How will 2025 mandatory carbon counting impact architecture?
Written by
10 June 2024
•
5 min read
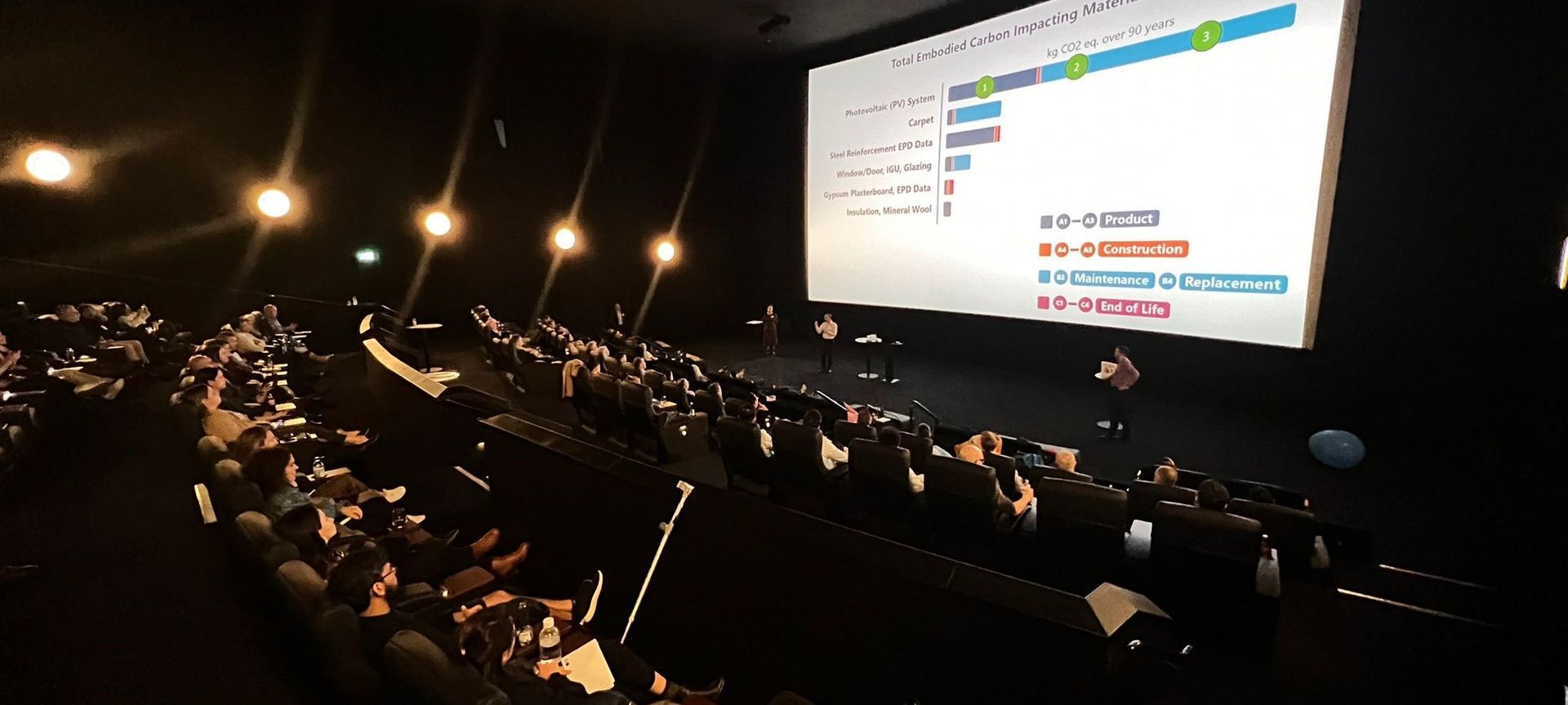
In its Emissions Reductions Plan, the Government has regulated that reporting on embodied and operational carbon for new buildings will be mandatory in 2025, with new building carbon emissions caps to be put in place from 2026-2030.
