How High-Quality Synthetic Grass is Made
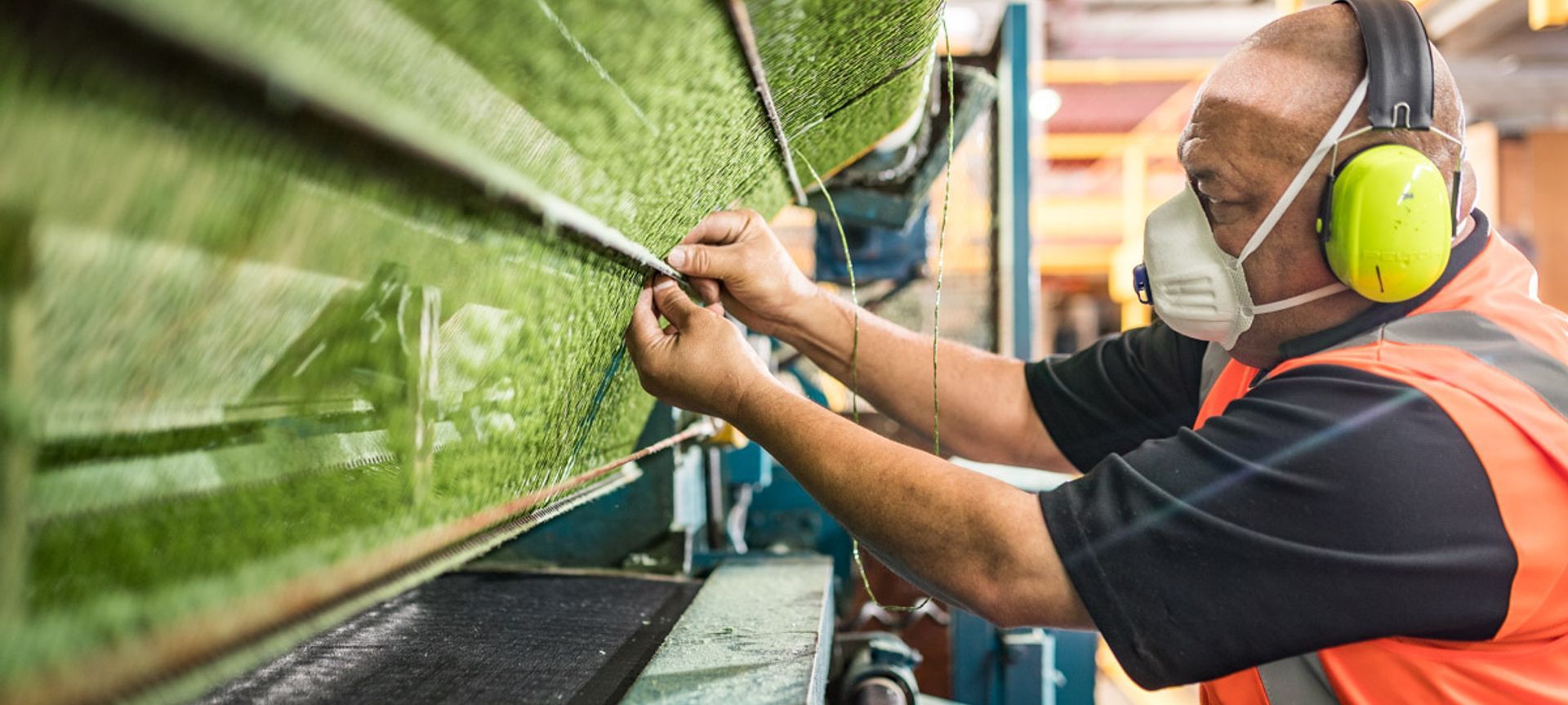
Whether you’re a fully-fledged grass nerd like us, or you’re after some background about the grass making process to feel more informed about choosing the right stuff, we’ve got you covered.
You might be surprised to discover that the beautiful, high-performance artificial grass you see around today has quite a history. In this article, we’re going to focus on the current, best-practice processes that create the highest quality synthetic grass.
