The party wall: a build featuring complex in situ concrete construction
Written by
18 July 2023
•
4 min read
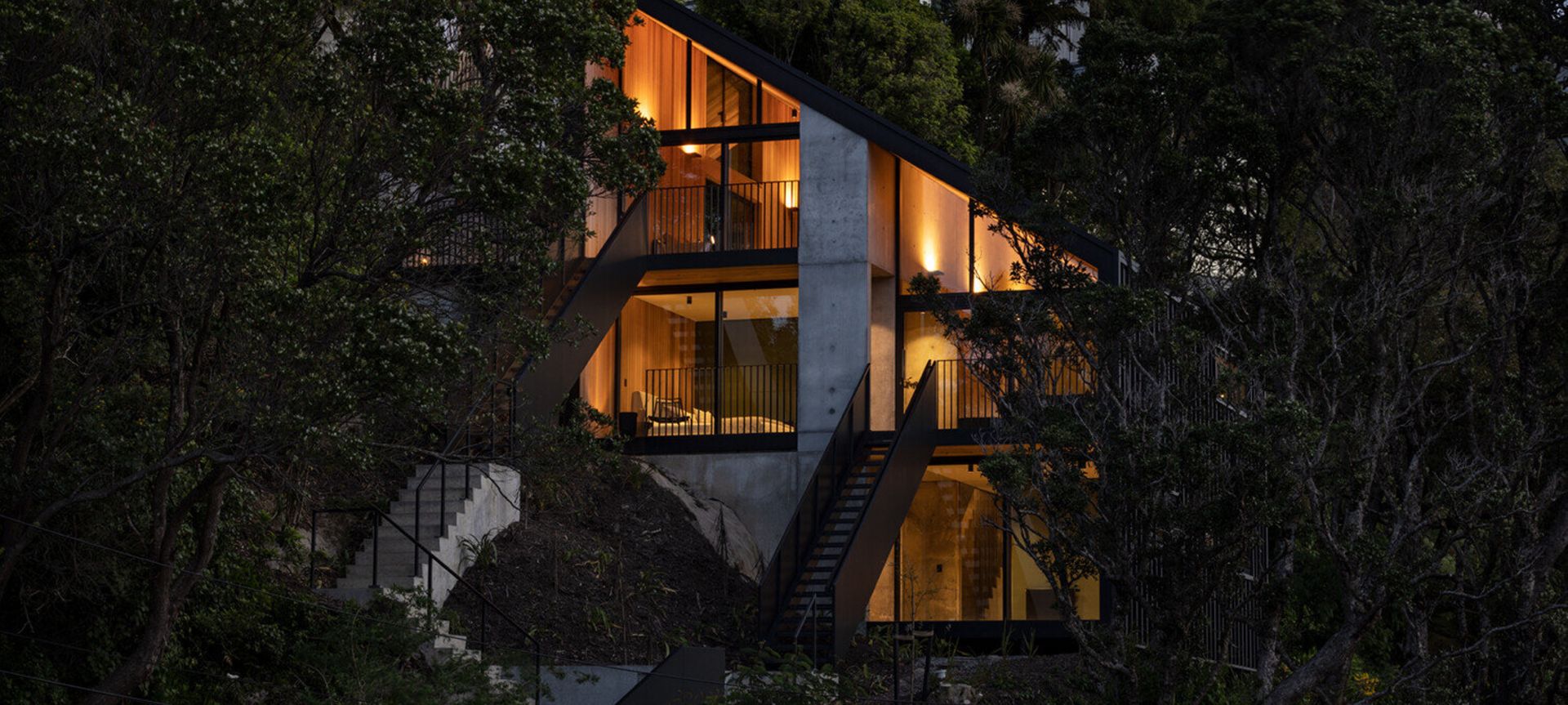
The site chosen for two, modest-sized townhouses designed by Patchwork Architecture overlooks Kelburn Viaduct in Wellington, and would have been a difficult site to build on, even if it hadn’t been for the three storey in situ concrete wall that divides the two houses.
Not only does the “party wall” provide a firewall between the two dwellings, it also features intricate in situ concrete staircases built into the wall, spanning the three storeys.
Director Adam Pierson from Dorset Construction, who is a specialist in building in situ concrete projects, says the build was further made challenging by the fact that it was started just before the first of the Covid-19 lockdowns.
“The concrete was poured in six stages, with stage two interrupted by the first Covid-19 lockdown. The wall was built over the course of the remaining stages, which made it a complex project.”
