There are lots of boxes to tick when designing and completing a construction project – crucially, projects of all sizes need to be delivered within budget and on time in a way that considers environmental impact while delivering stunning results.
Engaging the expertise of experienced product suppliers and manufacturers, such as Robertson's Building Products, is key to achieving this.
Known for its product innovation and extensive range of clay, glass, and stone bricks, the Melbourne-based company provides customised wall solutions to help craft design visions into practical, high-quality, award-winning designs.
One of these innovations is the Brick Inlay system – a façade solution by Robertson’s Building Products’ subsidiary, Robertson Façade Systems – which speeds construction time and significantly reduces build costs, while still enabling projects to be delivered to the highest standards.
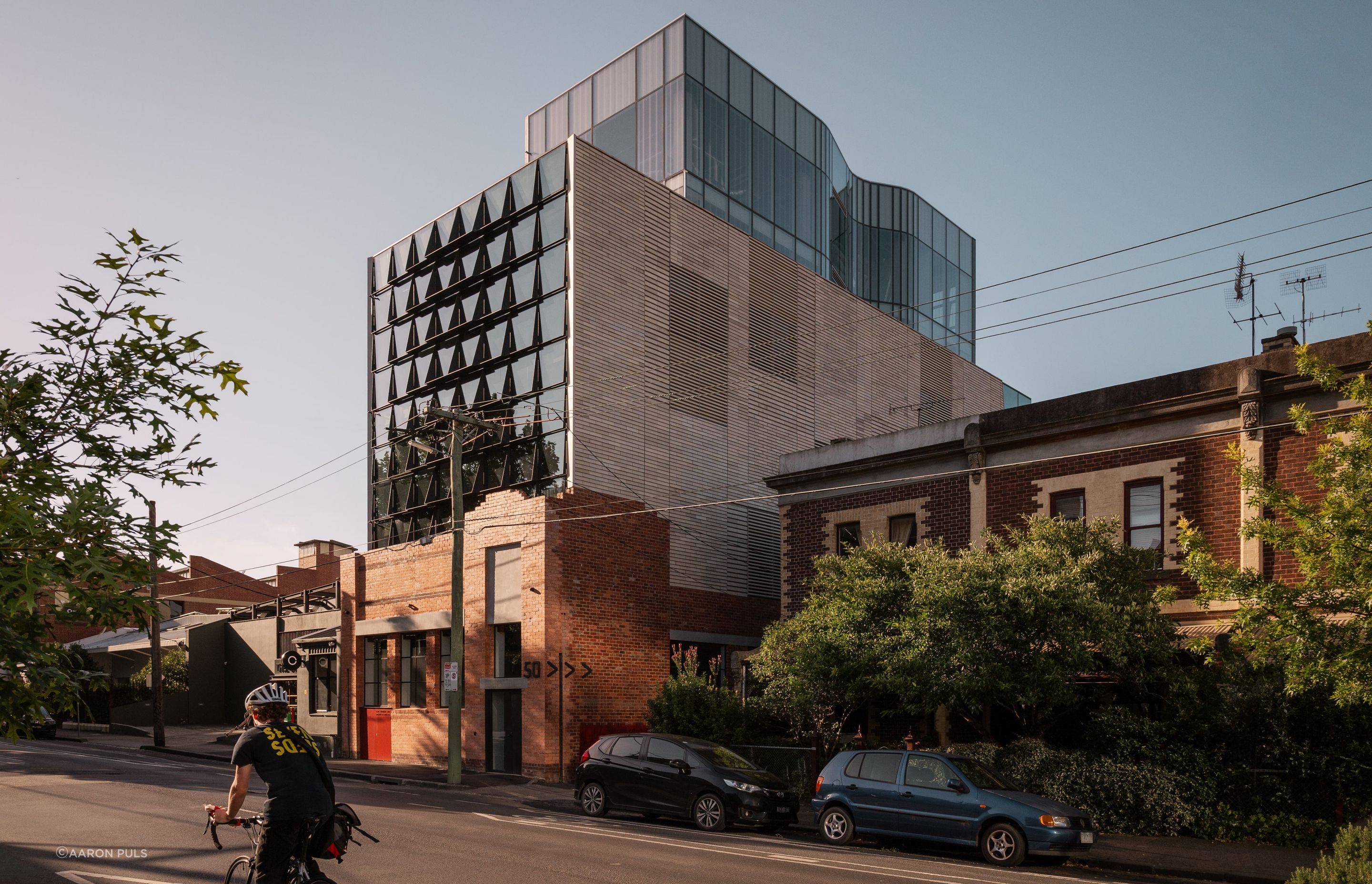
“The beauty of a panellised form of brick, is it gives us flexibility in construction to achieve things that might be otherwise difficult in a traditional sense. For example, if you have a zero lot, you can't put scaffolding on your neighbour's side to build the wall on your side. So, what options do you have?" says Peter Robertson, director of Robertson’s Building Products.