The Components of Synthetic Grass Turf Installation: A Quick Glossary
Synthetic grass is fundamentally made up of a number of components: The, backing cloth synthetic turf fibres and a latex or polyurethane coating. The grass is then joined and installed using pegs or nails (landscape grass) and or glue and tape to join the seams where the grass joins.
Backing:
The backing material in your grass is what gives it structure, adhesion, and holds everything together. Good quality and correct type of backing cloth is essential to the life and performance of the grass. For example a long pile landscape grass has more stabilising infill or ballast than a short pile sports product and therefore less prone to movement, expansion and contraction. Some applications like football and hockey put huge demands on the fibers and backing cloth and the correct dimensionally stable backing cloth is essential to ultimate performance.
Glue and Tape:
Rolls of turf are anywhere from 2.0m to 4.0m in width and therefore need to be joined. Correct choice of tape and glue and the correct application of glue are critical to the longevity of the seams. Again a residential landscape lawn may simply be butt jointed using nails or pins but a sports turf that is subjected to players feet, sticks, scrums, penalties etc will be joined using robust tape and glue/ The seams re generally undetectable – you shouldn’t notice it unless you’re really looking. Again, the type of seaming used depends on other factors, like what has been used as a backing. The most common materials used for seaming are tape and glue, sod staples and nails, or industrial double-sided tape.
