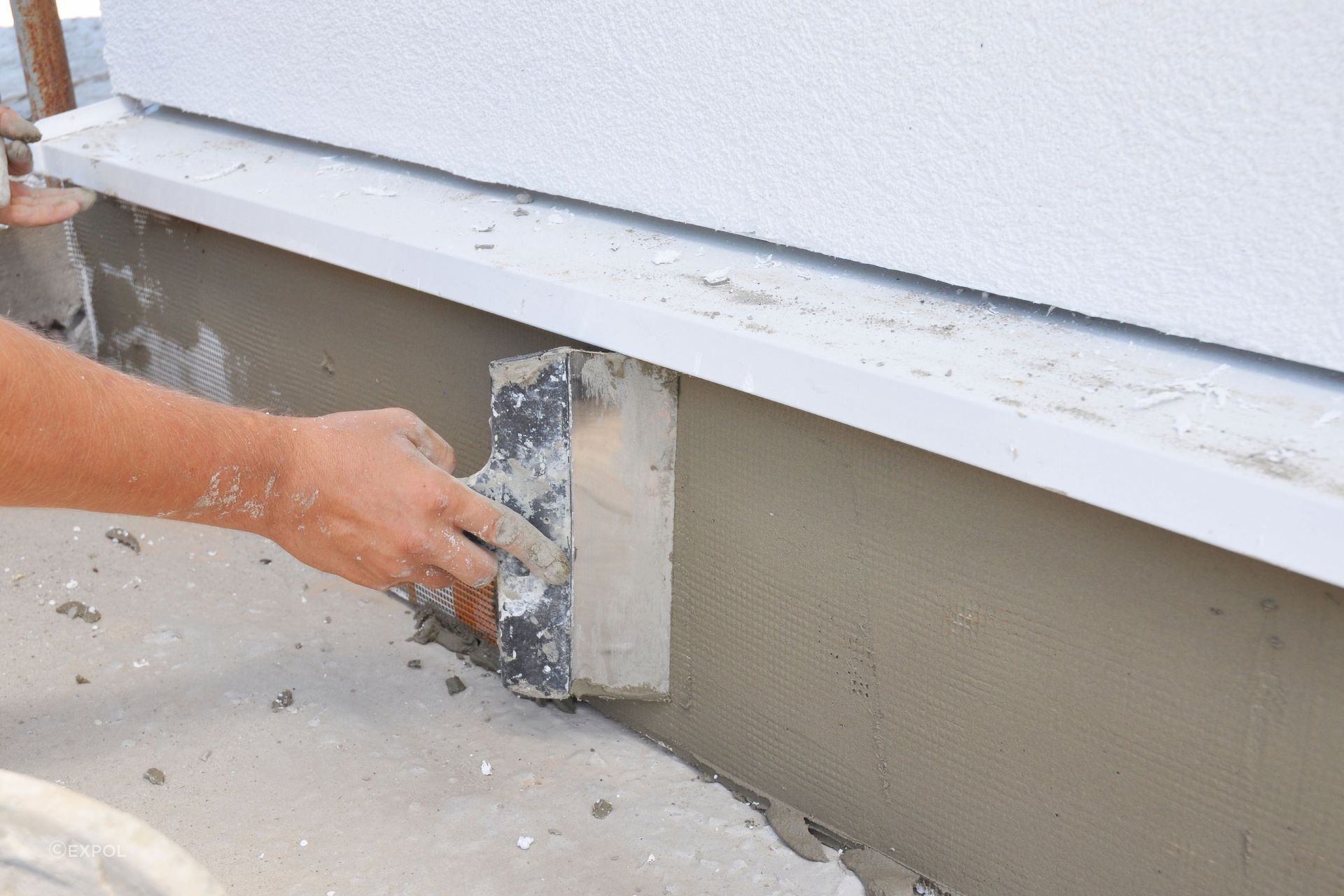
“What we’ve seen is that in terms of achieving the thermal resistance required, there can be a big cost reduction in moving insulation out of the roof and putting it into the slab,” says Cameron. “The modelling that we’ve done still allows the minimum R-values to be met in the roof, and those R-values still exceed the R-values that were required before the legislation was changed, so it’s not a huge historical departure.”
This also keeps in line with traditional construction methods.
“Once your slab is insulated, it will perform at that standard for the entire life of the building. Also, if we’re shifting insulation from the roof into the slab, that doesn’t prevent homeowners from being able to add further insulation to the roof at a later date if they want to increase the performance, as opposed to a slab. Once a slab is down, it is effectively impossible to retrofit any decent level of insulation.
“We’re encouraging architects, designers and builders to think about the way they use the calculation method and not only take into account achieving the requirements of the Building Code but also take into account how effective the insulation is for the money that’s spent.”