From inside either of the townhouses, it’s not possible to comprehend exactly how complex that process was, because you can’t see that the stairs for the other dwelling are recessed into the other townhouse's three-storey dividing wall.
Building that structure was one of the most complex in situ projects that Dorset Construction had been involved in at the time.
“Problem-solving the stages was not only about figuring out how to make the formwork the right shape but also making sure it didn’t come apart or move because concrete is quite hard to work with when you're doing anything vertical, because of the sheer weight of it.”
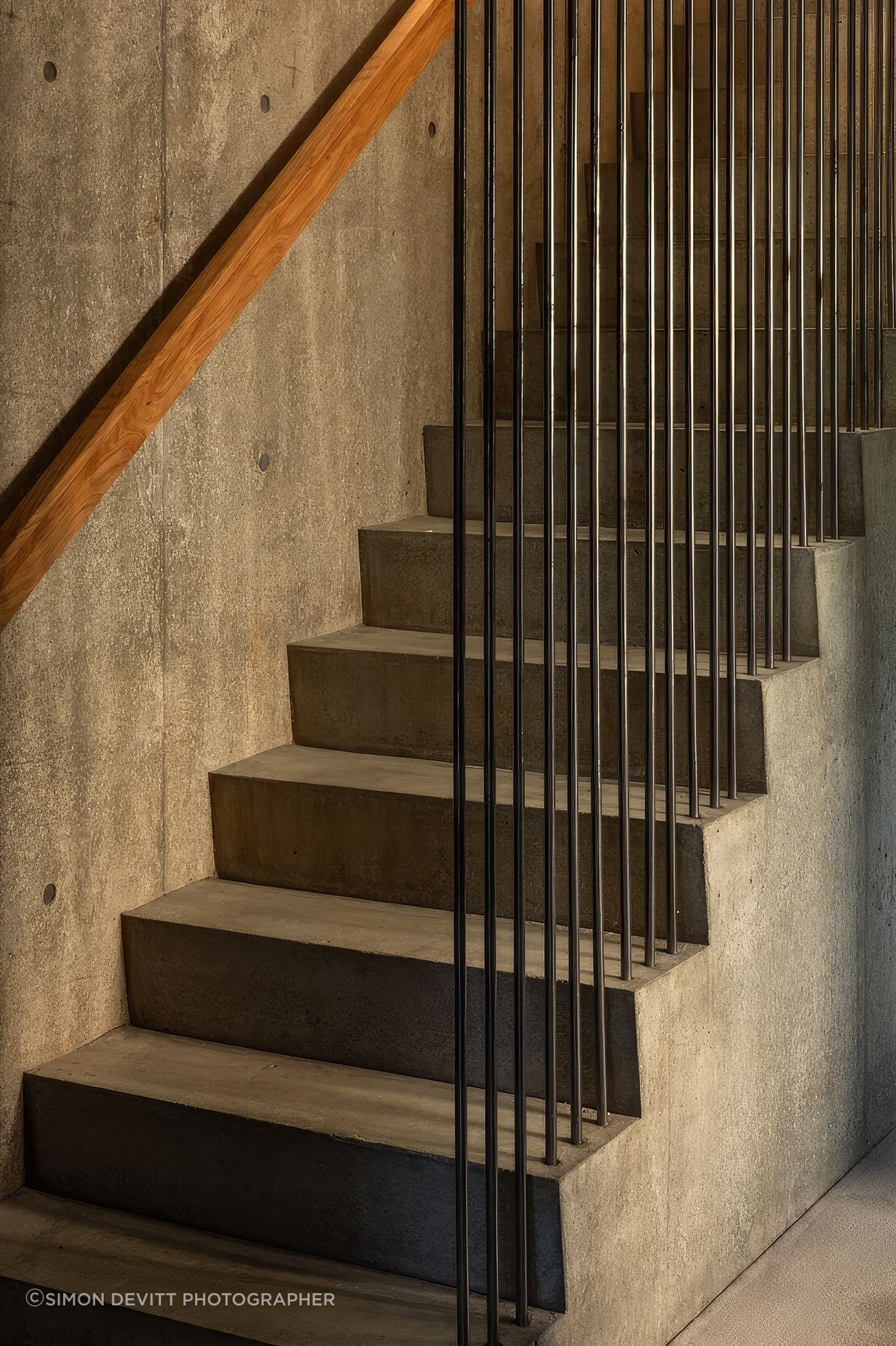

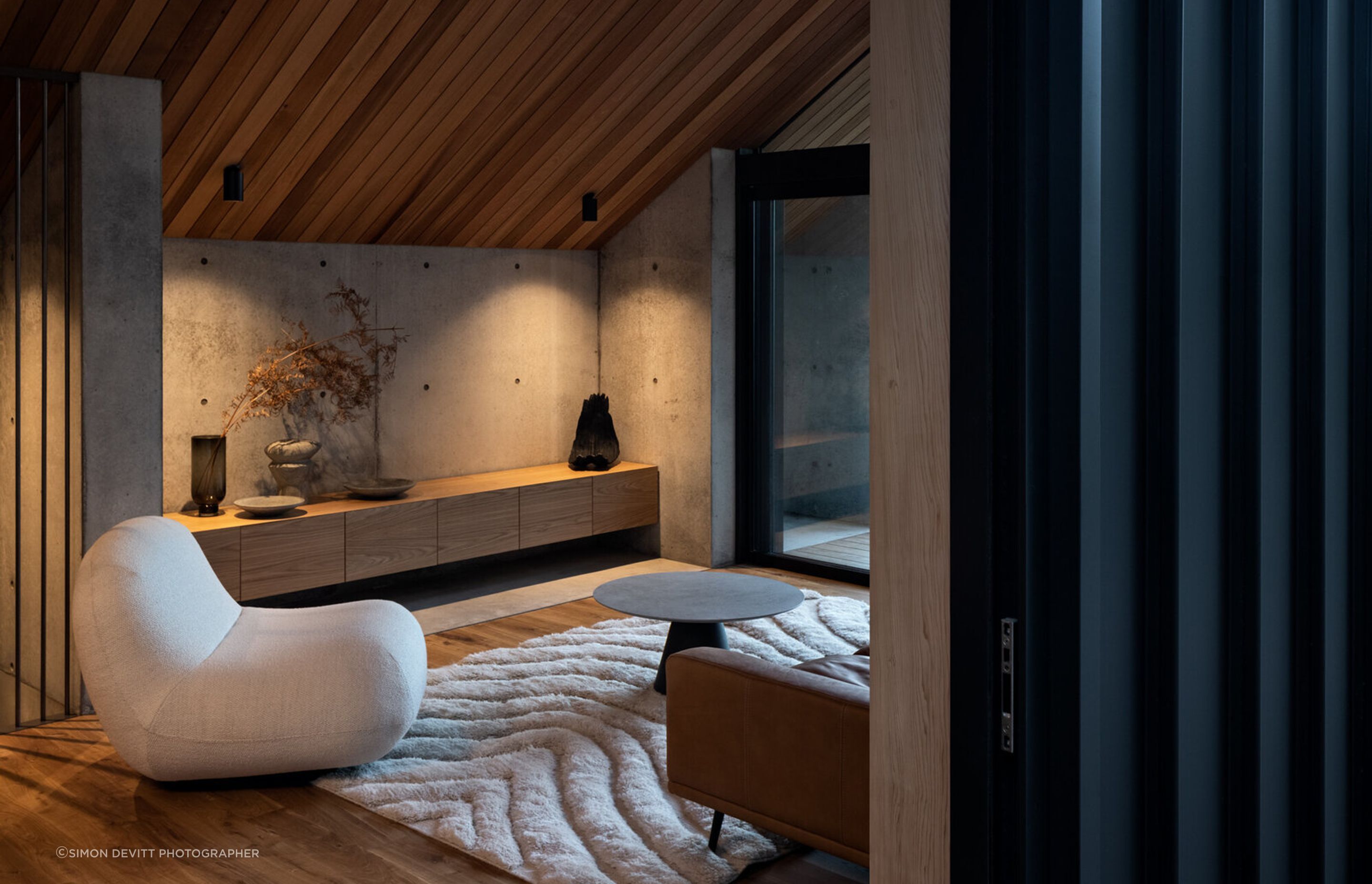
To make things even more challenging, due to the steep topography, it wasn’t possible to crane steel onto site, which meant that it was manpower alone that transported the heavy steel reinforcing onto site, and into place.
The formwork also had to be created in stages, ahead of each pour, says Pierson.
“We had to build the timber floors to help us gain access to the next stages of concrete as we built the wall and stairs up.”
