Factories overflow with products while most still unable to manufacture
Written by
10 September 2021
•
4 min read
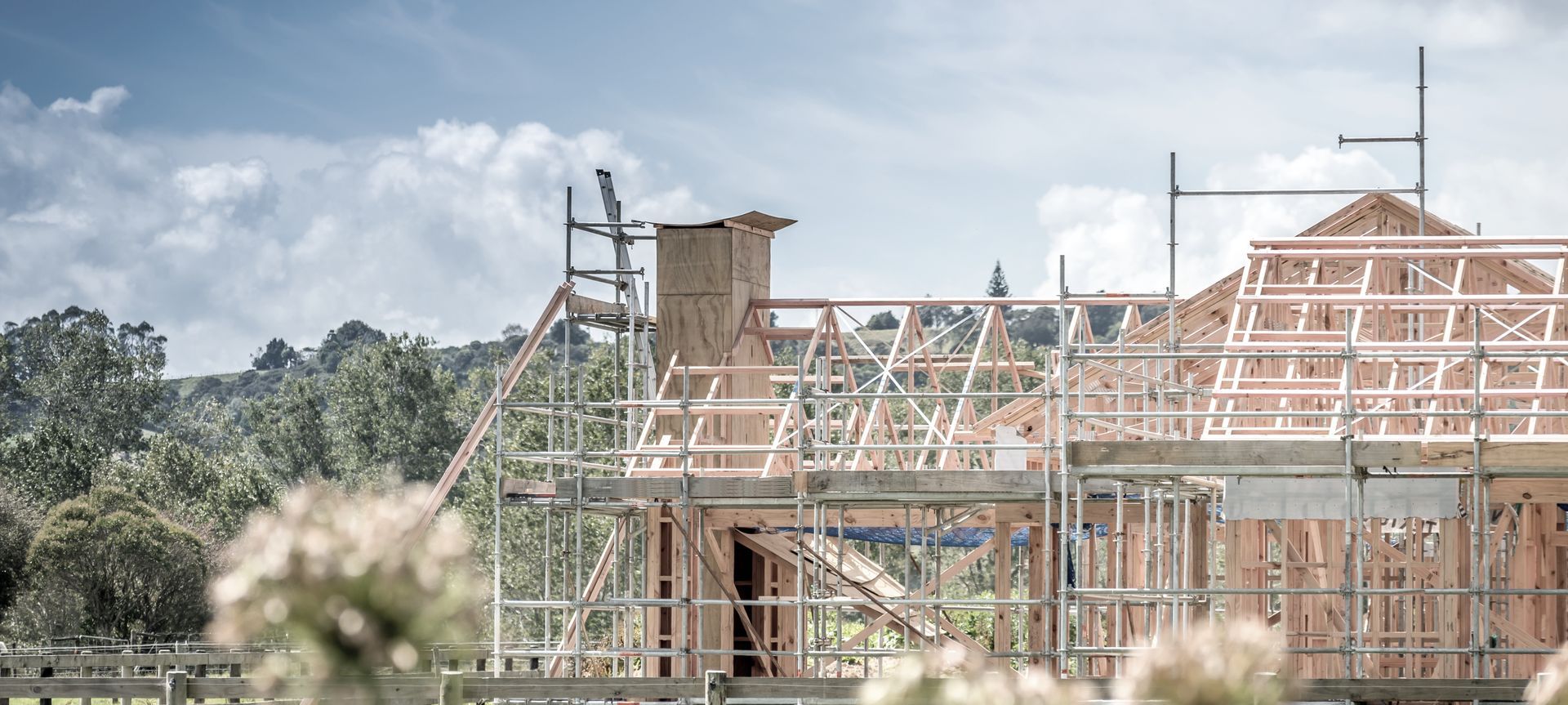
Under the level four lockdown in Auckland, MBIE has given four factories permission to fire up the plant and begin manufacturing, on account of construction outside of Auckland grinding to a halt due to severe shortages of crucial building materials.
But there’s many more manufacturers lining up to be considered as an essential service, amid criticisms that MBIE hasn’t responded quickly enough to enable other essential building material manufacturers to operate.
Currently only four manufacturers are allowed to operate (these companies produce roofing steel, plasterboard, gypsum plaster and insulation), with a total of only 100 workers authorised to go back to work.
MBIE is considering more applications for essential material manufacturers to operate, but building product suppliers are also complaining that their warehouses are starting to overflow with incoming products that they are unable to deliver under level four rules.
Halliday & Baillie, which manufactures the majority of its hardware products in Auckland, has a lot of stock on hand that can’t be sent out. Director Tiffiny Hodgson accepts that hardware isn’t an essential service and that it’s important to reduce worker numbers to support the Covid-19 elimination strategy, but she says she’s frustrated with the inability to shift product that’s already in stock.
“Couriers are delivering Lego from Farmers for crying out loud, but I’m not allowed to [send out] in-stock product.”
Tiffiny says there needs to be more consideration around how businesses will stay afloat if level four lockdowns continue, or are repeated in the future.
“People still need jobs and coming out of level three or four, if our income stream has significantly changed, then businesses will start to not need those people.”
Master Builders Association president Kerry Archer says he’s heard there are many more suppliers and manufacturers in talks with MBIE about being able to distribute essential building materials.
“The plumbing outfits and those sorts of guys, I don’t know if they’ve been given permission, but I think they’re pretty close from what I’ve heard to being allowed to distribute from warehouses.”
Kerry says builders in the industry who are operating at level two are highly concerned that the trickle of supplies making it to site will soon stop them from being able to complete work.
“I’m talking to builders daily who have run out of materials and they’re trying to figure out what they can do with their staff because they can’t get Pink Batts, so they can’t line their walls, or they can’t get Gib board so they can’t line their walls. Their Gib stoppers can’t get stopping compound and their plumbers can’t get plumbing fittings. There’s a huge flow-on effect.”
Couriers are delivering Lego from Farmers for crying out loud, but I’m not allowed to [send out] in-stock product
Kerry says there’s no easy answer as the government weighs up between public health, the housing supply problem, and the economy, but there will be a significant effect on the building industry.
“We’re going to have delays in getting materials, we’re going to have price increases, and we’re going to have lots of pressure on industry to deliver what we’re trying to deliver, and it’s probably only going to get worse.”
The South Island appears to have been affected less than the North Island, due to having its own manufacturing plants for plasterboard and other essential construction materials.
Daryl Hewitt from Christchurch-based construction company D J Hewitt Builders says his crew are back working again due to careful planning and ordering stock well ahead of time. However he knows that in spite of this, the Auckland lockdown will cause further delays to an already sluggish supply chain.
“It’s going to be a bottleneck in Auckland. It’s going to take a while before the supply chain levels out again.”
He says expecting delays, being patient and planning well ahead have become the new normal for the building industry.
“You have to think ahead and give people notice, and you have to expect that there are going to be unexpected delays… It’s a new industry at the moment, it’s learning how to build in a different way.”