UV coatings: creating unique products for your project
Written by
15 April 2024
•
4 min read
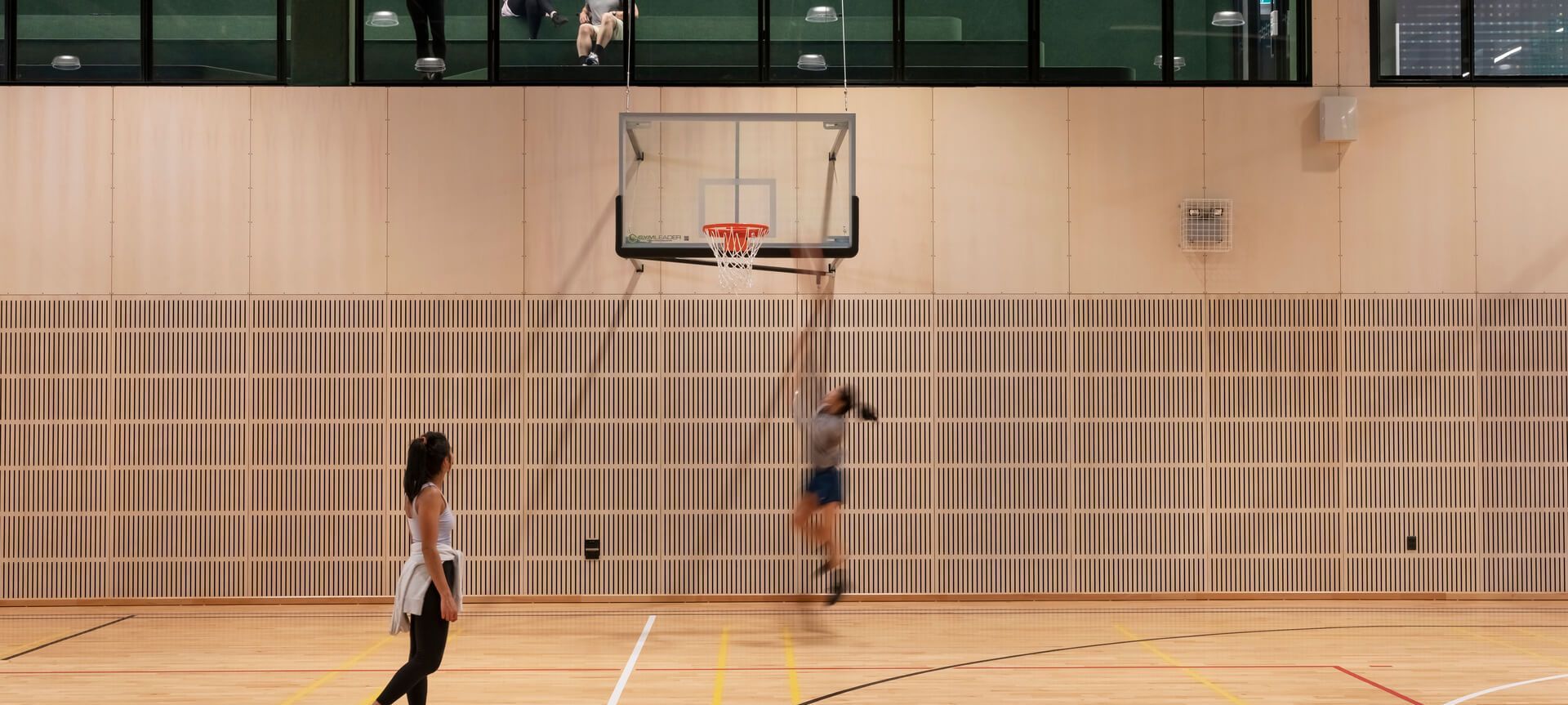
Bates Surfaces specialises in UV-cured coatings for building products and has been transforming interior panels into prefinished architectural products for more than 70 years.
The Bates team of UV-coatings technologists work with specifiers and specialist contractors on custom installations and are a strong partner for panel manufacturers in developing new product ranges for niche markets.
