Protecting and future-proofing interiors with UV coatings
Written by
28 March 2023
•
4 min read

Future-proofing in the architecture and construction industries has never been as important as it is today. There are obvious financial benefits attached to improving a material or product’s longevity – increasing the gap between installation and replacement is a particularly effective way of reducing long-term costs.
But future-proofing also brings an efficiency – and consequently, sustainability – factor into a project. Dedicating resources toward bolstering a material’s durability and postponing its end-of-life cycle goes a long way in keeping that material out of landfills.
UV coatings on interior and exterior panels – including any plywood walls, flooring, soffits and furniture and joinery – boast all of these benefits, plus an additional critical advantage: enhancing long-term aesthetics. By protecting the plywood from UV harm, the coatings defend against fading and discolouration – making the material look newer for longer.
To find out more, ArchiPro sat down with Andre Bates, CEO of Bates Surfaces, to discuss the ins and outs of UV coatings, the benefits and consequences of not using them, and the changes happening in the industry.
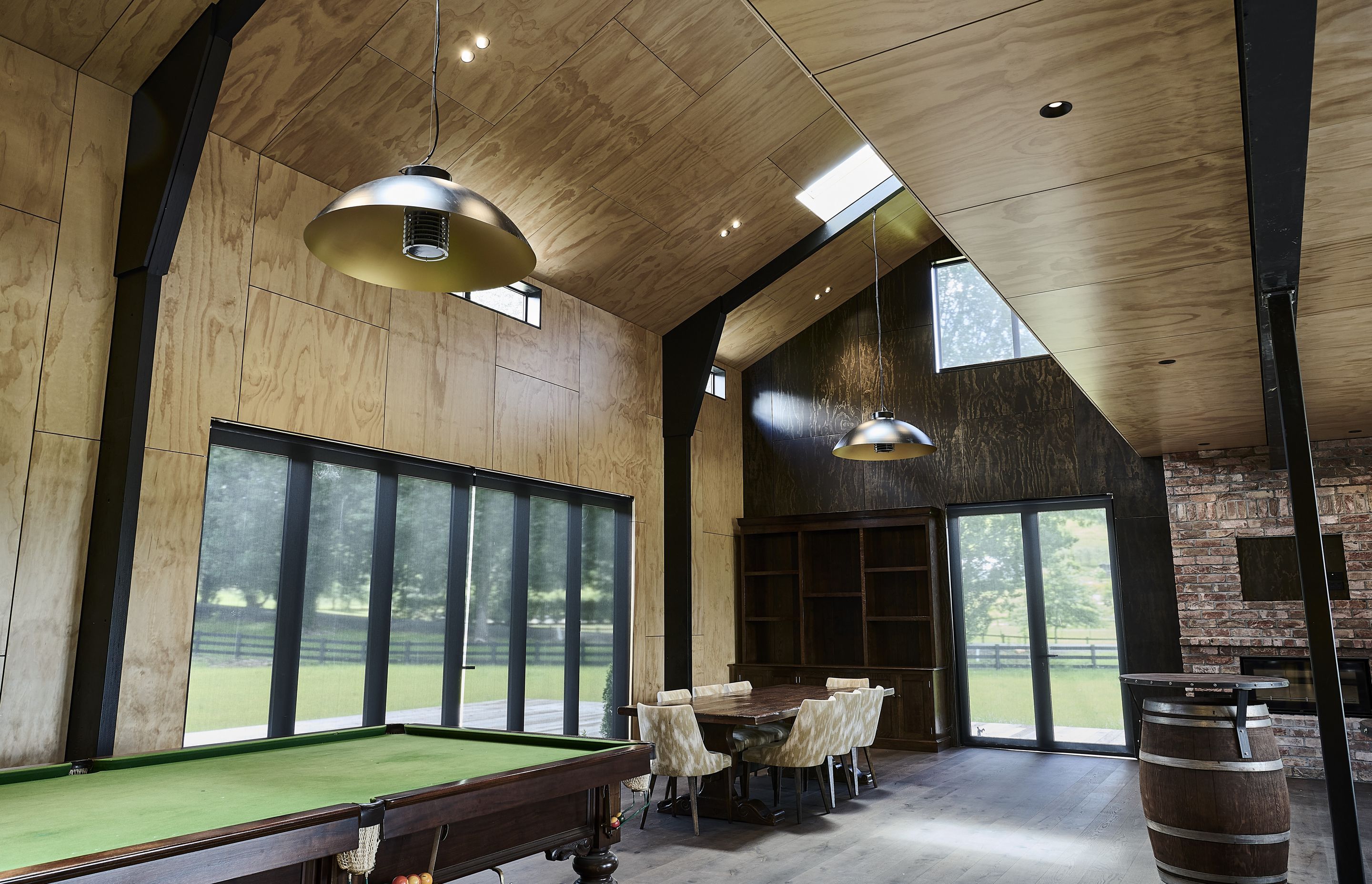
ArchiPro: Can you explain what UV coating is to those unfamiliar?
