Joey Chalk shares his passion for handcrafting timber pieces for the home
Written by
18 October 2022
•
6 min read
From following his dad around the building site at a young age and helping to make boats and kites on the weekends, Joey then graduated to helping on the tools as a teenager. His grandfather also left an impression with the beautiful pieces of furniture he made. Because of these influences, Joey knew early on in his life what he wanted to do.
“I’ve always thought that you should give anything you’re interested in a go,” he says.
“My father really encouraged me in high school and funded my first project and everything spiralled from there – I realised I could do what I love doing and it led to what I’m doing today.”
Joey’s first project wasn’t making the bespoke furniture pieces that are produced in his workshop today, though.
“I was really into skateboarding and I had an idea to make a skateboard that would be stronger. Turns out, my idea was bollocks,” he laughs. Still, Joey started a skateboard company in high school, making and selling his designs to local shops.
“I quickly learned what quality control meant and what customers expected. It really opened me up to the idea that I can make whatever I want, for the right audience.”
A background in building
After graduating high school and looking for the next step in his career, Joey officially joined his dad on the job site before stepping out on his own and creating Kingpost Builders.
“I really liked working on villas and bungalows where there was a lot more craftsmanship involved and having to tie into the existing features of the house, taking care with each step.”
After being diagnosed with bowel cancer, though, Joey says it was time for him to rethink his career: “That’s when, while I was on chemo, I started seriously tinkering with making furniture. By the end of the time I was better and able to work again, I had a handful of clients asking for pieces of furniture.”
The logical next step was for Kingpost Builders to become Kingpost Timberworks.
“In hindsight, we probably should’ve changed it to what it is now, which is Joey Chalk Fine Carpentry & Woodwork, because it’s taken me 10 years to realise that it’s my idea and my passion that is really behind each project.
“I really enjoy the challenge of a new project when someone contacts me and they’ve got this much space to work with, they want this material and they want to incorporate x and y – it becomes a 3D puzzle.”
It’s taken me 10 years to realise that it’s my idea and my passion that is really behind each project.
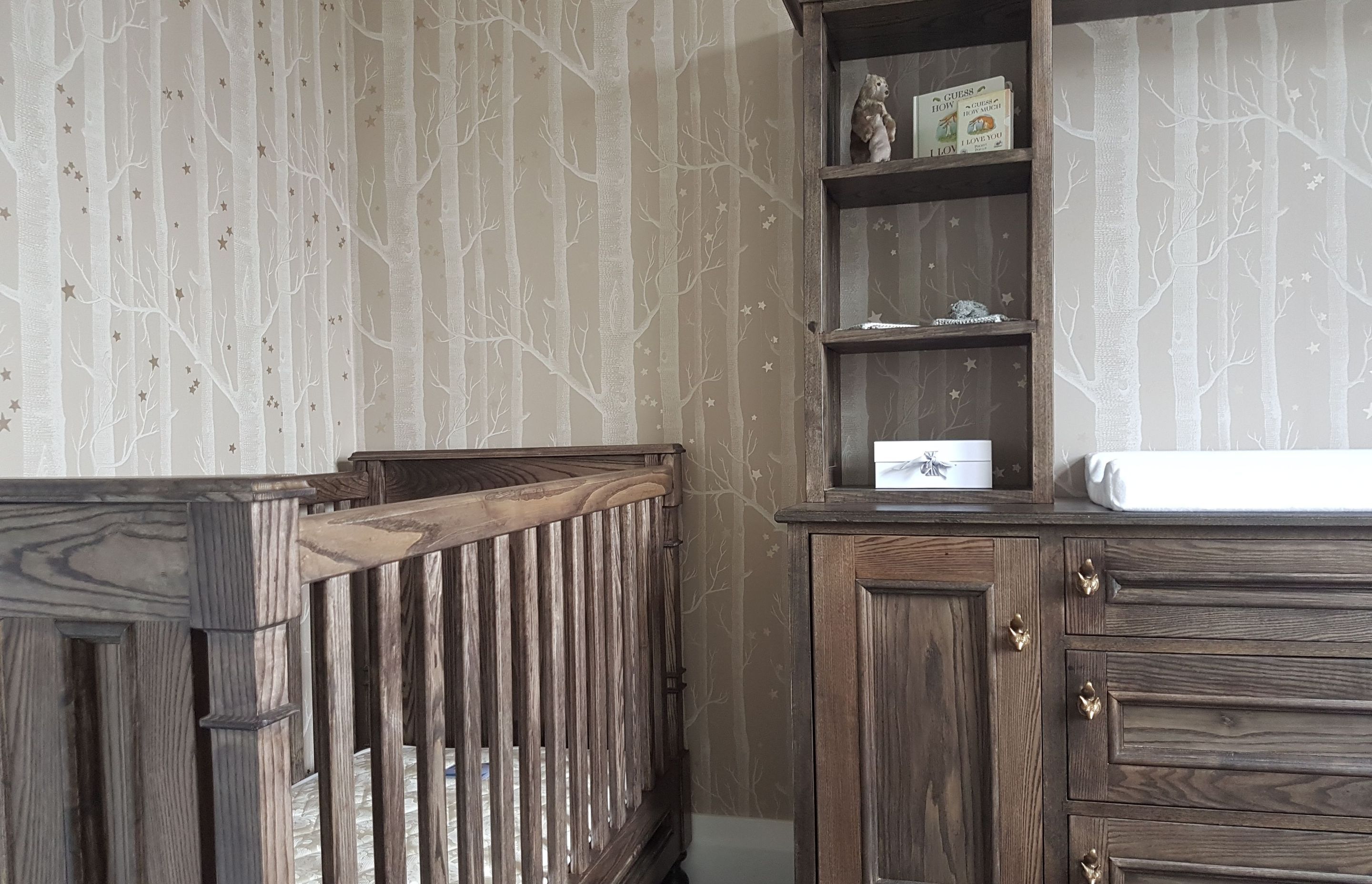
Joey’s approach to making furniture all comes back to the same mindset that saw him create a skateboard company: a fascination with making things, and making them well.
For this reason, he loves one of a kind pieces.
“We typically don’t do more than two or three of any one thing; maybe a set of dining chairs. I have been asked to make 500 of this or that, and that’s not really what we’re about,” says Joey.
