Ferrars & York, South Melbourne
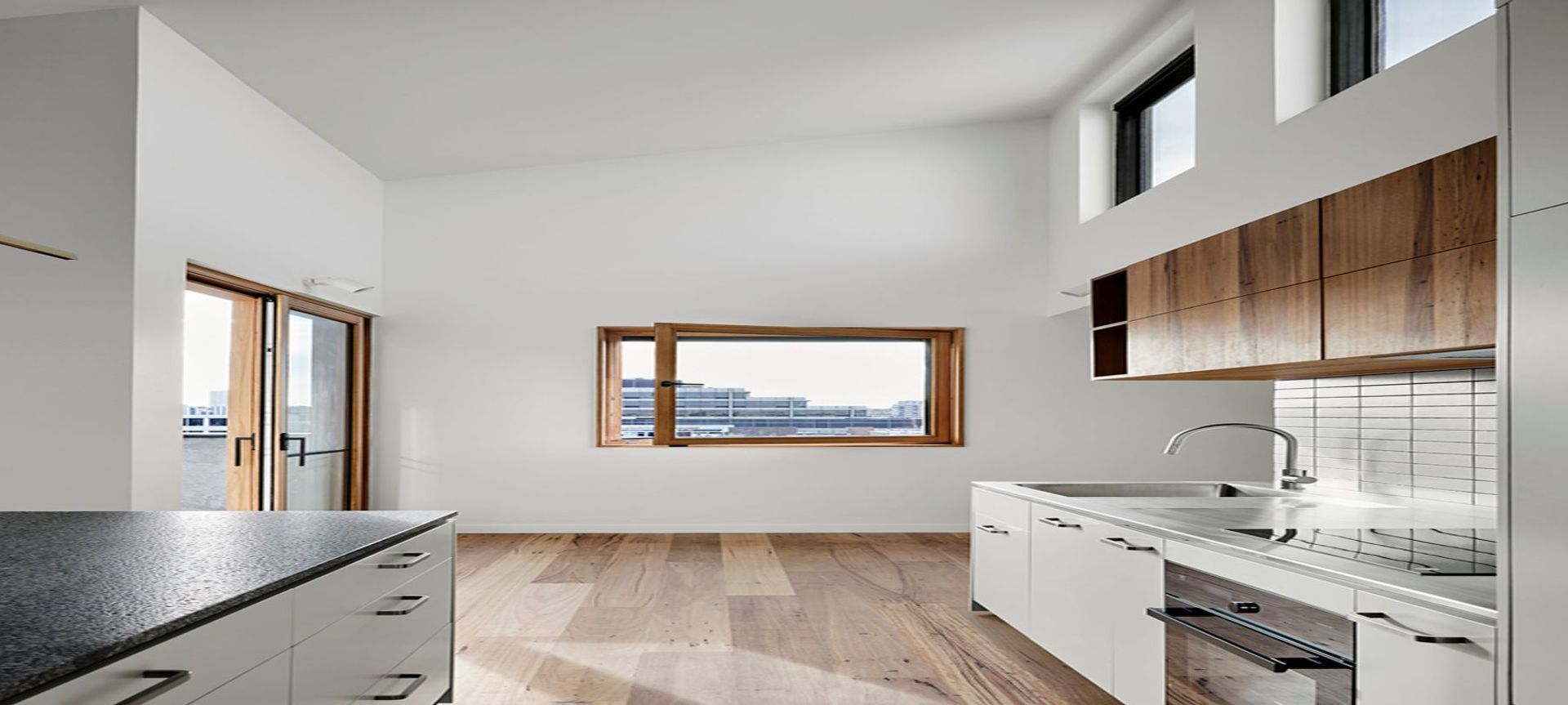
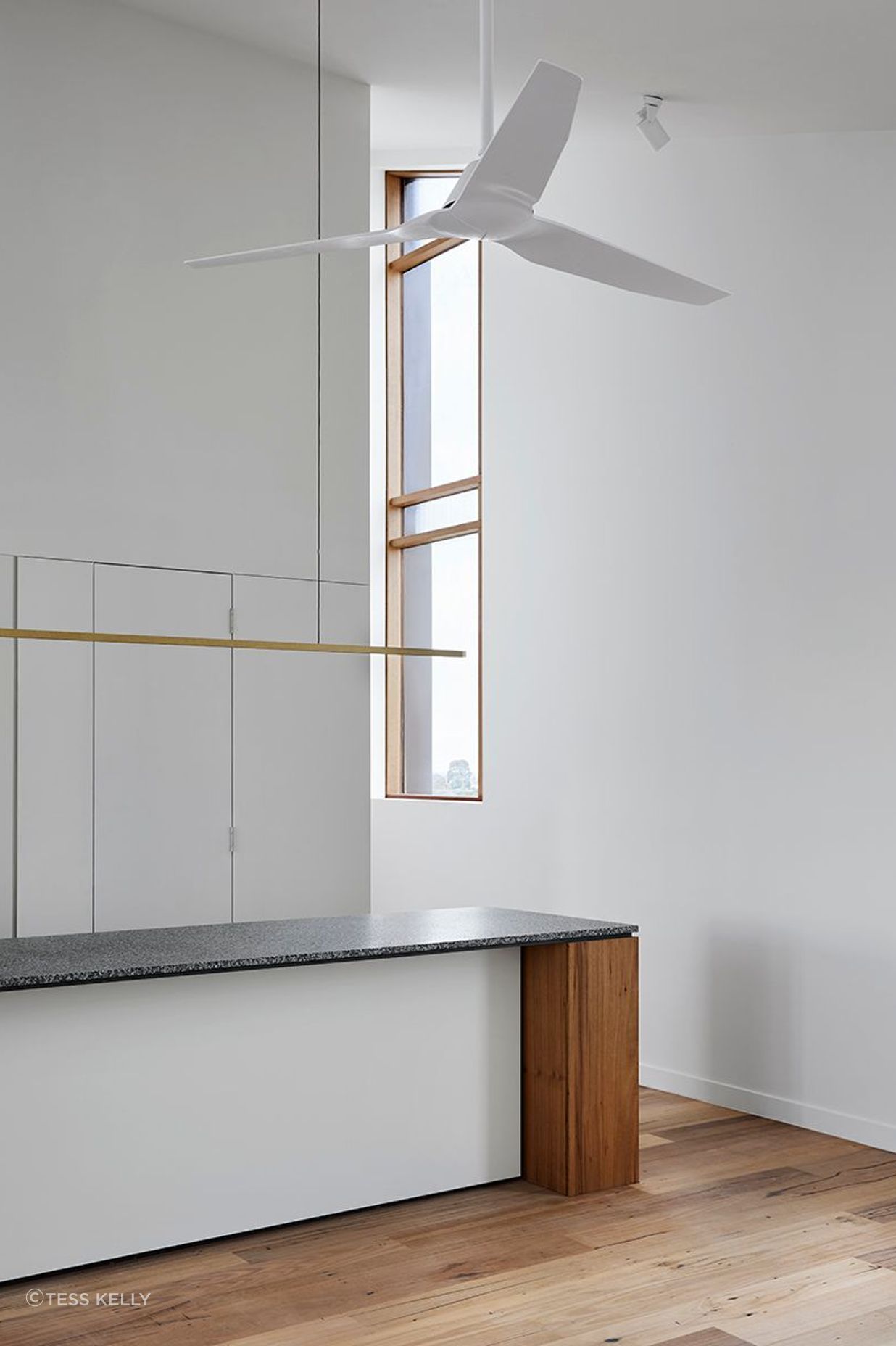
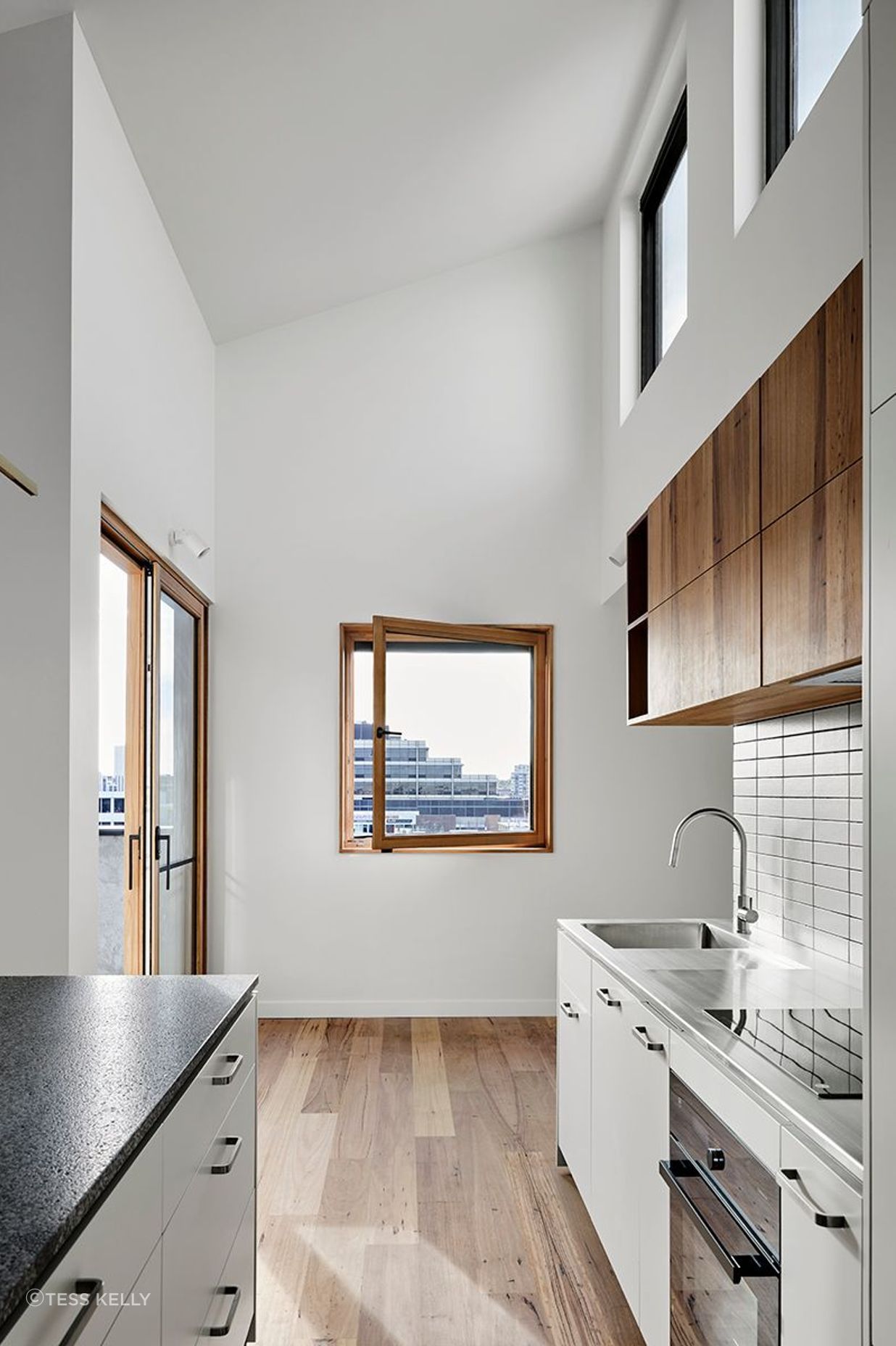
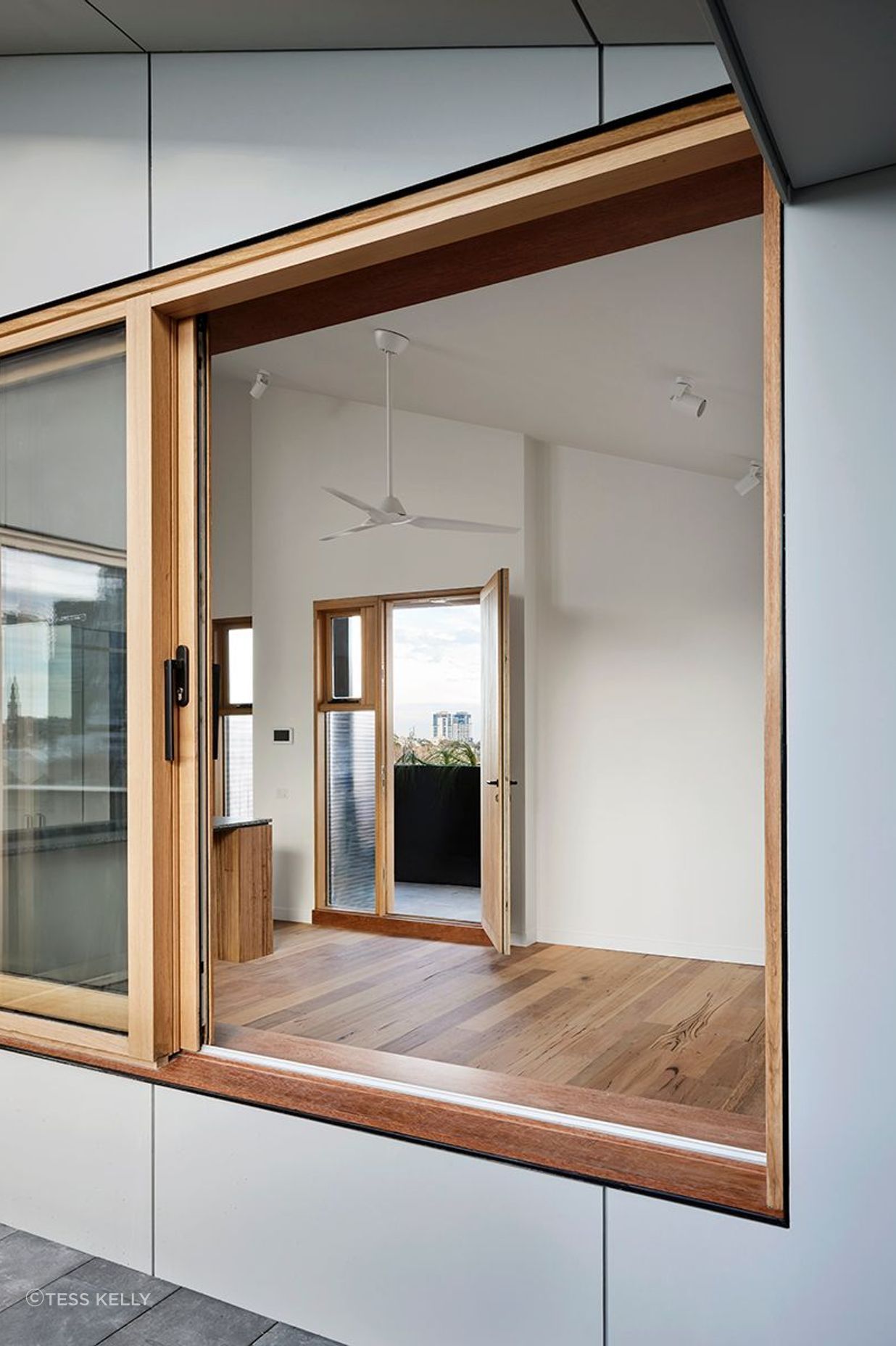
BACKGROUND
Located just 100 metres from the iconic South Melbourne Markets, Ferrars & York sets a new standard for selfsufficient apartment living. Designed in collaboration with Six Degrees Architects and enabled by HIP V. HYPE, this development features 22 carbon neutral apartments, all powered by 100% renewable energy and representing best practice in climate resilient design and construction. Building upon their success with Nightingale 2.0, HIP V. HYPE wanted to ensure Ferrars & York took optimisation, sustainability and innovative design to the next level. “So much of what we seek to do is make sustainable living easier and more convenient,” says Liam Wallis, Founder of HIP V. HYPE. “We wanted to take all our learnings from Nightingale 2.0, and create a building that was a step up.” Everything in Ferrars & York’s design speaks to quality, durability and long-term value, particularly its low impact, responsibly-sourced products, energy-efficient heating, cooling and ventilation systems, and emphasis on natural light. Open walkways and a communal roof yard complete with fireplace and barbeque place an emphasis on community and create a sense of belonging. Ferrars & York’s carbon-neutral design will be the first of its kind in South Melbourne. To achieve this, HIP V. HYPE undertook a lifecycle analysis to calculate the embodied carbon used to construct the building itself, and then voluntarily purchased certified climate offsets from Climate Active.