To learn more about exactly how this will impact architects, designers and the buildings they design, we spoke to TM Consultants managing director Mike Baker, who gives expert advice on how to achieve a compliant, cost-effective building consent.
The new regulations
In order to gain a building consent in 2025, a detailed report on embodied carbon (the carbon dioxide embodied in the physical building materials) and operational carbon (how much is used while the building is operating) must be supplied. For the 12 months of 2025, the Government will collect these reports and identify caps on both embodied and operational carbon that will be set in place from 2026-2030.
“I do think this is a positive step because we're well behind the eight ball,” says Baker. “It’s all about making sure that the amount of CO2 in the atmosphere doesn't get higher because at its current trajectory we could see a one-and-a-half-degree temperature rise which would be catastrophic.”
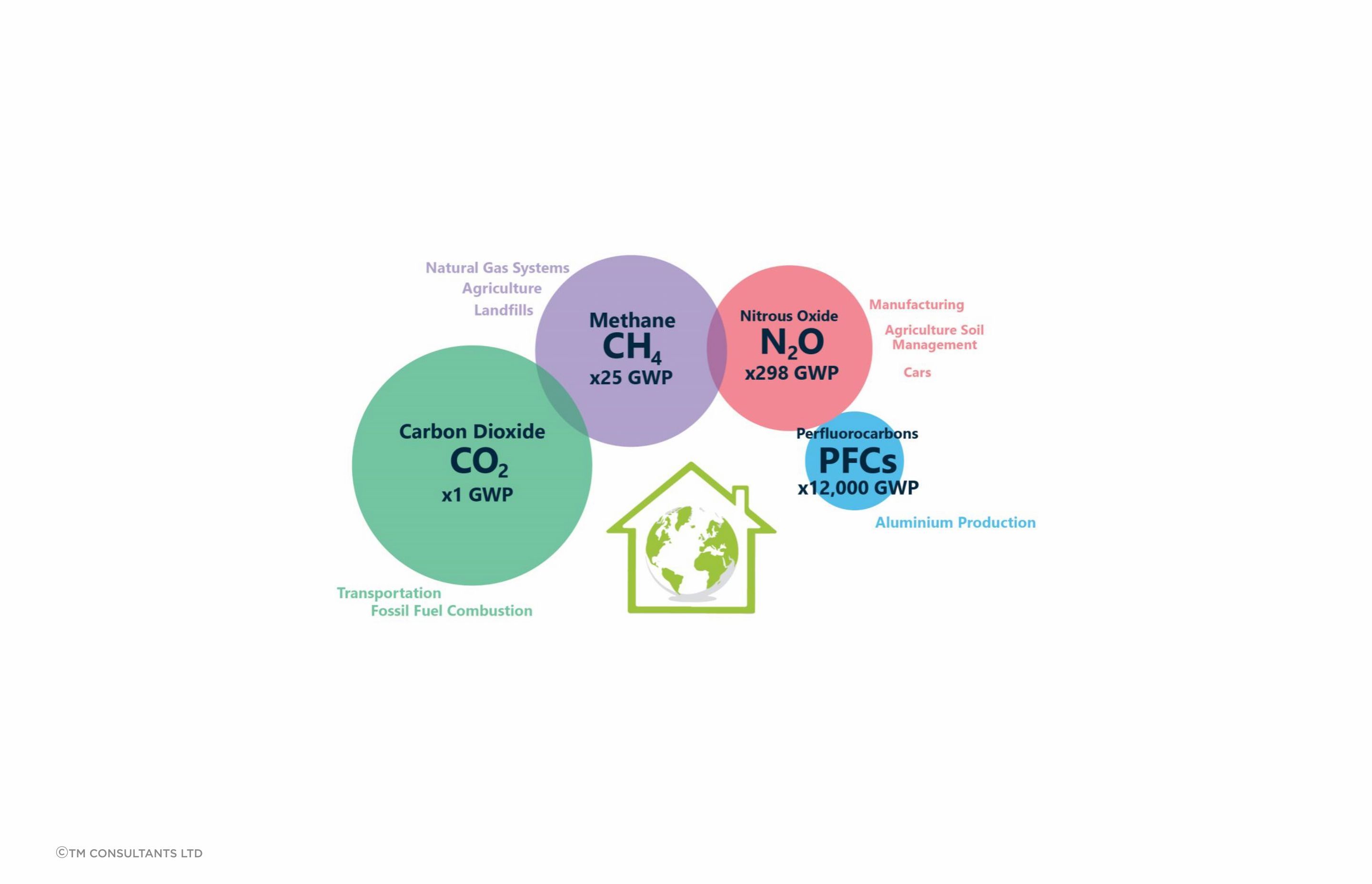
How to measure embodied and operational carbon
For each component within each product in a building, whether it be structural, carpet or air conditioning units, the embodied carbon must be measured and stated in a report. Some products have a product declaration certificate – called an EPD – stating the exact number of kilograms of CO2 embodied in the product. For products that don’t supply this information, architects will have to request it from the manufacturer, which isn’t as accurate.