“With each job, I know the details 100%. Often, I think people’s designs are not fully grasped by the people making it; it’s just another job that gets pumped through the system. Whereas, if I don’t understand the job completely, I really can’t make it. I’ve got to be right in it for the week or two I’m working on the job, and then I clear the cache and get into the next job.”
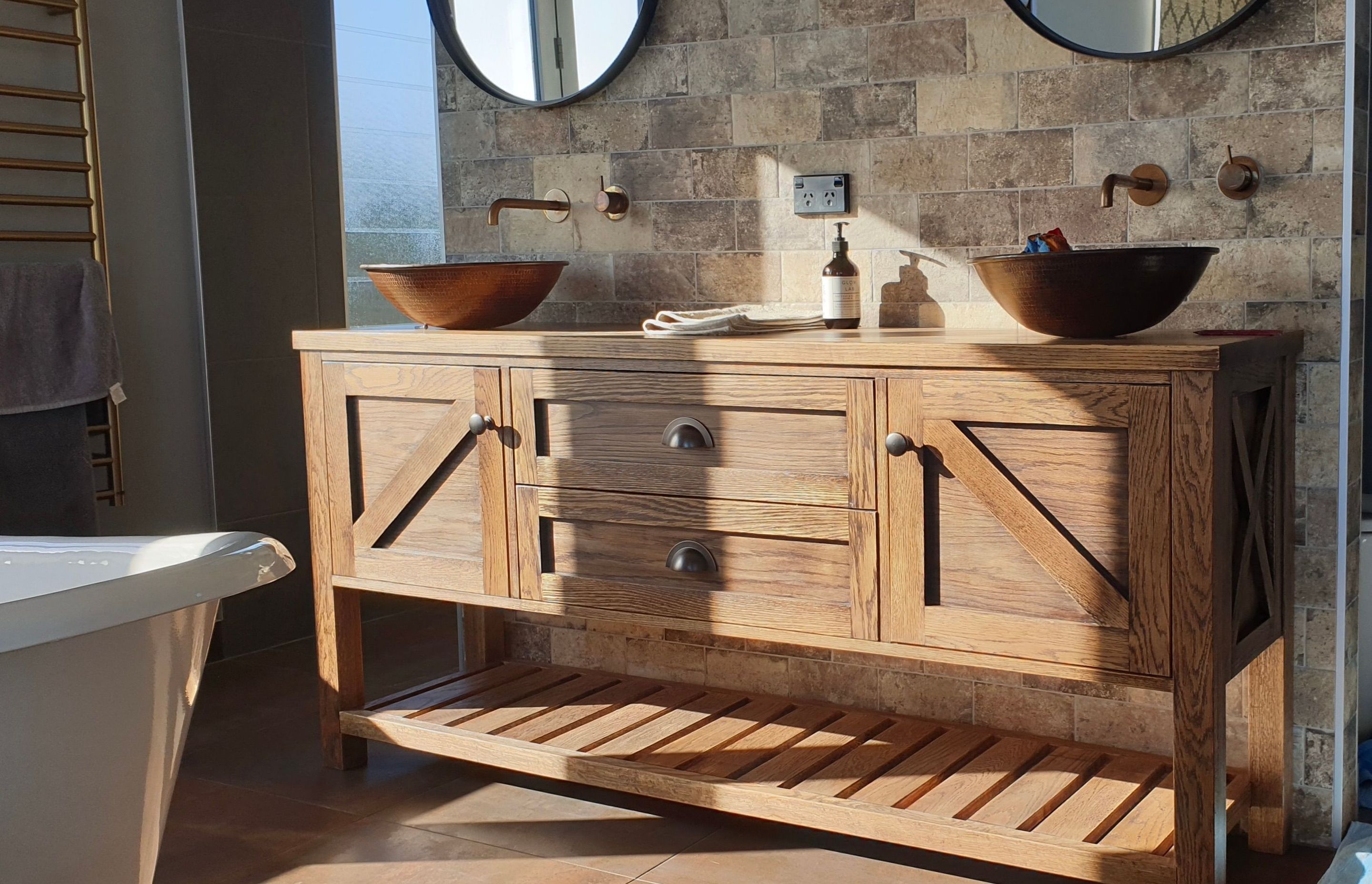
I’m here because there’s a very specific reason for needing something custom made.
Crafting bespoke timber pieces
No two jobs are ever the same for Joey, but he says that having a guideline for custom projects is important.
“As soon as you introduce a constraint, that amplifies the design ideas tenfold. If you have a limited palette and limited space, that gives the creativity much more freedom.”
For instance, specifications such as how many people a dining table is required to fit, or the size of the space it will sit in, allow Joey to bring a clear vision to life. Often, his designs will also include a unique addition.
“Typically with my jobs, there will be one or two features which no one else has done – which is why they’re coming to me. Maybe the client wants to incorporate a powerpoint into their dining table, or they want a shelving unit that incorporates grandma’s old vase.
“I’m here because there’s a very specific reason for needing something custom made, and it’s those sorts of things that really need to be thought about.”
Once Joey has an idea of the overall project, he makes a 3D model to determine how a piece is going to be made.