CHALLENGE
With Ferrars & York, HIP V. HYPE aimed to create a development that achieved both carbon neutrality and a targeted 8+ NatHERS energy rating. These lofty sustainability goals required careful consideration of the building envelope, especially the design of its windows and doors, which needed to deliver exceptional thermal performance and airtightness. “When it comes to both energy efficiency and acoustics, windows and doors are your weak point,” Liam explains. “That’s where you have the most heat gain and heat loss throughout a year and, when we build apartment buildings in high-density locations, you can end up with health impacts due to noise if you don’t insulate or seal your property correctly.” Of course, it was important that the energy-efficient windows and doors were easy to operate, easy to maintain and consistent with Ferrars & York’s contemporary aesthetic. A development of this complexity, particularly one running amid a pandemic, also called for an experienced supplier who could reliably deliver the project in time and in full
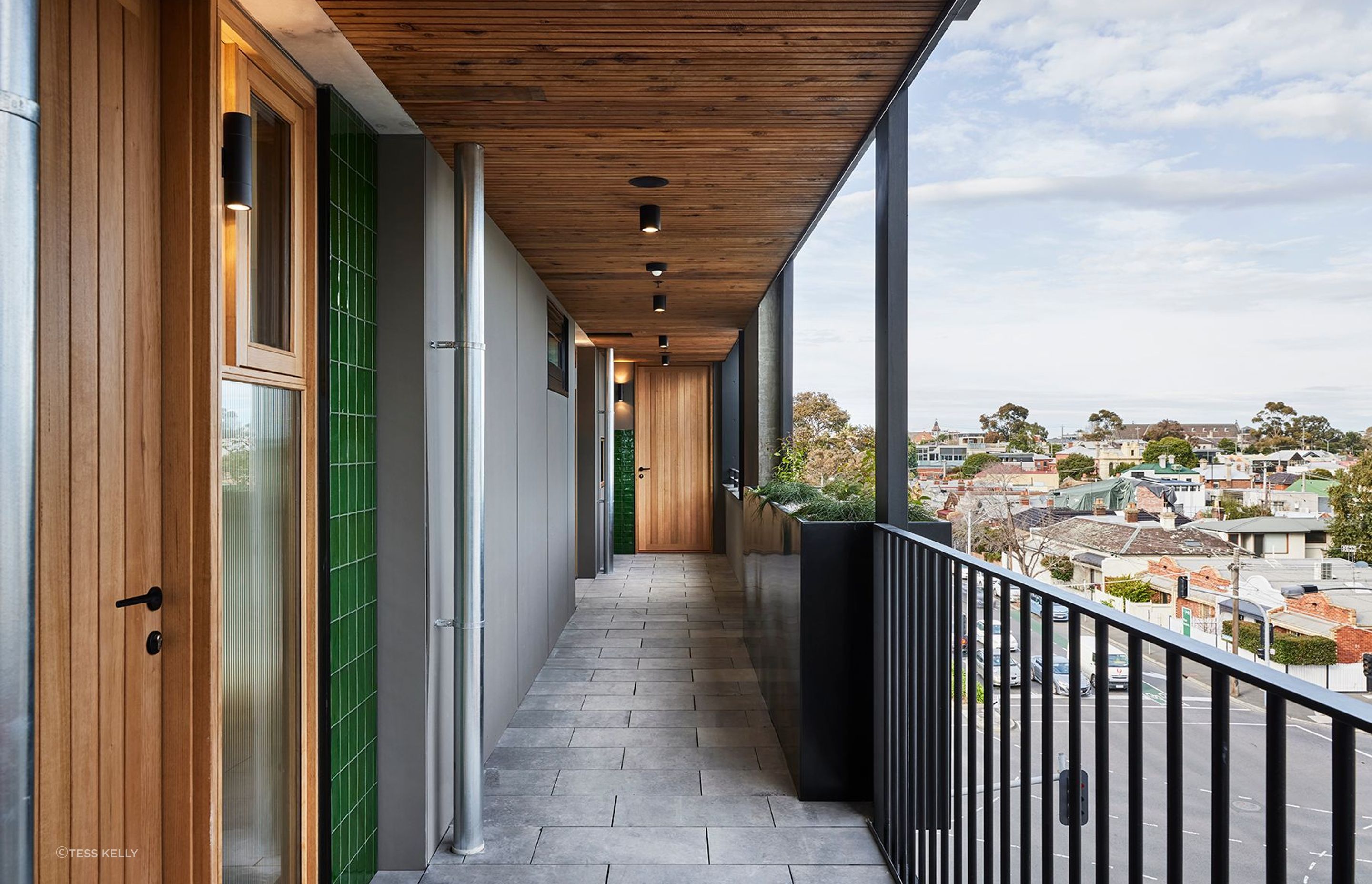
“So much of what we seek to do is make sustainable living easier and more convenient”
SOLUTION
As a company that is up for any design challenge, BINQ Windows was the ideal partner for the project. BINQ offer some of the most thermally-efficient timber window and door systems on the market, making it possible for Ferrars & York to achieve an 8+ star energy rating. Using European design principles, the Archetto Series Tilt & Turn window, Lift & Slide door and IV68 hinged door maximise glass with their low profile and provide the ultimate climate control with continuous rubber gaskets that are uniformly compressed with multi-point locking systems.
