The 12-sided hilltop nest capturing Kapiti Coast’s panoramic views
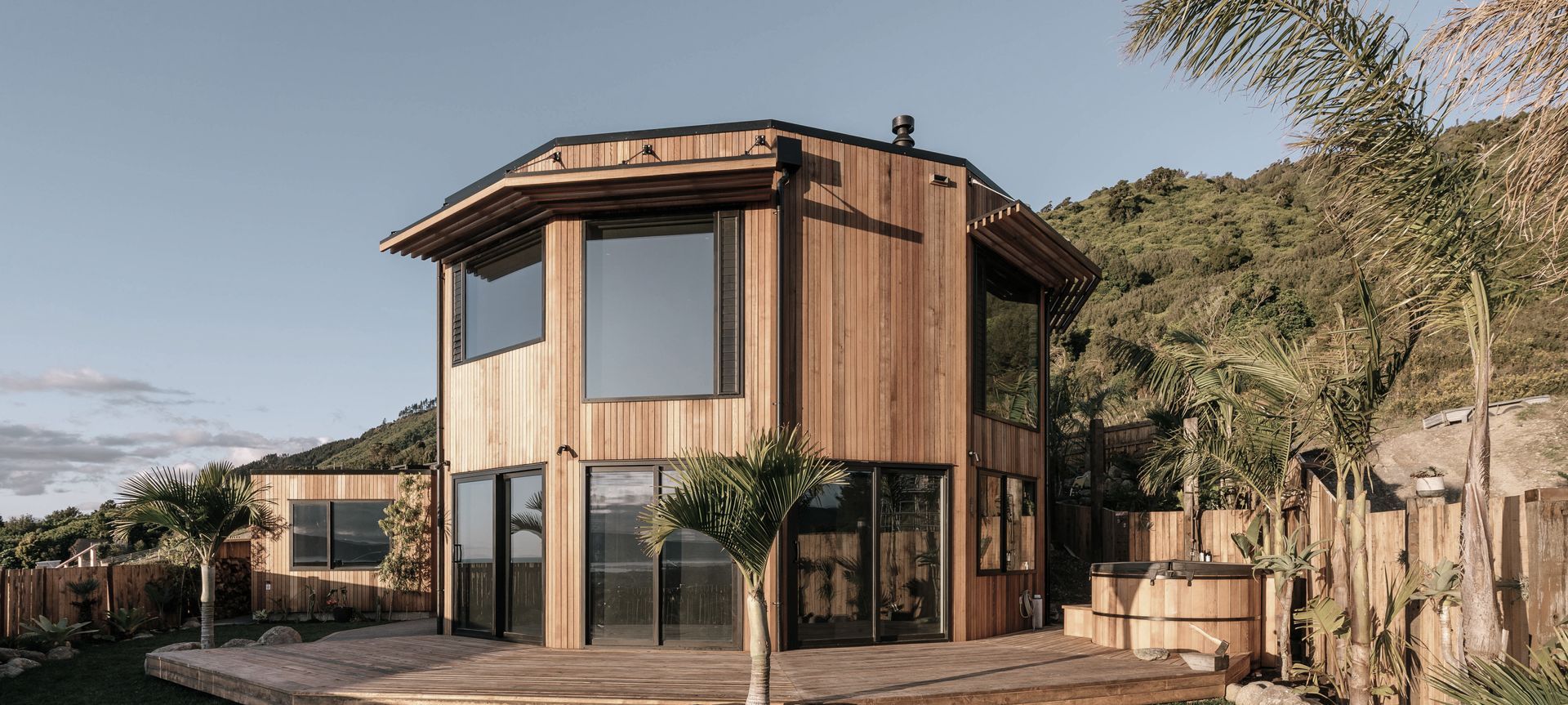
Situated in the heart of the Kapiti Coast District, Waikanae township captures sweeping views of New Zealand’s west coastline, stretching from Mt Taranaki down to the South Island. It’s rare for a rural town to have such expansive visibility of its broader surroundings, and Novare Architecture’s Gary Phillips recognised this unique quality in his design of Round House.
“It's a beautiful site. When you're there, the views feel similar to what you’d experience from a helicopter,” says Gary. “So my ambition became to capture that feeling of the location.”
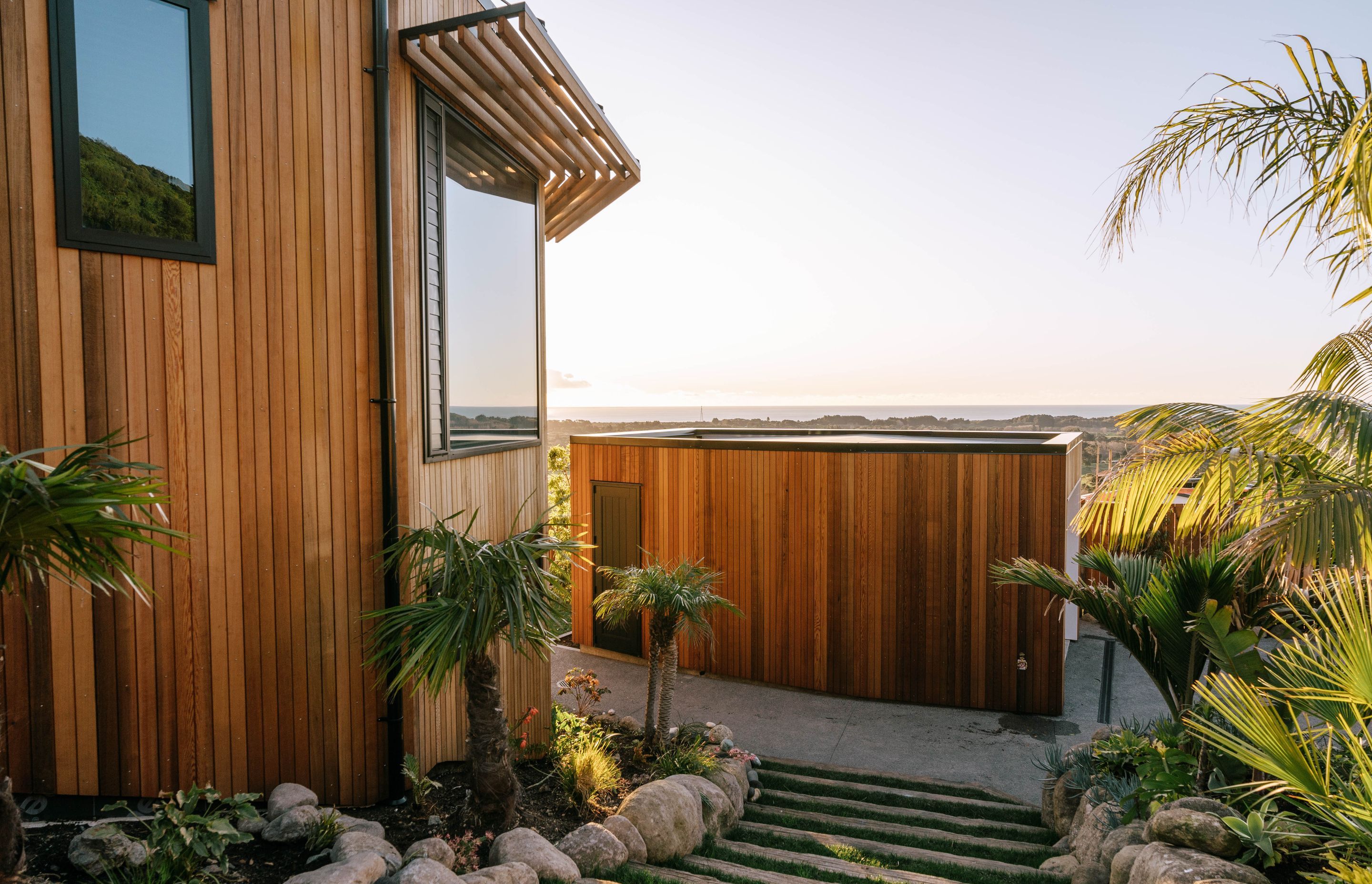
Since the 1970s, Gary has dedicated himself to the art of sustainable building, and for this project, sustainability was a key concern. However, the brief also requested an unusual structural form: a round, two-storey house.
