What is the ‘best’ way to make environmentally friendly furniture? A common consensus is that a reduction in carbon emissions is the most important goal, so furniture made with a minimal carbon footprint is the most environmentally friendly way. Additional viewpoints would point to practices resulting in minimal waste and pollution, using the lightest and fewer possible materials, making objects recyclable, and using recycled materials.
The truth is that all of these are correct. A reduction in carbon emissions is not just a goal, but also the result of methods, which grouped together form circular design principles. If circular is an attempt to design out waste, carbon emissions can usually be classed as waste. An estimate from the 2021 Circularity Gap Report claimed that a global circular economy could reduce global greenhouse gas emissions by as much as 39%.
However, the most recent Circularity Gap Report, released in early 2023, shows that the global economy is only 7.2% circular, down from 8.6% in 2020, and 9.1% in 2018. This is a worrying trend and one that will be hard to divert. True, our population is increasing, but so too is our general consumption. One of the key findings from the report is that material use per person has risen X1.7 compared to 1970. For industries such as furniture, we can work to use fewer materials, but equally important is choosing the right materials, especially recycling waste.
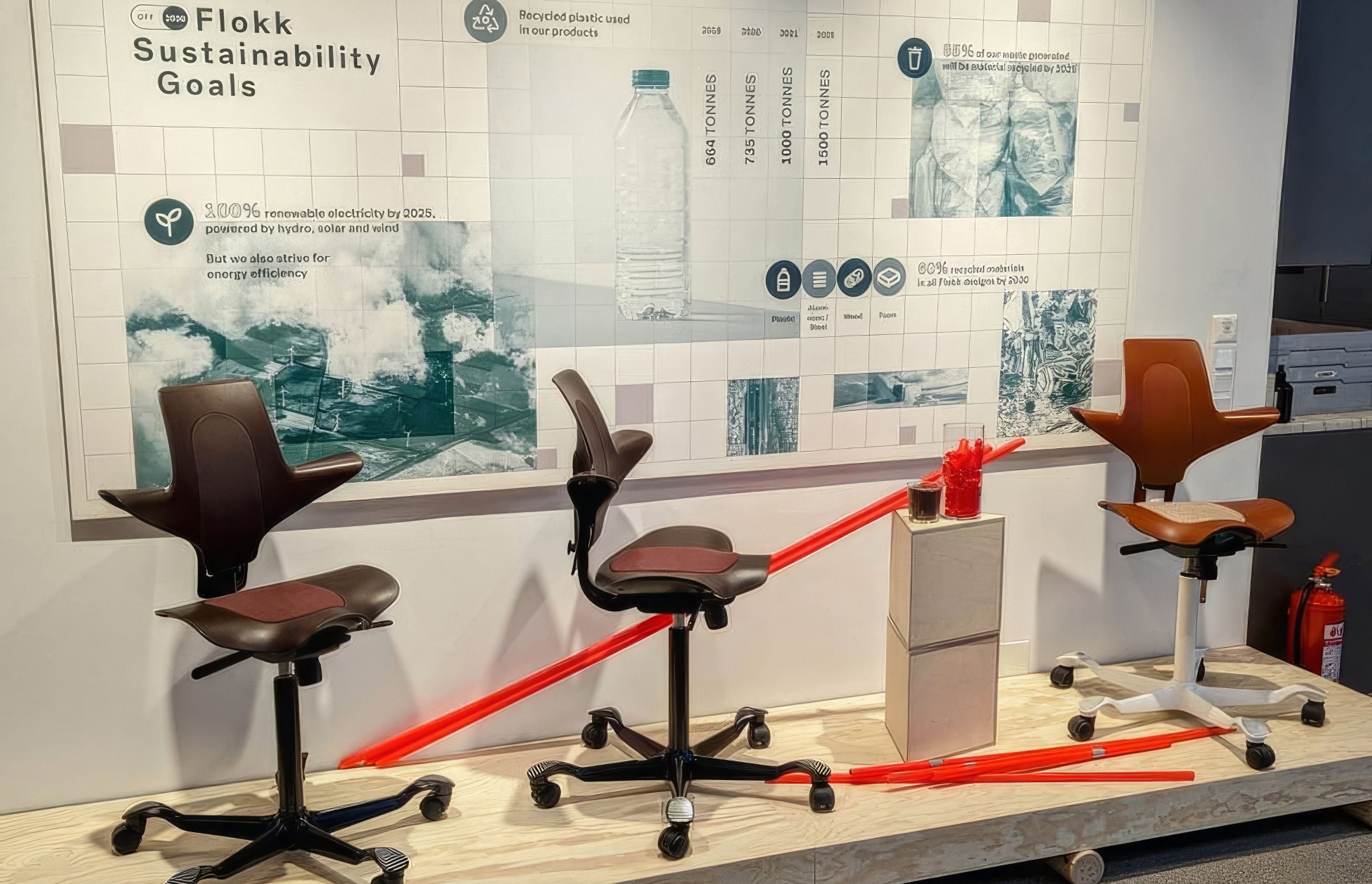
REVO – ENDLESSLY RECYCLABLE
Pearson Lloyd is a design studio that has spent 25 years designing products always with circularity in mind. During Stockholm Design Week, Founders Luke Pearson and Tom Lloyd presented the thinking behind Revo, their latest design for Flokk brand Profim. A stylish collection of sofas, benches, screens, and stools in softly contoured organic shapes, the design of Revo is rooted in circularity.