“If you don't have an EPD, that information you put in the report has to have some factor of safety, which means you automatically have to inflate the amount of CO2 in that product because they haven't given you an EPD certificate,” warns Baker.
Doing so may increase the amount of carbon dioxide embodied in your building design which could put you over the threshold and stop you from getting building consent.
So how will this impact the construction industry? Baker says those products with EPD certificates will be increasingly specified, while those without will be specified less.
“It's going to have a reasonably big impact on those suppliers that don't have an EPD certificate and it will also lift design costs because it's more time you're going to have to spend on researching materials.”
In terms of designing buildings to achieve the caps that will be put in place from 2026 onwards, it could also impact on which materials are chosen. Designs will need to comply with a ‘reference’ building, which is the same building but with predetermined carbon limits on it already, and every single component of the building must be measured and come under those limits.
“If it says X kilograms of CO2 are allowed in the reference building, you somehow have to balance your materials to make sure you are below that, so if you had heaps of concrete then maybe it means you're going to have to use less carpet.”
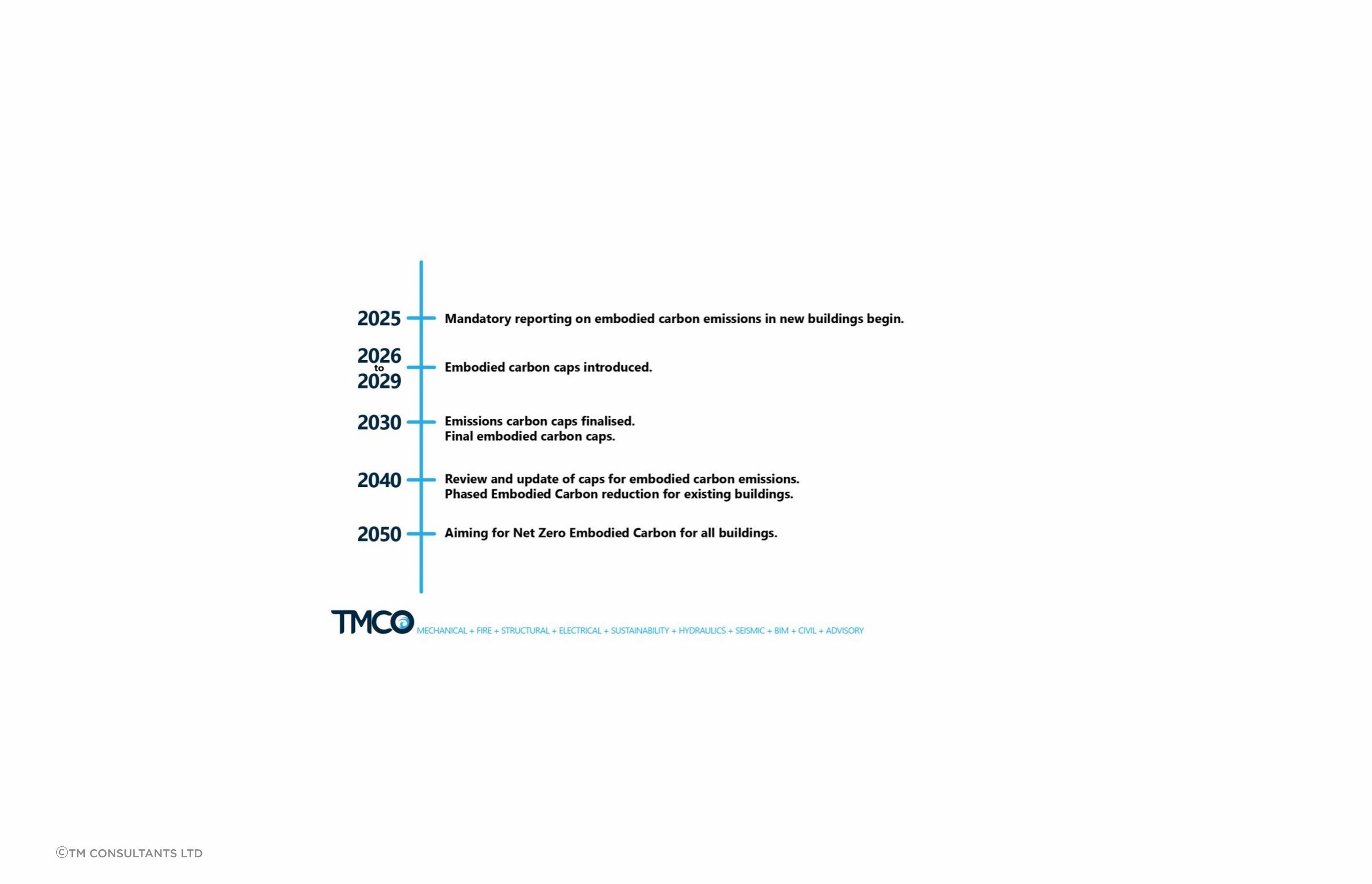
What architects & designers need to know about mandatory carbon reporting
Anyone embarking on designing a project next year will need to keep in mind the extra time cost of researching materials, reporting, and how this will impact on the design timeline. Architects and designers can undertake reporting work themselves or they can engage a consultant to supply the report.
“We have our own libraries of materials showing how much carbon is in each product so we’re well placed to create those reports,” says Baker.
