The durability of cladding: the best claddings to suit the New Zealand climate
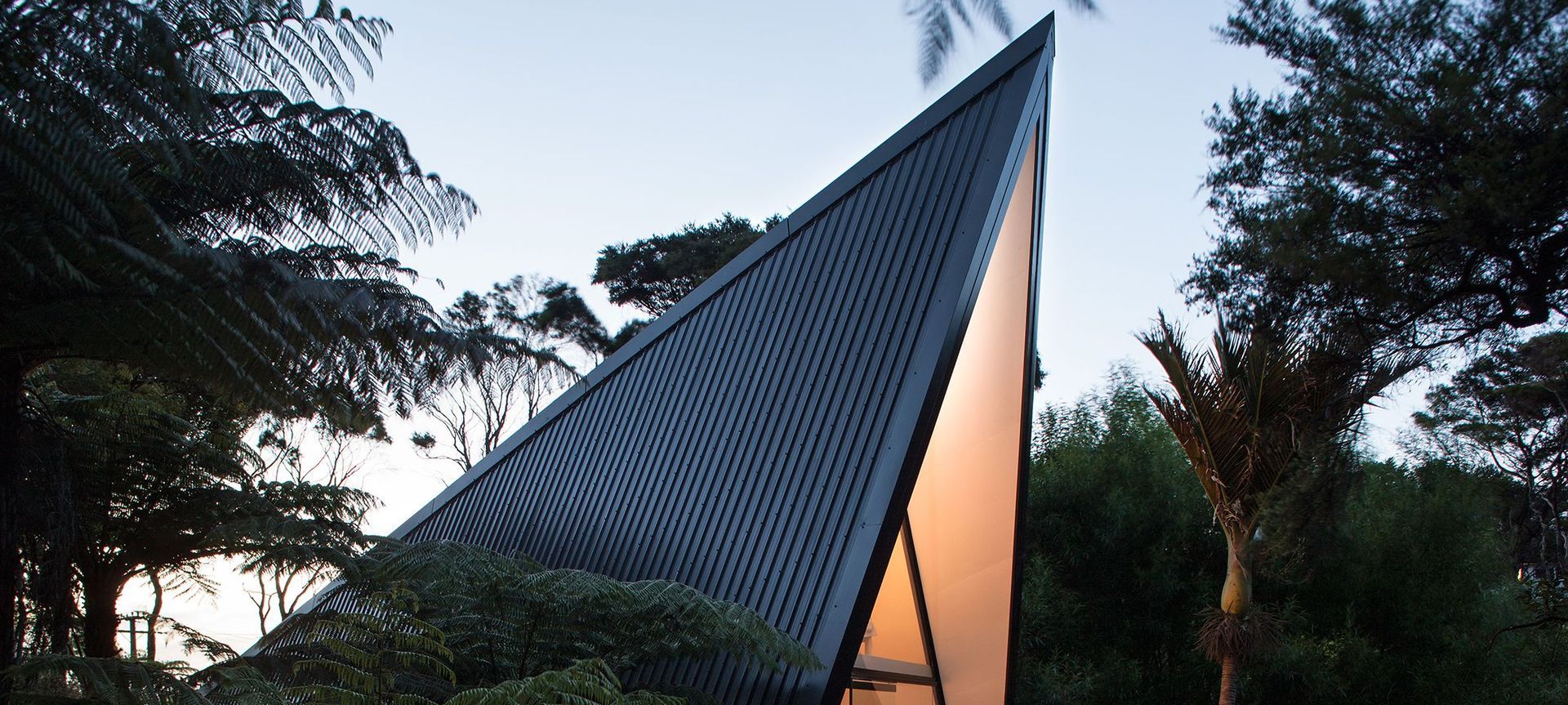
It is well known that using the wrong cladding materials in the wrong environment can have devastating consequences. Just think about products like asbestos – now proven to be a human carcinogen – that was used as cladding from the 1950s to the 1980s. Then, there was the ‘leaky homes crisis’ that occurred between the late 1980s and mid-2000s, when plaster-style monolithic cladding systems allowed moisture in between the cladding and the timber structure with no means of escape, causing billions of dollars of repairs and replacement to an estimated 42,000 homes around the country, not to mention the health implications.*
It, therefore, comes as no surprise that, today, most architects, designers and builders have become a lot more risk adverse when it comes to specifying cladding systems.
