Engineering solutions for Kiwi homes
Written by
24 August 2021
•
4 min read
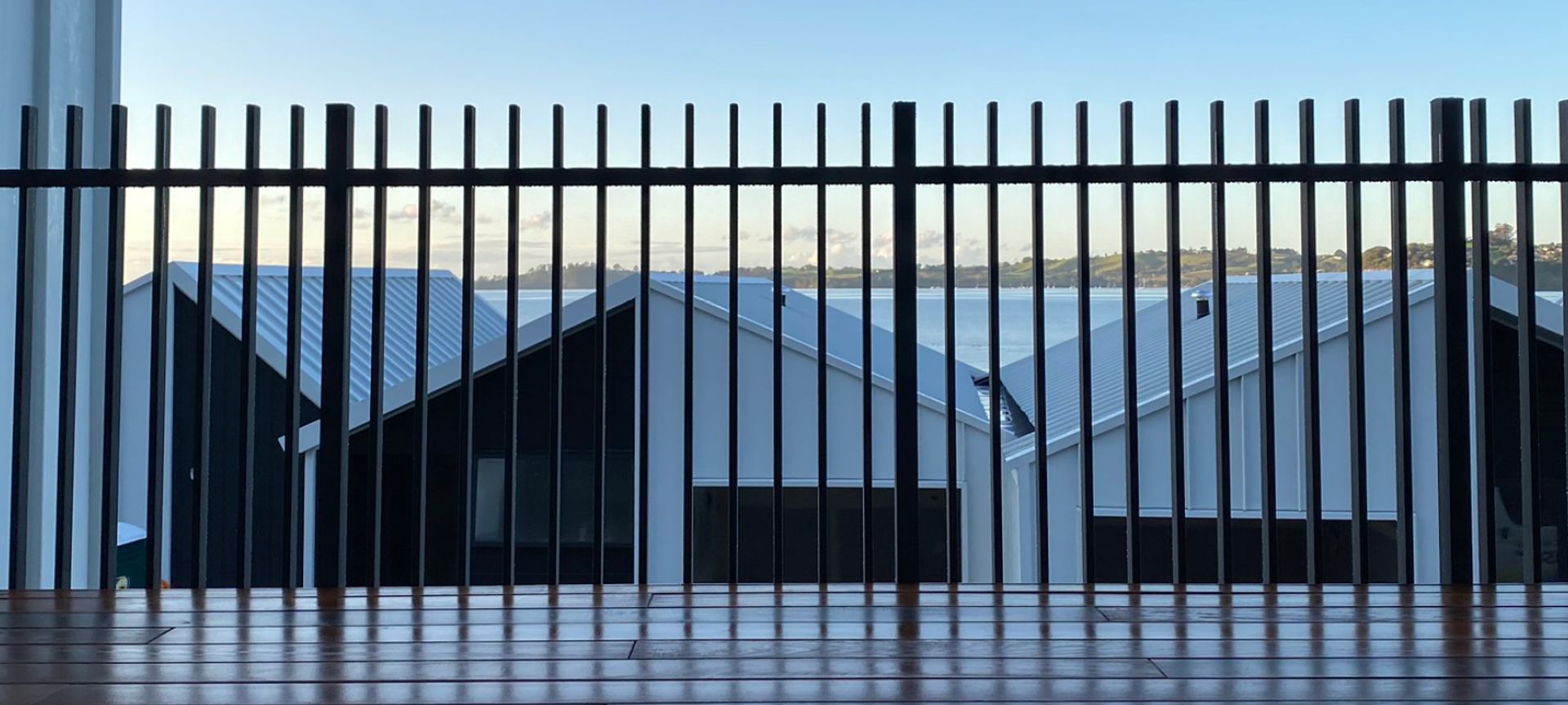
Since the dawn of time there have been a handful of materials that have had such an impact on the human species as to directly influence our evolution—namely, stone, bronze and iron. Since the 19th century, there has been a new material that has driven our progress like no other.
This material is lightweight, malleable, 100 per cent recyclable and is used in the food, automotive, energy, construction, transportation and aerospace industries. So great, in fact, has it’s impact been on modern society that we could rightly say we’re living in the ‘Aluminum Age’.
When Juralco began offering the market a brand of security screens within an aluminium frame back in the 1960s it was a product that would ultimately revolutionise the industry and lead to even more products for the now locally owned company.
“Juralco has a great commitment to innovation with many years of in-house development and industry-defining products. The business has expanded a lot since the 1960s in terms of offering and market share and now offers premium aluminium and glass products,” says Rob Mellor, National Sales and Marketing Manager.
