The future of polished concrete
Written by
22 August 2019
•
3 min read

There are five choices to make when specifying a honed or polished concrete floor, but it is the last that is the most important. We had a chat to PeterFell about how to achieve the best concrete floor outcome. The way most honed and polished concrete floors are finished with a sealant that sits on top of the concrete. This type of seal is economical but not as durable as the alternative. The alternative is a system unique to PeterFell, and one crafted with speciality products imported from Arizona, which together are known as the PeterFell C² Polished Concrete System.
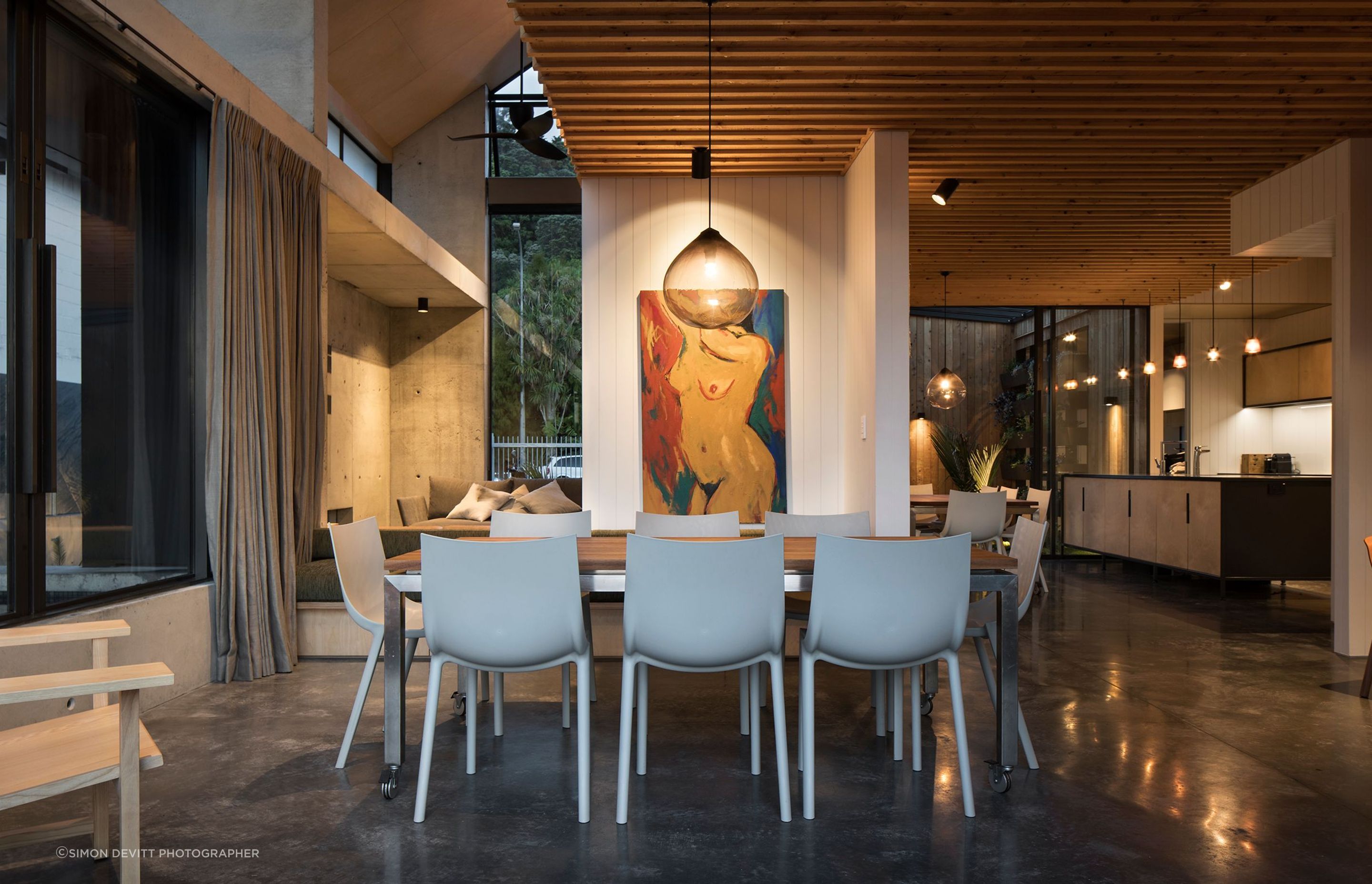
C² makes up one of five key choices that need to be made when specifying a honed or polished concrete floor. The first is the aggregate type, which will depend on what stones are available in the area. The second is colour. The final concrete colour is a result of the mix of stones and the colour chosen.
