Why timber treatment levels are essential to understand in New Zealand
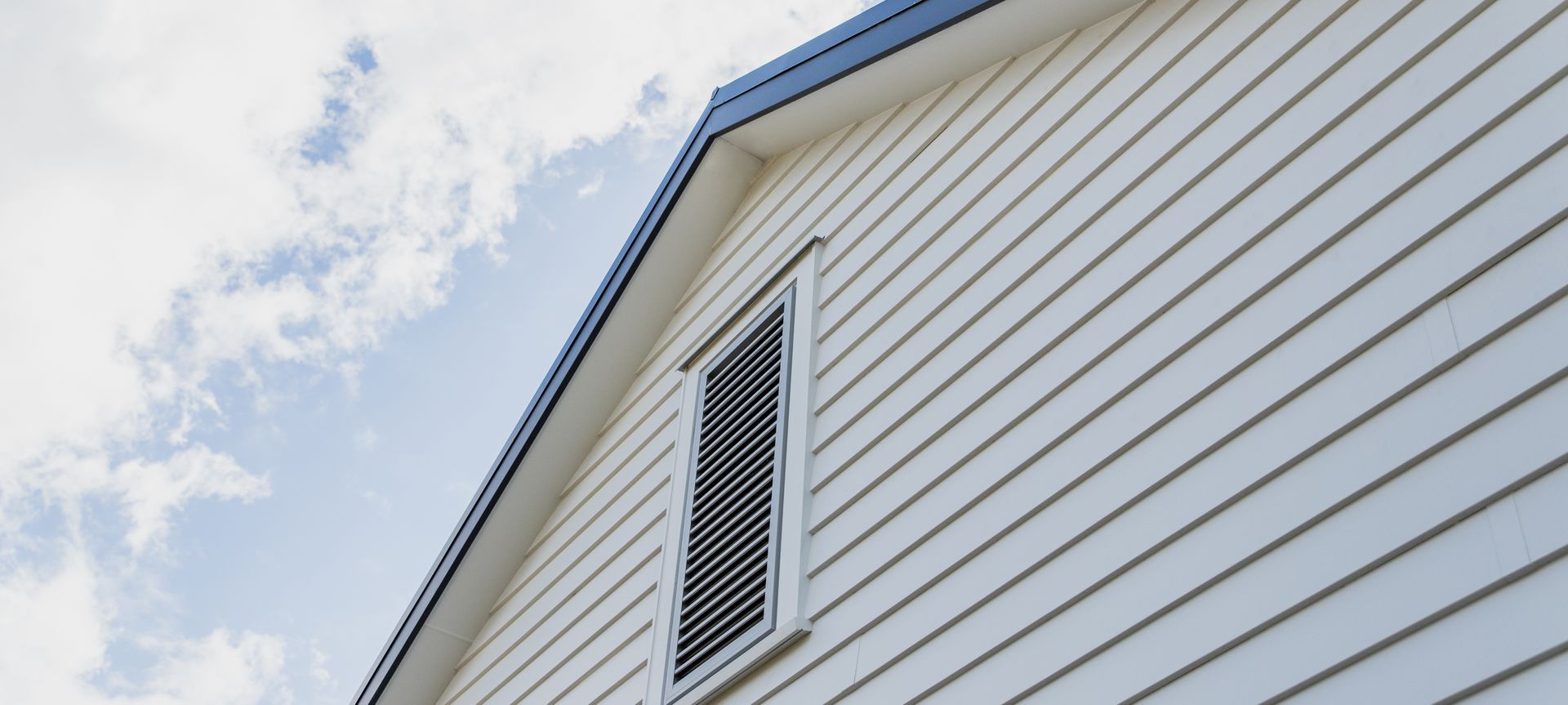
New Zealand's geographical location and topography shape a dynamic weather environment affected by cold fronts, warm fronts, low-pressure systems, and tropical cyclones. As such, it's imperative the building materials New Zealanders use are resilient in all weather conditions, from torrential rain to scorching sun. For exterior applications, timber treatment is essential to understand.