Andre Bates: It’s a surface treatment and application for substrates, including interior panels, that protects substrates and paint from the damaging effects of UV light. It helps lengthen the life of the surface by boosting its durability and ensuring it doesn’t get sun-faded or otherwise discoloured.
AP: What is the value in coating interior panels with UV coatings?
AB: From a macro perspective, we invested in UV technology many years ago as it offered our process and products environmental and sustainability credentials not available with our old solvent-based technology.
UV coating is an environmentally sustainable technology with a comparatively low carbon footprint, energy consumption and wastage, and it also allows very fast production rates.
Unlike oil or solvent-based paint, for example, UV-coated substrate does not negatively impact the environment or produce volatile organic compounds (VOCs), which are harmful chemicals that leach into the air we breathe indoors.
From a micro perspective, UV coating technology is safest for our employees, is cost-effective, and has better longevity. The following benefits are also associated with our products:
- Protects the substrate and paint against UV harm.
- Accentuates clarity and maintains colour integrity against fading and discolouration, enhancing the durability and extending the ‘new-look’ period.
- Ideal and highly effective in maintaining fidelity on printed boards.
- UV-coated surfaces have better resistance to abrasion and scratches, and offer better hardness.
- It contains antimicrobial properties and does not allow moulds to embed into the coating.
- Easy to clean and resistant to household cleaning products and most commercial cleaning products.
- Protects against VOC from harmful substances such as resins, formaldehyde and other chemicals.
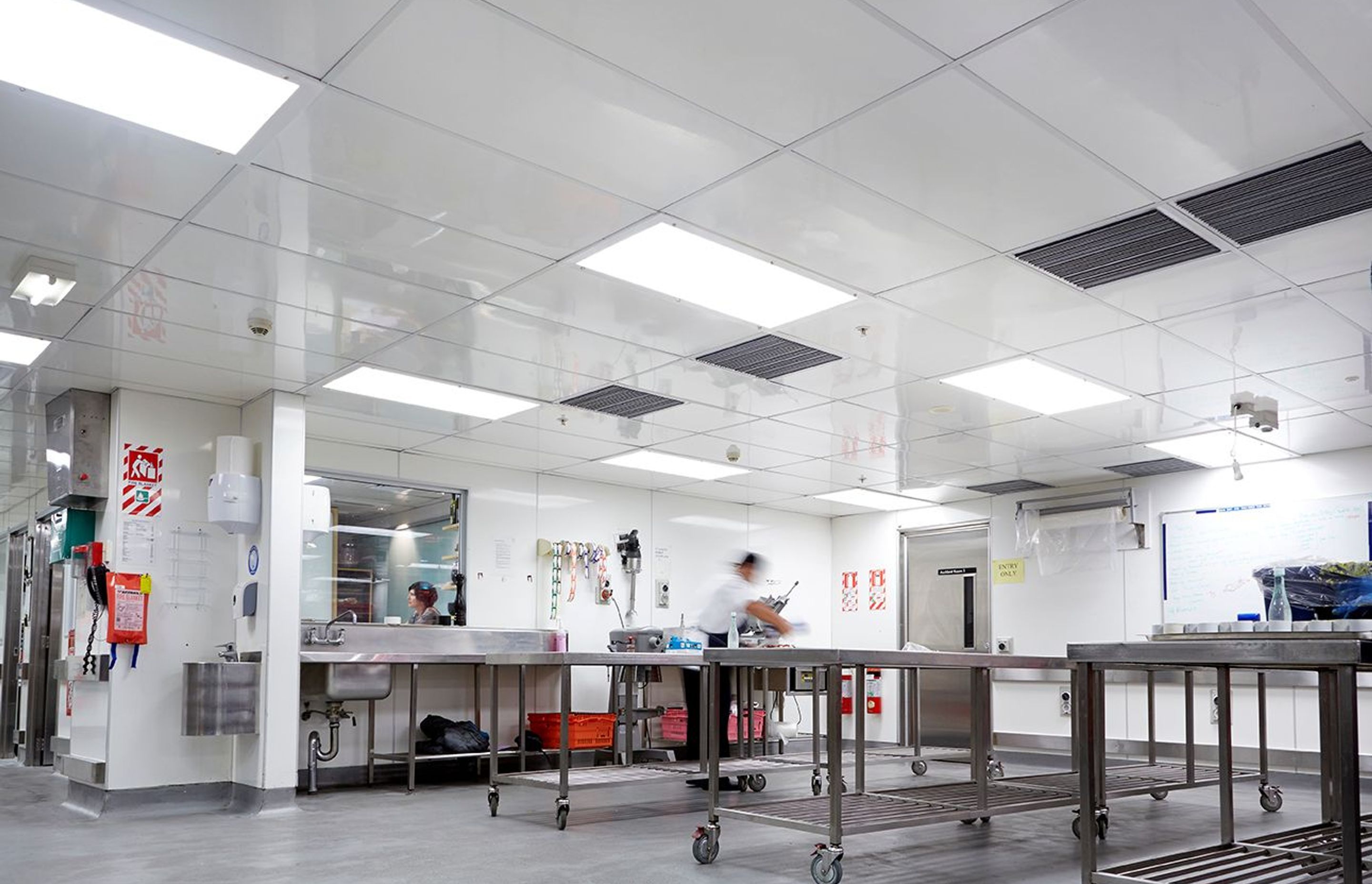
AP: What are the consequences of not protecting panels in this way?
AB: Manufacturers, as well as new domestic and commercial buildings, are increasingly encouraged through regulations and social pressures to be environmentally sustainable. Increasing longevity adds value to any physical investment, and interior panels and surfaces are no exception.
Perhaps more importantly, our UV coatings conform to the Red List Declaration of non-harmful substances, which is a positive for our customers’ health and well-being.