When aggregate and colour are finalised, the next choice is the level of stone exposure. The depth of the grinder determines the finished level of stone exposure. Following this is the polish, and finally the choice of sealant - either a standard seal coating or the PeterFell C² Polished Concrete system. “With the C² system, lithium silicate-based densifiers are used during the grinding and polishing process to harden and densify the floor,” PeterFell’s Michael Ross says. “The lithium silicate chemically reacts with the weakest component in the cement matrix, calcium hydroxide, to form calcium silica hydrate - what becomes one of the strongest components.”
This is the first part of the C² process, and is known as C² Hard. The second part is known as C² Seal; the stage that sets this system apart from most others.
“On completion of the polishing process, microfilm products are applied and burnished or melted. Burnishing is essentially the melting of the seal or microfilm, which provides for a shell-like layer. Most other systems do not melt in this way and so have microcracks and therefore lower durability and stain resistance,” Michael says.
“Using this system means the seal is effectively melted into the concrete itself rather than sitting on the surface as other products do. It is less film-forming and leads to a much more stable, durable finish.”
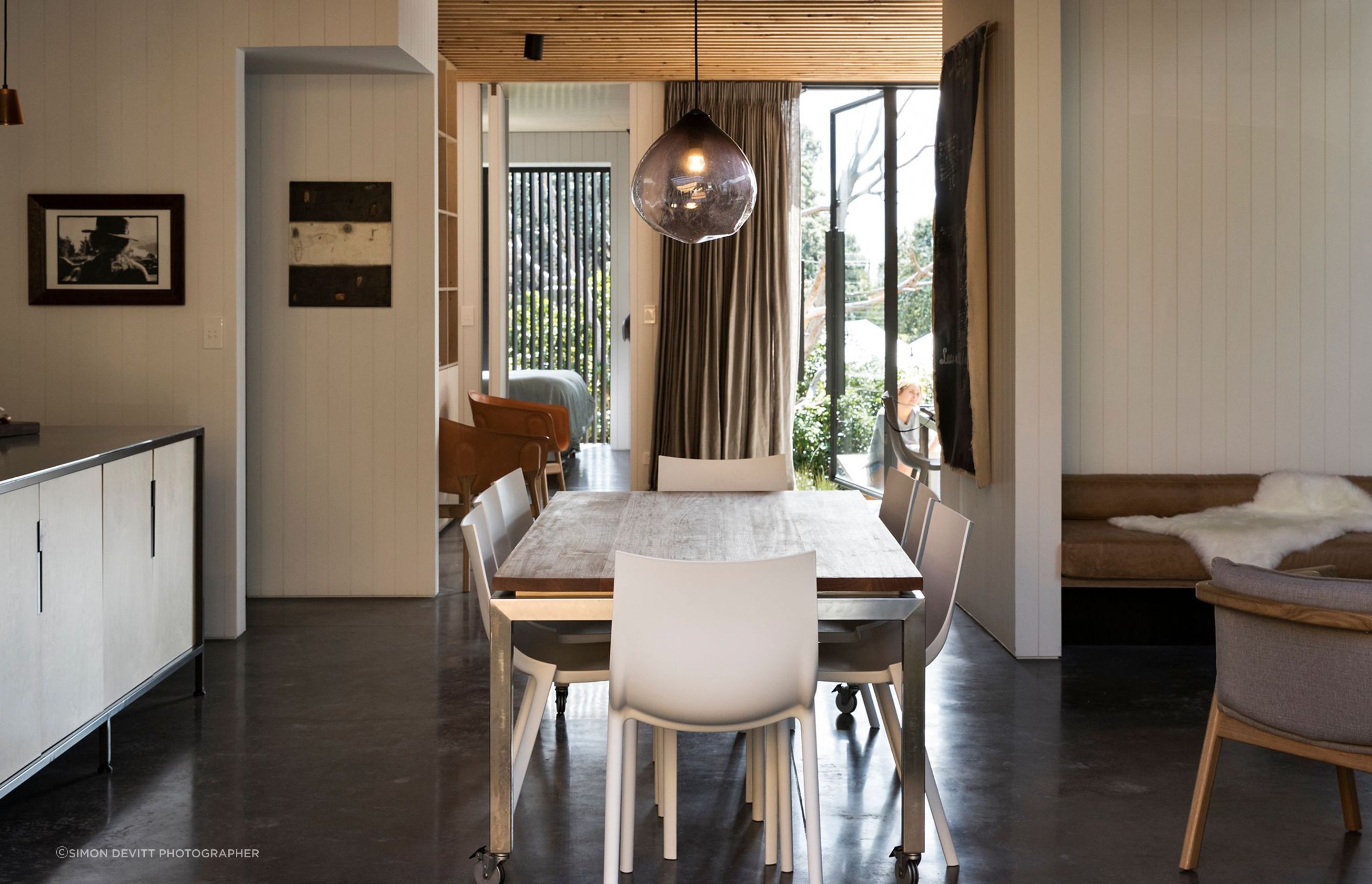
PeterFell C² Polished Concrete System is suitable for almost any indoor application from residential settings through to large commercial and industrial spaces. It has been used widely in New Zealand including in Christchurch Airport, numerous supermarkets and in hundreds of homes around the country.
