Viblock Masonry for consistent design and a speedier, more efficient build
Written by
03 September 2020
•
3 min read
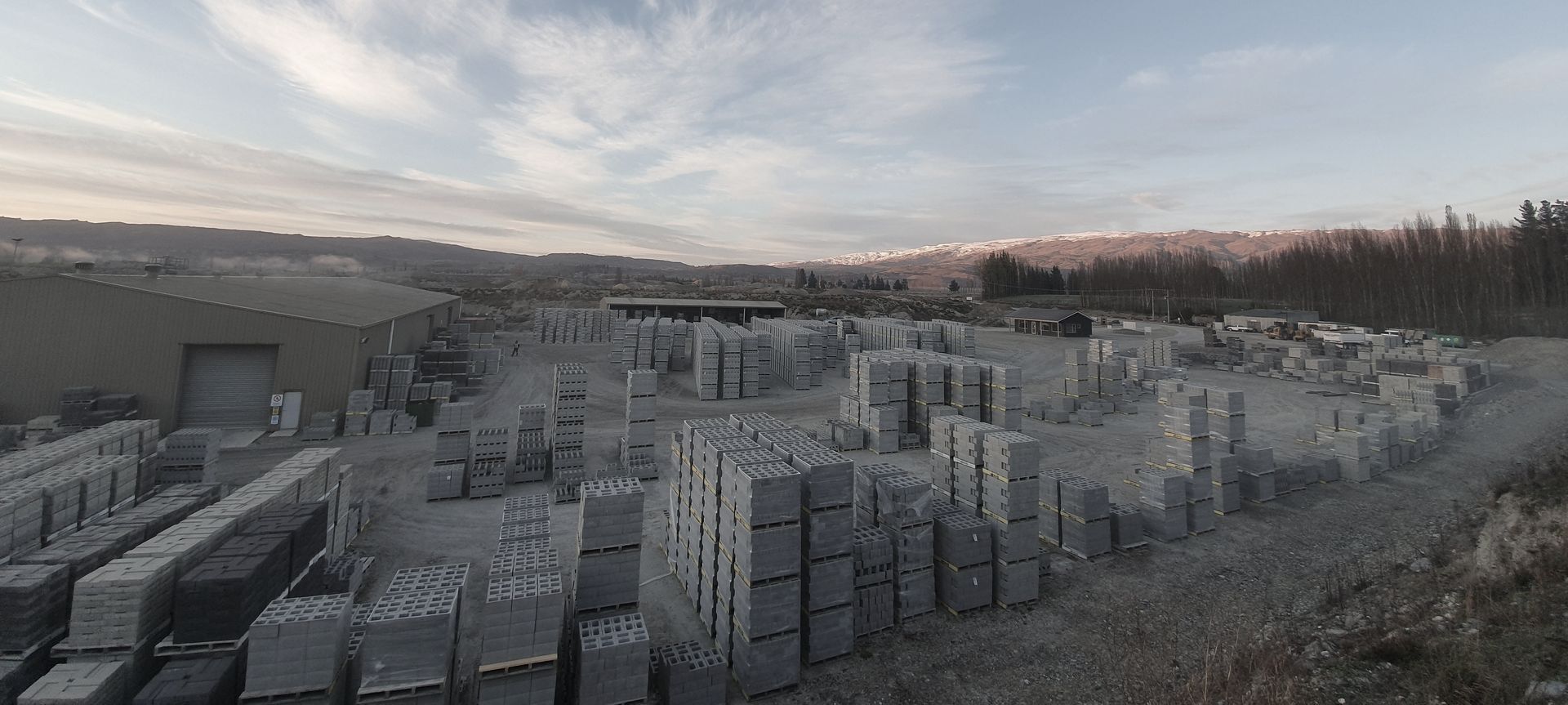
Jim Hunter, general manager of Viblock, which manufactures architectural masonry blocks and pavers in Central Otago, says designers can use NZS4229 to specify masonry without the need for any engineering input.
Compared to other passive-home materials such as stone, rammed earth, clay bricks and in situ/pre-cast concrete, concrete masonry is a fast build product with well-established design systems.
“That’s a massive benefit to designers as it speeds up the concept design phase. They can design a building to that standard without having to go back and forward to engineers, which can be quite a tense process.
“Having the consistent design developed by industry experts creates consistent trade products which means an efficient build, not based on subjective opinion. It’s based on agreed standards.”
