Containing fire: how membrane roofing performs in building fires
Written by
05 February 2020
•
5 min read
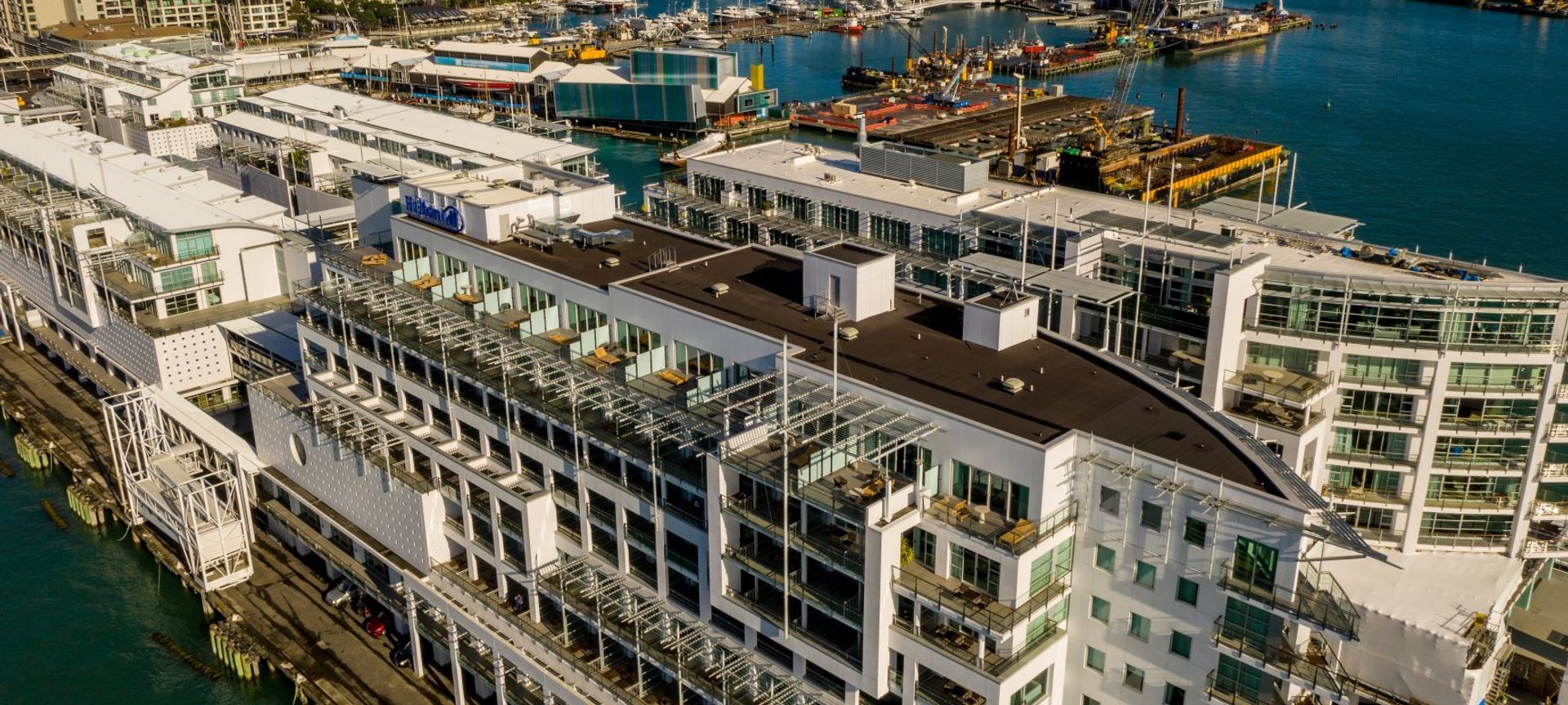
Fire has been a dominant topic of conversation in the architectural world recently in the wake of many incidents around the world, including the Grenfell Tower disaster in London, and most recently the Sky City Convention Centre fire in Auckland. While these two fires were of drastically different scale and outcome, they both pushed the topic of fire and building design to the top of the table.