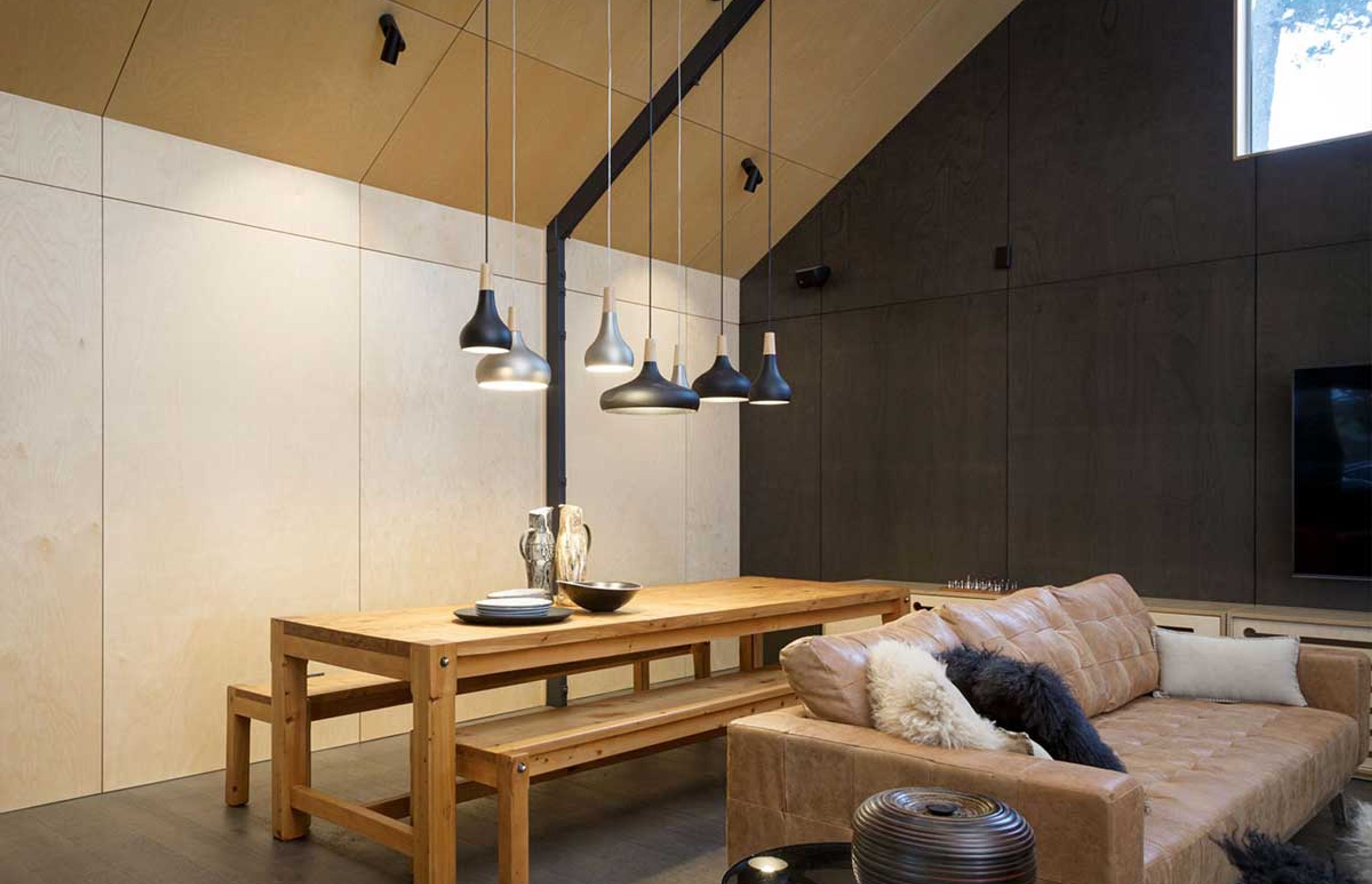
AP: How has technology changed in the last decade or so to improve this offering?
AB: UV technology has progressed from being able to cure clear finishes to now heavily pigmented coatings, which has allowed the use of colour production. UV cure has also advanced to enable a much lower energy consumption, moving from traditional mercury vapour and gallium lamps for pigment coating to the use of LED technology.