When it came to materials, the decision was made to not use plywood, but rather recycled expanded polypropylene (REPP). The move from wood to plastic may appear to be a step in the wrong direction, but the sheer abundance of plastic waste and the non-circularity of plywood makes it a more attractive proposition.
Luke Pearson “Replacing the plywood base structure with REPP maximises the potential reuse of the base materials. Plywood has no circularity. REPP, which is already in its second life, can be fully remoulded for a third, a fourth, ad infinitum.”
The REPP also drastically reduces the weight, by up to 40%. This makes it a more dynamic piece of furniture in the office, but also reduces costs, both financially and environmentally, when it comes to transport. In fact, by choosing recycled materials, the CO2e emissions of production are less when compared to plywood, and the materials are then available for recycling once again.
The design of the product also allows for easy disassembly. The covers are removable, making them easy to clean and replace, and nothing is glued together. 74% of the materials used to make Revo are recyclable – compared to 5% in the equivalent wood structure. In addition, because the REPP is already recycled – representing 90% of the total product volume – minimal new materials are required to build the collection.
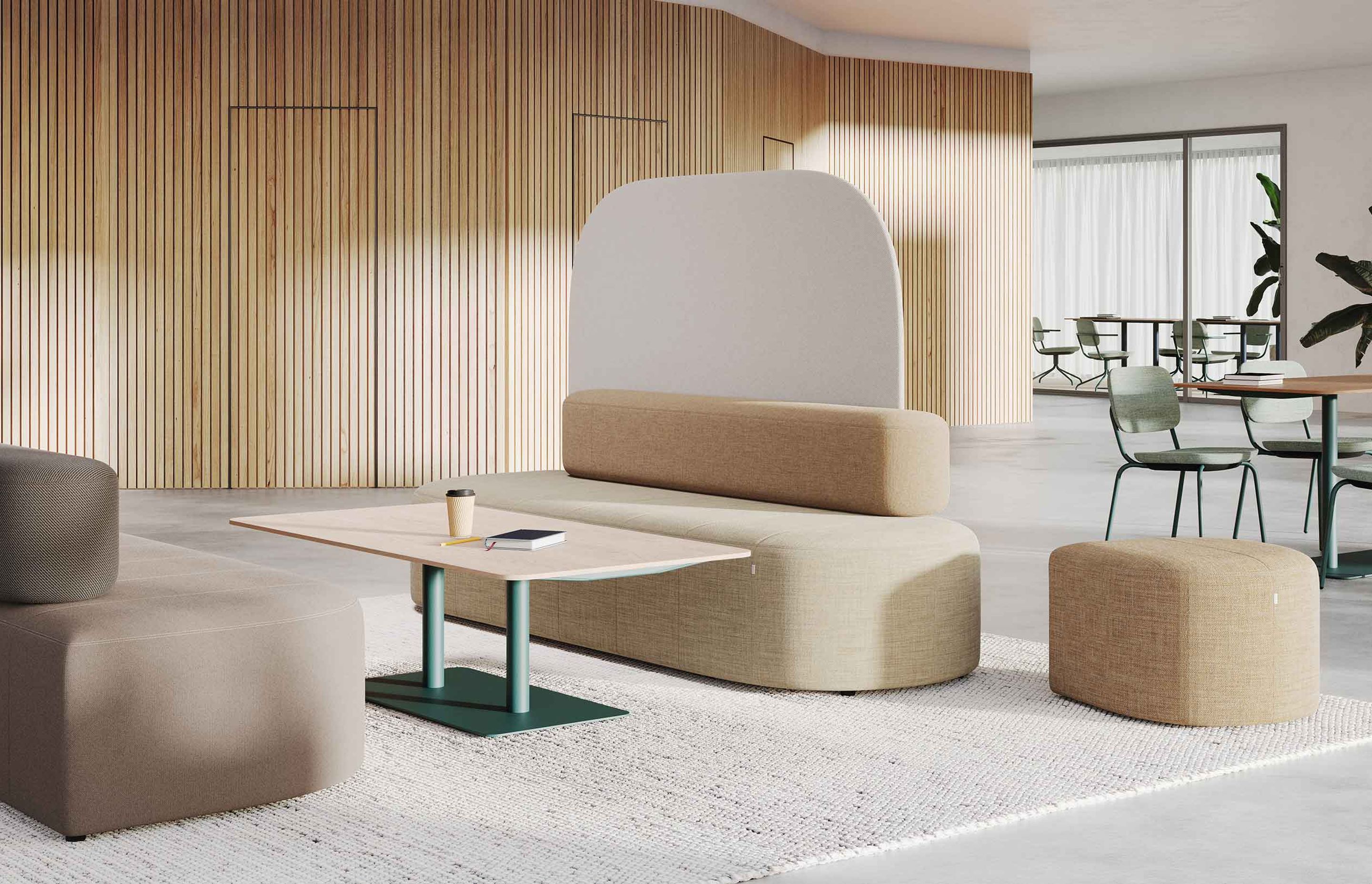
FINANCIALLY VIABLE WASTE STREAMS
Circular design is an attractive end to the means. Through circular design, we can reduce carbon emissions, reduce virgin material consumption and reduce the amount of waste accumulating on the planet. One of the main blockages is financial incentives. It is historically cheaper to use raw materials than to process waste materials for reuse.
This is where the power of industrialised processes can be used for good. Also speaking at the showroom event was Christian Lodgaard, SVP Flokk Design, who shared his experiences in bringing a chair made using recycled snow plough markers to market. What at first appeared to be a limited edition run soon became a full-scale product thanks to the collaboration with various stakeholders, making the material much more financially viable, and attractive in both cost and environmental credentials. The addition of the snow plough sticks adds another waste stream to Flokk's current use of 1328 tonnes of recycled plastics (2021) in production.
"Also in this respect, when transitioning to a low/no carbon economy, good design and industrial approaches offer scalability." says Christian, continuing; "The outcome will be impacts of sizes that would be unheard of - if one confined e.g. to craftmanship type production."
At the launch of the Revo, recycled plastic comprised 25% of the total plastic content. Already the figure has passed 30% and the goal is to go higher than 75%. This process is making use of the materials available locally, thus incentivizing the scale-up of proper waste handling in that part of Europe. The alternative would have been to transport waste across the continent, which is not a sustainable method.
By sharing these experiences the hope is to inspire others to work together to create these material streams. In addition, with the current global situation with rising energy and material prices, waste materials - of which there are millions of metric tonnes - are a gold mine waiting to be exploited, this time for the good of the planet.