Turf Pegs:
Nails, or turf pegs, can be used in some installation processes of residential landscape turf, and secure the grass to keep it from lifting or curling. They’re what keep everything in place!
Yarn/ Synthetic Turf Fibres:
Yarn, or synthetic turf fibres, are the “blades of grass” – the final component of synthetic grass, and the one that you’ll see and interact with the most. Yarns vary with colour, performance, and design, and while there are endless options out there, you can usually narrow your choices down by determining the main purpose of the grass. Quality resins, pigments or colourants that don’t use heavy metals and quality proven UV additives are all critical elements of the yarns. The yarn is the most expensive element in your grass system so if its to cheap to be true then perhaps some of these critical elements are lacking...
Artificial Grass Manufacturing Process
How fibres (the “blades of grass”) are made
Synthetic turf fibres are made from polypropylene, polyethylene or in some cases Polyamide (Nylon) polymers depending on the final products use and application.. The polymers come in small bead form and are melted using a combination of heat and pressure before being extruded into a shape that replicates natural grass blades or specifically engineered to perform for a particular application. During the melting and extrusion phase pigments (colours) and UV additives are added.
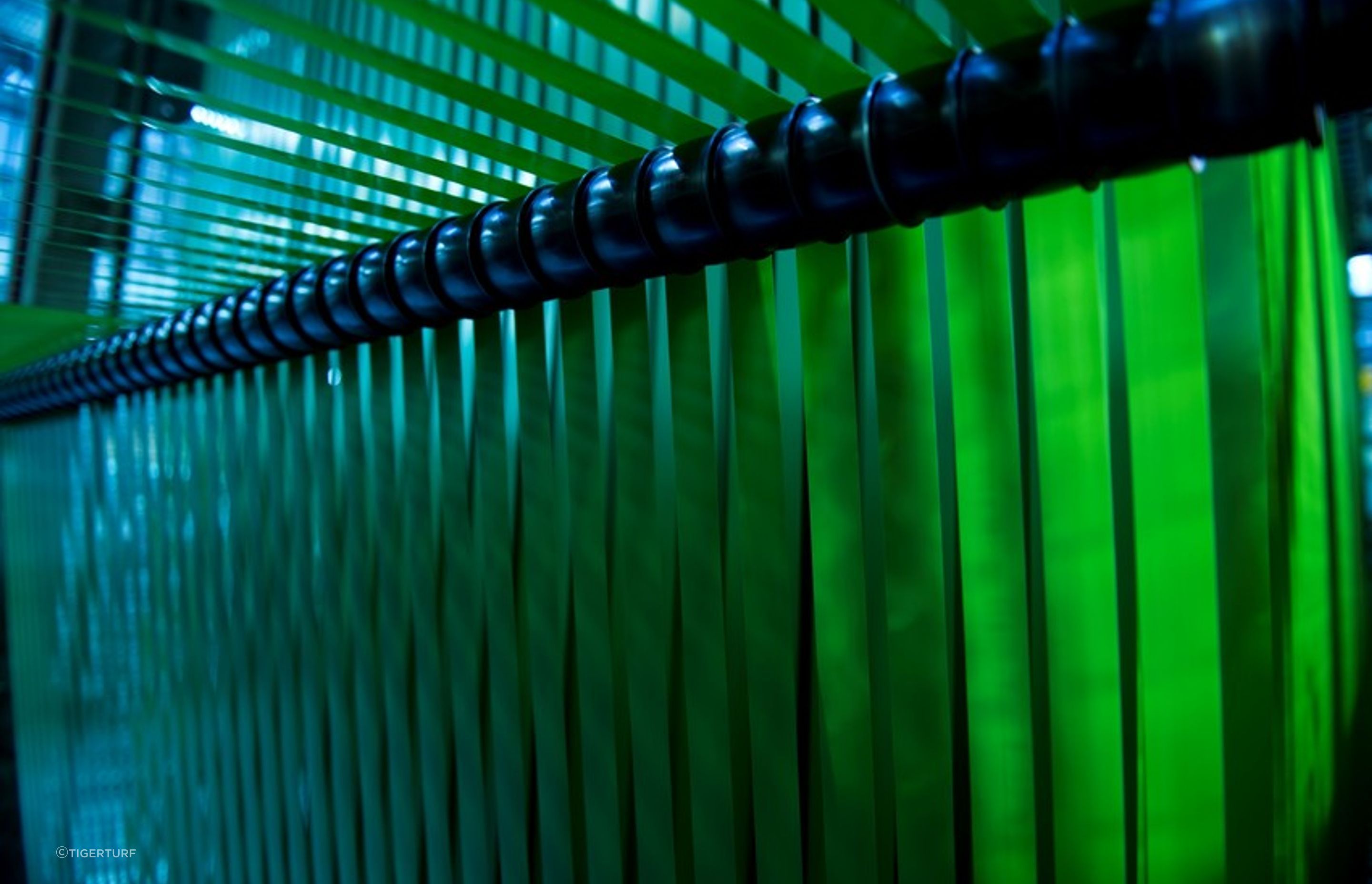
The extrusion process can differ depending on the purpose of the grass – the resulting pattern determines how the grass will ultimately perform.
The “blades” take their first form when they come out of the extruder as a long, thin strand of material.
The strands are then Wound onto a bobbin or spool to be transported to the grass/turf manufacturers for tufting.
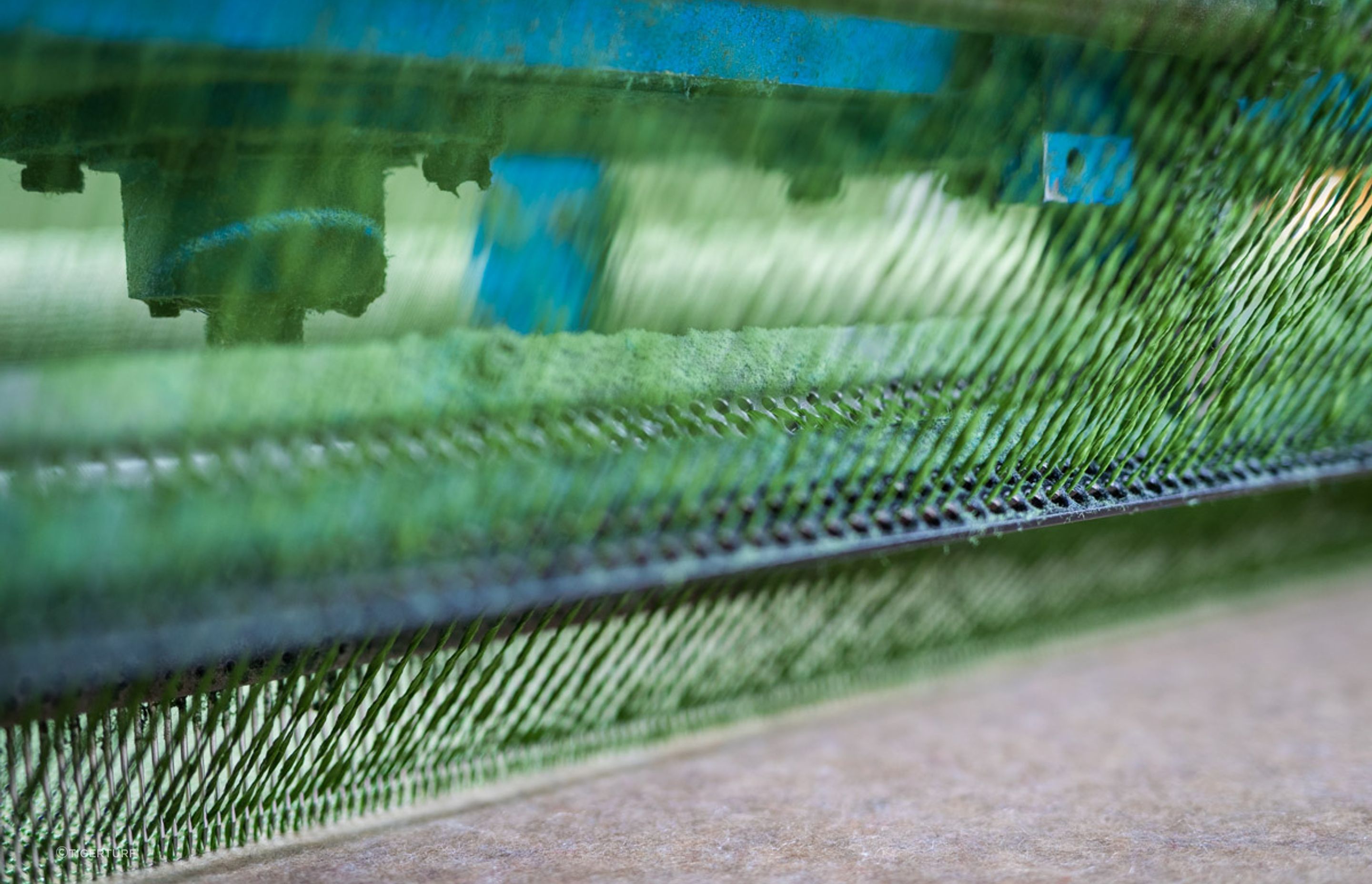
High quality yarn doesn’t depend on any one component or factor, because the process can be slightly different depending on the desired outcome. An advanced, use-specific extrusion process, however, can help develop a higher quality end product. The best manufacturers are those that are able to control the design process, polymer selection, design and develop the additives and high performance UV stabilisers.
Why backings matter
The backing material of synthetic grass will differ depending on its primary purpose – you might use a different backing for outdoor than indoor use, for example; and a different backing for a lawn than a professional sports field. As an example a typical landscape grass will have 12 – 20kg sand per m2 weighing it down meaning the backing cloth is not being subjected to expansion, contraction etc. By contrast a watered hockey turf has no sand in it meaning the backing cloth must perform at much higher level than the landscape turf.