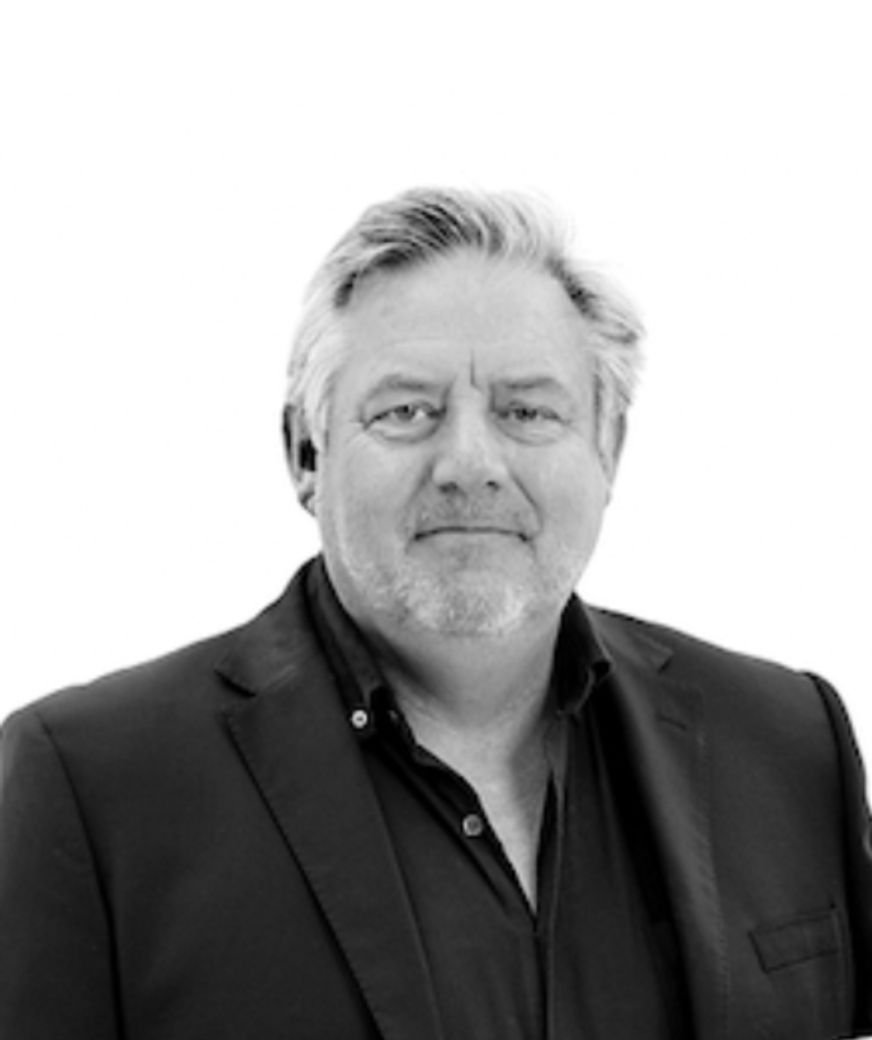
"Our inert UV coatings can achieve high-gloss and low-gloss matt surfaces that are incredibly hardwearing," says Andre Bates, CEO at Bates Surfaces. "We can produce very hard surfaces, some comparable to laminates, with equivalent abrasion resistance and a longer life."
Other features available with UV coatings include soft-touch fingerprint-free surfaces, antimicrobial properties, and intumescent additives to achieve a fire rating. UV stabilisers can also be added for greater protection against fade.
"UV coatings are also environmentally cleaner than solvent-based coatings, with minimal VOCs."
With an ultra-fast curing time, the coating process allows the quality of every panel to be checked, minimising wastage on the production line. Prefinished UV-coated panels get a better finish and durability than traditional paints and lead to faster installation times on site.
Services for product manufacturers and importers
Bates Surfaces coats well-known panel brands in the New Zealand market, partnering with top-tier local and global coatings companies. For OEM (original equipment manufacturer) products – such as doors, panels, and linings – Bates is a high-volume UV coatings partner for finished coatings and pre-priming on all major substrates.
"Our R&D facility has a lab equipped for prototyping, sampling, proof of concept and technology testing," says Bates. "Collaborations with producers combine the best of both worlds, drawing on our tech and manufacturing capability and their scale, marketing and distribution."
Their ongoing focus is on future-proofing, product durability, eco-friendliness and design. Bates has stayed at the forefront of product innovation to become New Zealand’s largest and most respected UV coatings applicators.
