uPVC windows and the Building Code changes — Why these are the windows of New Zealand’s future
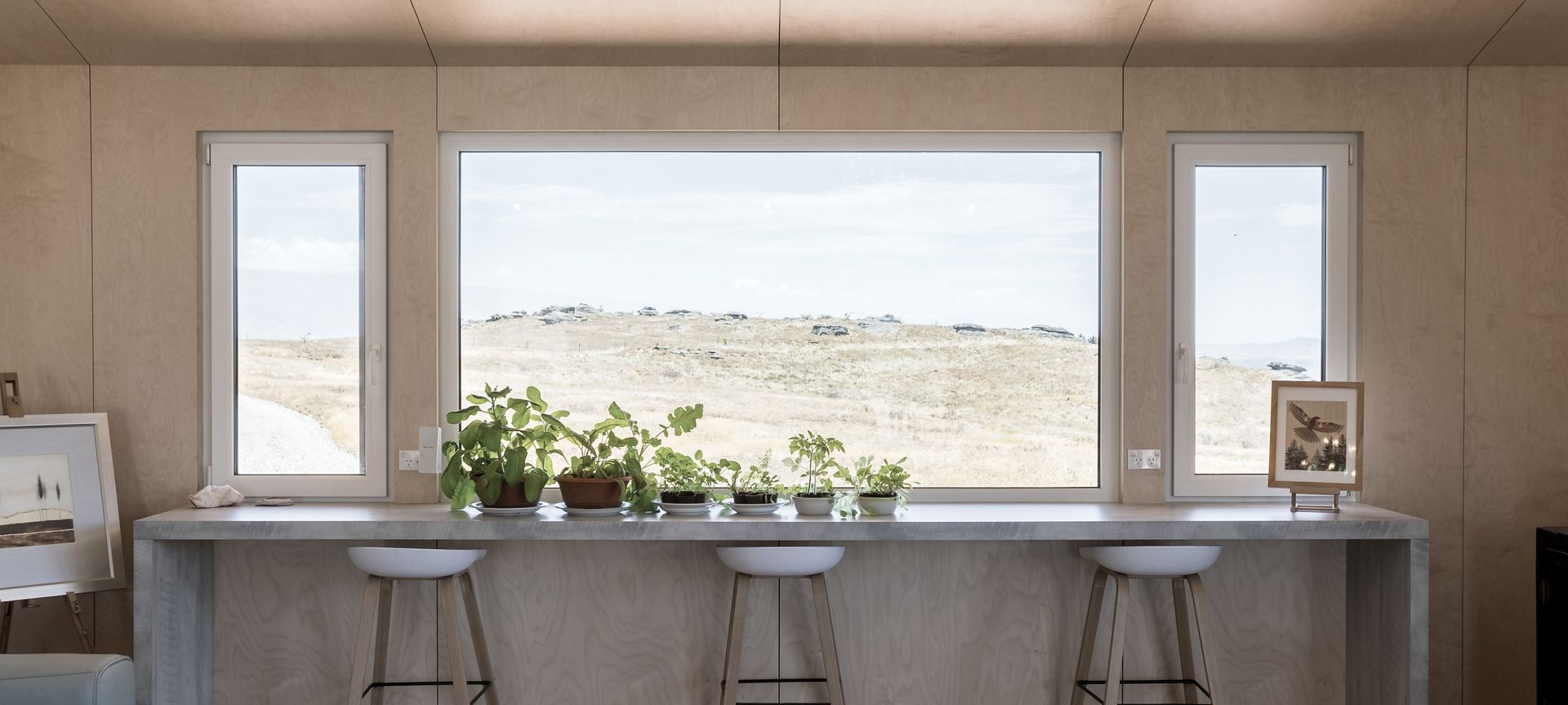
Aluminium-framed windows have been the norm in New Zealand for generations. Aluminium is an easily-accessible, easily workable material, with abundant numbers of manufacturers and suppliers throughout the country.