“I’d previously designed an eco-transportable home for James Davis, the same client, on a different site in Waikanae. But I've also designed a number of hexagonal homes in years gone by, so James knew I had experience with the round building form,” Gary adds.
Round House was designed with 12 sides, each providing at least one window to the outdoors. From the outside, it can be difficult for people to understand how the interior works and where furniture would fit. But once you’re inside, everything makes sense. “There's a lot of organic synergy in round homes; they just feel good,” shares Gary. “Most of the world is wedded to the right angle, but James was not. He wanted something totally different.”
Clad almost entirely in western red cedar, Round House is distinctly homely. Its material palette is kept simple, using mostly vertical cedar cladding and black aluminium joinery, which also extends to the detached garage and front gate.
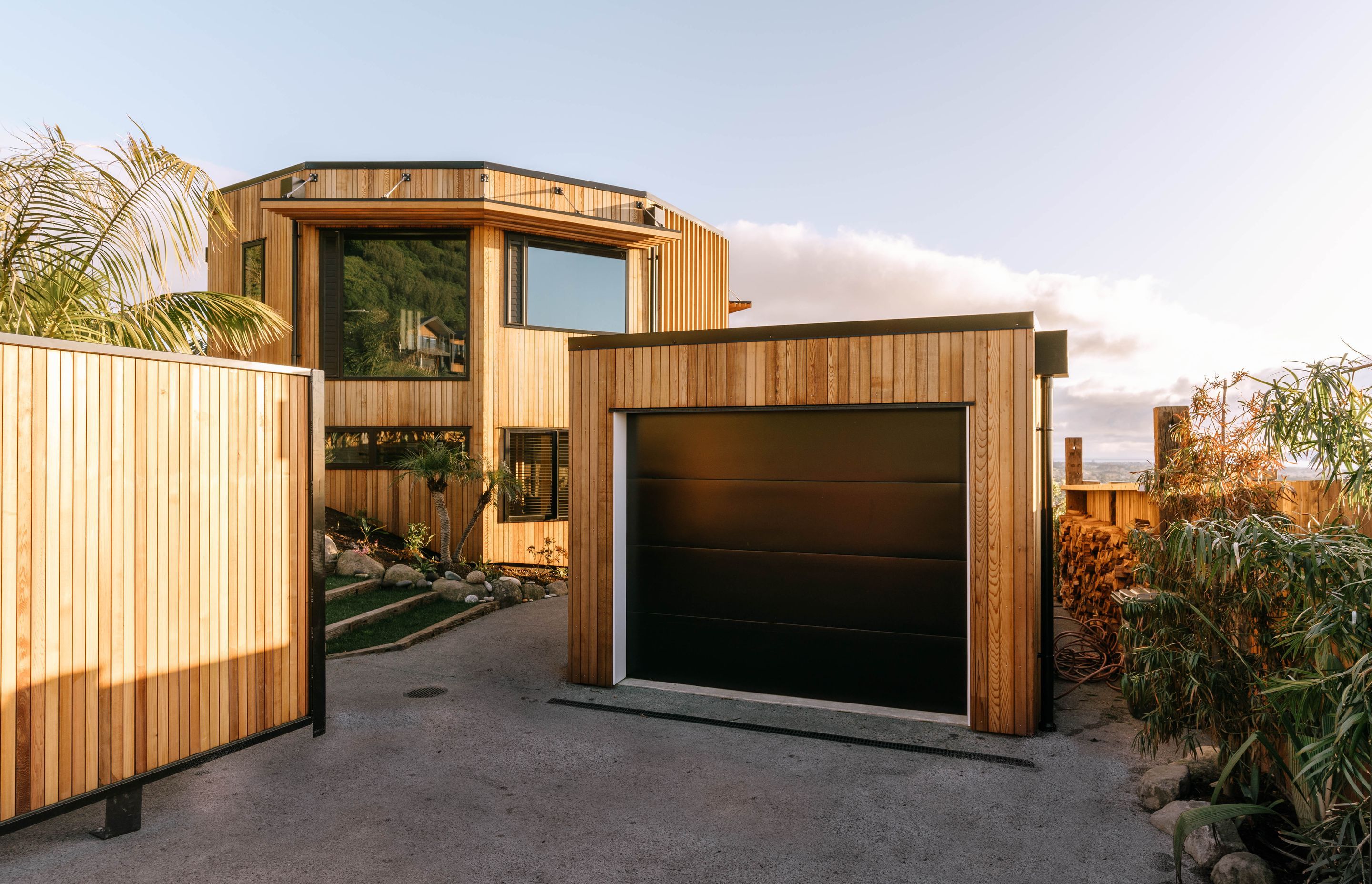

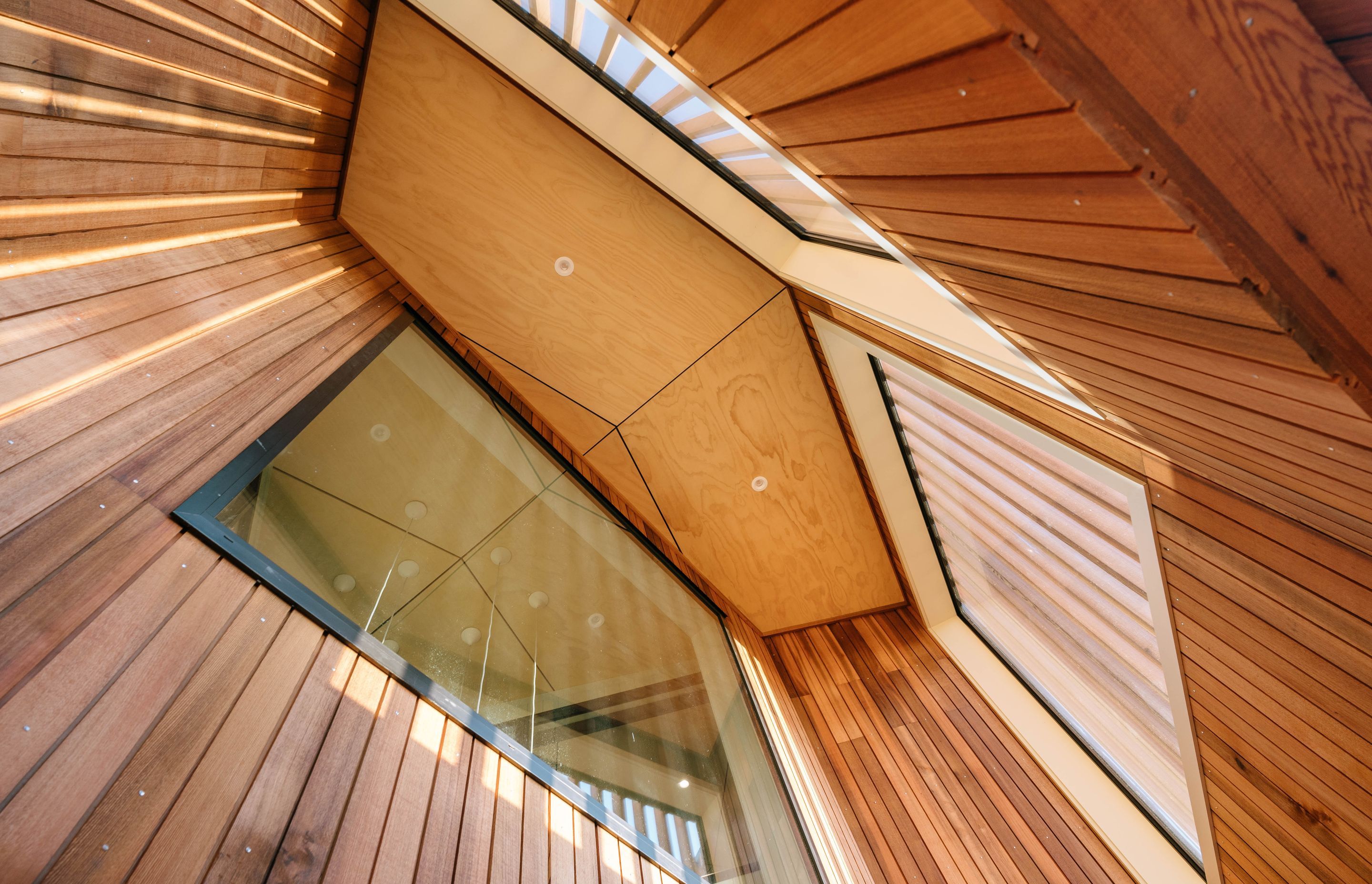
The entry porch is recessed, set back into the home and sheltered by a beautiful double-height ceiling featuring birch plywood with negative detailing. In the same passage, an internal window situated on the second storey looks out to two exterior windows positioned at equal height.
From the outside, these windows are enclosed by vertical cedar rain screens that run the height of the top floor — a subtle yet striking design element. And as you move indoors, the surrounding landscape reappears, framed by the home’s windows and large sliding doors.