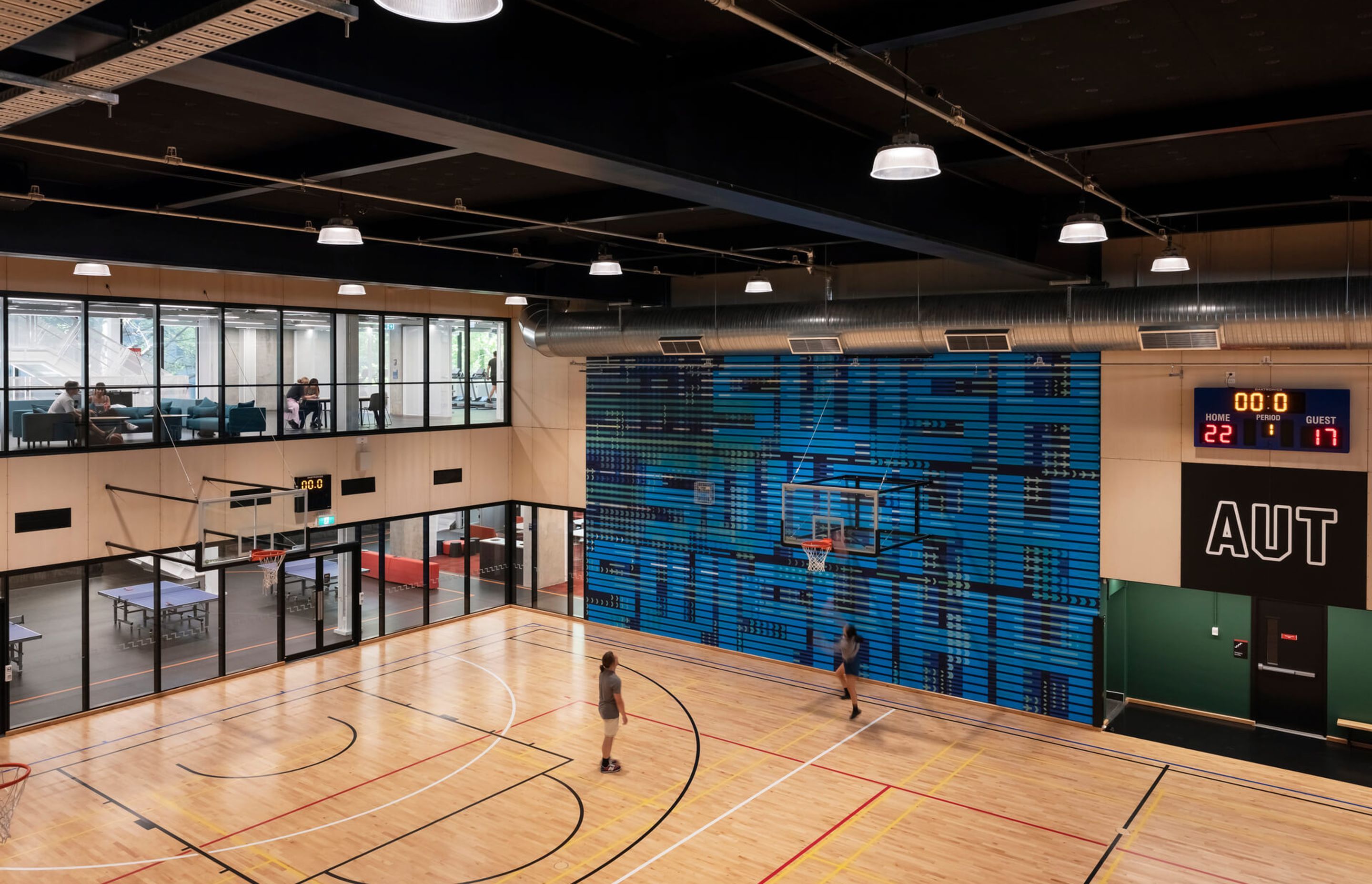
CustomCoat services reduce waste on kāhikatea panels
The Bates Surfaces CustomCoat service is for one-off, custom projects, providing a low-cost, factory-controlled coatings solution for special projects.
CustomCoat was the process of choice for acoustics specialists Asona, when they fabricated and installed veneered panels at the Sports Hall at AUT’s Te Āhuru Recreation Centre.
"The architects, Jasmax, specified kāhikatea as part of the Track my Tree programme. Sourced from a single log, it was used as the feature veneer on wall panels inside the three-story-high gymnasium," says Bates. "Asona approached us to do the coating, as the finish needed to be highly durable to take the impact of players and sports games."
A series of solid and perforated fire-rated MDF panels – to meet acoustic, fire and impact resistance criteria for the gym – were specified and finished with the native timber.
"The kāhikatea produced beautiful veneer leaves, which we book-matched and fixed to an MDF with a black core," says Suzanne Pooley, national sales manager for Asona. "For the perforated panels, we developed a pattern to suit the design and specification requirements and practical fixing points."