"It’s hugely important to get the cladding right because if you get it wrong, the implications for the homeowner and for the industry are huge and we don’t want to take those risks," explains Chris Tate. "These days we use tried-and-tested claddings and ask, ‘how long has the cladding been around?’ If it’s just come into the market, then, personally, I won’t touch it. While I wasn’t working in architecture pre-2000, my generation understood the lessons and I’m very cautious about trying out new claddings – they need to have a track record."
Naturally, some claddings perform better than others in terms of watertightness and longevity. "It’s crucial to think about the suitability of a cladding to the climate," Chris says. "Putting cheap cladding up quickly onto a timber frame is about the worst thing you can do in the New Zealand climate where we have a lot of humidity and rain. It may be okay in California where it doesn’t rain – but not here."
In New Zealand, claddings have a 10-year implied warranty according to the Building Act. “Claddings need to last for 10 years but we really want our claddings to last for at least 20 to 30 years, because that’s our liability period and since buildings are designed to last for a minimum of 50 years, so we want the cladding to last as long as possible. The same goes with roofs.”
The compatibility of the roofing, flashings and fixings are crucial too, and these should be designed together to last for the same period. “It’s a real science to make a whole cladding system that works well,” says Chris. “For example, you don’t want a roofing material to leach onto the cladding product as that can be devastating, so we really do rely on our suppliers to help us to understand how the whole system works together.”
Chris suggests that it’s worth spending money on good-quality cladding systems that is proven to suit the New Zealand environment. “In my own practice, we repeatedly use certain claddings,” he states. “We don’t just look at its aesthetic and ease of construction, we look at how easy it is to maintain, particularly if a house near the ocean and the cladding needs to deal with salty sea spray, sand and wind.”
“There are some key claddings we regularly use, such as pre-cast concrete panels, which provide structure and cladding as an all-in-one system. We also use plastered brick or plastered block, which is a pretty bulletproof system. We really like bulletproof systems!” he says.
Chris also utilises various locally made metal claddings, such as pre-formed steel cladding. “We use a lot of Colorsteel, seen in our Tent House on Waiheke Island, because it is durable, cost-effective, and comes pre-finished with embedded colour,” he says. “It’s really designed for our environment, which is why you see so many houses clad in Colorsteel in New Zealand. It’s low maintenance so you only have to wash it down each year, and all the caps and flashings are made from the same material. The service the company provides is fantastic too.”
When using timber, Chris likes to use Accoya timber, which is a sustainable, eco-friendly high-performance wood that is specially treated using a special acetylization process to make it highly stable. It’s reputed to last for more than 50 years above ground. “Basically, it will outlast the building and can be finished with whatever paint or stain you like,” he says. “It is really beautiful and gets better with time – developing a really lovely patina after six or seven years.”
“Cedar cladding is also a popular choice and it’s great if you’re prepared to maintain it every year or two, although that’s a big ask of a lot of homeowners, especially if the house is more than a single storey because scaffolding alone can cost thousands of dollars to hire. We often use it in conjunction with sheet aluminium and Accoya, mostly as rain screening where it doesn’t do the job of waterproofing. We recommend using cedar on the lower storey where it’s easier to maintain.”
In fact, maintenance is the big thing when it comes to ensuring cladding remains durable. “We try to educate our clients to have a cladding maintenance plan,” explains Chris. “Maintaining a house is similar to maintaining a boat or a car; you wouldn’t buy a car worth hundreds of thousands of dollars and leave it for years before maintaining it, so why would you do that with your home, which is worth so much more?”
“For example, the Tent House is my family holiday home and, even though the Colorsteel cladding is very durable, I still clean it every year to keep salt and debris off the exterior of the house – and many people don’t realise that cobwebs retain moisture too. It is also good to maintain your aluminium joinery by keeping it clear of corrosive salt and abrasive sand.”
