Local business sets goal to become the most sustainable architectural hardware company in the world
Written by
18 August 2024
•
5 min read
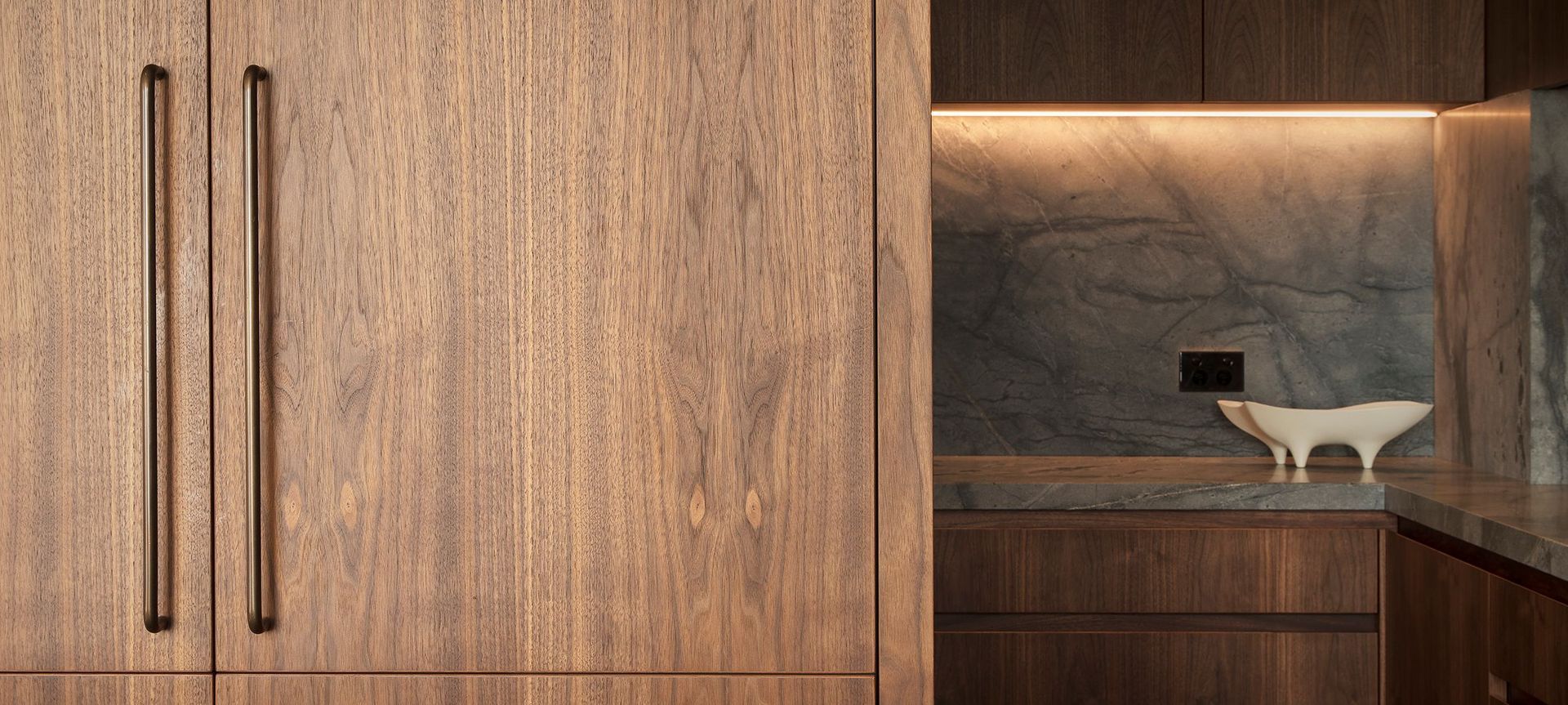
Halliday + Baillie is known for their beautiful architectural hardware, with pieces installed in homes and workplaces worldwide. Now, the business is looking to add another qualifier to their reputation.
“Our vision is to become the most sustainable hardware company in the world!” says Tiffiny Hodgson, Director of Halliday + Baillie.
“I know it seems like a grandiose statement, but everything we do leads us a little closer. We’re aiming to be a front-runner in the architectural hardware industry by leading the way in both sustainable manufacturing processes and ethical practices. Fair pay and robust health and safety for everyone involved in the manufacturing process is also important, not only for overall product quality but also for the quality of life of those working with us.”