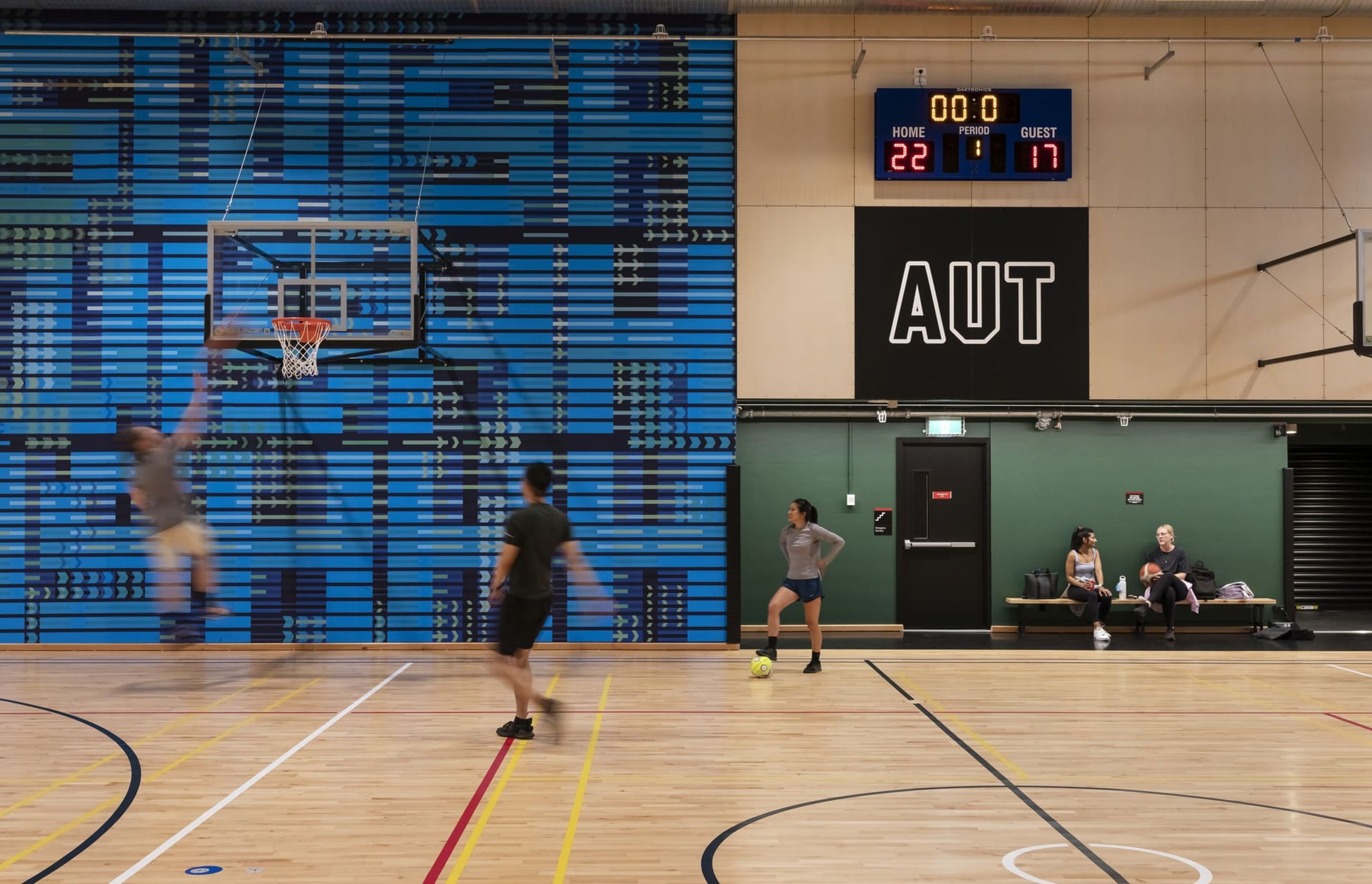
Often referred to as ‘New Zealand oak’, kāhikatea has a very pale tone, so Bates Surfaces created a range of samples that maintained the original raw material colour for design approval.
"In combination with a special barrier coat, we were able to keep that naturally pale tone," says Bates.
"As it’s a protected native timber, with a permit required for milling for commercial use, there was access to only one log. A finite amount of veneer was available – they had just enough to do the gym fit-out."
With no room for error, the CustomCoat process proved ideal.
"Thanks to the instant curing process, we can spot any imperfections immediately and adjust the line, which keeps waste to an absolute minimum."
The CustomCoat service used for this AUT gym interior is offered by Bates Surfaces for one-off projects. Sectors include hospitality, workplace, education, retail, industrial, commercial and residential interiors.
Quick turnaround, quality control
For CustomCoat and OEM services, turnaround is efficient and rapid.
"What we make today is for sale this month," says Bates. "A customer can drop their panels in and collect them in weeks or even just a few days.
"We can do commercial one-off jobs at a scale and a cost point that is only possible because of our investment in world-class technology. Thanks to our controlled factory environment, we provide consistency and quality control right through the run."
Contact Bates Surfaces to learn more about OEM services and CustomCoat. The brand’s in-house products – PureCoat, PlyPlay, and Fenta Ceiling Tiles – can also be viewed on ArchiPro.