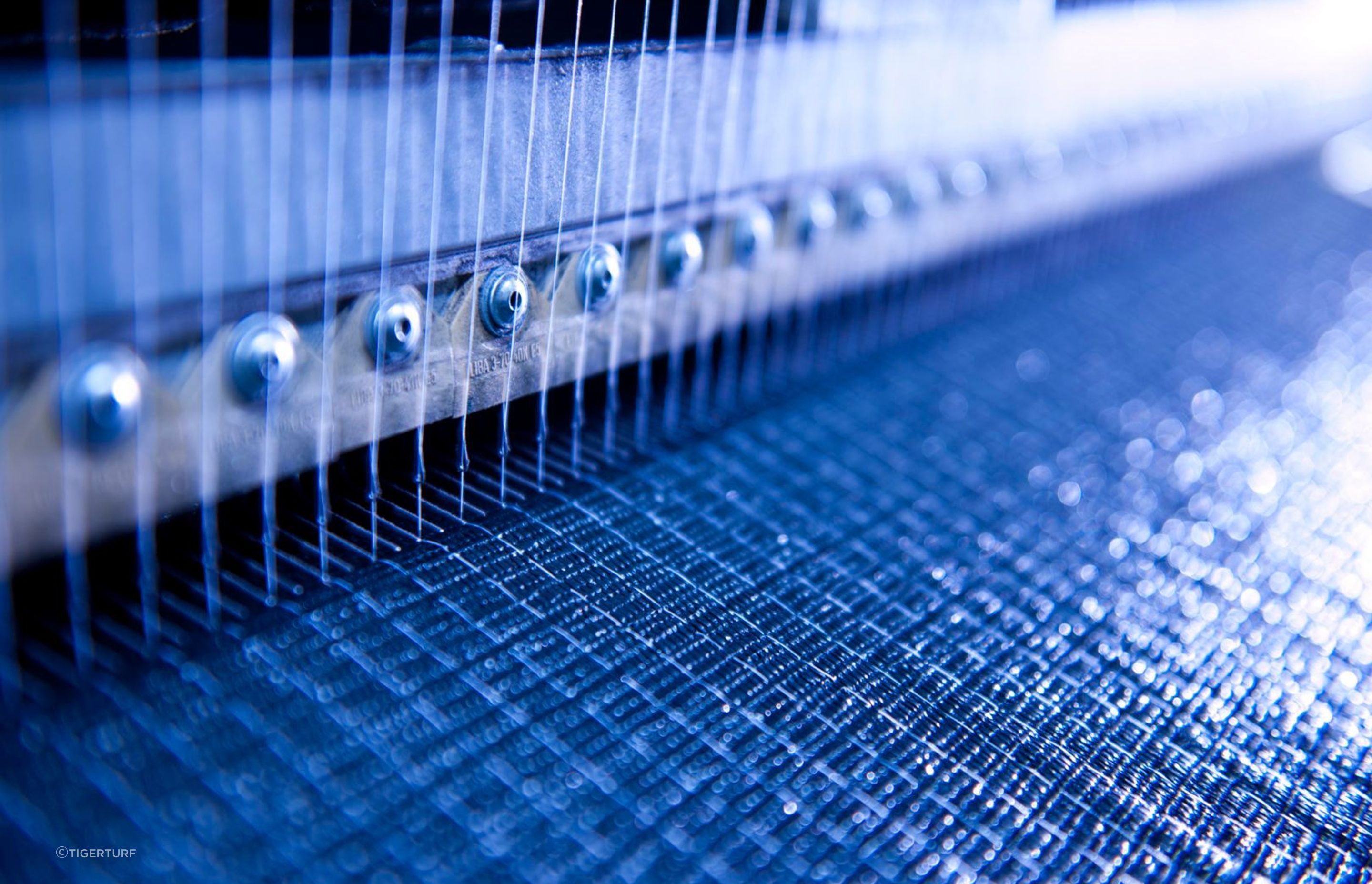
The quality of the backing used determines how well the tuft locks – the better it locks, the less yarn it will lose over time. Backings also play an important role in how well the various layers of the finished product stay together.
A high-quality synthetic grass manufacturer will boast a range of backings that are fit for purpose. These can include plain (tension-free) backings; fleeced backings; multilayer (or double woven and fleeced) backings; and warp-knitted backings. A quality manufacturer should be able to prove tuft lock and filament bond statistics for their products as part of their quality process.
Weaving or tufting the yarn
Traditionally, synthetic yarn is “tufted” onto the backing. Tufting is a way of weaving textiles (it’s the same as the process for carpet-making), and for synthetic grass, this is part of what keeps the blades from coming loose from the base.