Construction of façades can also face complications due to weather, seismic requirements and time constraints. However, by embedding brick, porcelain, or stone tiles into precast concrete panels during off-site panel manufacturing, patterns and textures can be customised – including arches and curved façades – in a cost-effective way that meets structural needs and isn’t impeded by poor weather conditions.
“With brick embedded in precast concrete, we can tick all of those boxes,” says Robertson.
“Reinforced concrete is a tremendous product to address seismic issues, and embedding the brick within the concrete creates this extraordinary bond which is much greater than what can generally be achieved with an adhesive solution or mechanical solution.
“Part of this thinking rolled through to Zero Gipps where it was a different approach to one traditionally taken with brick. With a shingle-style approach, the brick isn’t fully embedded in the concrete, but the strength of the bond allowed the confidence to design and manufacture.”
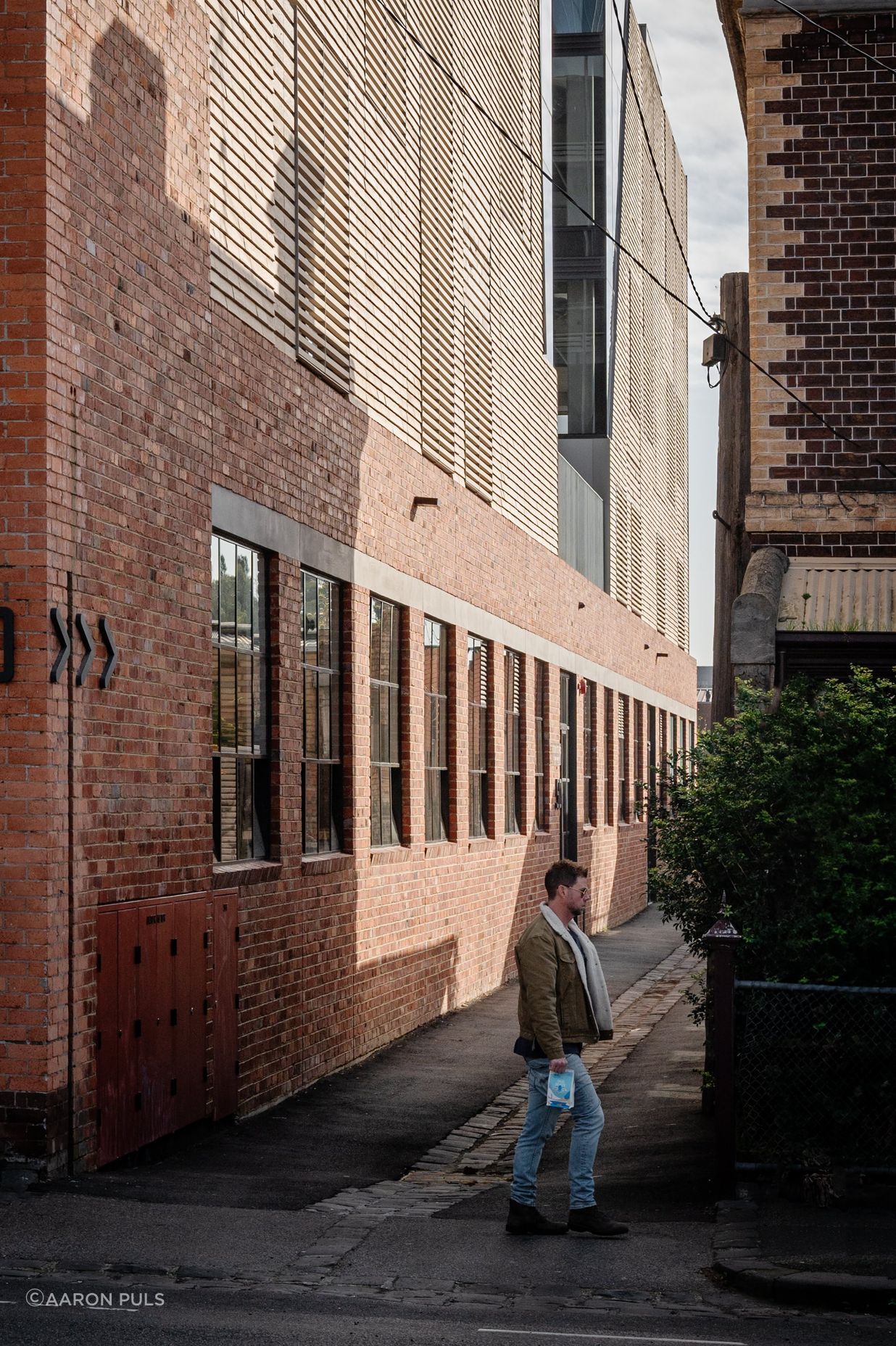

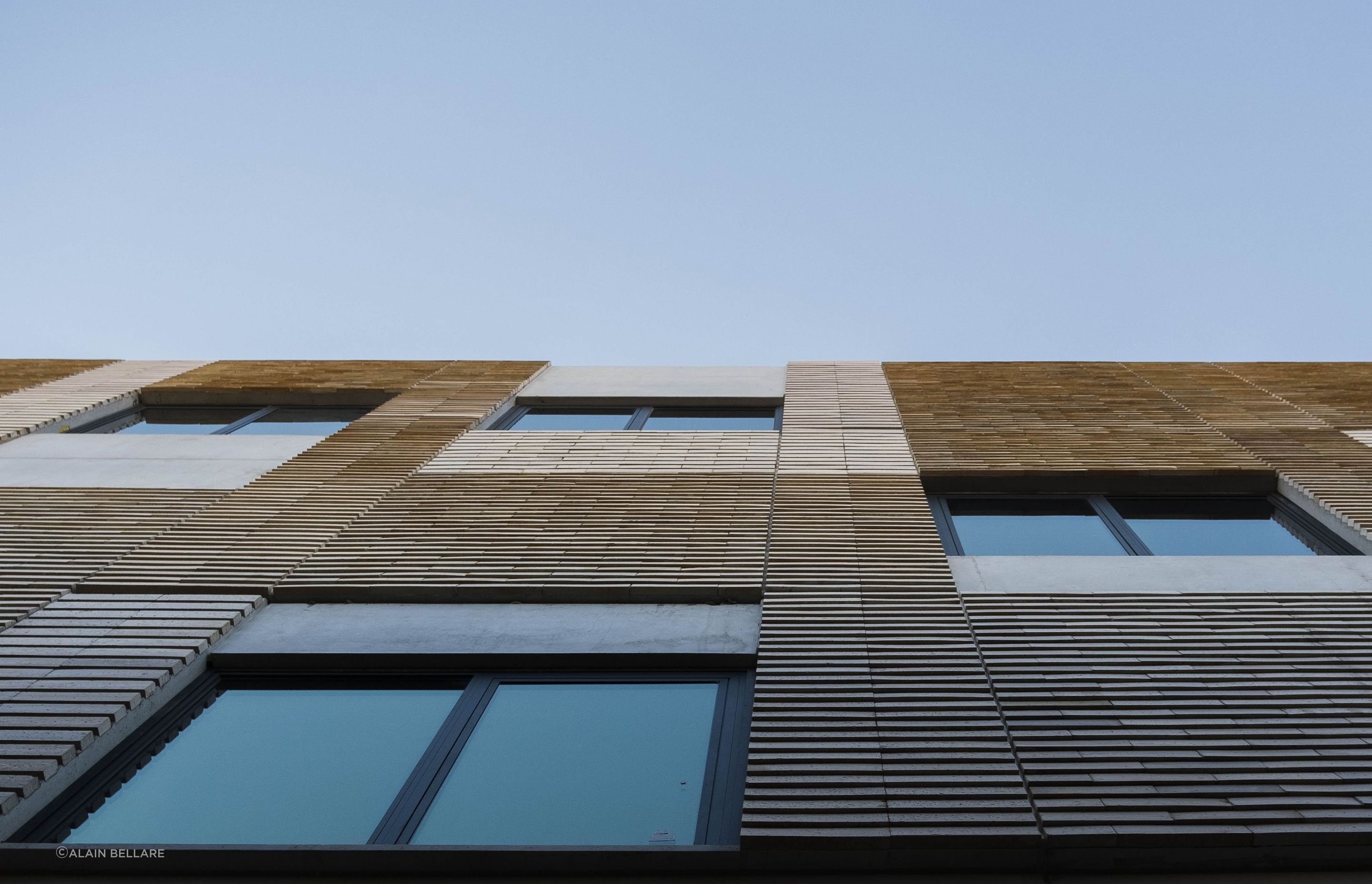
Fusing a traditional building material with innovative technology to create eye-catching, custom designs
Paying homage to its history, the Zero Gipps development in Collingwood – a contemporary six-storey workplace building designed around wellness and sustainability – has retained its original building at street level, with a limited palette of brick, concrete and glass, allowing the building to fit in with its surroundings.
Sitting above the original brickwork, locally-sourced Krause Imperial Emperor Bricks in Ghost Grey have been used to create a textural façade with an almost fabric-like effect.
“The architects wanted to create this texture in the wall to create a play of light and shadow. We flipped the bricks so that you see the top edge of the brick, which normally has mortar on top of it – we exposed a part of the brick that’s not normally seen, and have them sitting in this shiplap angle. We have different types of bonds running down the building to create subtle patterning, so you see stacked bricks versus staggered bricks,” says Robertson.
Robertson Façade Systems’ Brick Inlay was the answer in achieving this tactile and intriguing façade, allowing the bricks to sit on an angle thanks to custom-made moulds.