Since 1988, family-owned South Pacific Timber, which specialises in cladding, decking, mouldings and flooring, has refined its expertise in this area. For the last 20 years, they've partnered with leading New Zealand timber manufacturer KLC to offer environmentally friendly, durable, treated timber for exterior applications.
For several years, South Pacific Timber had experienced issues with dissatisfied customers using H3.1 treated timber for exterior timber use. The game-changing moment for the business dawned 15 years ago, as they were confronted with the monumental importance of timber treatment levels in New Zealand climates. Long-time customers and fraternal owners of Gracewood Construction, Ross and Paul Grace, arrived at South Pacific Timber's yard with a rotten piece of pine.
"I smiled at Ross and said, 'I bet you didn't get that from us!'" shares Andrew Vincent, Director at South Pacific Timber. "He said, 'Invoice 20463. 18 months ago.'
"I punched it into the computer, and sure enough, we'd supplied some H3.1 timber to the experienced Gracewood Construction. I said, 'Ross, I'm very embarrassed, and I'm very sorry. We need to replace this'."
The interaction was not the first of its kind caused by the failure of H3.1 treated timber, but it was the last for South Pacific Timber. It prompted a bold, customer-first decision: stop selling H3.1 treated timber. Contrary to many businesses' decisions, this wasn't motivated by sales growth. It was simply the right thing to do.
What is timber treatment?
Timber treatment refers to the process of chemically preserving timber to protect it from decay. The causes of decay are numerous and unavoidable. Prolonged exposure to rain and humidity, as well as insects and fungi, threaten the structural integrity of the wood, so timber treatment is essential to ensure its longevity.
The situational application of the timber is the primary determiner of the level of treatment it requires. In short, the higher the treatment level, the more resilient the timber.
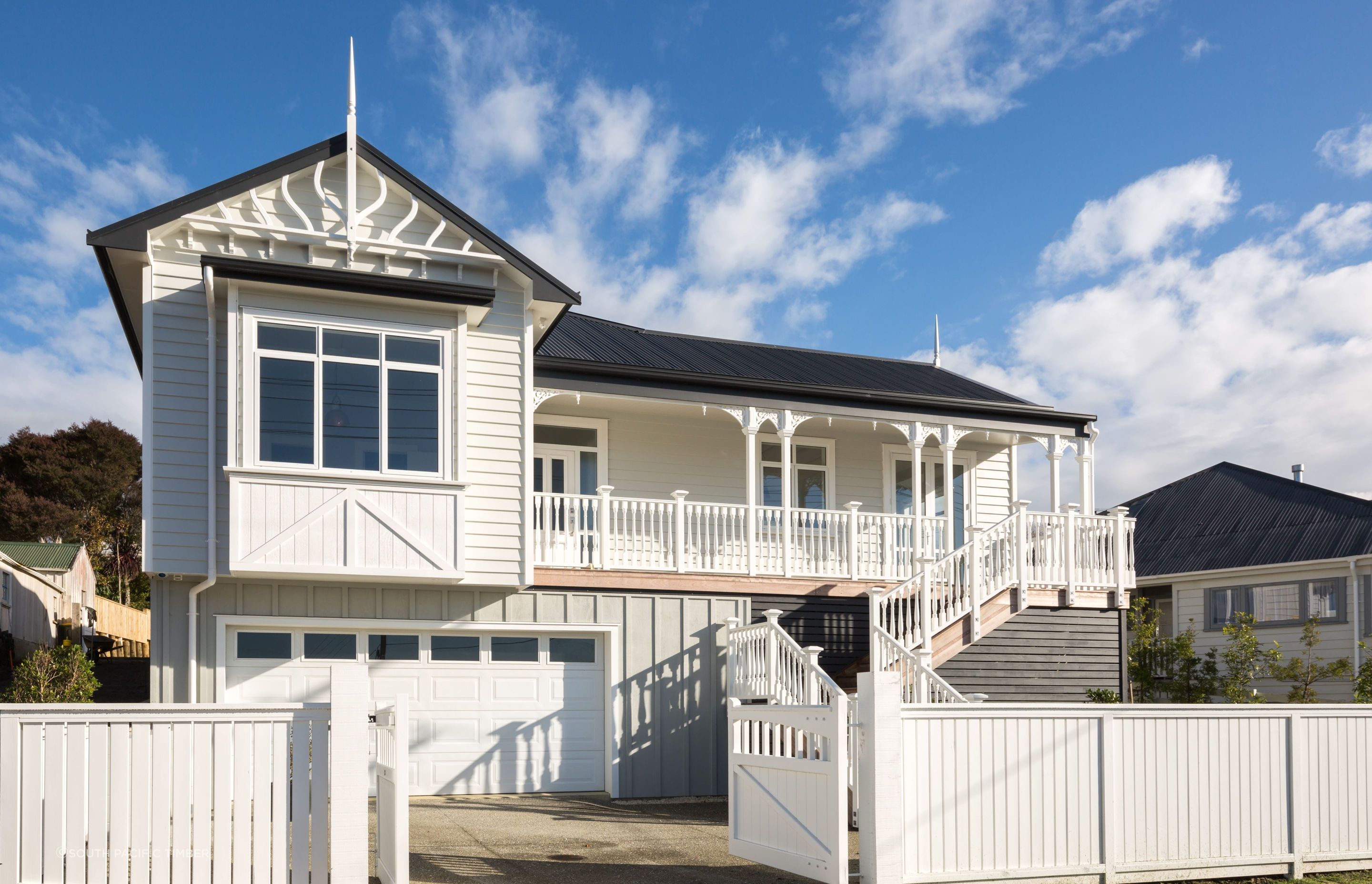
How is timber treated?
In New Zealand, several different products are approved to treat timber for outdoor use, including copper chrome arsenate (CCA), alkaline copper quaternary (ACQ), and MicroPro (MCA). The first and oldest, CCA, uses copper, chromium, and arsenic and, therefore, comes with some perceived environmental and health risks that have restricted its use in many countries.