However, technology has advanced, and a high-quality manufacturer may use a combination of tufting and weaving techniques. A woven surface is preferable for high-level sports fields because it enables an even more realistic pitch surface and enhances ball play. Woven technology also allows the manufacturer to mix a combination of different yarns not possible with tufting, the yarn bundles can be offset when weaving and the tuft lock or filament bond of the yarns in the backing is up to 4 x stronger with weaving than tufting. Woven products are however typically more expensive than tufted products
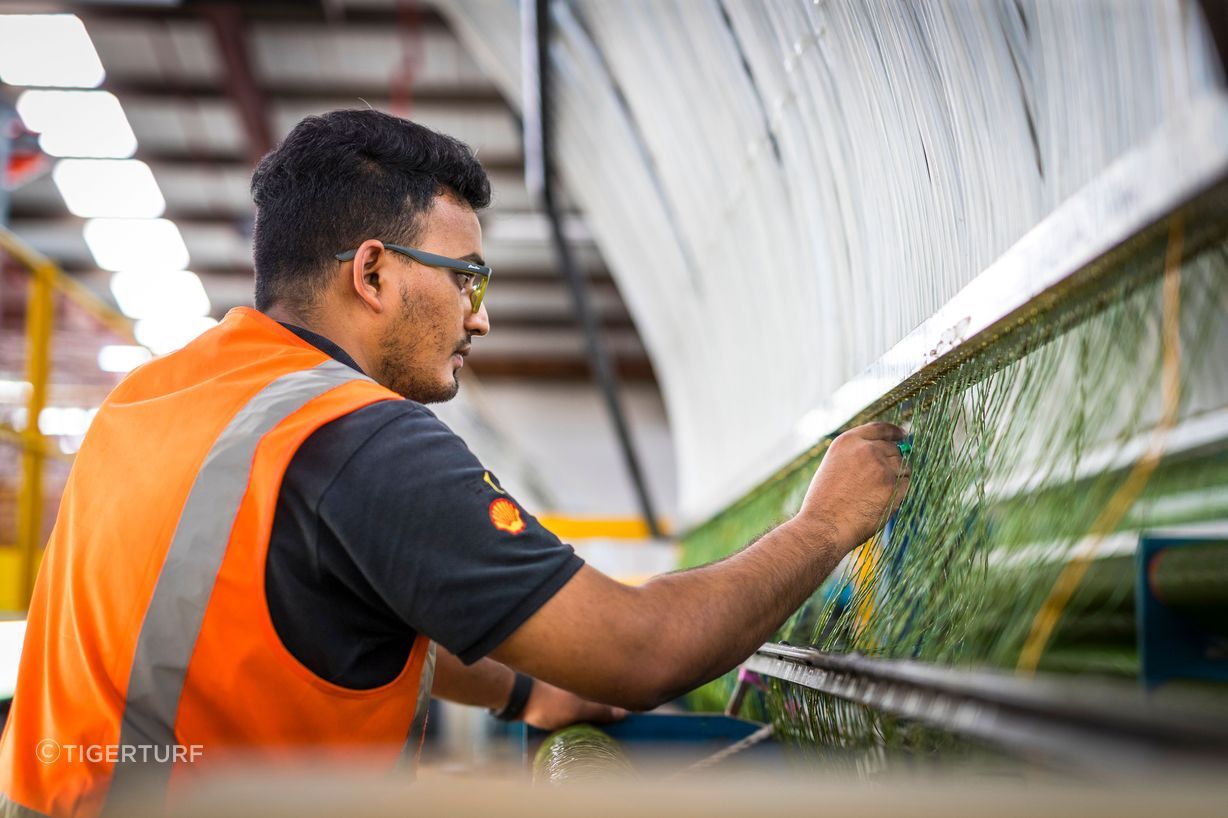
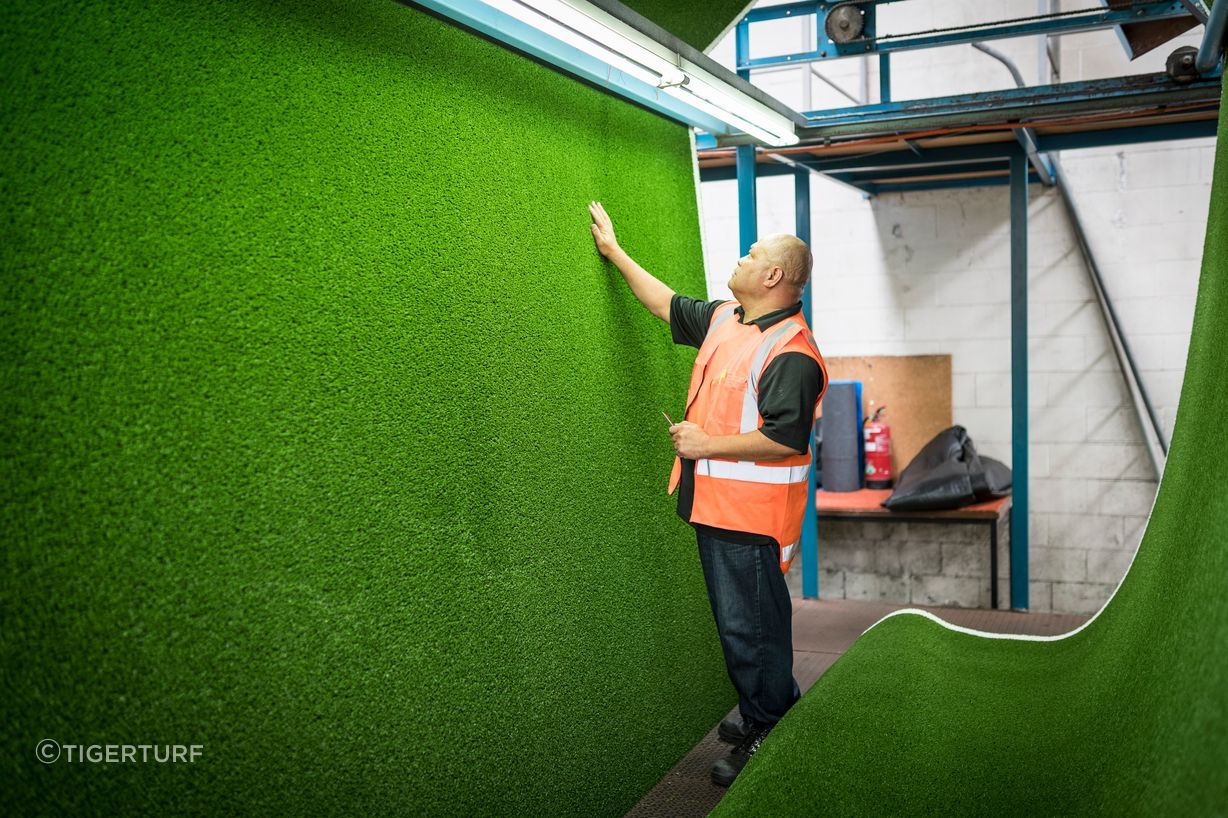
Testing and quality control
Because of the high uptake of artificial turf for professional sports and commercial purposes, new products undergo extensive testing and quality checks.
What is measured during quality control?
Numerous checks are made during the new product development process:
- Correct yarn and backing cloth for the product type
- Correct pile height and stitch rate for the product type
- Using only yarns from one production dye lot (colour lot)
- Latex or Polyurethane blend for product type
- Weight of latex/Polyurethane applied during production
- Tuft lock and or filament bind (how well the yarn is stuck in backing cloth
- Sports markings, lines, or logos are to correct standards and sizes
- Labelling show name, pile height, product dates and batches etc
- Weather and UVprotective wrap to ensure grass stays in the best shape possible until the time it is installed
Good quality synthetic grass is a whole system, not a single component
Creating high-quality artificial grass requires high-performance materials, but the key factor is how these components interact. The system's performance depends on the turf construction, the synergy of its components, and proper installation and maintenance. Variety is essential; quality isn't determined by a single factor. A good manufacturer or supplier is distinguished by their commitment to perfecting this combination. TigerTurf exemplifies this by manufacturing its own synthetic grass in Auckland, New Zealand, ensuring meticulous quality control and superior products.