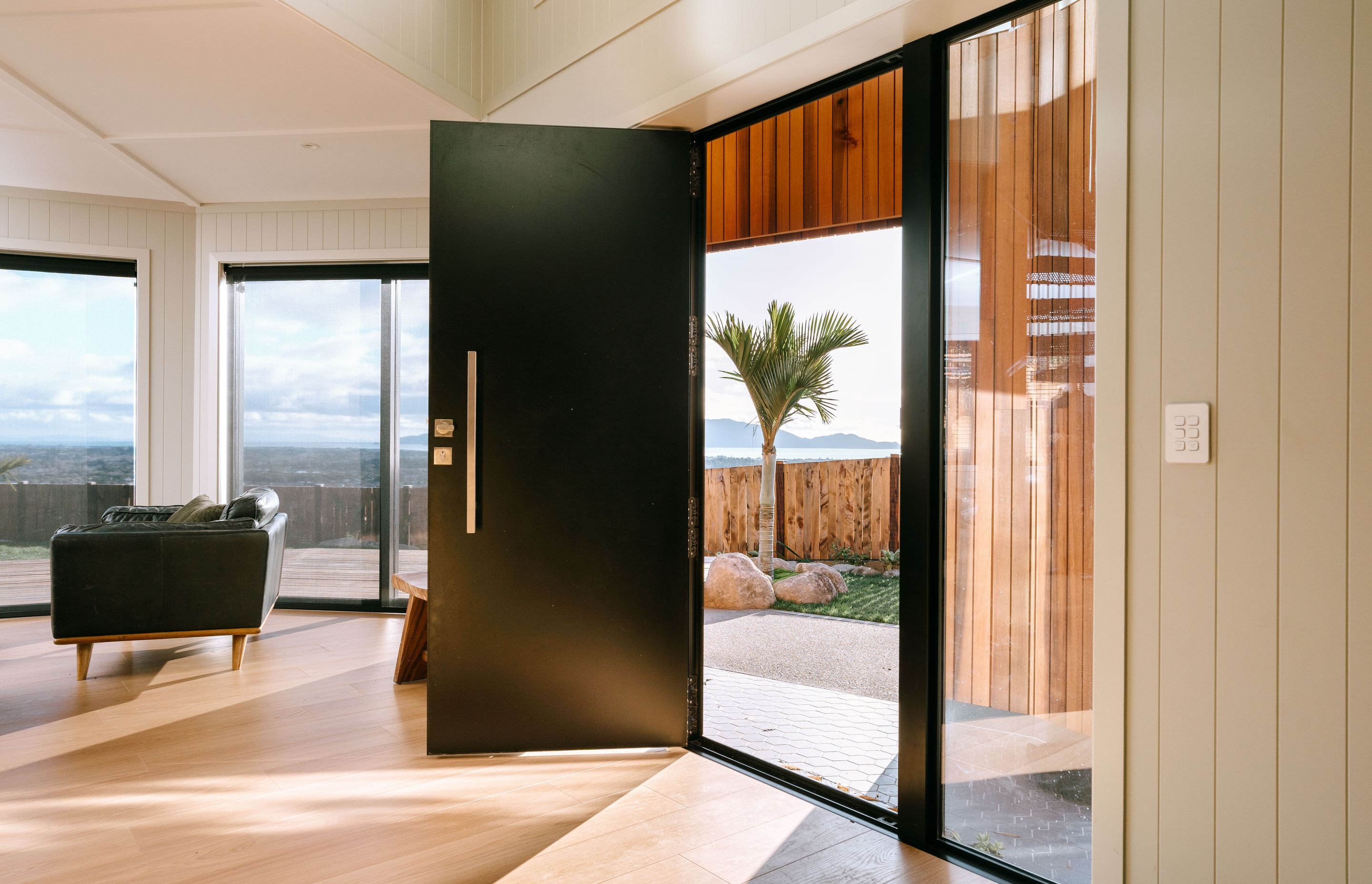
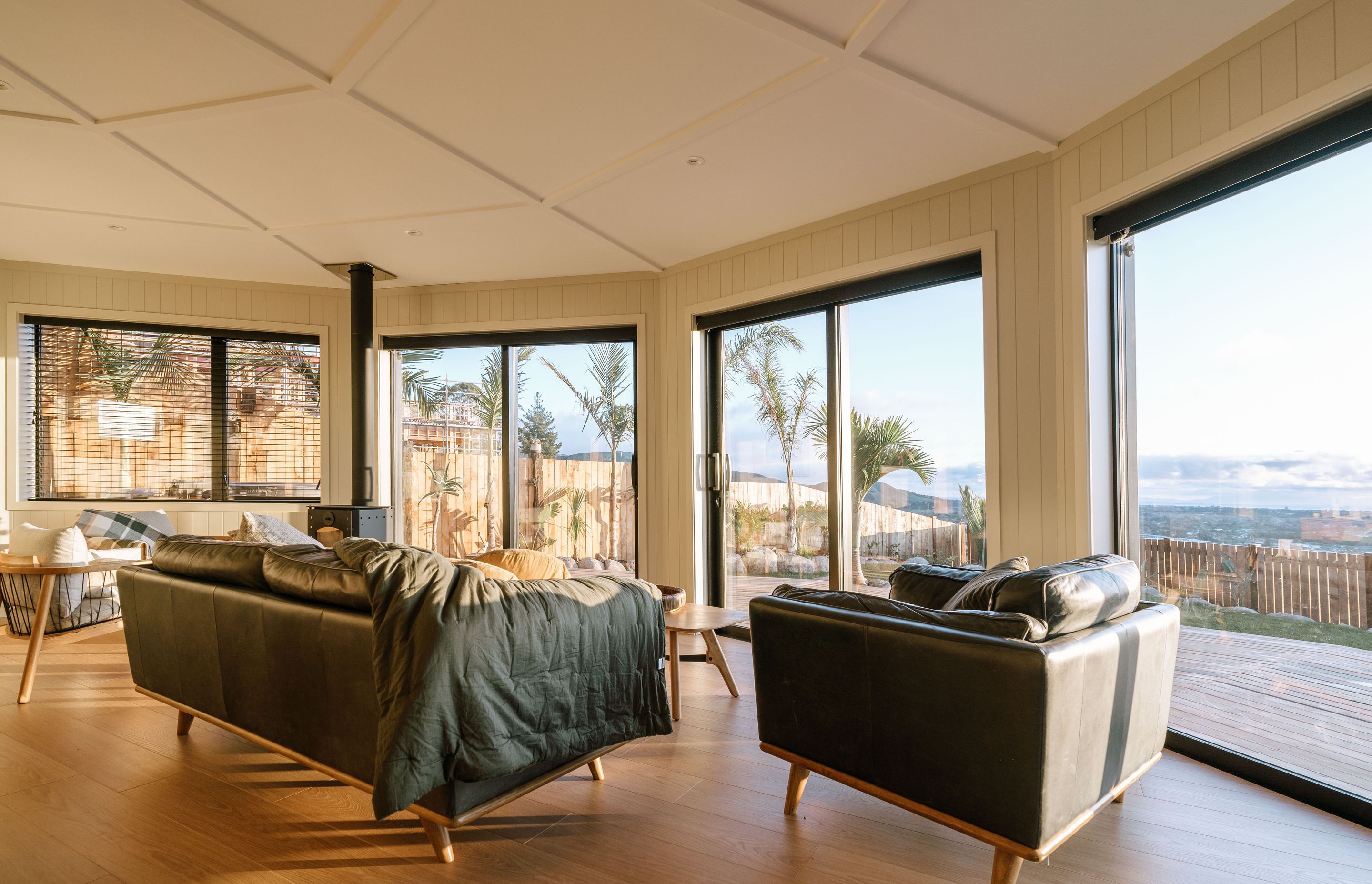
Each window has been carefully designed to take in a specific view,” shares Gary. “For instance, there’s one facing Kapiti Island, one looking north, and one turning to the hill behind the house, which is often shrouded in mist and really quite magical.