These types of windows are also cheaper and easier to make and install, and they remain a minimum requirement in the Building Code, albeit requiring double glazing after a Building Code change in the late 2000s. For this reason, they are still widely used as the window of choice for renovations and new builds with tight budgets.
But inclusion as a minimum legal requirement on the Building Code to make a dwelling habitable does not a good window make. Aluminium is widely known to be thermally inefficient, meaning both the heat and cold transfer easily through the joinery, even with double glazing.
Thermally broken aluminium windows — which involve having the aluminium 'split’, with a plastic separator providing thermal resistance — alleviate this problem somewhat. But they are considerably more expensive — a similar price to a much more efficient, warm and future-proof solution: uPVC windows.
Already common throughout much of Europe, where aluminium has largely been phased out, uPVC windows are slowly but steadily gaining momentum in Aotearoa — and this is being hastened by the most recent change to the building code.
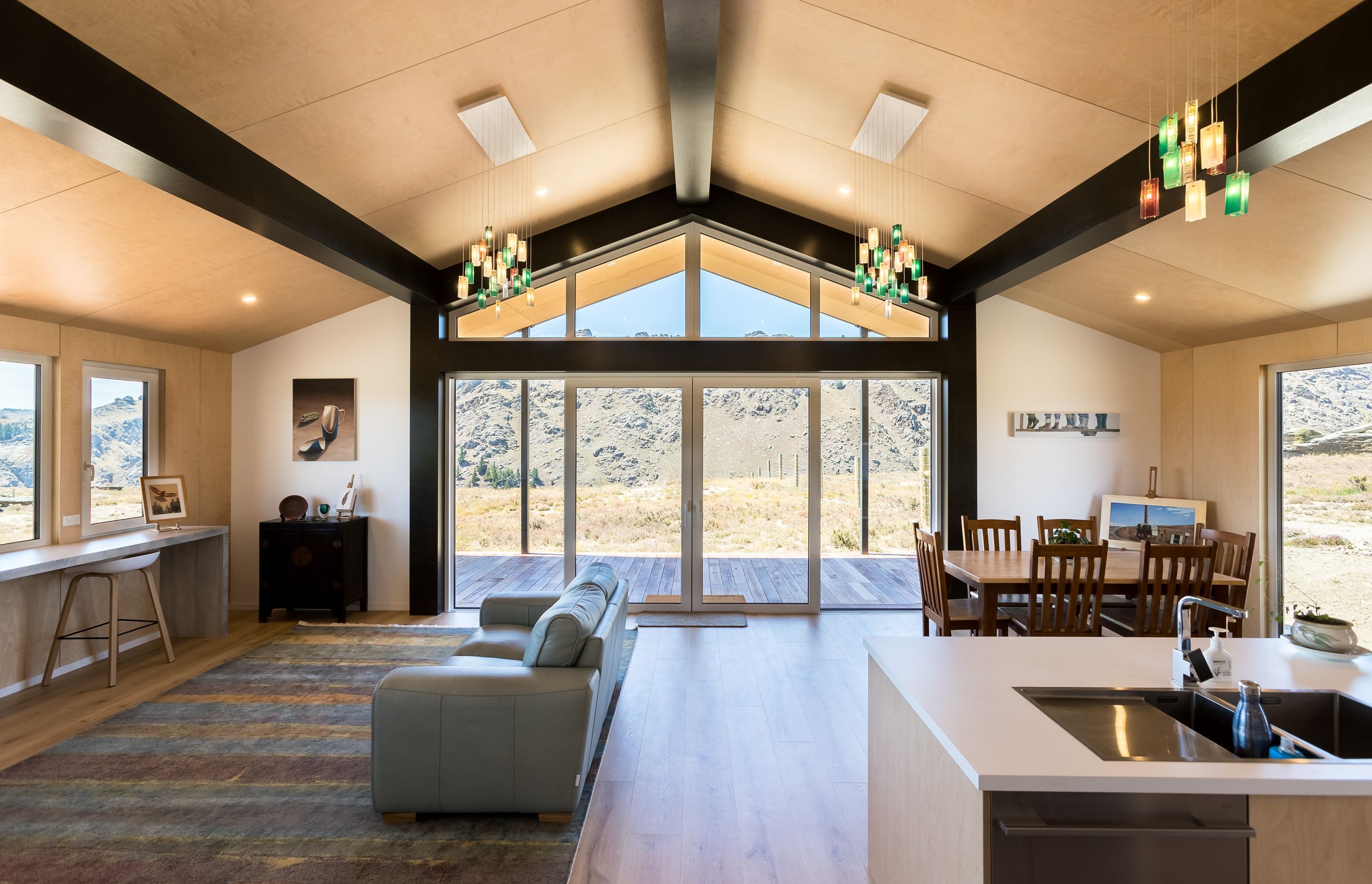
A rising standard
Martin Ball, the director of NK Windows, one of the country’s most experienced uPVC window suppliers, explains the change.
