Safer stone: the luxurious, safe surfaces for projects
Written by
26 November 2024
•
3 min read
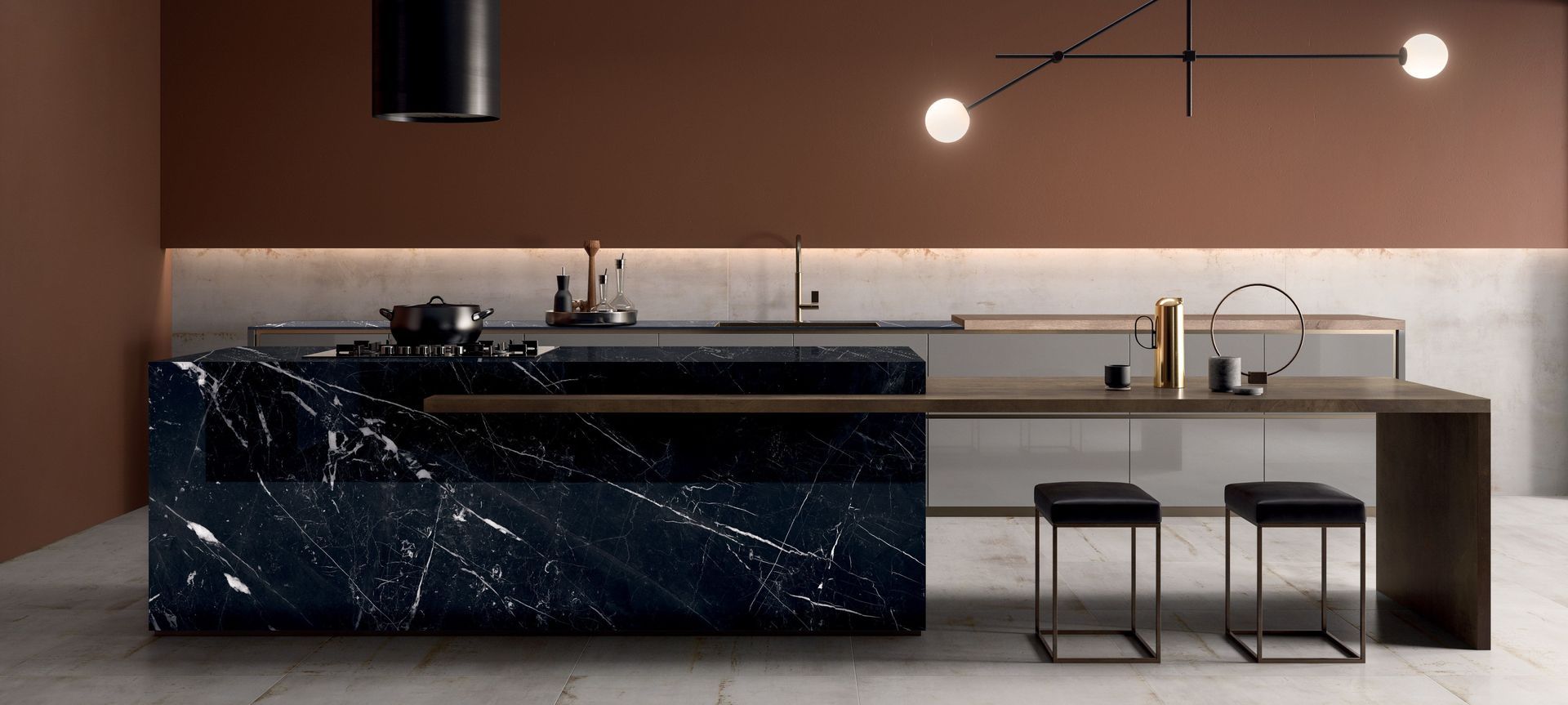
Although New Zealand hasn’t yet banned engineered stone with high levels of crystalline silica, it’s a safe presumption that the move might not be too far away.
Similar to our neighbours, it would mean a move away from many of the stones currently used in both residential and commercial projects, across a wide range of uses – from kitchen benchtops to bathroom vanities and fireplace surrounds.
