Logistics Automation - Think about the Floor!
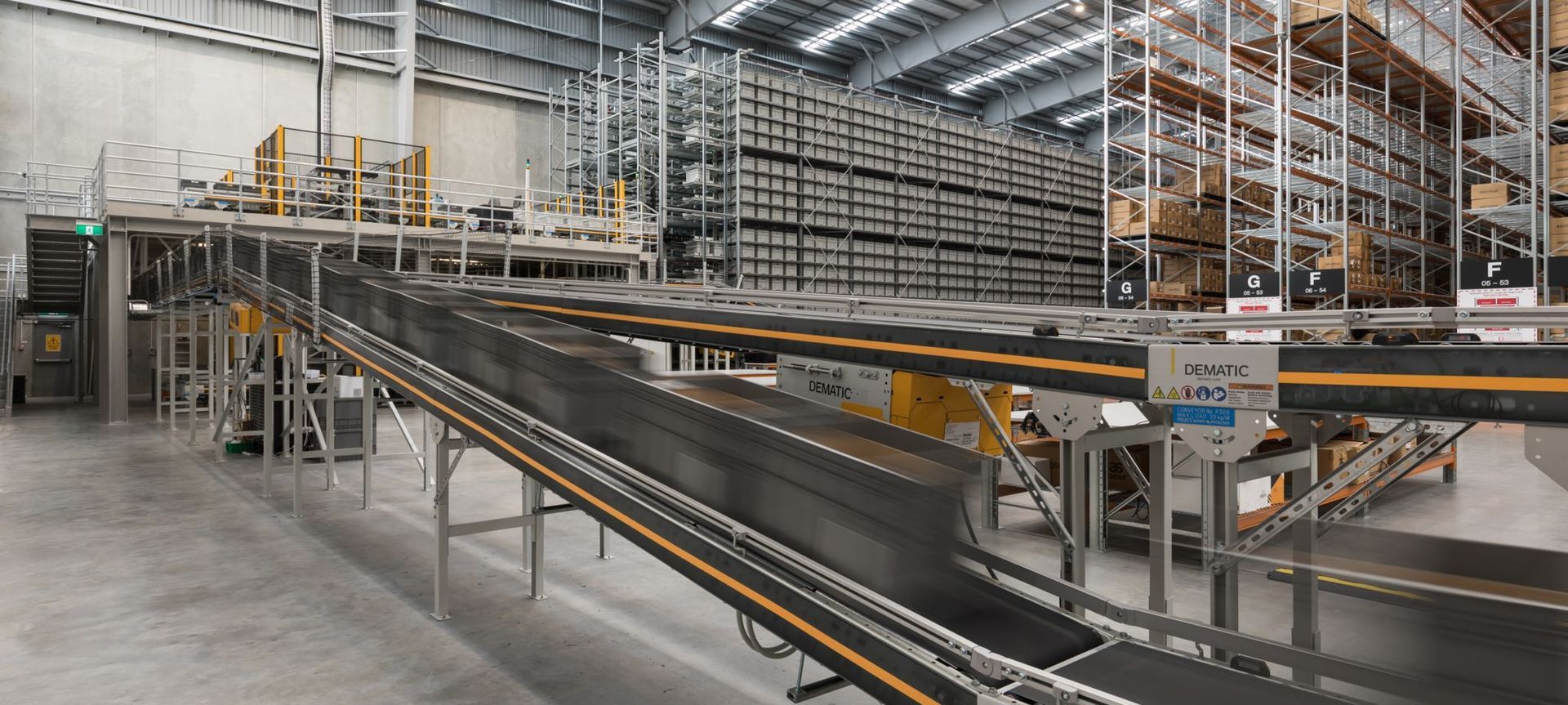
There has been a recent surge in the adoption of automated logistics equipment in New Zealand, ranging from small robots (AGVs/AMRs) to large automated storage and retrieval systems (ASRS).
These automated systems are introducing new and unique demands for industrial floor slab performance. For any companies considering adopting automation in new or existing facilities, it is critical that the suitability of the floor is considered before investing in the automated systems.
Conslab have been involved in a number of automated logistics projects, and have found the following areas require specific attention:
Floor Surface Regularity
Existing standard for industrial floor surface regularity, such as ConcreteNZ TS01:2021, provide a robust specification and measurement framework for conventional warehousing applications. Many automation systems have bespoke specifications for surface regularity (flatness/levelness) which fall outside of such standards.
Small AGVs for example often require precise control of floor regularity over a smaller distance than conventional MHEs, due to their close wheel spacing. Conversely, some automated racking systems require very precise control of surface regularity over a large area, which is not required with conventional warehousing storage systems.
Floor Slab Deflection
ASRS systems require very rigid floors to limit deflection under load, and allow operation of their automated shuttles. Often the slab is specified as “quasi-rigid”, but in the real world it is almost impossible to design a slab which is actually quasi-rigid. If the slab isn’t quasi-rigid then the load from the rack changes as the slab deflects, and slab deflection changes as the load changes. There is a dependency between the two and so you need to iterate to get to the correct answer.
This requires a very different design approach than for conventional slabs, where for a given load case there is a certain slab thickness required to carry those loads. For ASRS slabs the design needs to be iterated between the racking design and slab designer, which requires time that often isn’t allowed for in tight design/construction programmes.
Joint Location and Design
Many automated systems require tight control of floor joint openings and levels. AGVs with small, closely spaced wheels can have issues traversing large or un-even floor joints. The very precise paths of AGVs also results in repeated impacts on specific joint locations, often leading to joint damage and deterioration, further disrupting the AGVs path. ASRS systems typically aren’t compatible with joints at all, and require slabs with no movement joints within the ASRS area.
Given this sensitivity to joints, the key motivation when designing the slabs is to eliminate or minimise the need for joints. If movement joints are required in the slab, careful consideration needs to go into their design to limit deterioration from AGV traffic and allow for easy maintenance and re-levelling if required, such as the patented Conslab Rhino Joint.
Conclusion
To unlock the benefits of automated logistics equipment it is critical that the floor slab is up to the task. In most cases this means some level of customisation of the slab, either by remediating an existing slab or designing new slabs for specific equipment. The days of spec-build industrial floors may soon be in the past.
For expert advice on the best floor slab solution on your next automation project - get in touch with Conslab.