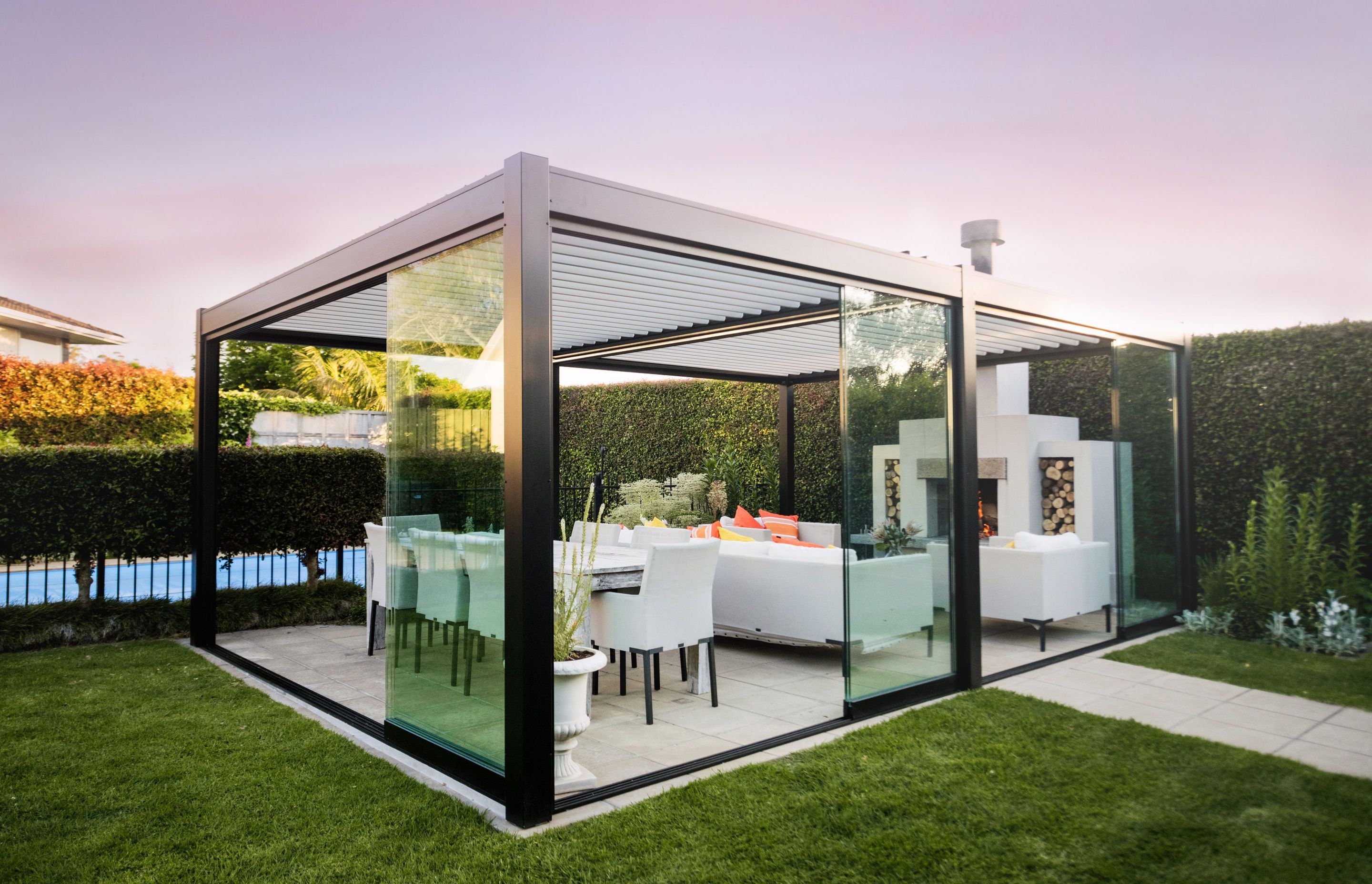
Juralco: innovative solutions, leading processes
“Being New Zealand owned and operated allows us to freely design and develop products specifically for New Zealand customers and which are suited to our unique environment. Similarly, owning the process from start to finish means that quality control can be monitored rigorously and production can be optimised to keep to a tight turnaround.
“Juralco operates an end-to-end process with manufacturing, powder coating and distribution all housed in the same location. Having the ability to assemble and manufacture products in-house means that innovation is a natural occurrence; experts in aluminium products are on hand; and, there are no roadblocks to putting something new together.”
Rob says there are also environmental benefits to having complete control over the production process.
“Juralco is able to keep processes as thorough as possible; reducing waste, recycling off-cuts and keeping the powder-coating process spotlessly clean, which is both beneficial for the end result and the environment. Juralco is a fully accredited Dulux aluminium applicator and uses a sophisticated automatic powder-coating process.
“The journey to sustainability starts at the beginning. More than half of our raw aluminium is sourced in New Zealand from the Tiwai Point facility, which produces the most environmentally friendly aluminium in the world thanks to its use of hydroelectric power.
“Another factor to aluminium’s sustainability is that it produces almost zero waste onsite and is highly durable. Under Building Code durability requirements, materials are required to be sufficiently durable. As a material, aluminium meets B2 Durability requirements for no less than 50 years.”