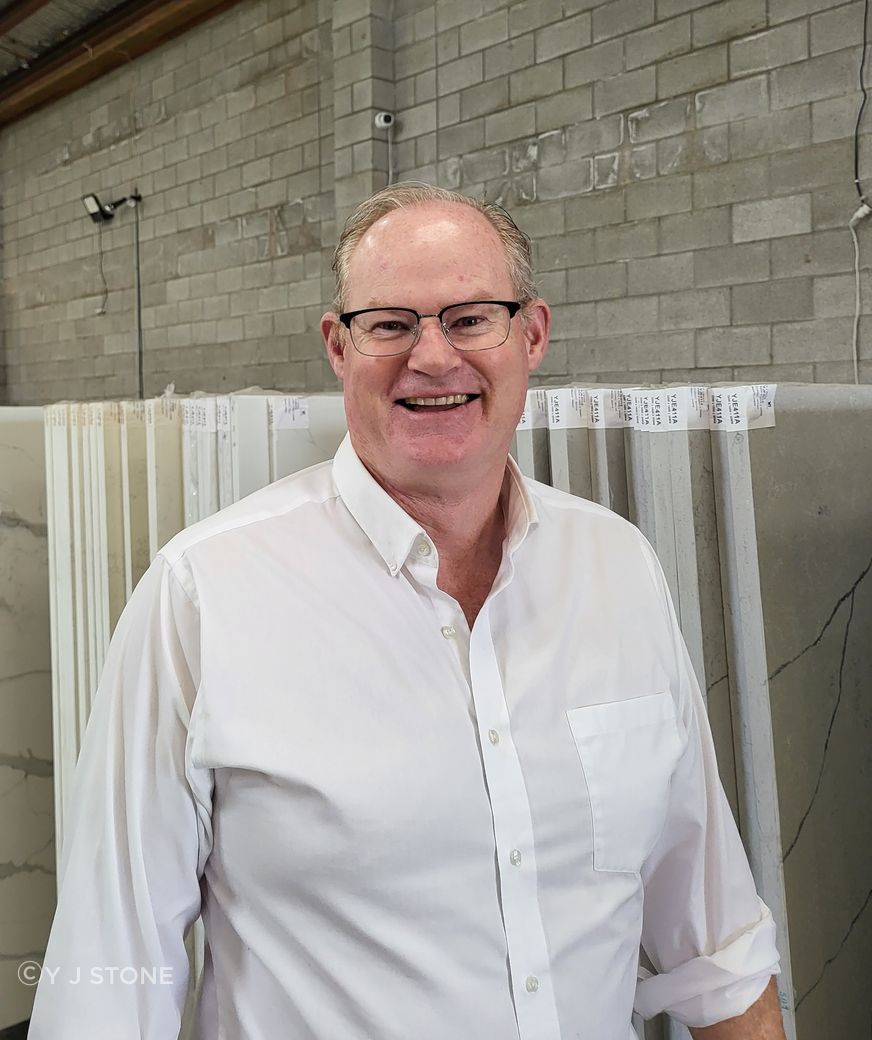
“Unlike Australia, there’s been no legislation change here. But from our perspective, looking forward to the health and safety benefits for fabricators and peace of mind for homeowners, we still wanted to make a change,” says Y J Stone’s Paul Nicholson. “We’ve decided that we want to go down the path of zero silica – more than just shifting to low silica.”
Y J Stone has experienced high interest in its zero-silica products. “What it means is eliminating the issue of crystalline silica in the fabricator’s workplace. Whereas, no matter if you have a low silica or high silica product, you’re still dealing with silica as an issue. So, we wanted to go down the pathway of where we’re completely eliminating the issue for our fabricators.”
