Making an inset pull with Auburn Woodturning
Written by
06 July 2023
•
3 min read

Auburn Woodturning is a family-owned business in Melbourne with a rich history in custom woodturning and creating beautiful wood designs.
Over the last 75 years, their quality craftsmanship and knowledge have been passed down from one family memeber to another. In addition to woodturning, they offer woodworking, computer numerical control (CNC) routing services and sell an array of heritage products, door handles and more.
Giving an exclusive peek into the business' day-to-day, Kerry Curtain from Auburn Woodturning shares the creative process in the reproduction of a circa 1950s inset pull.
The customer always comes first
Inset pulls play a vital functional role for doors. They are a recessed handle fixed within a mortised cavity that allows fingertips to pull the door outward. This project came as a unique customer request, a common occurrence for many of Auburn Woodturning's clientele as custom woodturning is the business' forte.
"The customer supplies drawings, images and a description of what they're ideally after. We then contact the customer with a range of questions to drill down on the measurements, application, and any missing details," says Kerry.
"Next, the workshop assesses our ability to make this to the customer's requirements – weighing up our equipment, know-how and time."
Depending on the design, additional sketches or images may be required including side profiles, outside diameter and any other internal measurements.
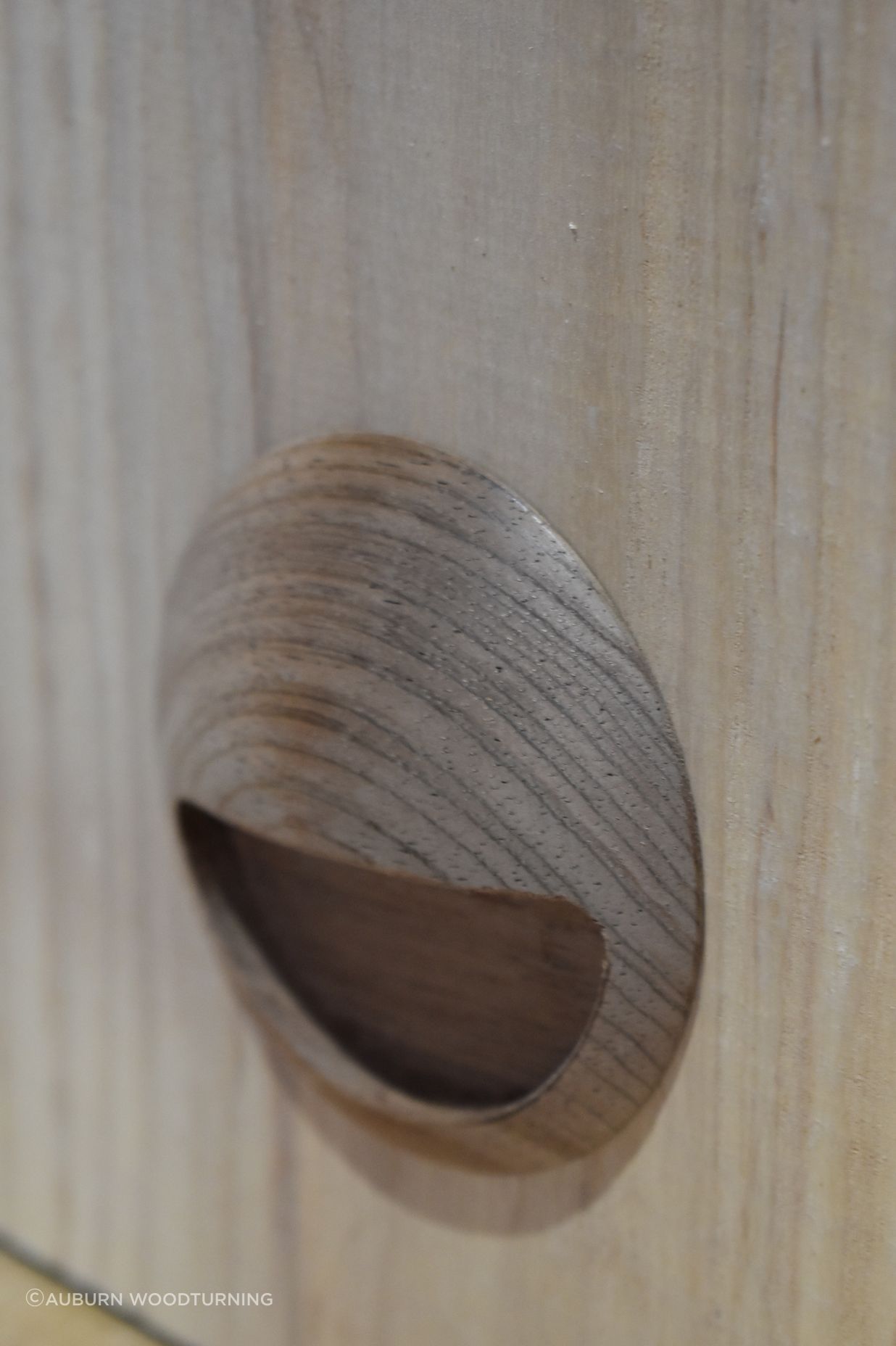
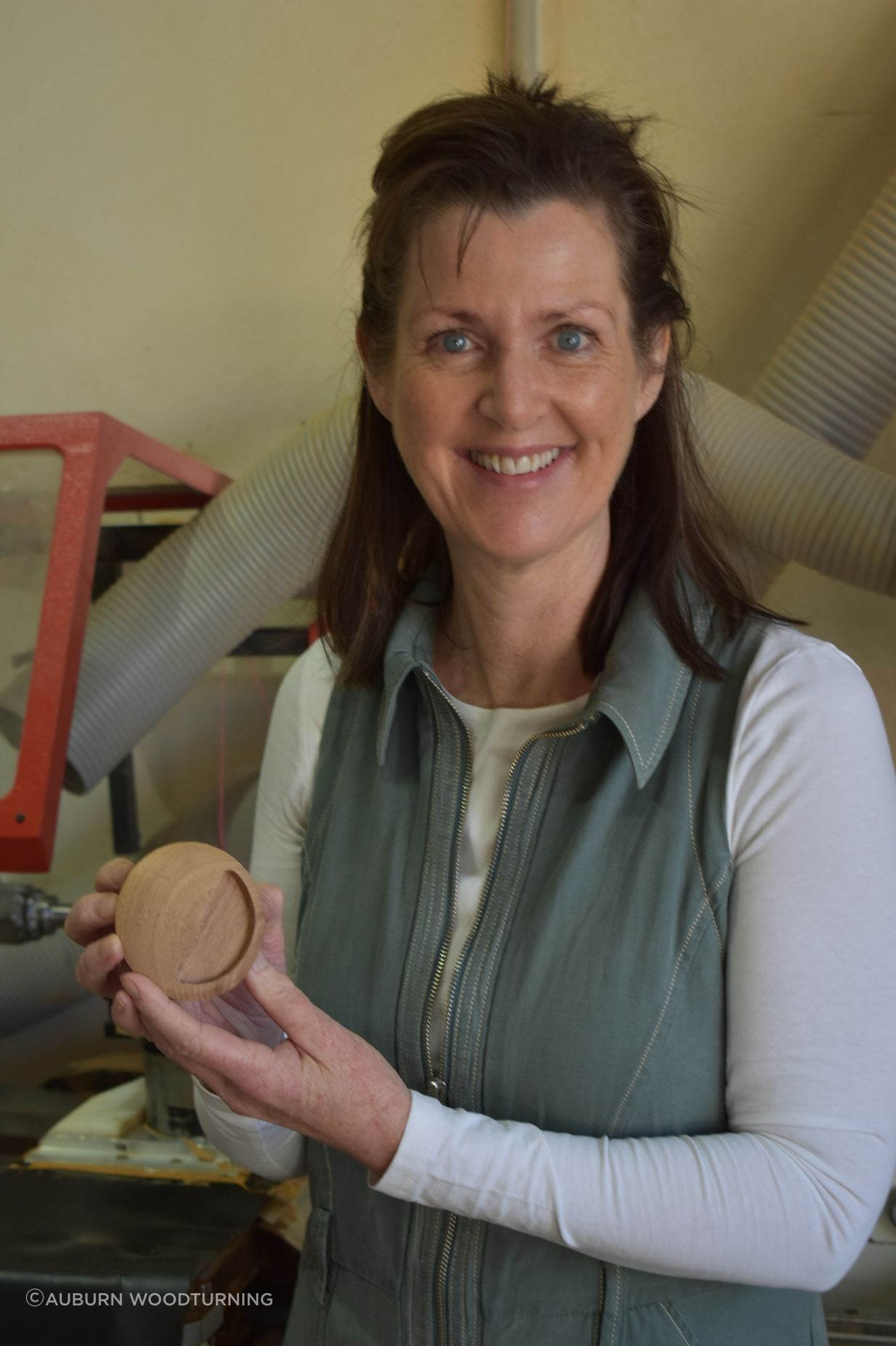
A sample is made to ensure customer satisfaction
The customer selects the type of timber for their project, provided the chosen material is well suited to the piece. Kerry explains that if any element of the production process is new to the team, they create a sample first to ensure the customer is happy.