ArchiPro caught up with Tiffiny Hodgson to learn more about Halliday + Baillie’s journey towards sustainability, and how they’ve implemented practices within the business to help them achieve their goals.
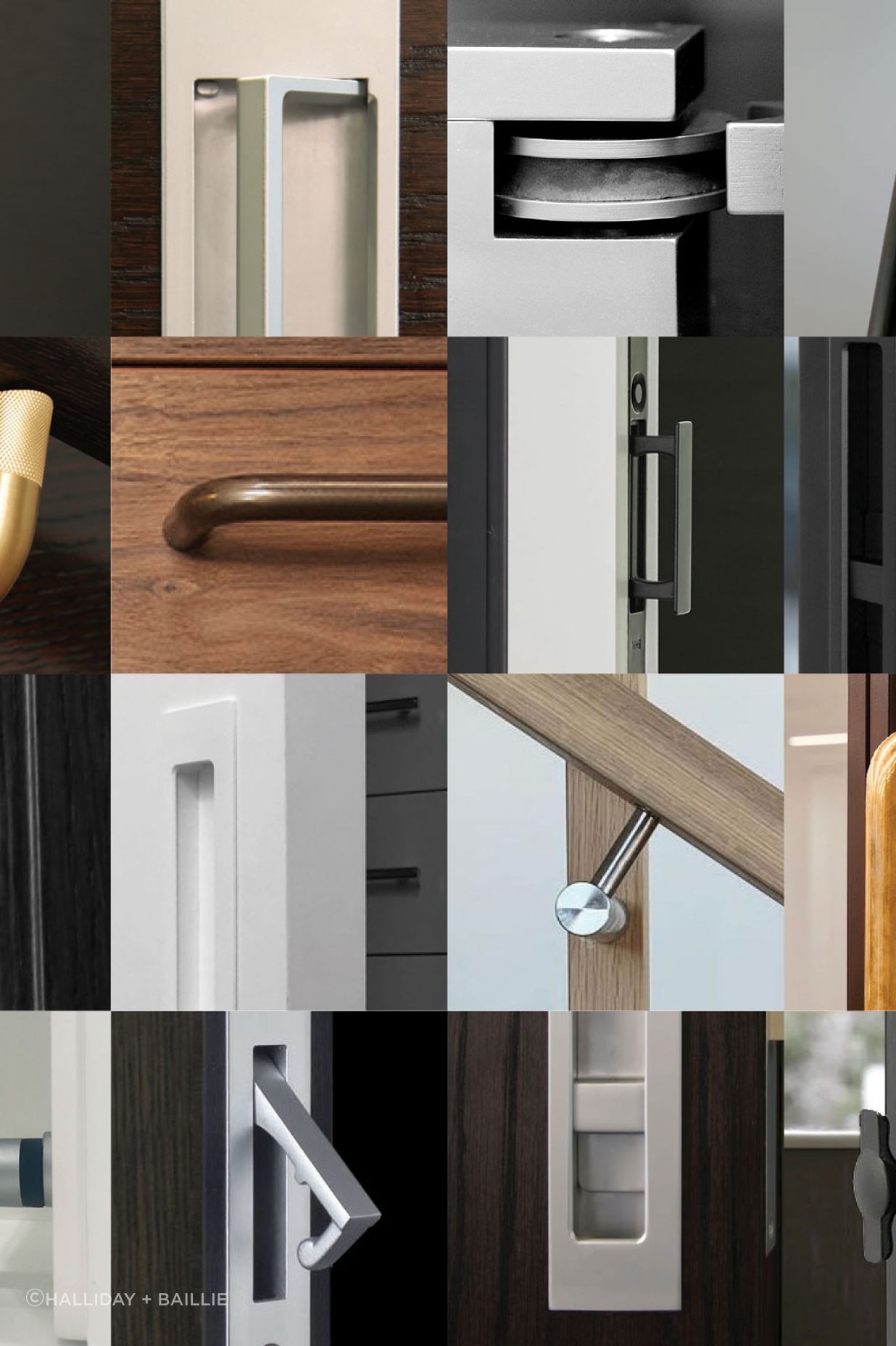
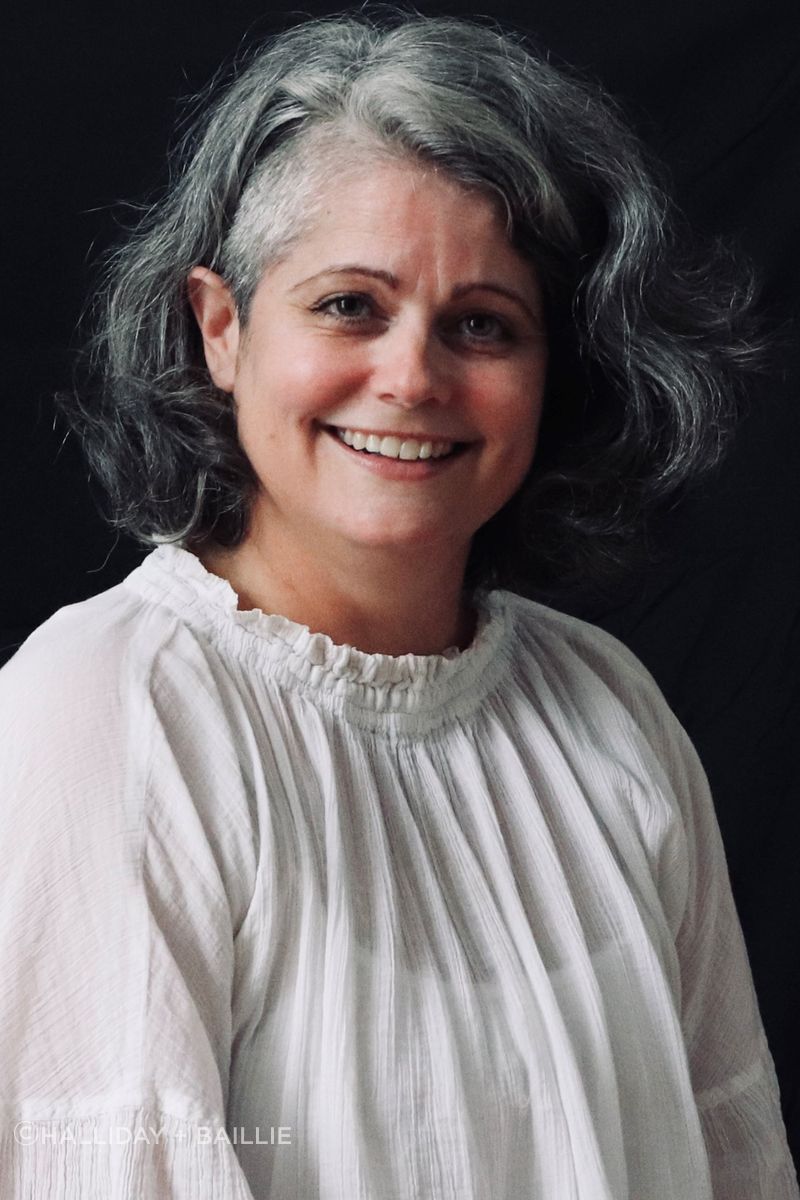
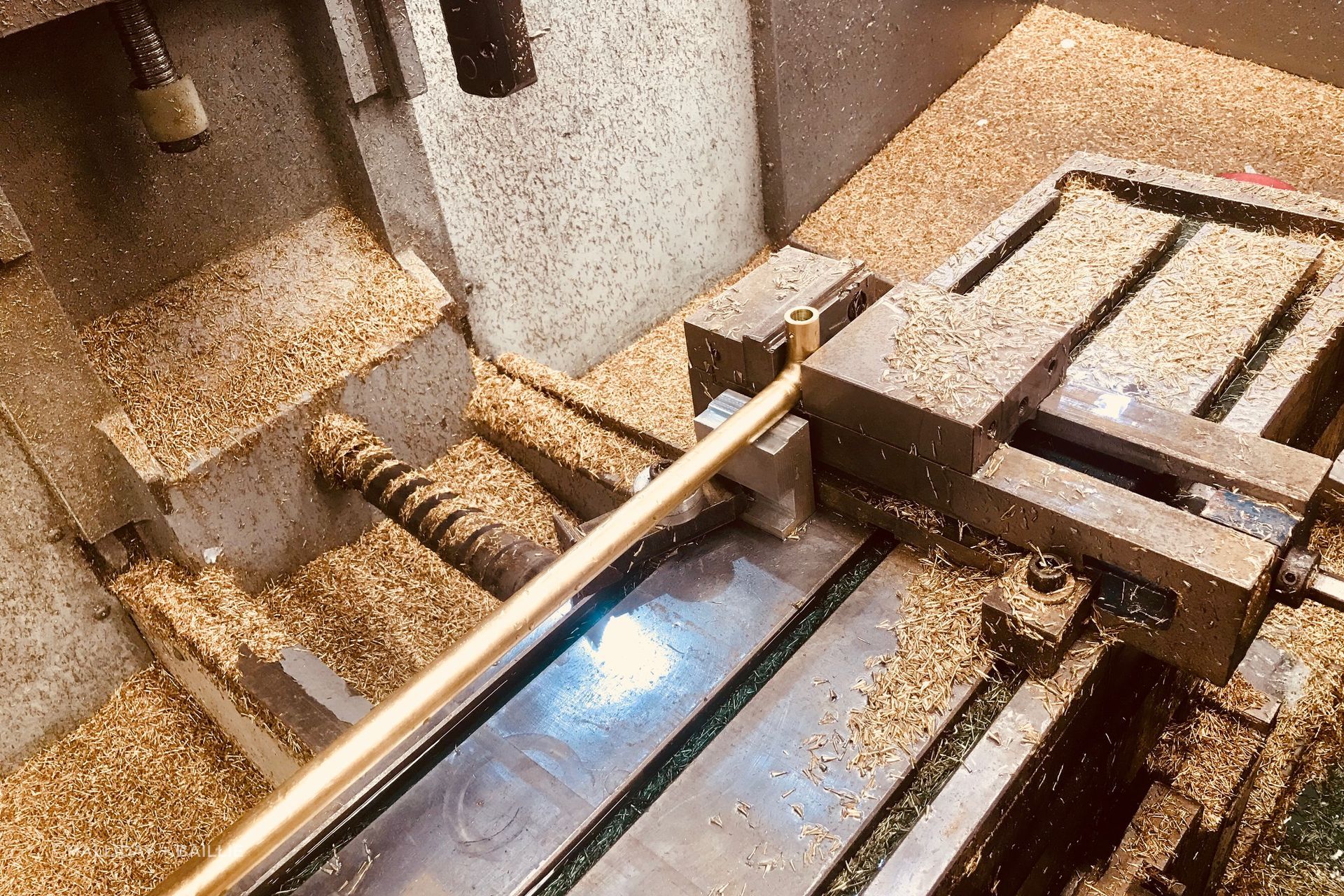
Sustainability at Halliday + Baillie
When running a sustainable business, you need to consider both the activities of your business and those of the companies you partner with at every stage of the product life cycle. For Halliday + Baillie, this means working with manufacturers in New Zealand who share their environmental goals.
“We make sure we are working not just with ‘best in field’ manufacturers, but those who are accredited producers working to ensure traceable provenance of materials used, who comply with international standards of environmental management, and provide high levels of employee safety,” Hodgson says.
“As a New Zealand designer and manufacturer, we are proud that over 98% of all the components and packaging used for our products are made here in New Zealand. To keep our footprint even smaller, most are made within 20km of our head office.”
Alongside choosing local components and packaging, H+B encourages the use of recyclable materials where possible, choosing to work with suppliers who are dedicated to reducing the consumption of materials used in manufacturing, and downstream waste.
“All of our milled, turned, and CNC components in brass, stainless steel, and aluminium are made under ISO-certified conditions including complying with internationally agreed standards on environmental management systems. This ensures efficient use of resources and reduction of waste.”
Implementing waste reduction includes safe and sustainable management of chemical waste, too.
“Our brass, stainless steel and aluminium products are RoHS and REACH certified (the European Union’s directive for the restriction of hazardous substances). This confirms that the proportion of hazardous or difficult to dispose of substances such as lead, mercury, hexavalent chromium, and cadmium are less than the maximum allowed under international law,” Hodgson explains.
“We also ensure that no liquid chemicals, solvents or caustic solutions are used in our manufacture. The powder coat finishes we use are highly durable and corrosion resistant, with negligible total VOCs and formaldehyde emissions which is especially important in indoor environments. All of our powder coating options also comply with international standards for thermoset coatings.”