“The changes have lifted the H1 code nearer to international standards in terms of the R-value for the building envelope,” says Martin. “And they’re projecting a 40% decrease in energy costs for heating because of this.”
Crucially, the new code introduces new ‘climate zones’, where the colder South has new minimum R-values, covering most of Southland, Otago and Canterbury. According to the Ministry of Business, Innovation and Employment in its report, the R-values for these climate zones “are achievable with double glazing and Low E coatings in uPVC, timber frames and thermally broken frames.”
For these three regions, the ‘norm’ of non-thermally broken double glazed aluminium windows is no longer tenable. So companies like NK Windows, which is based in Canterbury, is on standby to assist in getting new builds up to code with uPVC windows.
Martin says some of NK Windows’ products already go above and beyond the minimum standards of the new H1 code, and expects that as more people learn about what the Building Code changes mean for them, they may be attracted to going beyond the minimum requirements in their region.
“Our expectation is that the market will get a lot more educated around the thermal performance of the building, and the energy costs, the carbon footprint,” he says.
“Some people who want to build better may see the new minimums and see that the rest of the world is already moving on from where we’re moving to. And this education has the potential to enhance opportunities for even better uPVC solutions — moving away from a historical tendency to build on the back of pure aesthetics coupled with a minimal build standard for the climate it’s in.