BINQ’s window and door systems are an essential component in Ferrars & York’s exceptional average energy rating of 8.6 stars (out of 10), which means more comfort for occupants, better acoustic performance, significantly lower energy bills and a lower carbon footprint. “With good quality doors and window systems that are sealed correctly, you are using significantly less energy to heat or cool your home by virtue of the airtightness you are achieving,” Liam explains.
In addition, BINQ’s contemporary styling and Australian hardwood frames easily met the architectural aesthetic brief. “BINQ is a company that is dedicated towards creating beautiful products that not only perform well, but are also easy to use and look incredible,” Liam says. “Some of BINQ’s window frames weigh up to 200 kilograms, and yet you can move the entire window frame with two fingers. When people interact with a system like that, it gives them real confidence in the quality of the construction and a greater sense of connection with the building.”
Forward planning and scheduling were critical to ensure the project ran seamlessly during a time when international supply chain issues and local labour shortages were causing delays across the industry. The BINQ production scheduling team worked closely with the building contractor’s project managers to identify a staged delivery plan and key site logistical constraints and together with the builder, Ironside, a detailed plan was set out and executed to ensure minimum disruption to all parties.
“The heart of the relationship we’ve formed with BINQ is that we have a commitment to them and their product, and they have a commitment to us,” says Liam. “It’s a genuine collaborative relationship.”