Calculating the carbon content is not always simple. For example, steel has different numbers depending on where it's coming from.
“Having that insider insight is really valuable, and also having that significant knowledge of the building materials,” shares Baker. “But it’s not only on the construction side; we have structural engineers on the building services side, mechanical engineers who have detailed knowledge of air conditioning systems, electrical engineers for lighting, and energy engineers who do all the modelling. It's not a new thing for us, but it's a new thing for the industry!”
When using a consultant, Baker says early engagement is key, because the structure of a building will generally have 50% of the embodied carbon tied up in it.
“If you need to comply, you can’t wait until it's the end of the design concepts and then start doing the calculation and discover you’re miles over. Get those who know involved at the start.”
Having this depth of knowledge at your fingertips means any design is possible.
“We can make any material work so long as we're engaged at the outset. If you want to do a concrete building, we can make that work, but we have to be careful how we make it work so that we don't go over those numbers.”

How can you reduce your CO2
Baker says reducing CO2 in the upgrade of an existing building requires clever tactical moves right from the outset of the design. A case in point is the renovation of the University of Auckland’s 202 building, which achieved a six-star Green Star rating by reusing much of the existing structure, while working around it to create a beautiful new space.
The “reuse and recycle” mentality is also important in the designing of new buildings, says Baker.
“When you're designing a building, design it with deconstruction in mind rather than demolition.”
Explore projects by TM Consultants