“I think this change in the Building Code will start a chain reaction, and people will become a lot more aware of the thermal efficiency of their homes.”
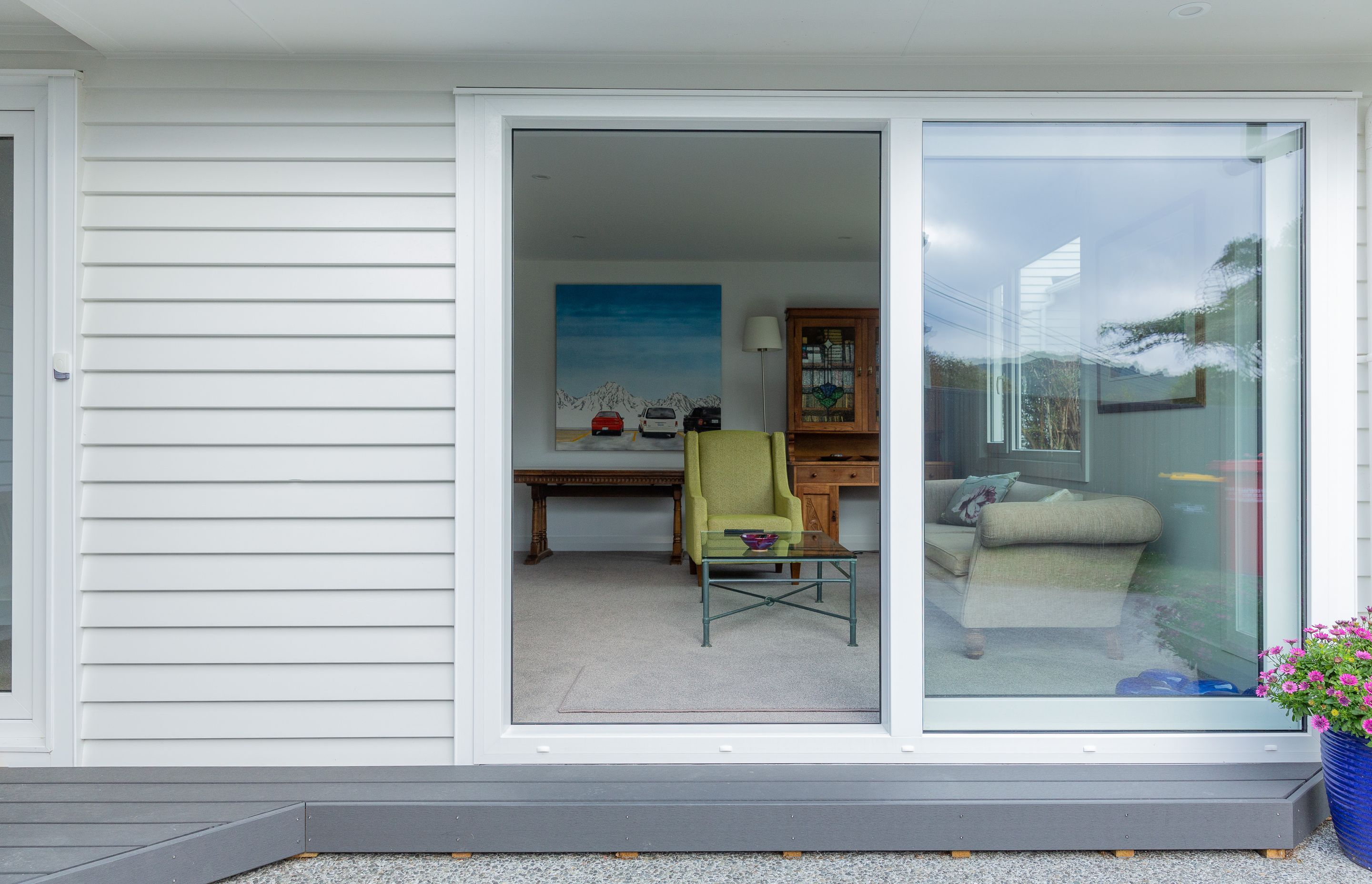
NK Windows on standby
In anticipation of the change, NK Windows is mobilising. The company is in the process of doubling its production capacity, and it plans to expand its operations around the country.
“Currently we're in the bottom half of the North Island, and will continue to increase our presence further north over the next three or four years,” says Martin.
“In fact, a large proportion of our enquiries are coming from further north, where minimum standards are less strict than the cold south — and while it may be down to a greater population, I think it’s a reaction to these Building Code changes, it’s people thinking about how to improve their homes past the minimum.”
uPVC windows are at the forefront of this trend, but Martin says that some misconceptions about uPVC are still holding a lot of people back. Many uPVC windows may not be suitable for the high UV sunlight we receive in New Zealand, and it’s common knowledge that uPVC is not as versatile when it comes to colours and aesthetics. But NK Windows knows this, and has options.
“We import windows that have been specifically designed and adjusted for the high UV environments in New Zealand,” says Martin. “And we have a continually expanding range of colour options with our uPVC solutions, including a lot of quite modern woodgrain finishes now.
“And in fact one of the benefits of uPVC is that you can mix and match colours — you can put a darker colour on the exterior, and in a lighter one on the interior, it’s quite versatile,” says Martin.
“It’s a win-win-win”
Learn more about NK Windows and its uPVC offerings.