“Suitable for ground, honed or polished floors, the PeterFell C² Polished Concrete system creates fantastic looking floors that will last for years,” Michael says. “With this system, the client can control the level of lustre in the polishing process from satin right through to a mirror finish.”
PeterFell specialises in coloured concrete, with a range of more than 80 colours available as well as the ability to create custom colours for bespoke projects. Make sure you visit PeterFell on ArchiPro here to find out more about creating the perfect concrete floor.
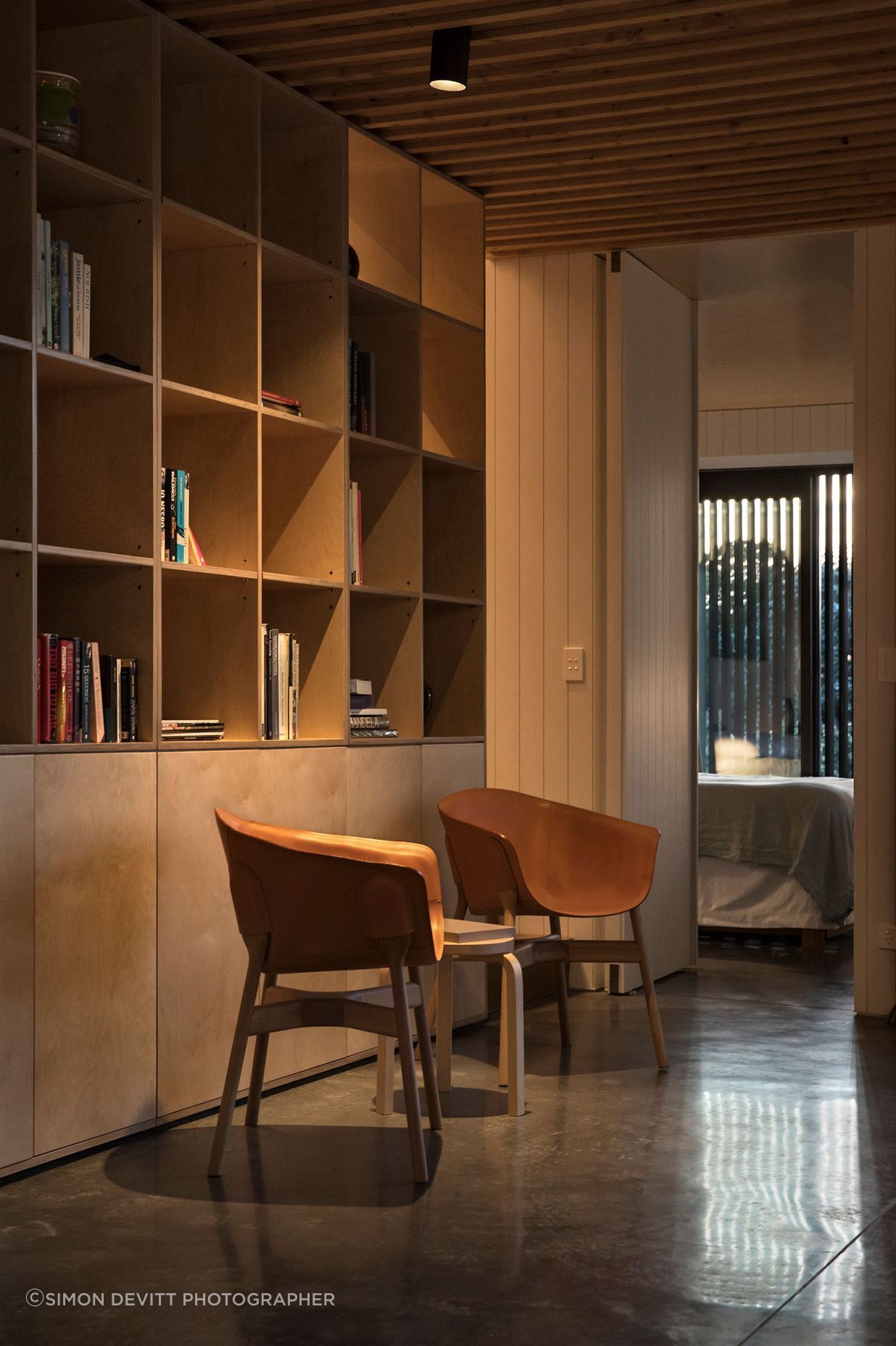