"This is to ensure the piece can be made to customer expectations and to evaluate complexities, quality and production time. Often this may take two or three shots to get it right."
For this project of a circa 1950s inset pull, three main production processes were involved:
- The overall shape is turned on a lathe
- Cut-out for fingers is run on the CNC router
- The finger groove on the internal underside is hand carved
Photos of the sample are then sent to the customer for feedback. Additional discussions are also held to further hone in on alternations for aesthetics and functionality.
"In this example, most of the serious troubleshooting was around the finger groove in the underside. The tool bits available were not suitable for cutting a functional finger groove. The solution was to outsource the piece for hand carving," says Kerry.
"In these instances where we can, we will refer the customer to another craftsman or business that may be able to assist. It is always good to share."
Finishing is the last step of the process. After the machining, the design is sanded by hand for a smooth fine finish.
Top tip: check Intellectual Property Rights and trust the design process
When approaching woodturners for bespoke wood designs, Kerry advises checking that the intended design is acceptable for re-creation.
"Ensure the design you choose does not infringe on the Intellectual Property Rights of others," she explains.
Her second tip is to stay communicative and collaborative with the workshop team to get the best results.
"The liaison between our customer service team and the workshop works well for customers. They know they have been heard and understood and that we are genuinely giving our best shot at success. Customers truly value this."
Check out Auburn Woodturning on Archipro today.