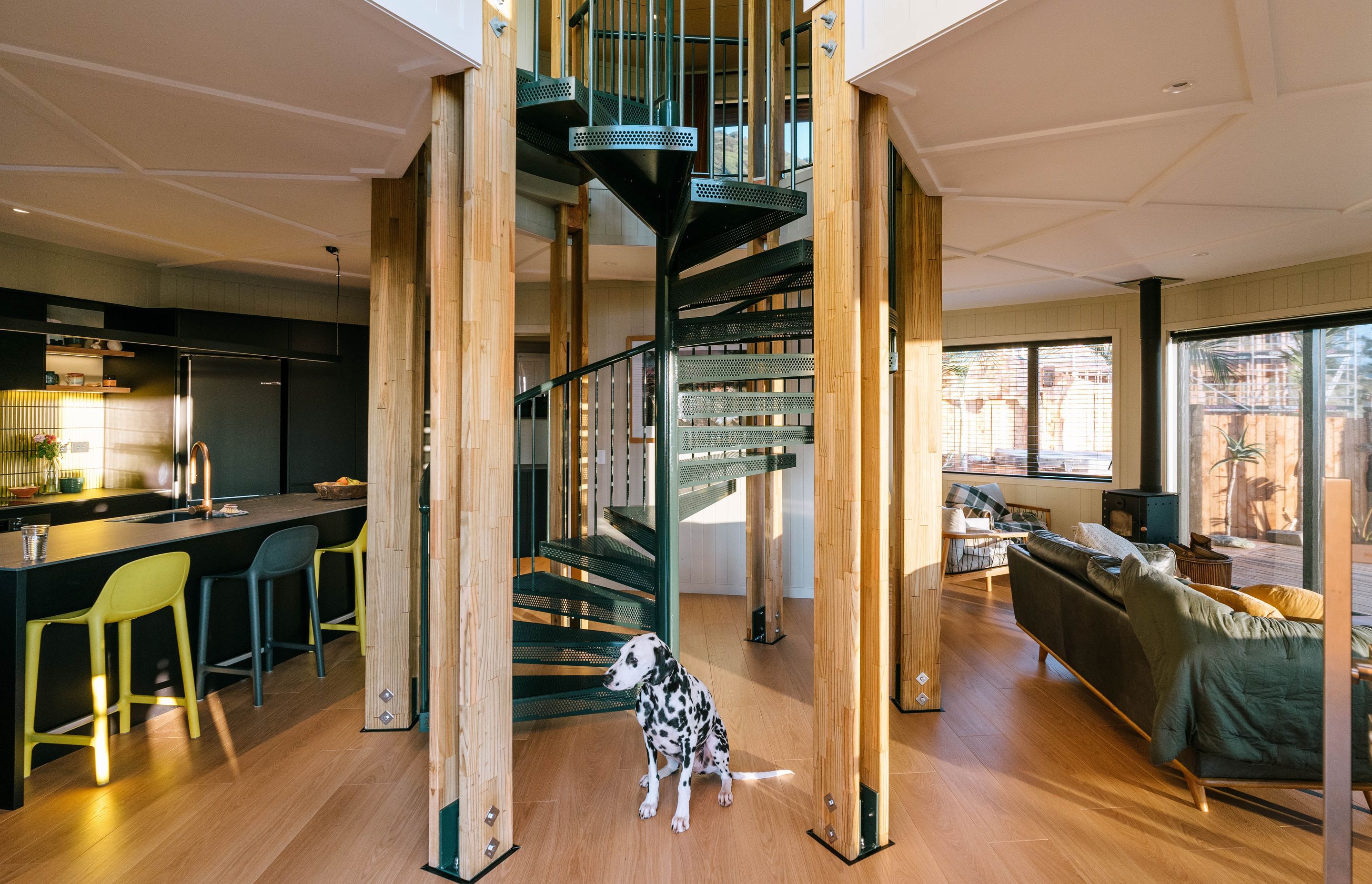
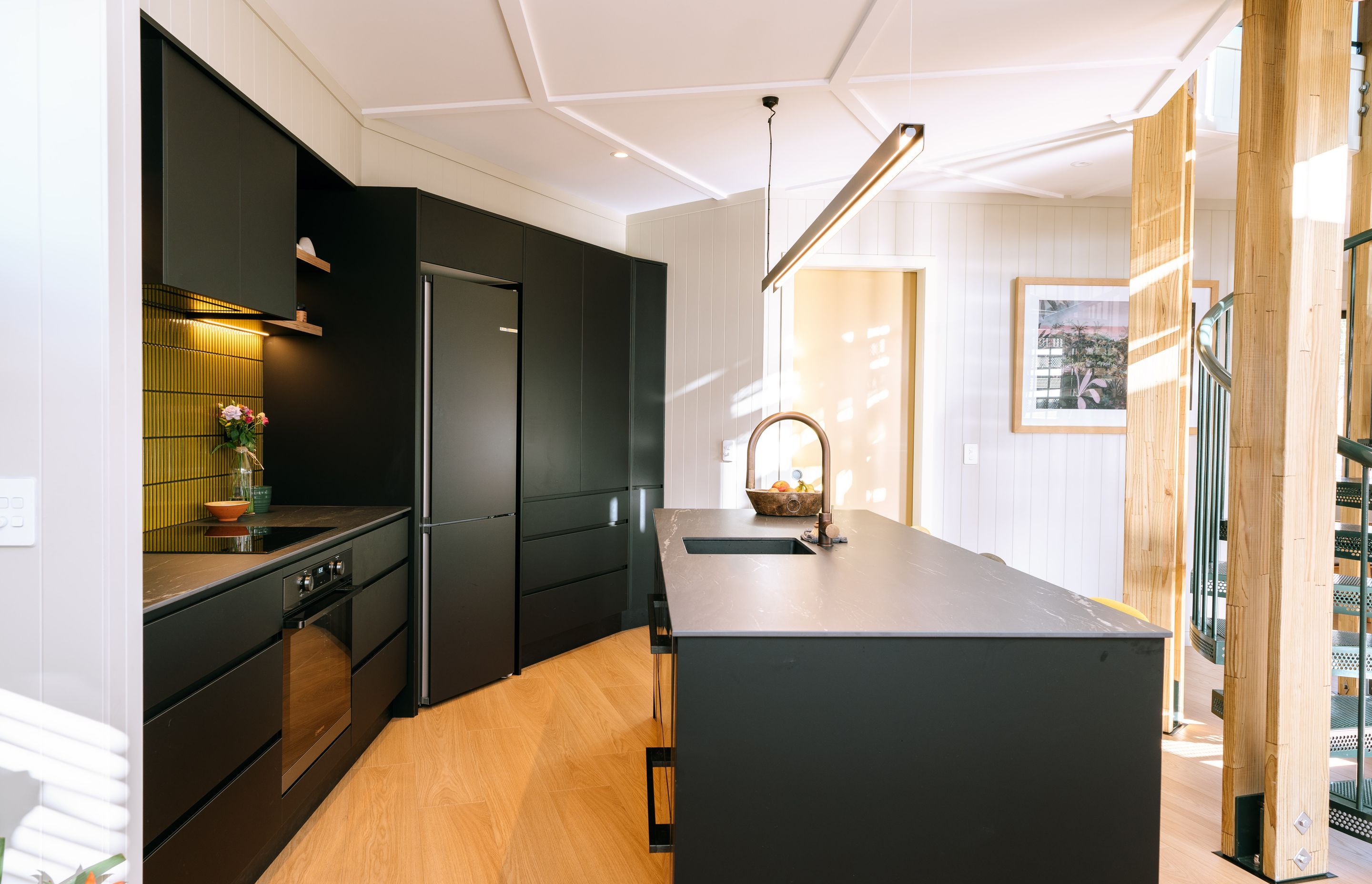
The ground floor houses an open-plan kitchen, dining area, and lounge, with a separate laundry and connecting bathroom hidden behind a cavity door.