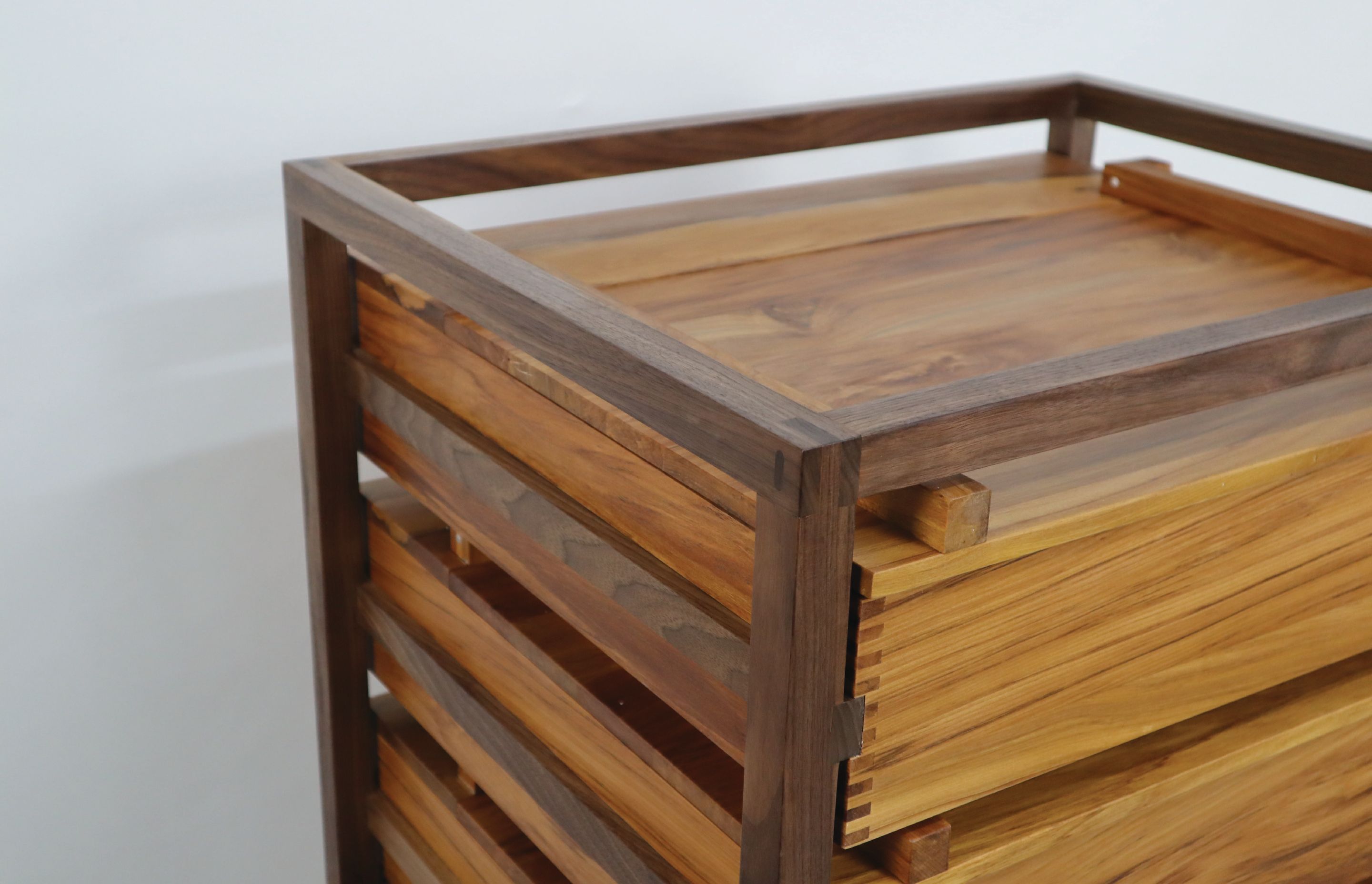
Of course, while each Joey Chalk creation is made in a traditional way, the bespoke designs are often far from traditional.
“People’s living spaces are getting smaller as the cost of building increases, and so people are trying to incorporate more things into that one space. A good example is the tiny house phenomenon, where you’ve got someone who wants a bed that folds up into a couch and then the TV pops out from under it somewhere as well.
“A lot of my job is actually engineering and inventing ways to fulfil the brief. It’s one thing for an architect or designer to say you will have a foldout TV unit, but it’s another thing to actually work out how to do that and make it work on a daily basis.
“That’s an awesome challenge to have to figure out. It might be a very utilitarian piece, but there’s a lot of thought that goes into making these things work.”
Currently in the stage of setting up a new workshop location which will eventually include a showroom, Joey is excited to finally be able to show his work and collaborate with clients in person on these sorts of projects.
“It will be a nice quiet space away from the machines where we can talk, look at samples, look at pieces of furniture that I’ve made and have a much better feel for what you might expect to get, rather than just seeing sawdust on the ground all the time,” he laughs.
Explore Joey’s latest work on ArchiPro.
Words by Cassie Birrer