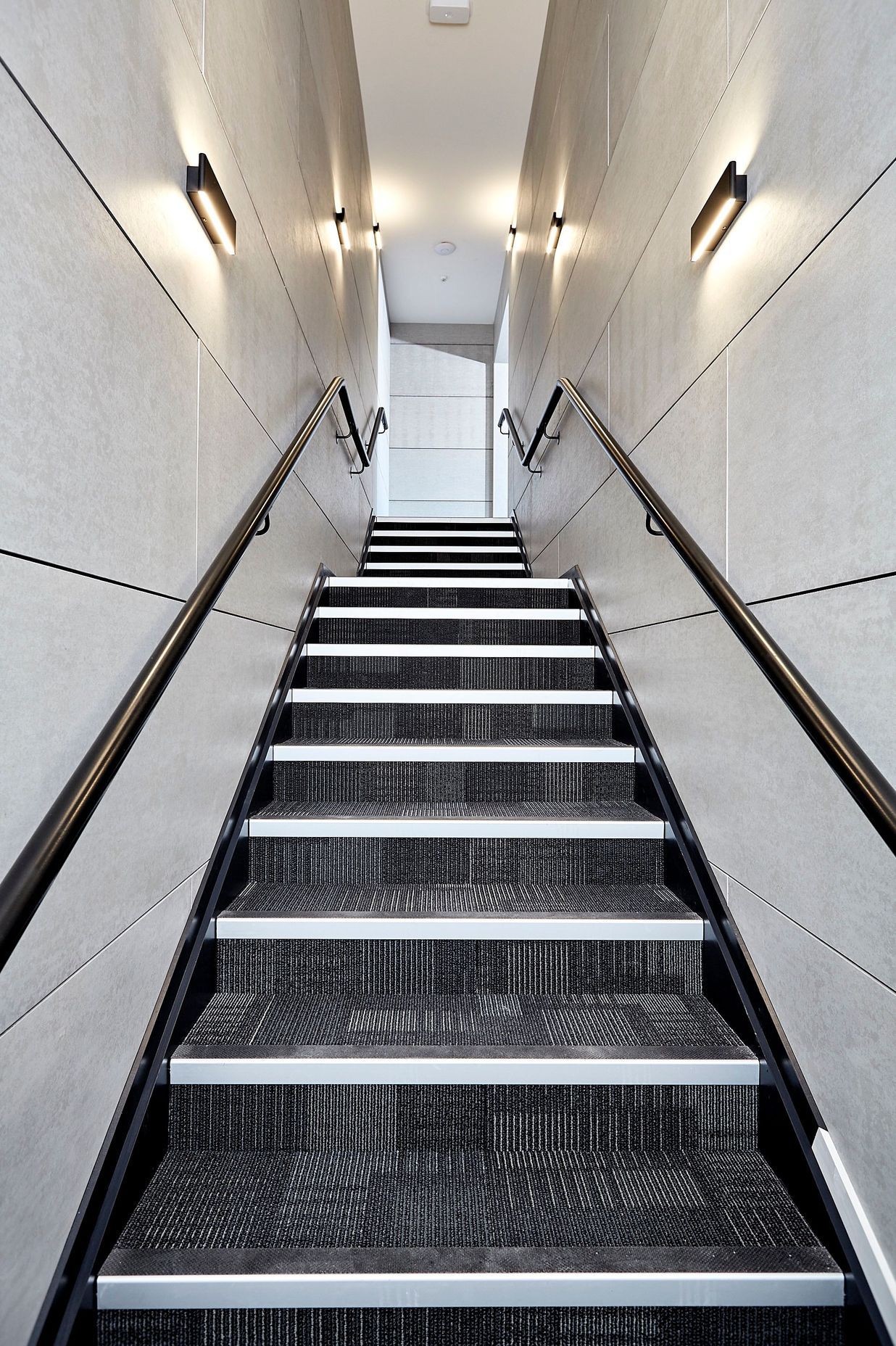
AP: I understand you have a few different offerings – can you take me through these and tell me the benefits of each?
AB: We offer high-grade urethane UV coatings for high wear and UV sunlight exposure. These are also used in very high moisture zones such as wet rooms, showers and industrial zones, which require regular hygiene requirements.
These can come in any colour and gloss level – from mirror finishes to matte surfaces with soft touch properties. Our coatings can be used for hygiene areas where regular wash downs are required, and contain antimicrobial additives that have been certified.
Also offered are low-cost solutions for OEM producers such as door manufacturers, cabinet makers and the pre-primed market on all major substrates.
We also produce decorative panels for the residential market, such as Plyplay. We're also involved in a new range of UV digital products that will be on the market later this year.
This technology has enabled Bates Surfaces to be VOC-free since 2015, reducing our production and energy footprint, and offering sustainable and environmentally friendly solutions for our customers.
Learn more about Bates Surfaces and its services.