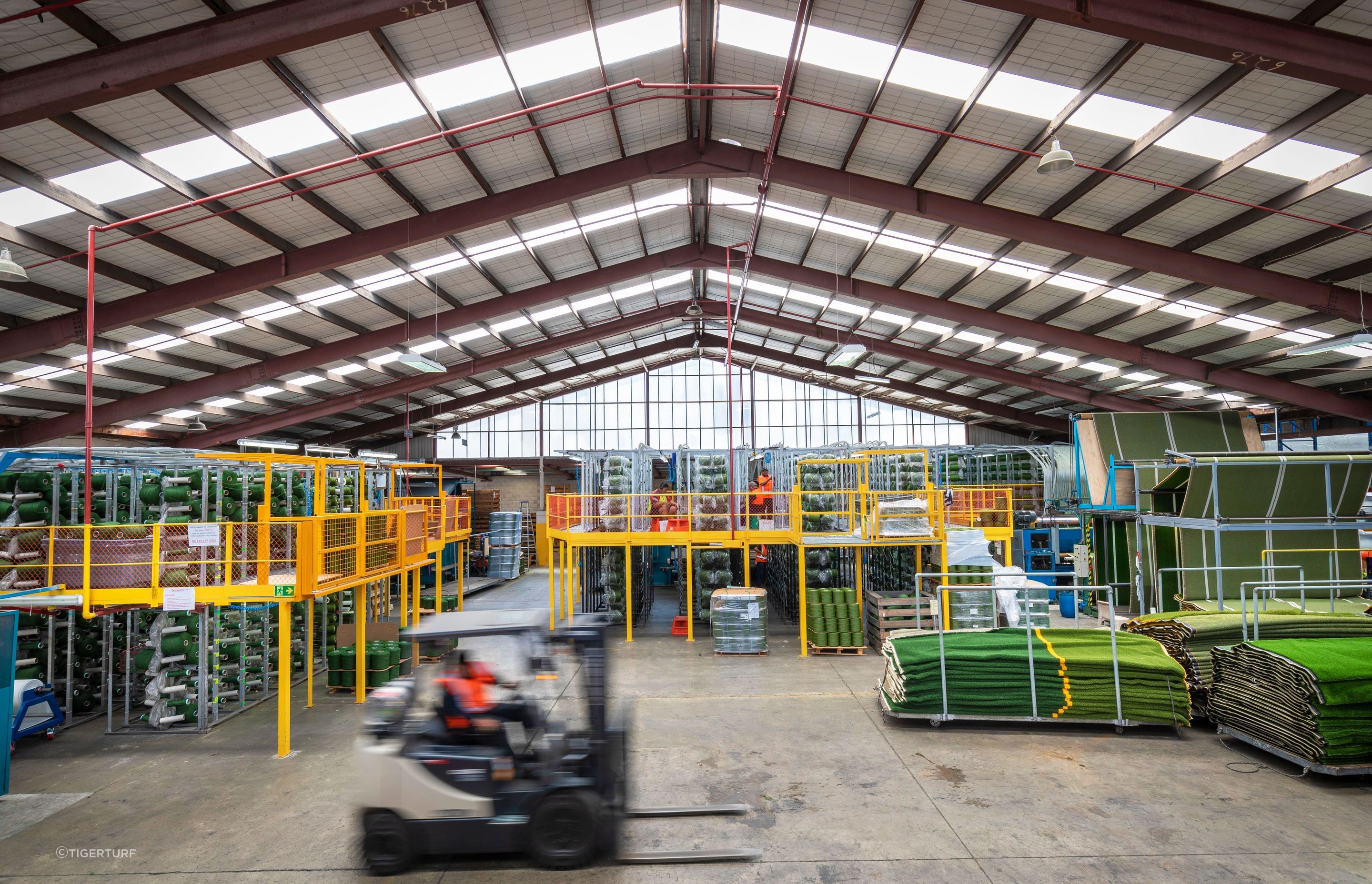