“This resulted in questions being asked of innumerable construction material suppliers and manufacturers - an understandable response to tragedy and loss,” Viking Roofspec’s Brendon Sutton says. “However, what we noticed was a misunderstanding about fire and the way individual building materials protect from or contain fire; whether or not a material will burn in a fire is another question entirely, and one to which the answer is, predominantly, yes.
“Nearly all solid materials aside from steel, glass and concrete - each having sand as a core ingredient - will ignite and burn if heated for long enough and exposed to sufficient oxygen,” Brendon says.
However, whether or not a material will ignite or burn may be irrelevant as a standalone question, according to Brendon.
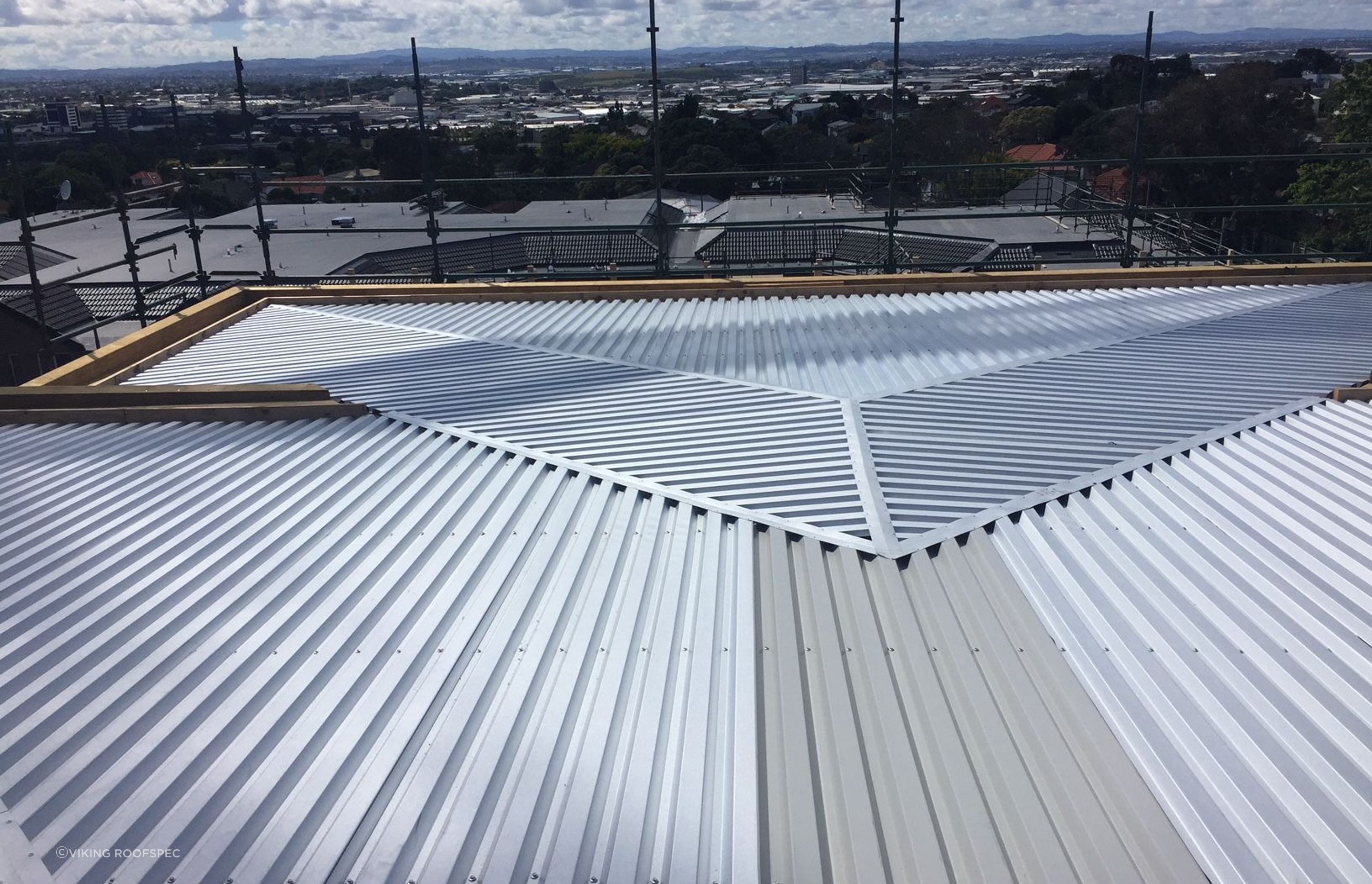
“Rather, a building needs to be looked at in a more holistic way. It is not solely about materials but it is about the design as a whole. If you look at the statistics around building fires, you’ll find that more than 75 per cent of all fires begin inside the building, rather than outside.