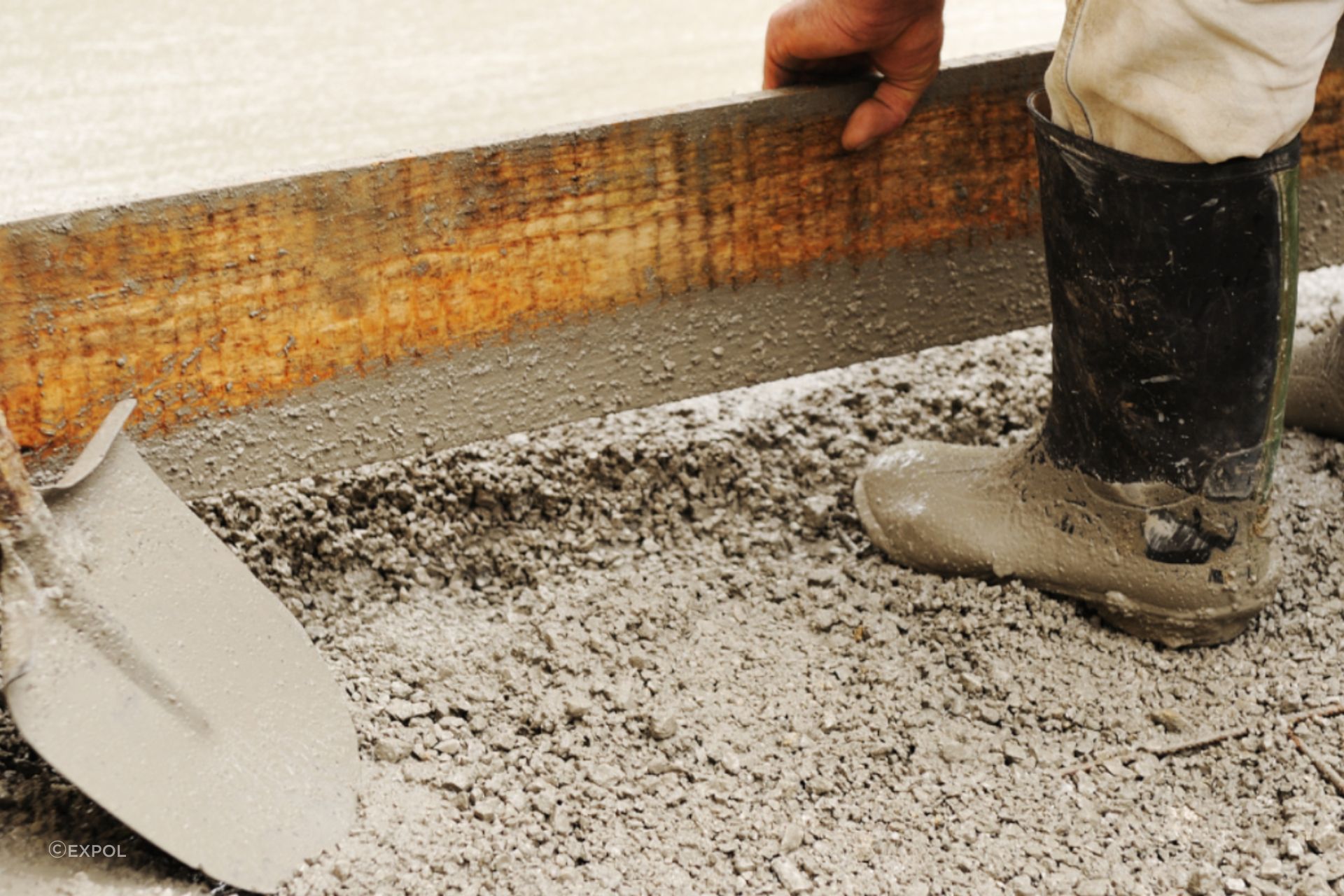
Making it easy to determine the right R-values for projects using the calculation method, EXPOL has a set of tables that show the different area-to-perimeter ratios, the different R-values that can be achieved with those ratios, and what the result is when adding or taking away different products.
There are also other benefits that result from improving a slab’s thermal performance. Research undertaken by BRANZ in 2021 showed that if a slab edge is effectively insulated, walls can achieve a 30 per cent to 40 per cent increase in thermal performance compared to a home with no slab edge insulation.
“Essentially, there are three ways you can increase the performance of a slab – with the use of waffle pods, by insulating under the slab with a product like our SLABX200, or by insulating around the perimeter of the slab. Our calculator takes all three of these products into account; you can mix and match any way you want, and it will show you the R-values that can be achieved with that mix of products,” says Cameron.
For example, by reducing roof insulation from R6.6 to R3.3 and offsetting this by improving slab thermal performance on a 150sqm home in Auckland, you can save between $2,000 and $4,400 per build, or 0.5 per cent to 1 per cent in overall cost, while delivering the same thermal performance of the building.
With changes imminent, EXPOL urges professionals to get in touch to learn more about effective slab insulation. Get in touch with the team and explore products on ArchiPro.