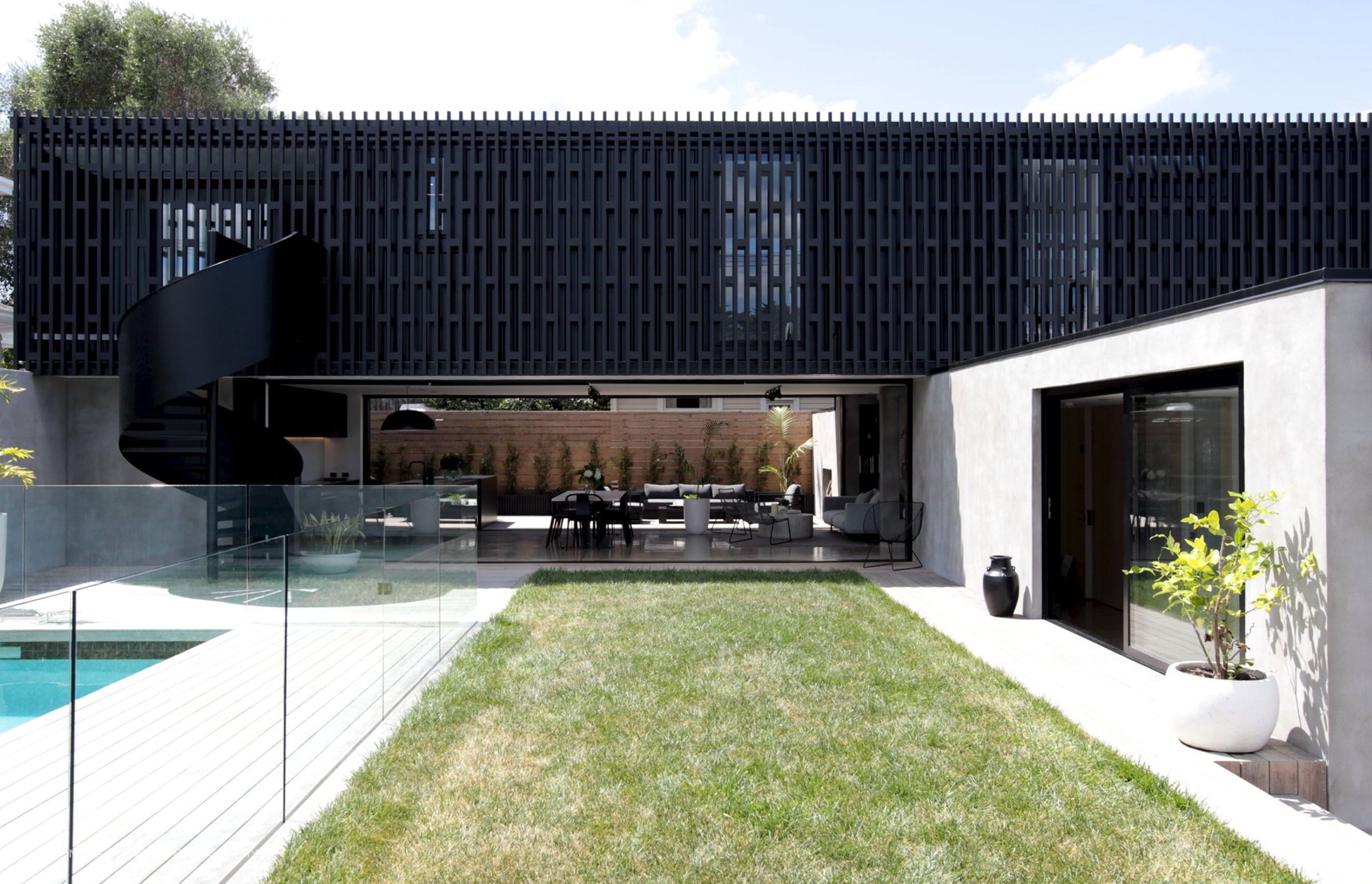
There are also ethical reasons for avoiding particular cladding products, suggests Chris. “There have been a number of products that have failed New Zealand homes over the years and we stay away from those for ethical reasons,” he says. “If I don’t believe in it, I won’t specify it because we have to think about the families that will have had to deal with the repercussions of a cladding that fails and take that into consideration with whatever we specify. We want claddings to be as bulletproof and maintenance-free as possible. You can double the life of your home just by maintaining the cladding properly.”
<sup>*Reference: The Building Act 2004 introduced a licensing scheme for building designers, builders and related trades. Under the Act, councils are required to be registered with a central authority and are subject to regular quality control procedure checks. </sup>