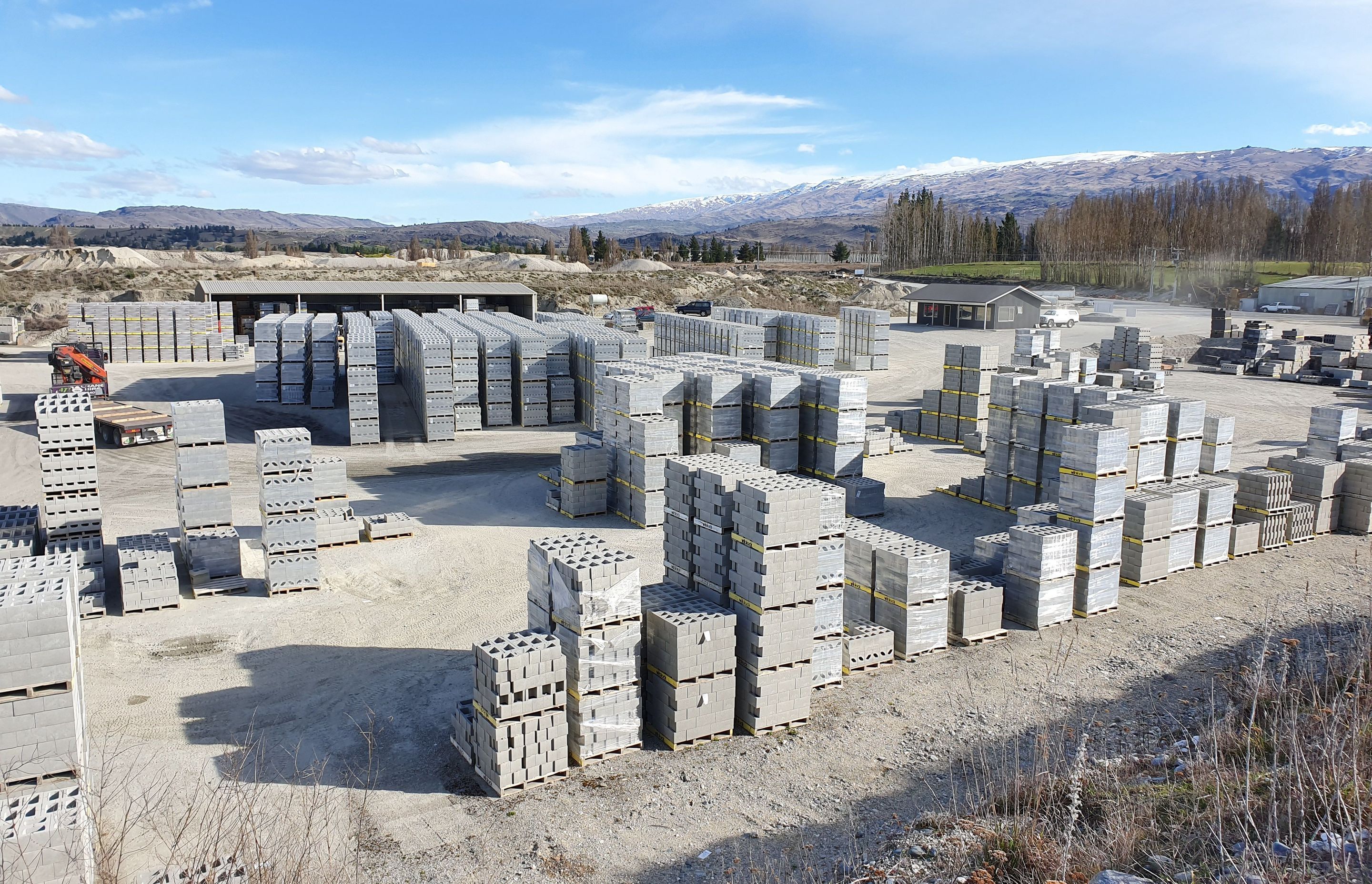
The NZ Concrete Association has done a lot of work raising awareness in this area and offers specific training for free.
BRANZ has helped promote the fact that using the thermal mass of concrete can provide a better performing home with summer cooling and winter warming. “We’re seeing a trend where people are utilising this principle even in timber framed homes with a north-facing masonry or Trombe wall.”
Other benefits of masonry include: improved sound insulation and durability compared to more lightweight materials that can be structurally compromised, hence the leaky building scenario; it requires little maintenance during its lifetime when laid and sealed to industry standards and, it is an ideal choice for fire walls.