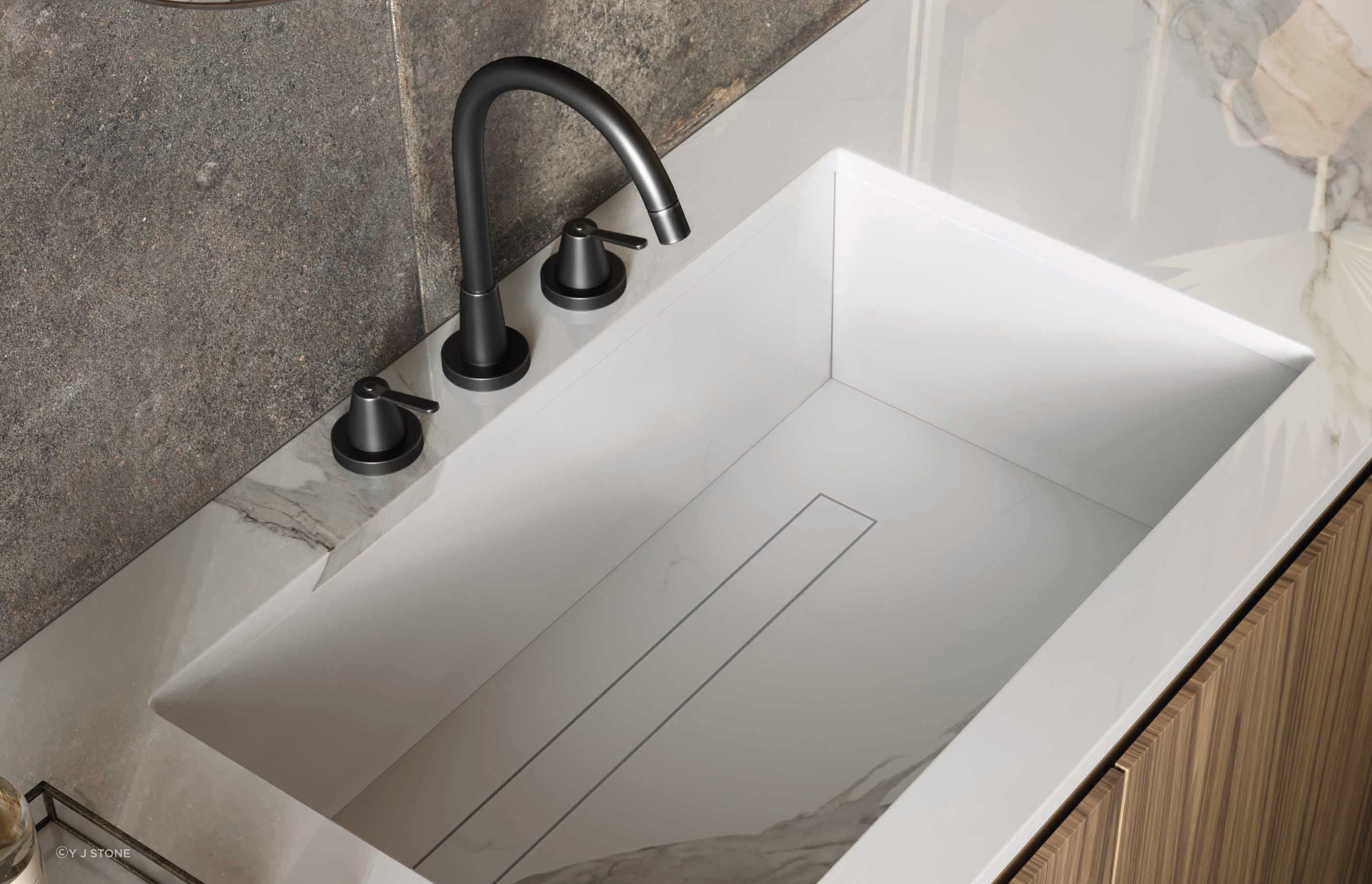
Luxurious Italian porcelain
Porcelain slabs by MATERIA, part of ABK Group, can be used indoors and out – think cladding, floor tiling, kitchen benchtops and even around swimming pools.
The composition of the stone is what gives it this durability and versatility. Made from a mixture of inert materials selected for their purity and fusibility, MATERIA slabs are made with a processing technology that accelerates the process of particle transformation. The raw materials are compacted to a high density before being fired in excess of 1200ºC to complete the sintering process. This results in the extreme durability of the slabs – they’re waterproof, non-porous and highly hygienic.
“Porcelain is a very safe material. It’s a very hygienic product to use, which is particularly important in kitchens and bathrooms. This is because it’s non-porous and you don’t need to worry about bacteria and germs getting into the surface,” says Paul.
Y J Stone stocks 12mm and 20mm porcelain slabs in a range of beautiful colours, with more colours and sizes available to order from the manufacturer in Italy. For large projects, the lead time is around 12 weeks.