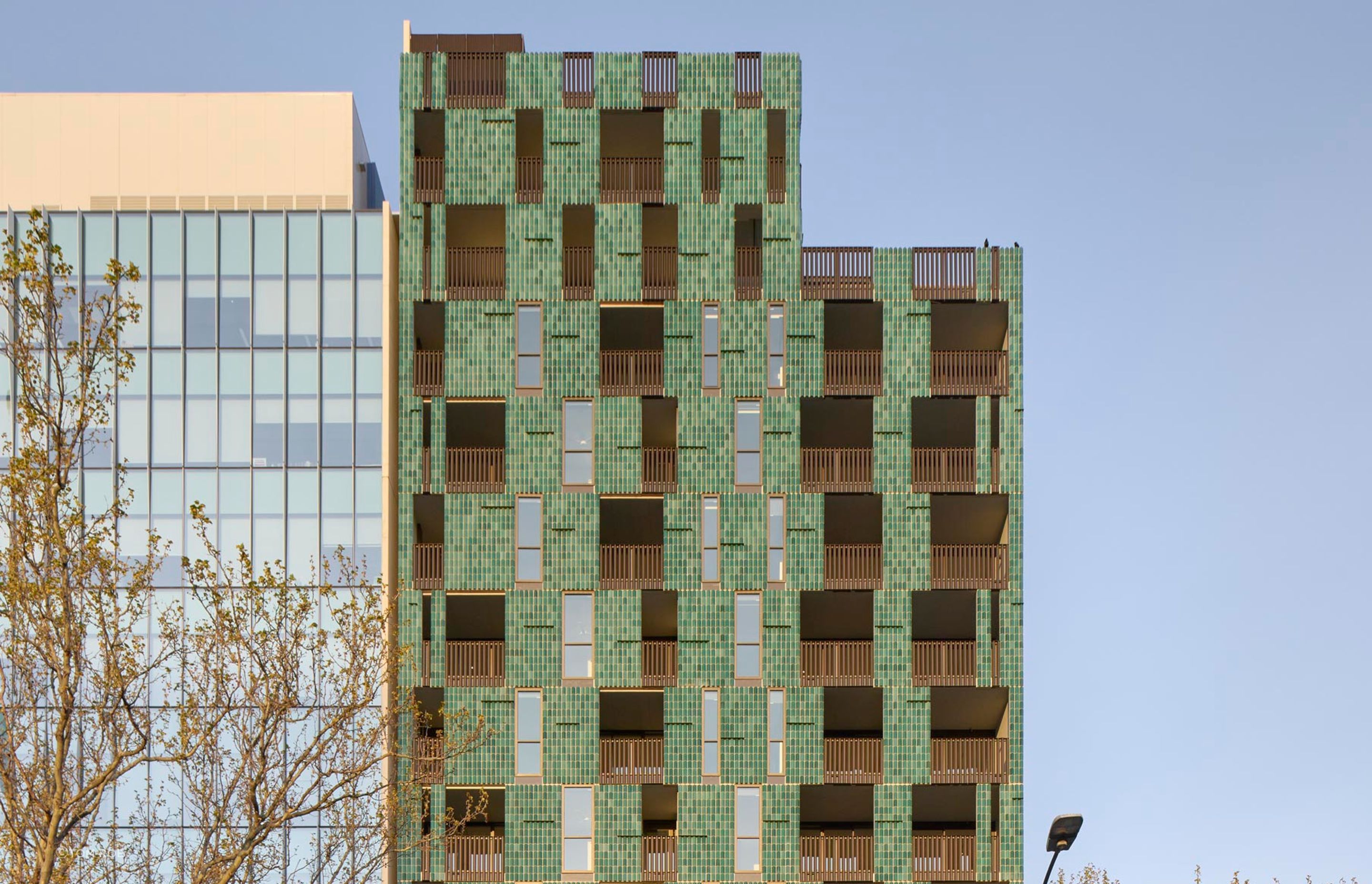
Read more - Brick size through the ages: Australia’s building block evolution
Inspired by the success of using Brick Inlay for Zero Gipps, SJB embraced the same system for its Tan Tat project on Elizabeth Street, Melbourne, to create a dialogue between heritage and contemporary.
Beautiful jade-coloured custom-glazed Rairies Montrieux brick tiles have been formatted in a way that references the heritage brick base, but rotated to define the new addition. The tiled panels are concertinaed as a nod to the client’s heritage and Chinese ornamental screens.
The key to successful projects such as these, says Robertson, is early engagement, communication and collaboration.
“Collaboration allows us to achieve the best results, and that’s one of the things that brings us joy – having that challenge in front of us and working together with architects to come up with an approach that works. Describe to us what you want to achieve, and let’s see whether we can come up with a solution; the earlier this is done, the less time that’s wasted and the faster the process.
“We are really happy to participate in the design stage to try to find solutions. We love working with the designers to allow their vision to be realised.”
Learn more about the Brick Inlay façade solution and get in touch with Robertson’s Building Products for your next project.