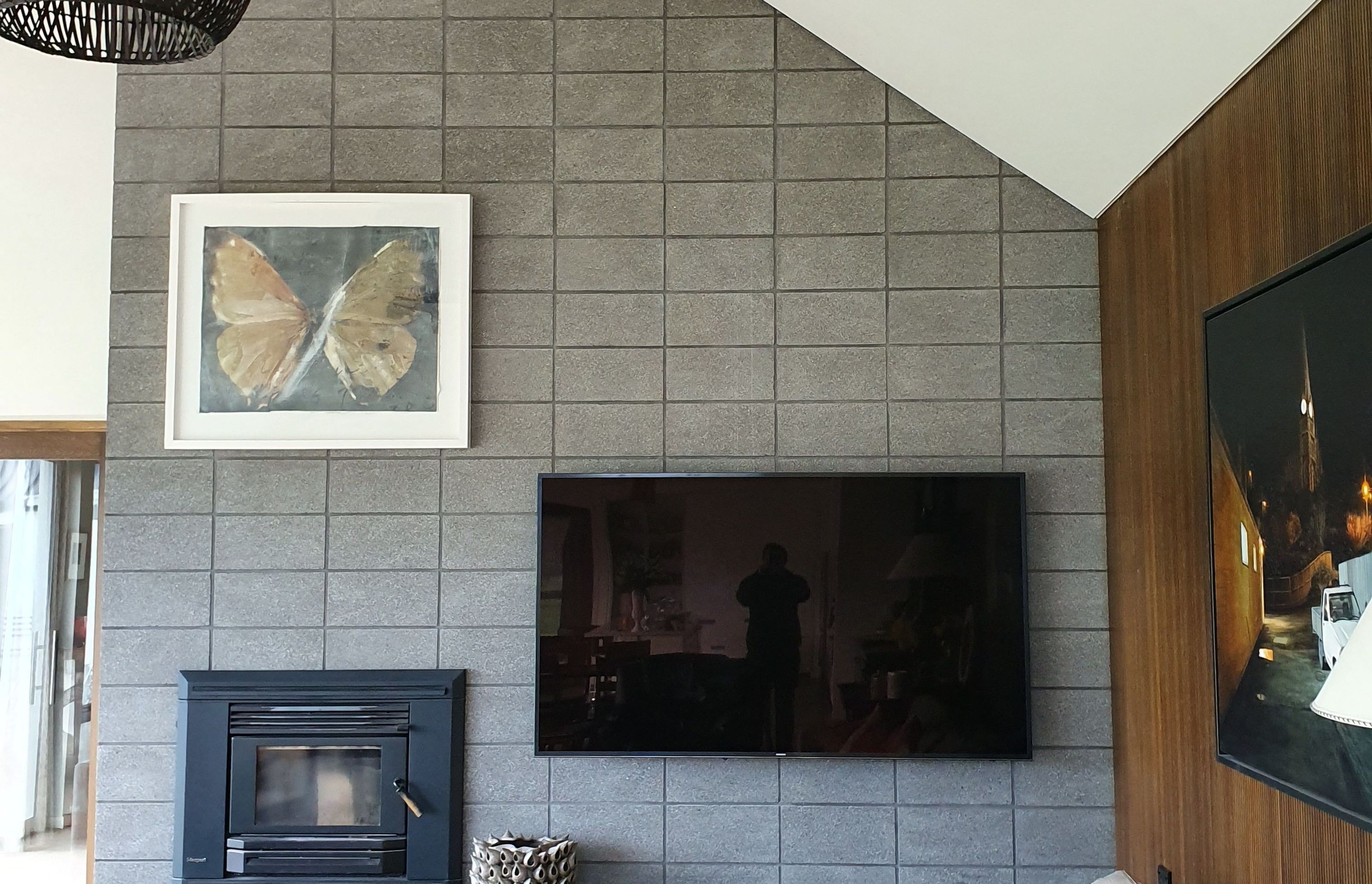
When selecting a masonry product, Jim says consistency is key. To that end, Viblock is a superior choice as it has a very efficient manufacturing process that allows structural quality and a repeatable colour range.
“We operate out of two sites in the South Island, but our concrete blocks are manufactured at our Earnscleugh, Central Otago, site, where an old gold mine put their gold tailings. We take the aggregate from that waste source—which has already been processed twice previously, first by the early mining settlers, then by the big mining companies—and now we’re making it into our masonry products. It’s a really consistent end product in terms of colour, texture and general performance.
“When we add different colour matches, we can be confident, provided site processes are followed, that we can colour match accurately. Most other companies aren’t producing coloured masonry because historically they have had issues.”