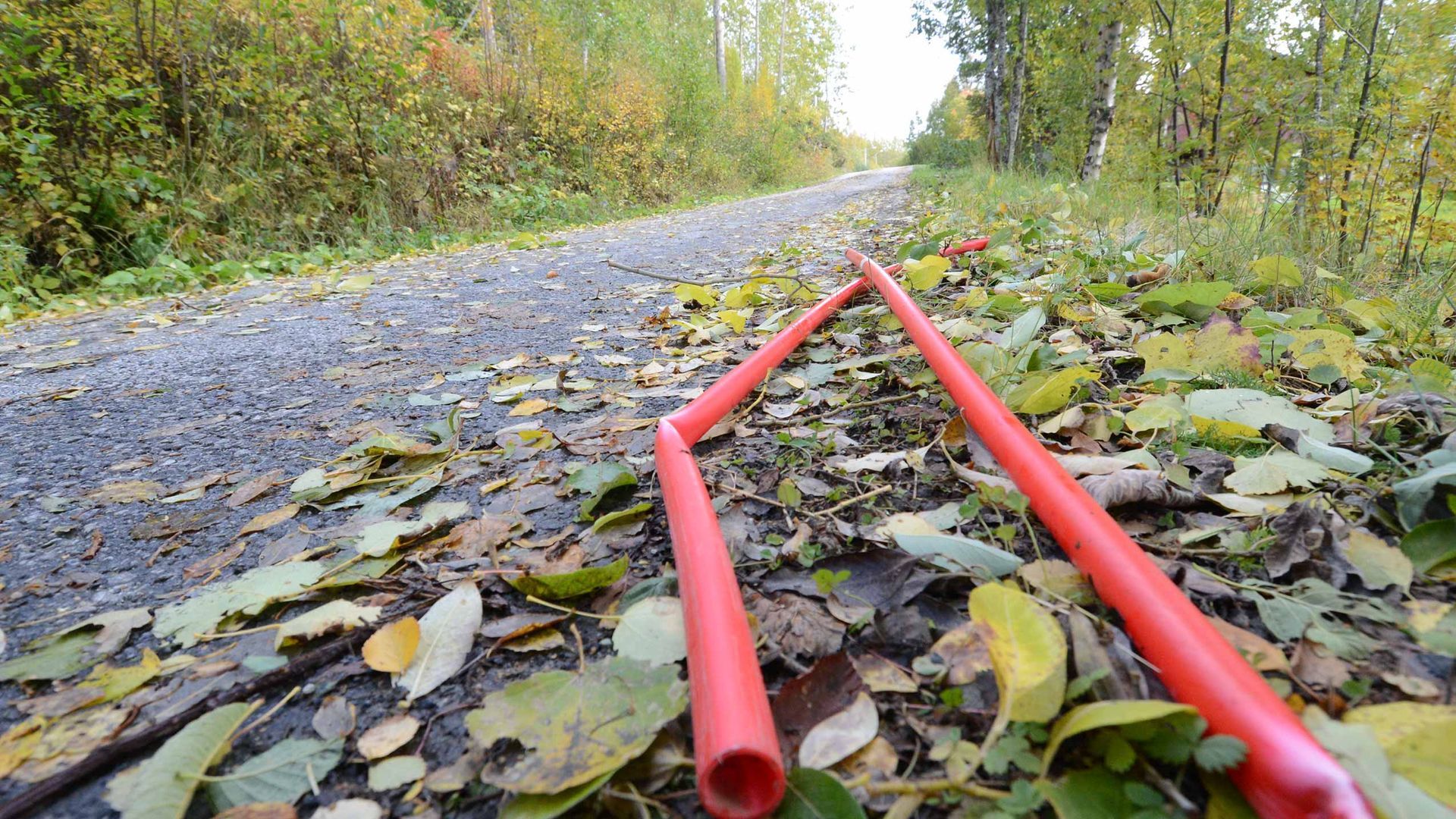