“This is a good way to look at a building’s design, with the primary priority to protect life ahead of the building itself, which is replaceable. That means multiple products and the design layout working in conjunction with one another must, first and foremost, be able to allow people to safely exit the building in the case of a fire.
“The volatile, unpredictable and uncompromising behaviour of fire is such that the Fire Code clauses of the Building Code (C1-C6) mostly relate to protecting people first and buildings second. Accordingly, the fire resistance properties of building materials are important but need to be viewed in a much wider context, taking into consideration the importance of the building's layout. For example, the Building Code incorporates requirements around the installation parameters for and positioning of appliances such as ovens. The location of fire exits is paramount as is the ease of access for emergency personnel,” Brendon says.
“That said, minimising the probability of fire spreading to a neighbouring property and ensuring the structural stability of a building in the case of a fire are parts of the Building Code (clauses C3 and C6) that relate more closely to the fire resistance properties of actual materials, rather than the other clauses.”
Membrane roofing and fire: what you need to know
In the case of roofing, for example, there are key performance requirements in terms of fire, which, Brendon says, are focused on the protection of life, and the ability to contain a fire, stopping it from spreading between areas and from the interior of a building to the exterior.
“With a flame’s propensity to burn upwards, the performance of a roof is currently assessed on the properties of the roof assembly's underside - not the exterior layer - to ensure fire is prevented from burning up and through a roof and spreading,” Brendon says.
“Therefore, in the case of a membrane roof, the substrate on which the membrane is installed is the pertinent material, and the one that is assessed to ensure it provides an acceptable level of fire resistance. If it doesn’t, a fire-resistant ceiling must be installed below it to prevent the upward spread of fire.”
As an example, Viking WarmSpan is a wam-roof-on-steel roof assembly designed for low slope roofs. The system is made up of three components: a wide-spanning steel tray roof deck; rigid insulation panels; and, a waterproofing membrane system on top.
It is the lower levels - the insulation and metal tray substrate - that must resist the fire, not the outer membrane.