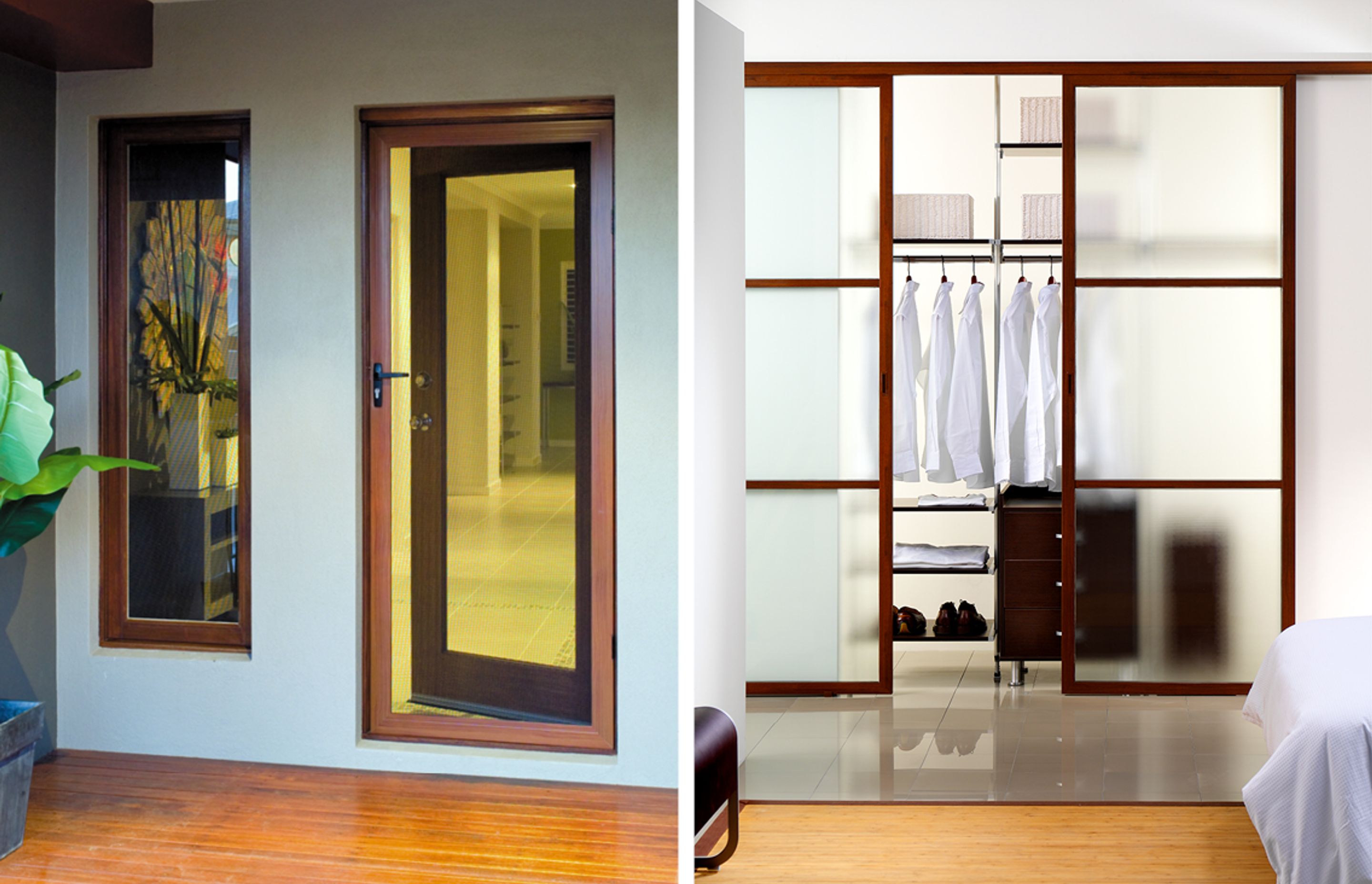
Juralco: a nationwide presence
“One of the critical factors in the ongoing success of the Juralco brand is its symbiotic relationship with its very own nationwide network of fabricators and franchised installers. The HomePlus network design and install Juralco products and systems and are critical in the product development process, picking up essential customer feedback on site.
“Having this level of involvement from a team of specialists means that if an idea is good, it's given a chance to succeed from the very beginning and means that working on custom solutions is viable from both a timeframe and budget perspective.”
Based in Henderson, Auckland with a distribution warehouse in Christchurch, Juralco designs, fabricates and installs a mix of residential and commercial products, including for multi-unit retirement projects.
“There are four pillars to the business—balustrades; insect and security screens; wardrobe doors and organisers; and, louvre systems. These are then augmented by a raft of other, complementary products, which allows us to provide customers with a comprehensive range of options for their home or commercial setting.”
Rob says the vast majority of jobs are turned around within seven days using stock on hand. Product extruded in New Zealand and then fabricated and powder coated takes around three weeks for delivery while product sourced from overseas takes around 12–16 weeks for delivery.
Learn more about custom-made aluminium products for your next residential or commercial project.