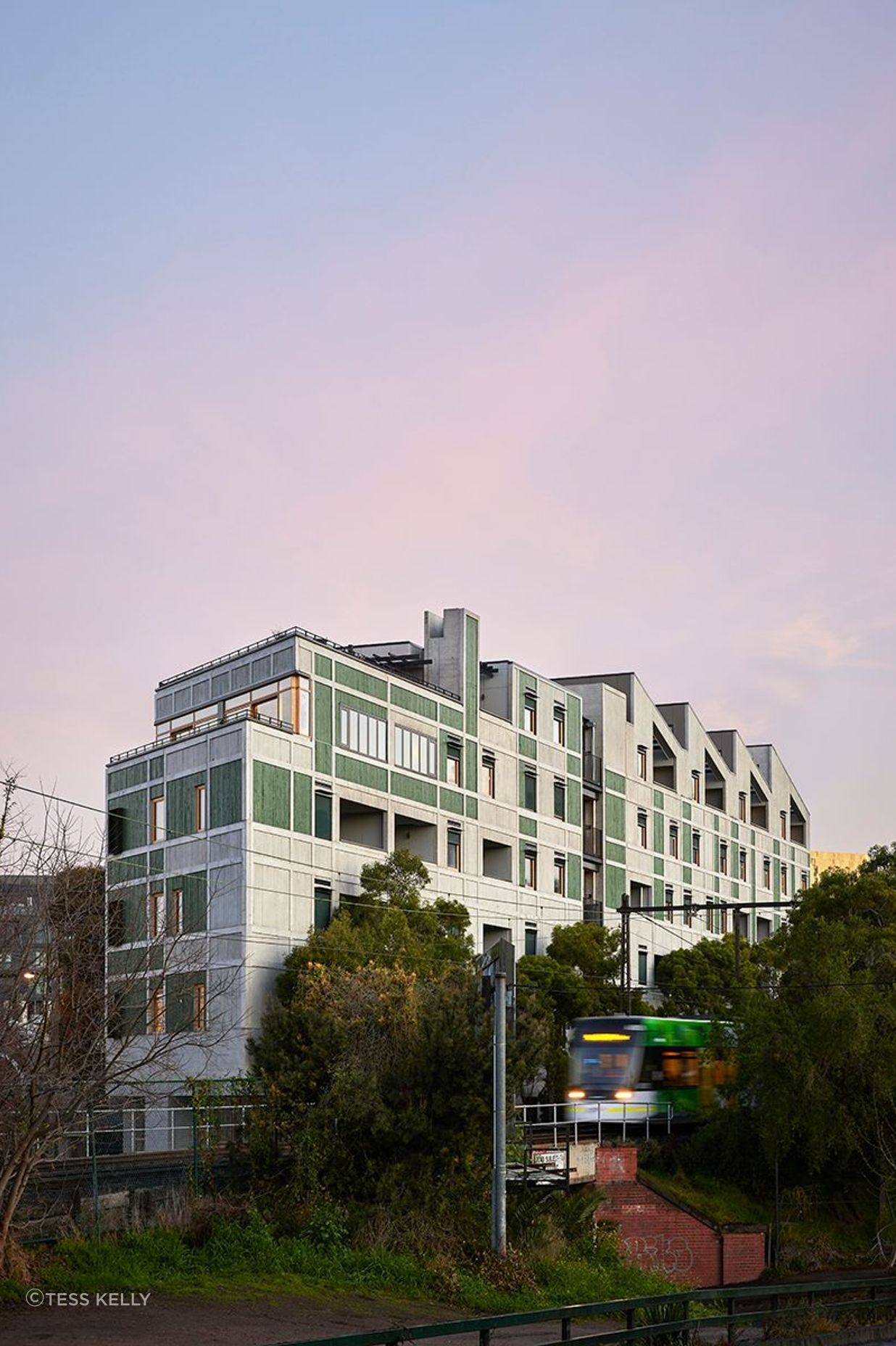