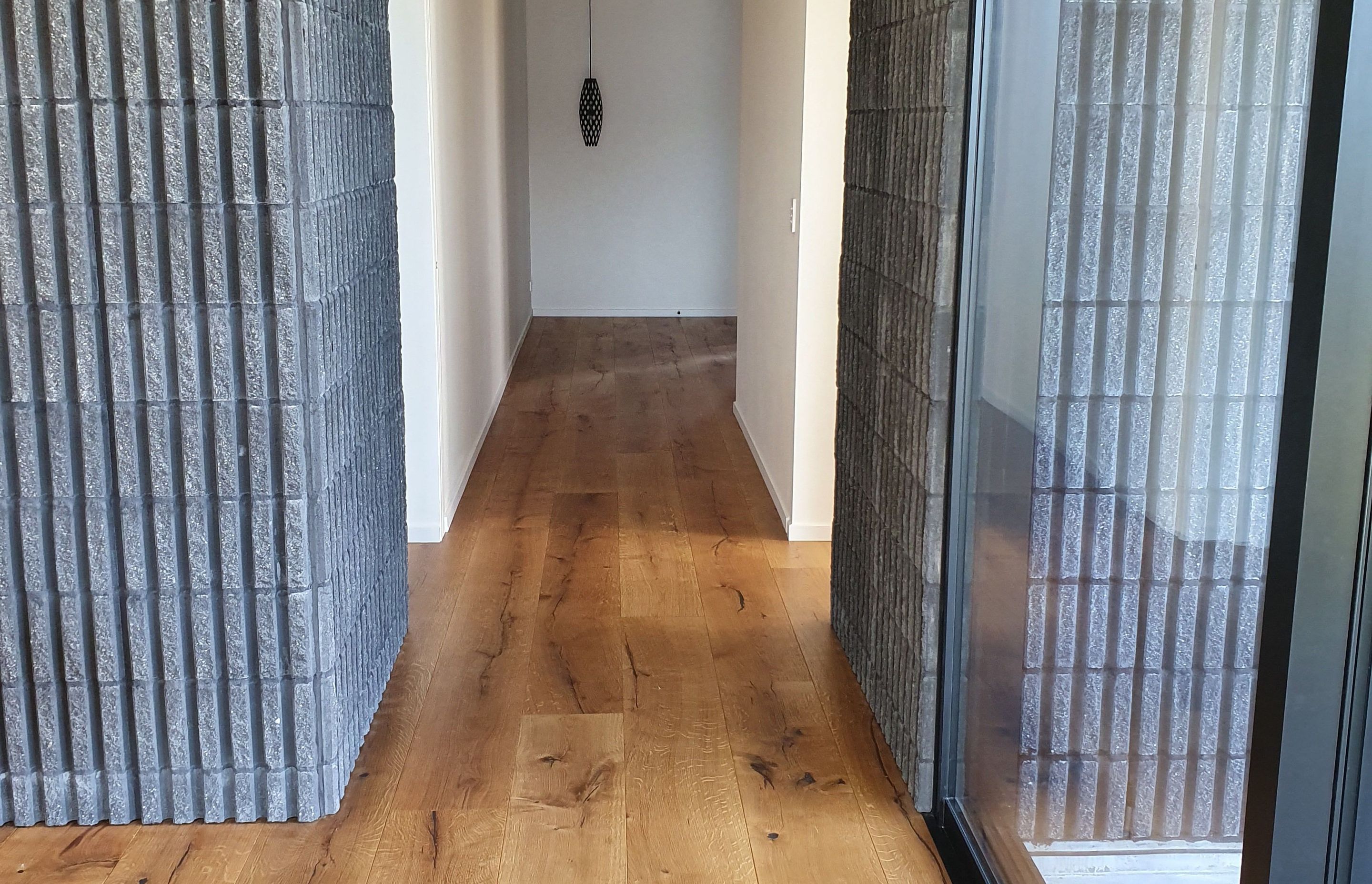
Viblock provides further variety with a range of sizes and finishes for structural blocks and veneers. Blocks can be honed for a smooth, more refined finish. When the blocks undergo most of the secondary processes, the aggregate is exposed so you can see the tailings.
“I like to say there are probably a few gold nuggets in there,” jokes Jim.
The masonry surface can be bush hammered for a textured surface or once it's dried, it can be guillotined and fluted for a natural split face look.
“That’s starting to become popular again,” says Jim.
Another option proving to be a popular is a process called rumbling, which softens the corners and edges resulting in a weathered look, creating an aged effect on the building.
People like the look of masonry, says Jim. “And we can meet most people’s wants and needs in this respect. But ultimately there is a raft of reasons to use masonry that give your home amazing performance.”
Learn more about the benefits and features of using Viblock for your building project.