To ensure each concrete pour was as full-proof and seamless as possible, Dorset Construction worked with Patchwork Architecture.
“We created a colour-coded 3D model to make sure we could get as much as possible done in each pour. Using the 3D model ensured we poured the right things in the right sequence.”
“In a structure like this, if your formwork has any weakness whatsoever it's not going to hold the concrete and it will either move or blow out completely. So everything has to be carefully thought out,” says Pierson. “Every time we stripped the formwork off to see how the concrete pour came out it was always a highlight and a relief!”
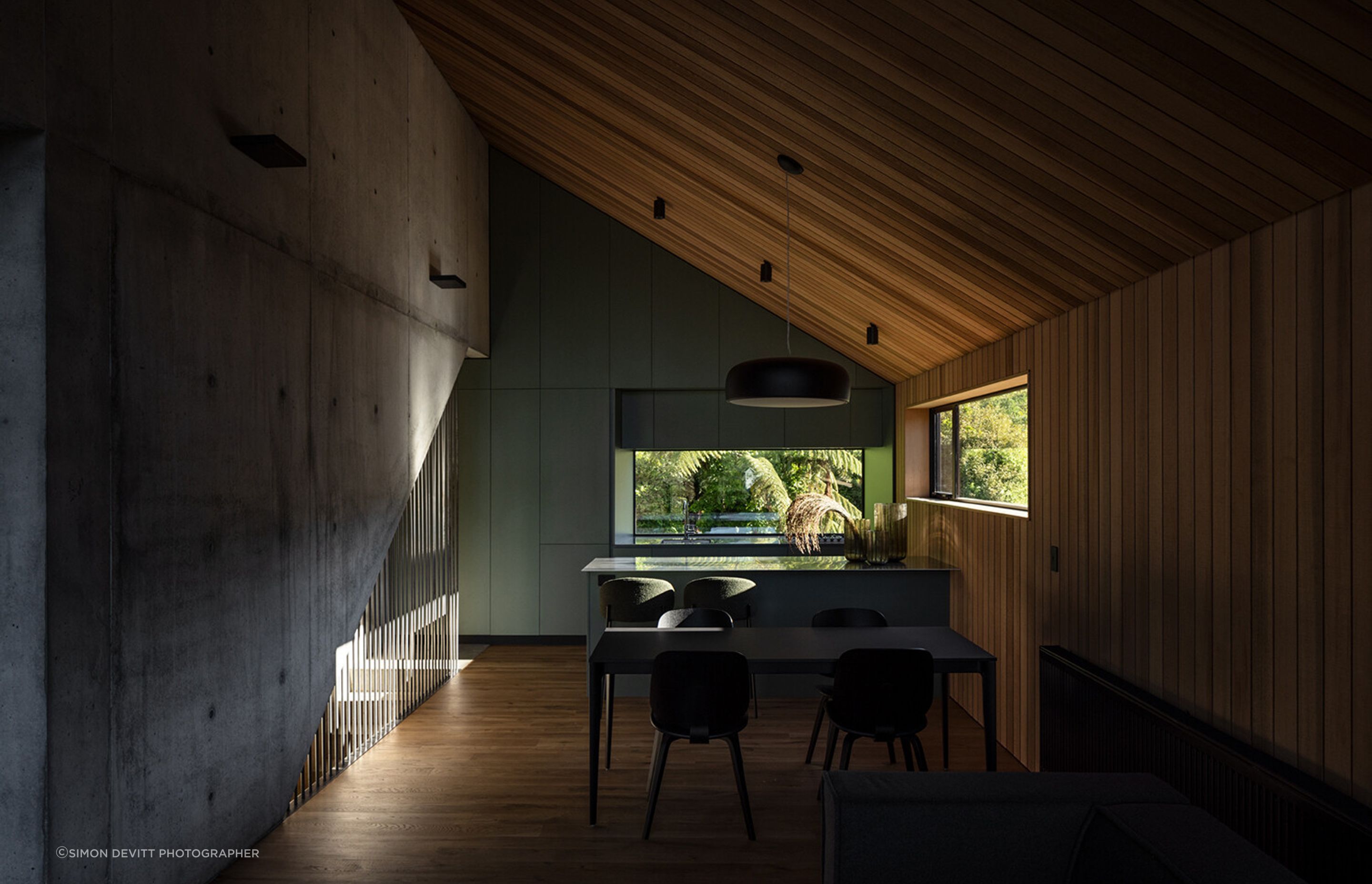
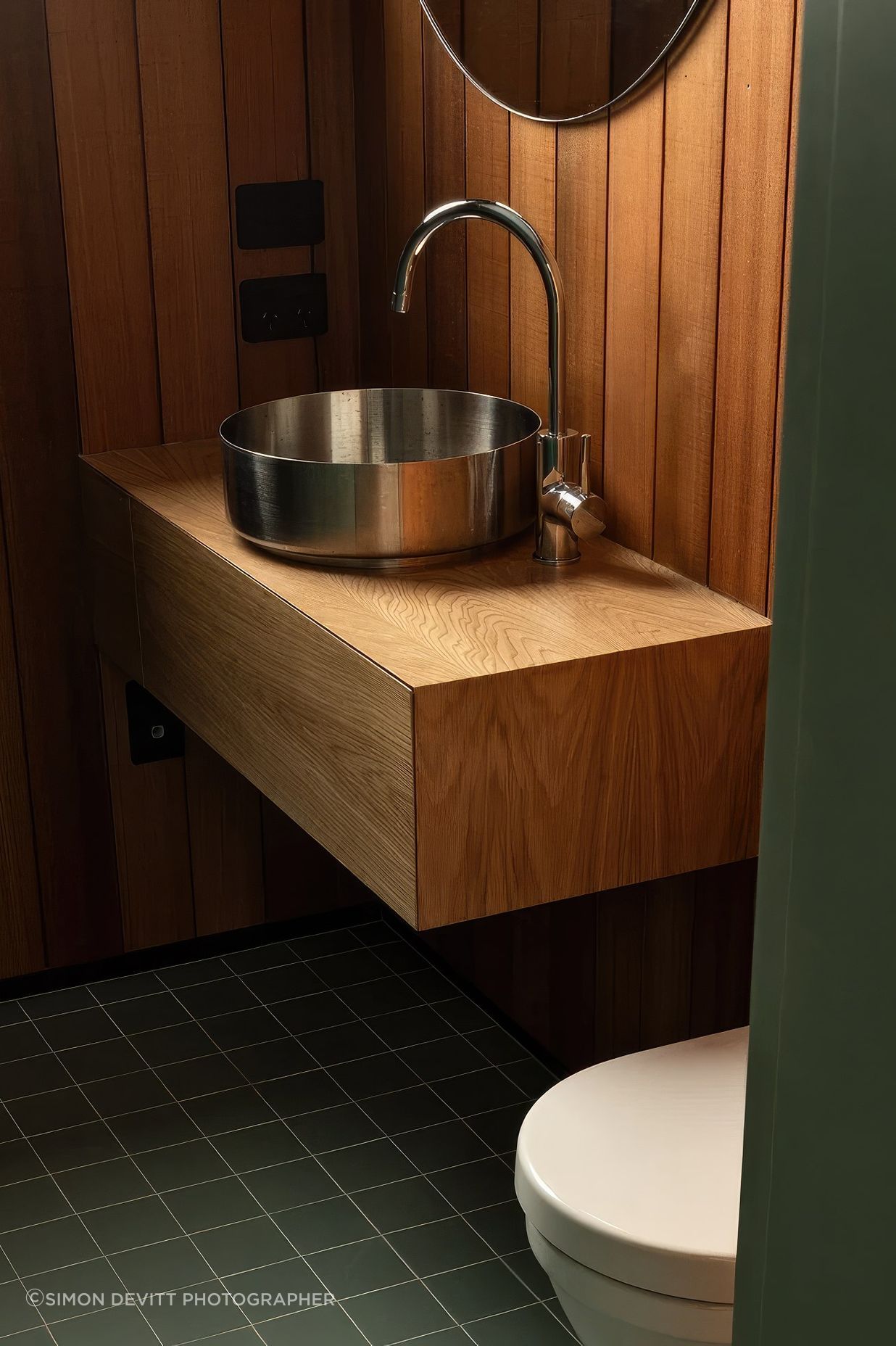
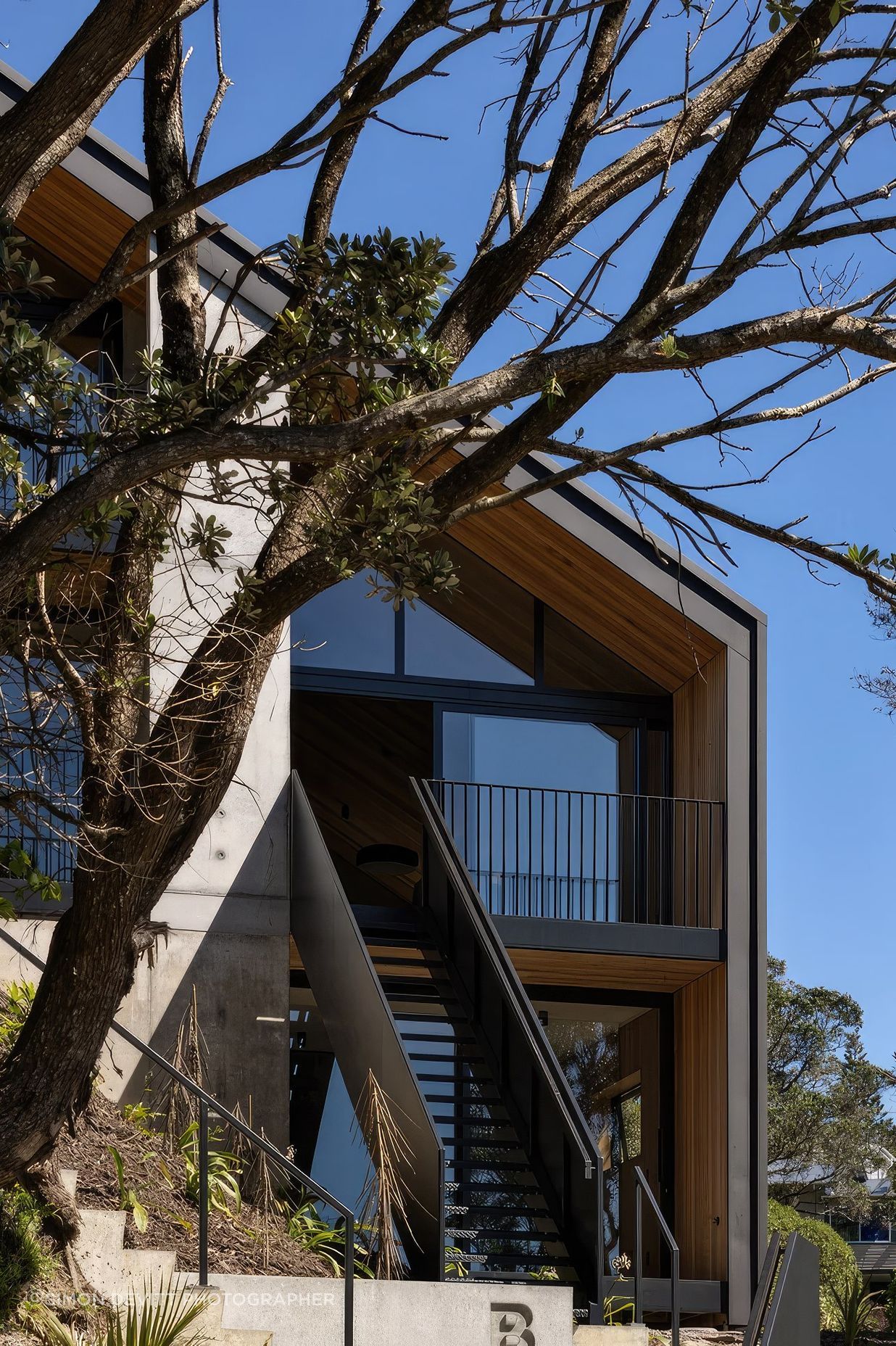
It’s a challenging way of building, but the result was worth all of the effort and showcases the builders’ skills, as the internal concrete staircase is an incredibly unique and sculptural feature in each of the townhouses.
Another standout feature is the cedar-lined ceiling that runs right through the interior out to the soffit on the exterior, showcasing the intricate carpentry work that Dorset Construction is known for.
Cedar lines many of the internal walls of each of the two-bedroom townhouses, and Pierson says supply chain issues with cedar meant that progression with the build was sometimes a challenge.
In spite of the pressures on timelines, supply chain and building construction, Pierson says the team is very proud of how well it has turned out.
The design received a national architecture award from NZIA and the feedback for the project has been positive.
“Our team pushed the boundaries of what we thought was possible with in-situ concrete and seeing it get recognition on a national level has really been a highlight and we’re incredibly happy with it.”
Discover more projects by Dorset Construction