From the main living area, sliding doors open to the spacious deck, which elegantly articulates the home’s form; and just around the corner, you’ll find the outdoor shower and cedar-clad hot tub.
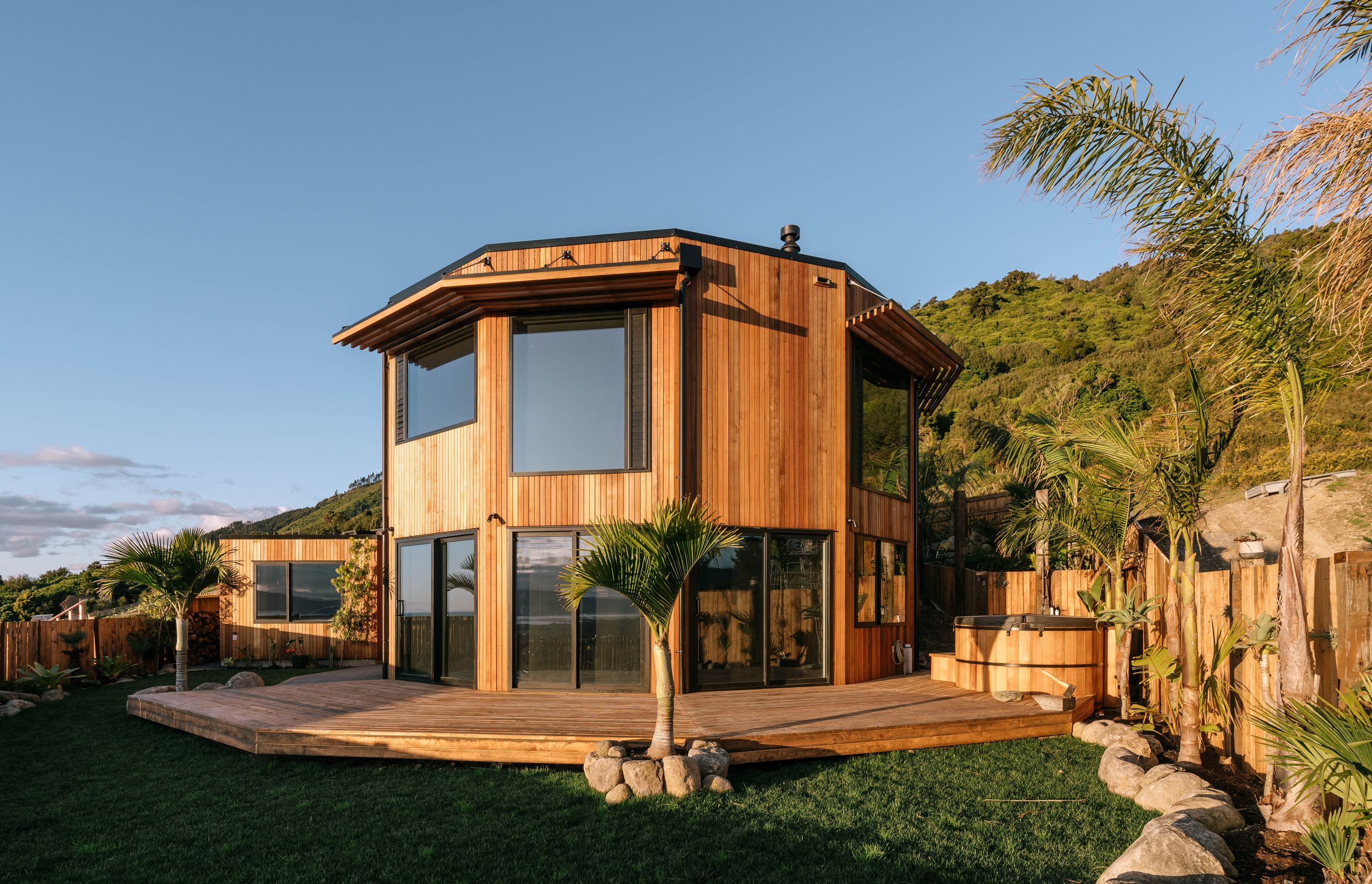
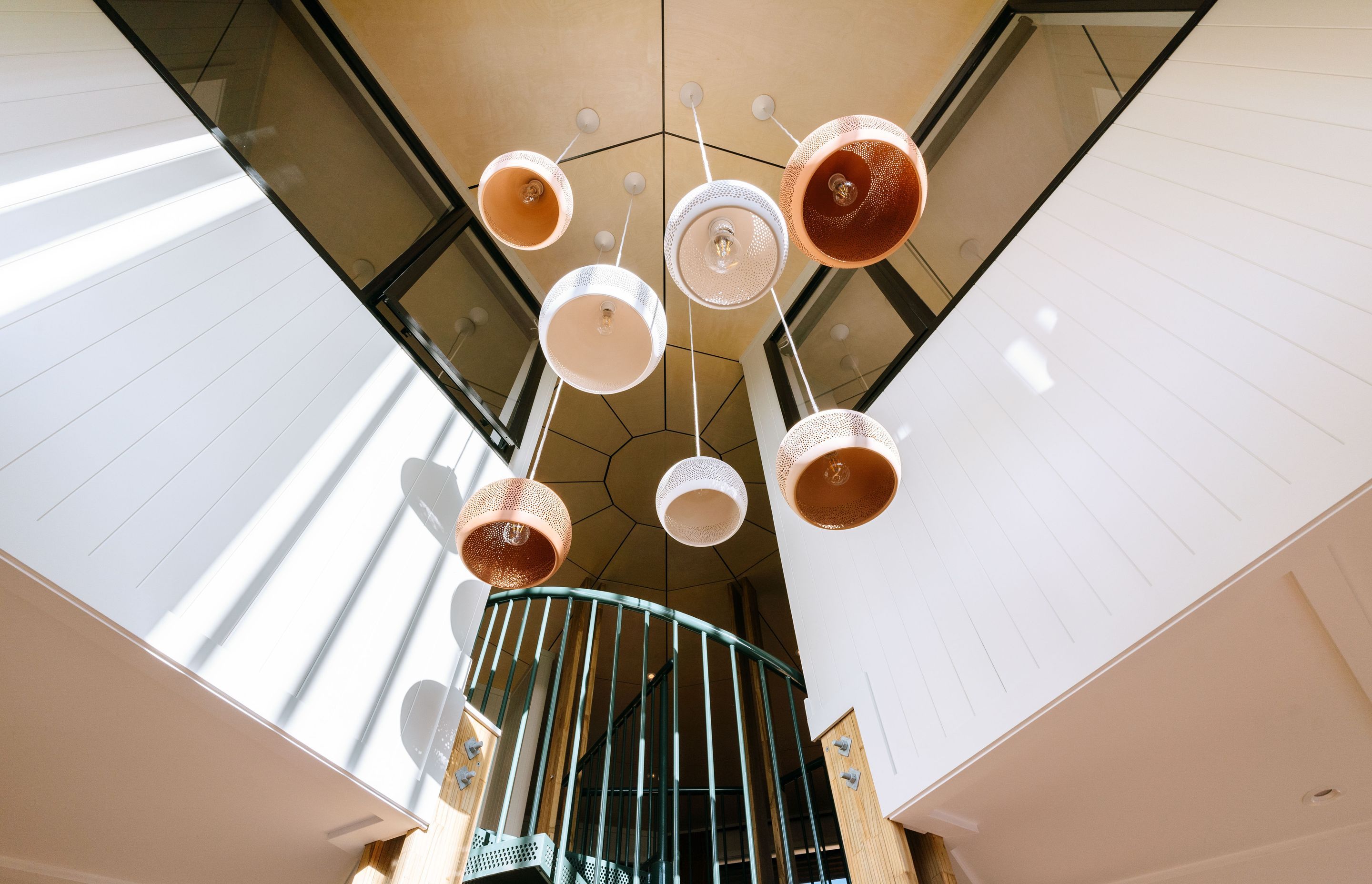
Inside, the perforated spiral staircase marks the lynchpin of the house, and, as you move up the stairs, the birch plywood ceiling becomes noticeable again, featuring hexagonal negative detailing.
On the landing, a generous lounge provides both a place to rest and a passage to the main bedroom. Meanwhile, the second bedroom and main bathroom live to the left of the staircase.
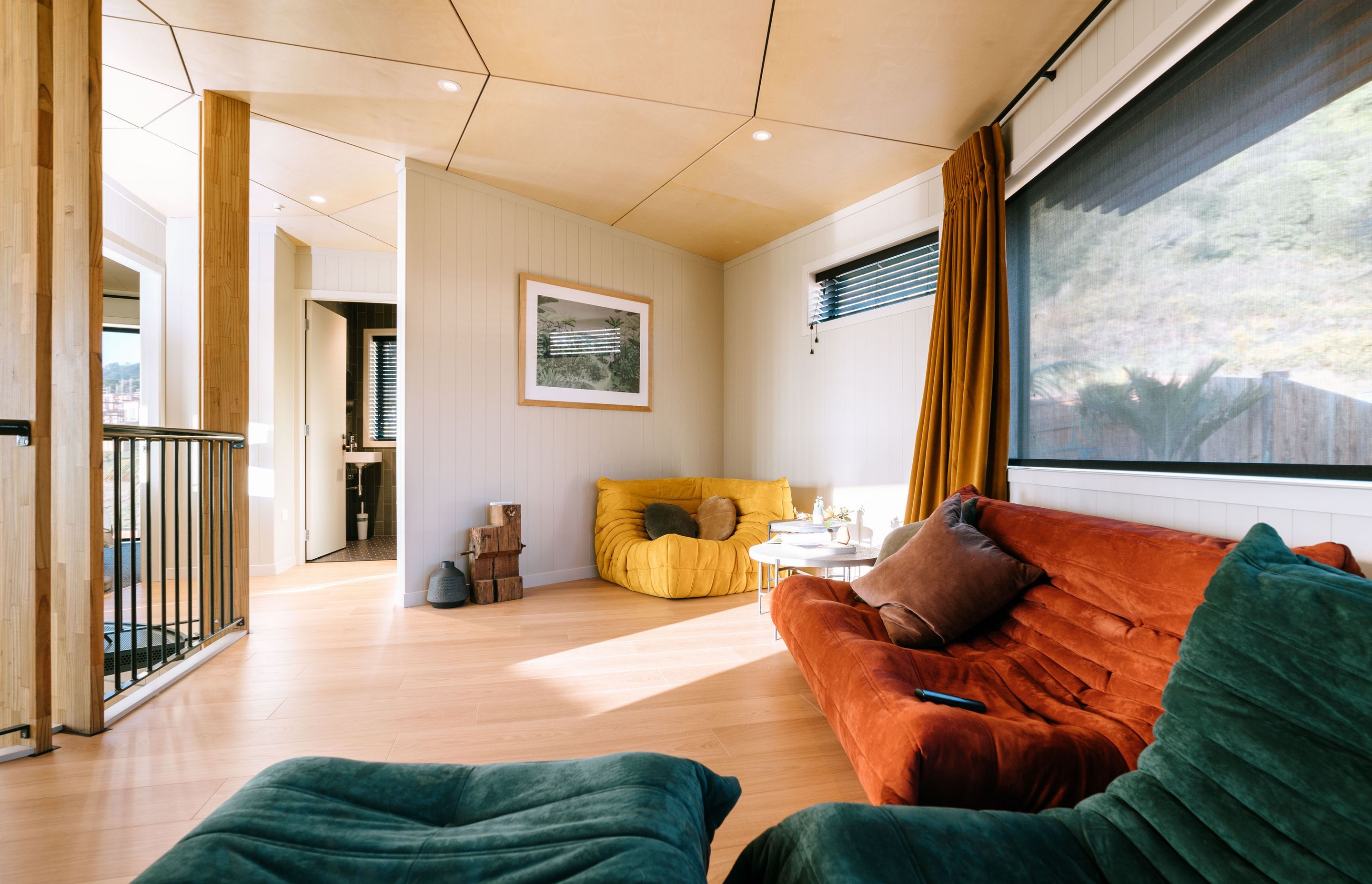
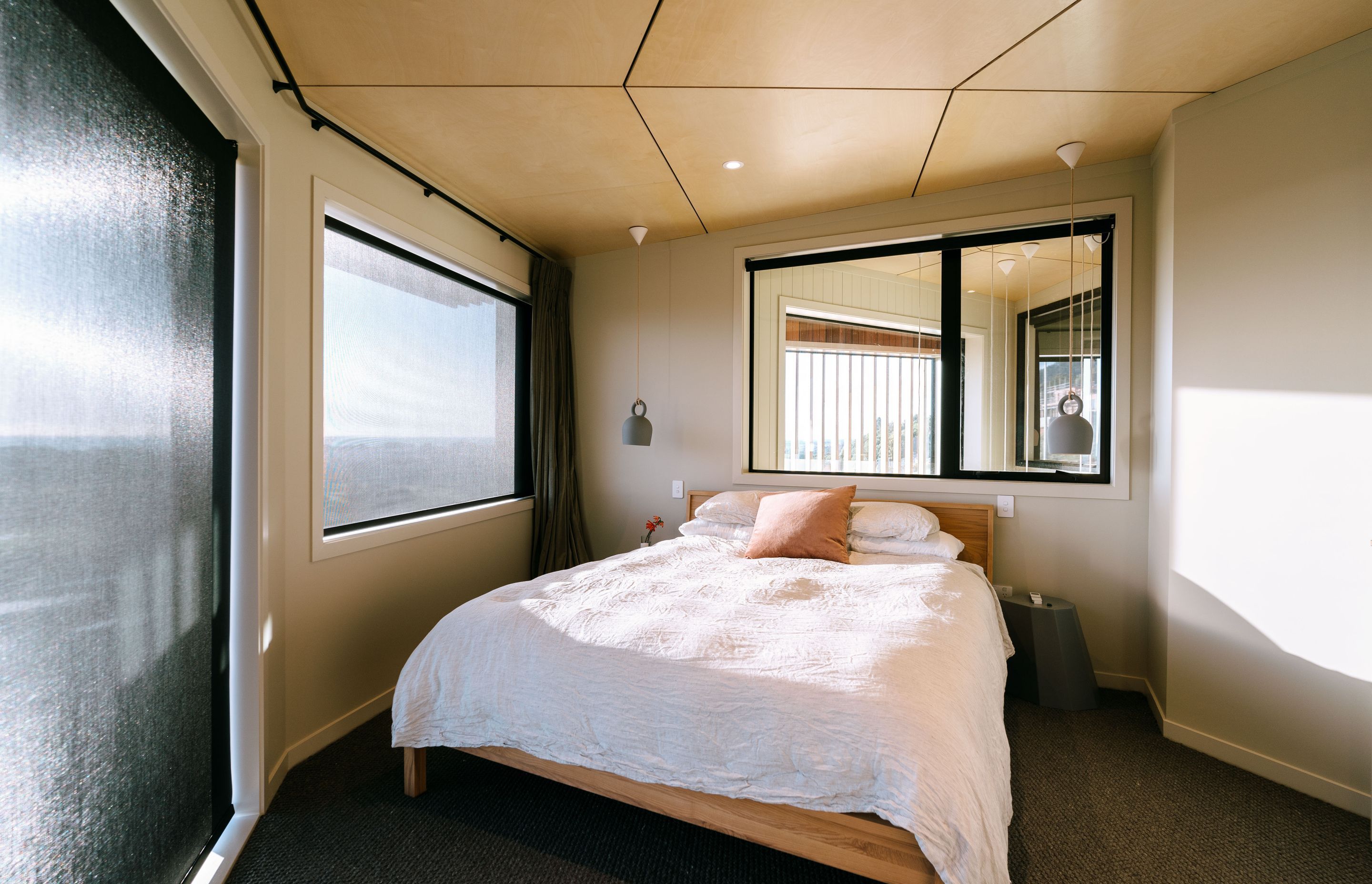
When looking at sustainability, one of the best decisions made was to use wider structural framing. “This allowed us to install thicker insulation,” says Gary. “We then filled the walls with mammoth insulation, which is a sustainable material made out of recycled plastic drink bottles.” More often than not, it is these ‘hidden’ design choices that have the biggest impact of all on a home’s energy efficiency.
Duane Cameron from Cameron Builders led the property’s construction and worked closely with the project’s engineer Hayden Milburn. They utilised Frank House’s prefab manufacturing services to build the majority of the structural elements, all of which were craned in over two days and weathertight within a week.
“Kiwis are still coming to terms with prefab building,” shares Duane. “They don’t understand the level of skill required and just how many advantages the method provides. We work with a system called hsbcad. It’s a BIM tool, and it allows us to translate architectural plans into a 3D model that’s accurate within a millimetre. That's where the time and energy goes with off-site work.”
By utilising prefab manufacturing, not only can more precise measurements be achieved, but it also reduces labour costs, material wastage, and the project’s timeline.
“Off-site construction is definitely the way to go,” Gary adds. “At the moment, I’m trying to figure out how much of each design can be prefabricated off-site and then brought in. And although Round House was not intended to be an example of the way forward, it has in many ways become just that.”
Explore more projects by Novare Architecture.