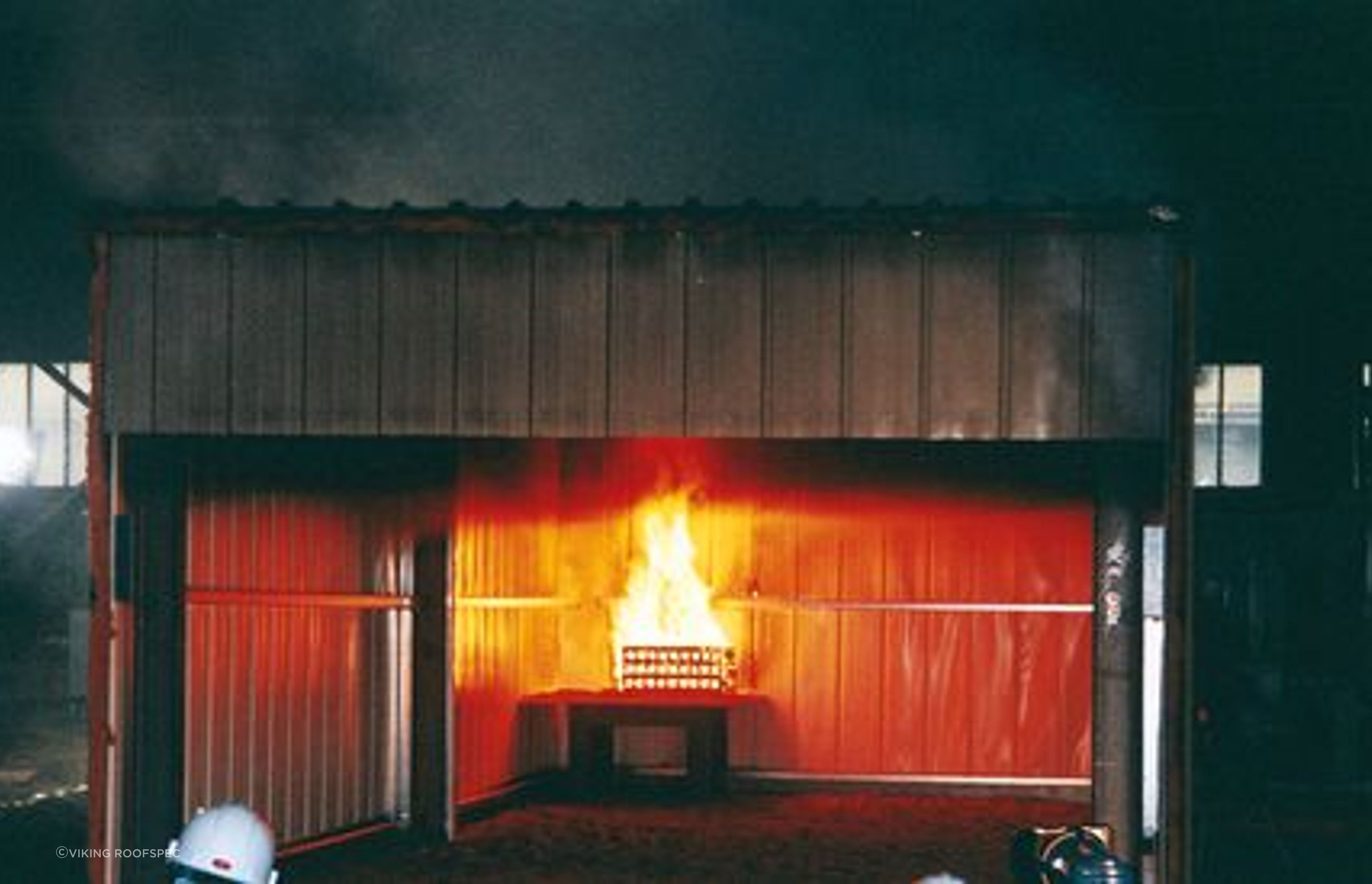
What are the requirements for the fire performance of a membrane roof?
“The New Zealand Building Code assesses the roofing assembly from the inside out. It requires the layers under the membrane, including the rigid insulation, to pass the ISO9705 ‘Room Test’, which involves lighting a fire inside a closed room lined with the materials being tested. The flame spread and amount of smoke produced are measured and reported.
“The highest rating a roof assembly can achieve is a Group 1S rating, which is the level Viking WarmSpan achieved in the test. This rating ensures a product will perform in fire, in that it will subdue flames, allowing people to exit the building safely, or put it out as well as stopping a fire spreading from the interior of a building to the exterior.
"The current Building Code doesn't require the external waterproofing membrane to be fire rated as a standalone material because the substrate below it, forming the barrier to the interior, is the critical layer," Brendon says.
Viking WarmSpan is commonly used on both residential and large-scale commercial projects around New Zealand including, most recently, Auckland’s new Hilton Hotel roof, several Ryman Healthcare villages, Dunedin Art Gallery and Queenstown’s iFly complex, favoured for both its high fire rating and superior thermal performance.
Find out more about the benefits of membrane roofing products.
<sup>Banner image: WarmSpan roofing installed on the new Hilton hotel in central Auckland. </sup>