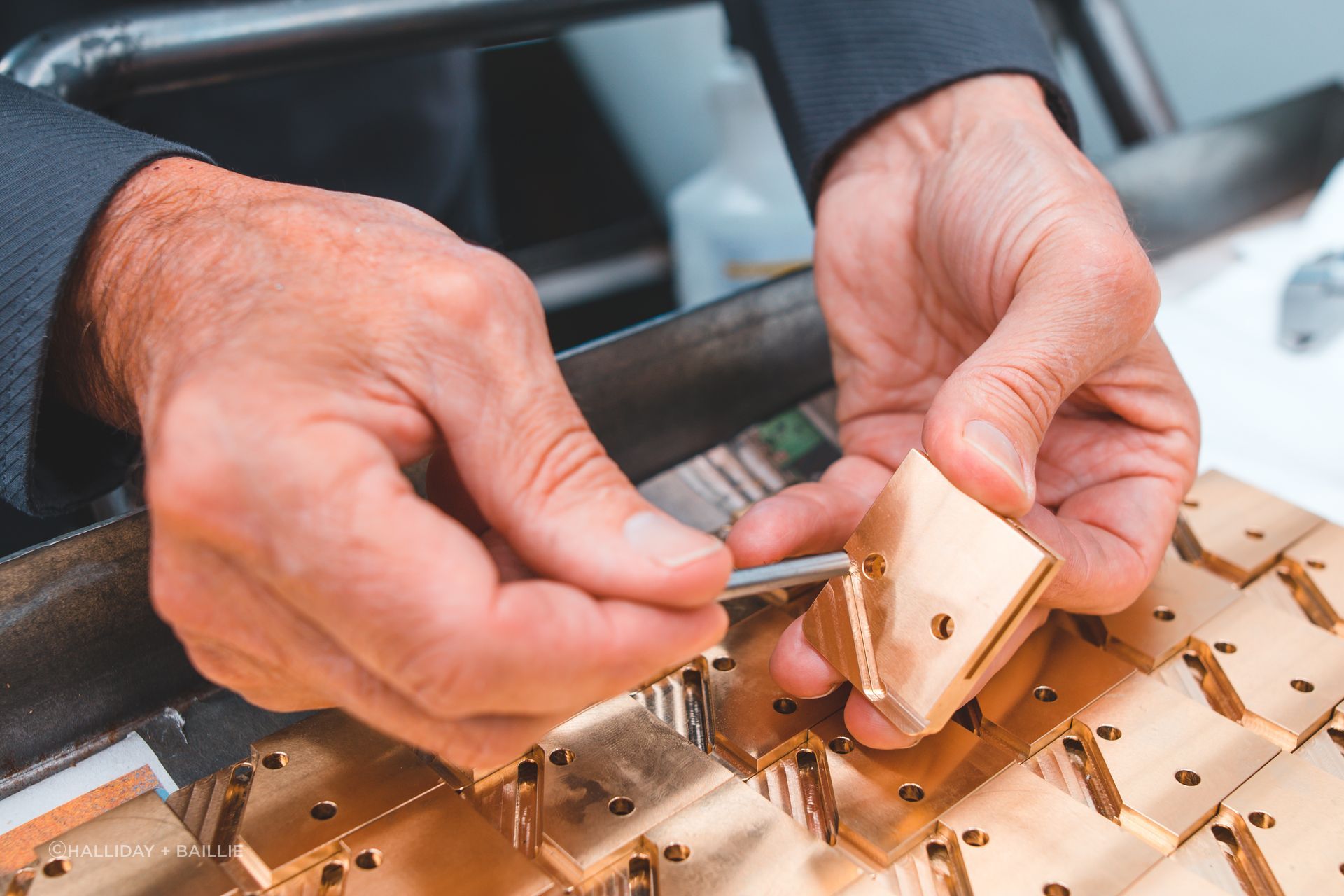
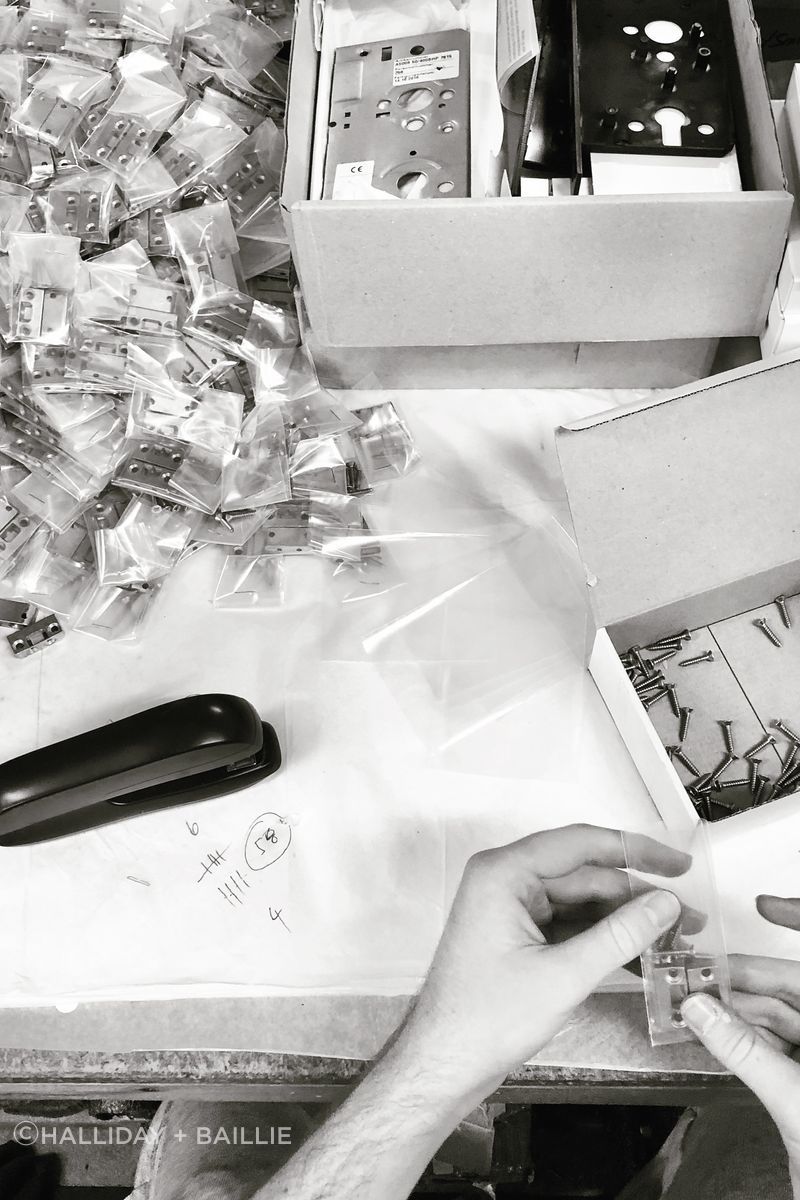
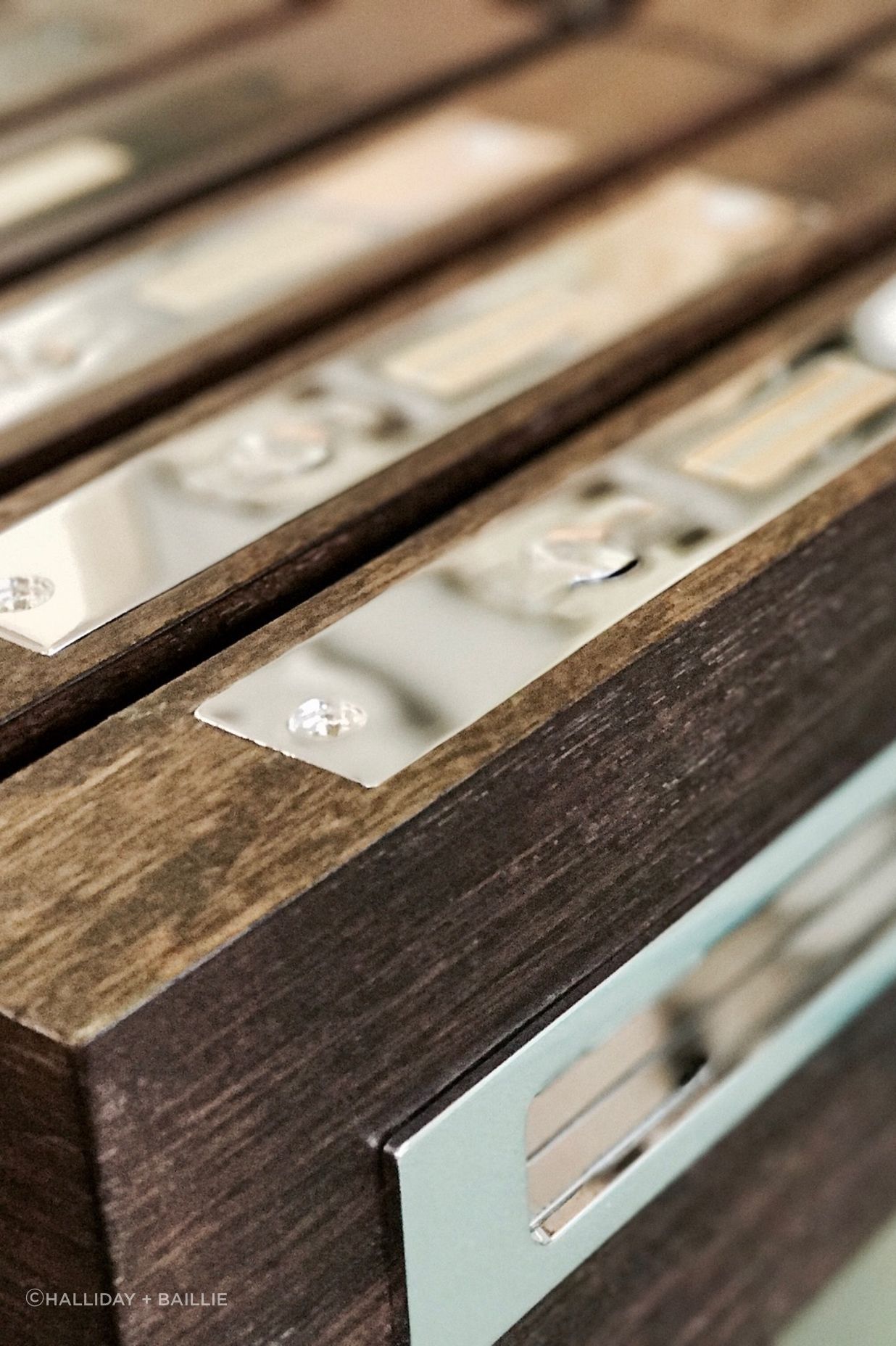
An ongoing journey
Sustainability cannot be achieved overnight, and many of the issues we’re dealing with today will only be mitigated through a collective effort from the industry as a whole. One of the growth areas H+B is looking at right now is packaging.
“Getting heavy, finely finished products from A to B requires carefully considered packaging, especially when “B” is on the other side of the world! We are constantly looking at improvements in packaging not just to safeguard our hardware, but to make a difference no matter which market they end up in.”
Currently, H+B packaging is primarily locally made cardboard boxes printed with compostable inks, and starch loose-fill packing chips that can dissolve in water or be composted. They have started investigating bio-plastics for vacuum sealing and loose bags, and have recently instituted processes for bulk orders where a single set of instructions are sent digitally for the whole order, rather than paper printed and included in each hardware set.
To hold themselves accountable, and ensure their efforts continue to contribute to global goals, H+B look to the expertise of third-party environmental certifiers.
“Monitoring our progress and impact comes in a variety of forms. The most obvious is working with materials, and suppliers that achieve or exceed high-level certification such as ISO 14001 (Environmental Management), RoHS and REACH,” May says.
“Manufacturing has a major environmental impact no matter what you are making. Halliday + Baillie has always been committed to producing all our hardware in New Zealand (with some extrusion products now also running in Australia, for the Australian market) in factories with stringent regulatory frameworks around waste management, contaminants, water use, and material sourcing. Our first choice is to make our products in New Zealand or regions with similarly strict environmental controls. These controls also allow us to be 100% certain of our manufacturing processes and quality, and remain agile when change is needed, or when regulations are updated.”
There are so many things individuals and businesses can do to make a difference, Hodgson says.
“Every change, no matter how small, is a move in the right direction. Don’t be afraid to talk to your suppliers and clients — a community of like-minded companies can make a major difference.”
Learn more about Halliday + Baillie.