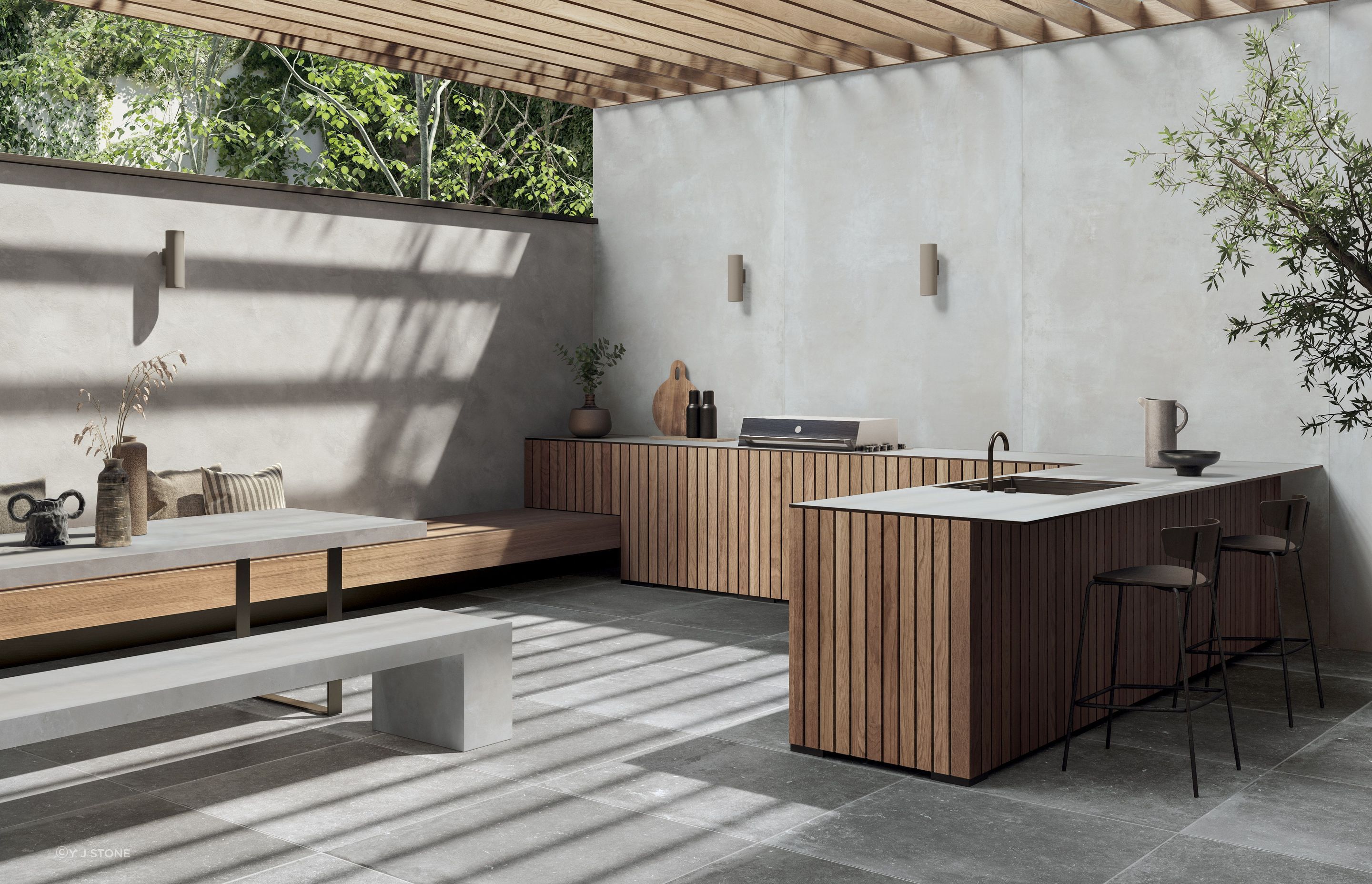
Crystalline silica-free engineered stone
Much the same in look and feel as traditional engineered stone, the raw materials used to produce zero silica stone means the product is safer to manufacture and reduces the risks associated with crystalline silica including silicosis.
“There are plenty of colour options for clients to choose from,” says Paul. “With our zero silica, some of the darker colours like the blacks and those with very heavy veining, like Calacatta, are still being developed because of the new raw materials that are required, but on the whole, everything else has very little difference.”
Technical data is available for architects, designers and developers to help decide which product is best for upcoming projects.
“Early contact is always good because then we can work with our suppliers in terms of obtaining any required colours for a specific project, although we do hold a range on hand here in New Zealand.”
The first container of Y J Stone’s zero silica-engineered stone slabs is arriving this month, with samples of the full slabs on display in the warehouse.
If you’d like to learn more about making the shift to a crystalline silica-free stone for your upcoming projects, get in touch with Y J Stone and explore more of their products on ArchiPro.