ACQ is a copper-based alternative to CCA. Whilst more environmentally friendly than its arsenic-infused counterpart, ACQ-treated timber still contains high levels of copper, which can contaminate the environment and increase the risk of corrosion to fasteners.
MicroPro is an advanced, micronised copper azole treatment system applied with pressure to the wood.
"With the MicroPro treatment, it's total penetration of the fibre," shares Trevor Attwood, New Zealand Sales Manager at KLC.
KLC's MicroPro treatment for Generation 2 H3.2 treated timber uses finger-jointed timber blanks of sustainably sourced, New Zealand-grown radiata pine and applies micronised copper azole preservative at a high pressure.
The finger-jointed blanks are then kiln-dried before being moulded to their profile. The profiles come in 6.3 metre-long lengths and are primed with a two-coat alkyd priming system to enhance water resistance.
KLC's system for Generation 2 H3.2 treated timber has four environmental certifications awarded by Scientific Certification Systems, Greenguard Environmental Institute, two from Global GreenTag, and comes with an impressive 50-year warranty.
What are the treatment levels?
In New Zealand, timber is given a hazard class rating to ensure it adheres to the Building Code's clause 'B2 Durability', which details the minimum durability requirements for building materials based on their location and function. The rating system ranges from hazard classes 1 (H1) to 6 (H6).
Hazard class 1 is split into two categories: H1.1 and H1.2. H1.1 is no longer produced, while H1.2 is for interior framing. H2 is intended for interior dry applications where termites are a potential risk and is specified for use in Australia only.
Hazard class 3 treated timber is intended for exterior above-ground applications, consisting of two categories: H3.1 and H3.2. H3.1 is used in free-draining situations where timber will be exposed to the weather but not ground contact, while H3.2 has enhanced protection and is used for timber at risk of water entrapment. A key element of H3.1 in an exterior timber cladding application is that it relies wholly on a robust paint system.
H4, H5, and H6 are higher hazard classes with higher concentrations of preservatives. H4 is used for non-structural ground contact, such as fence posts, whereas H5 is intended for structural ground contact in critical applications, such as house piles. H6 is specified for seawater immersion.
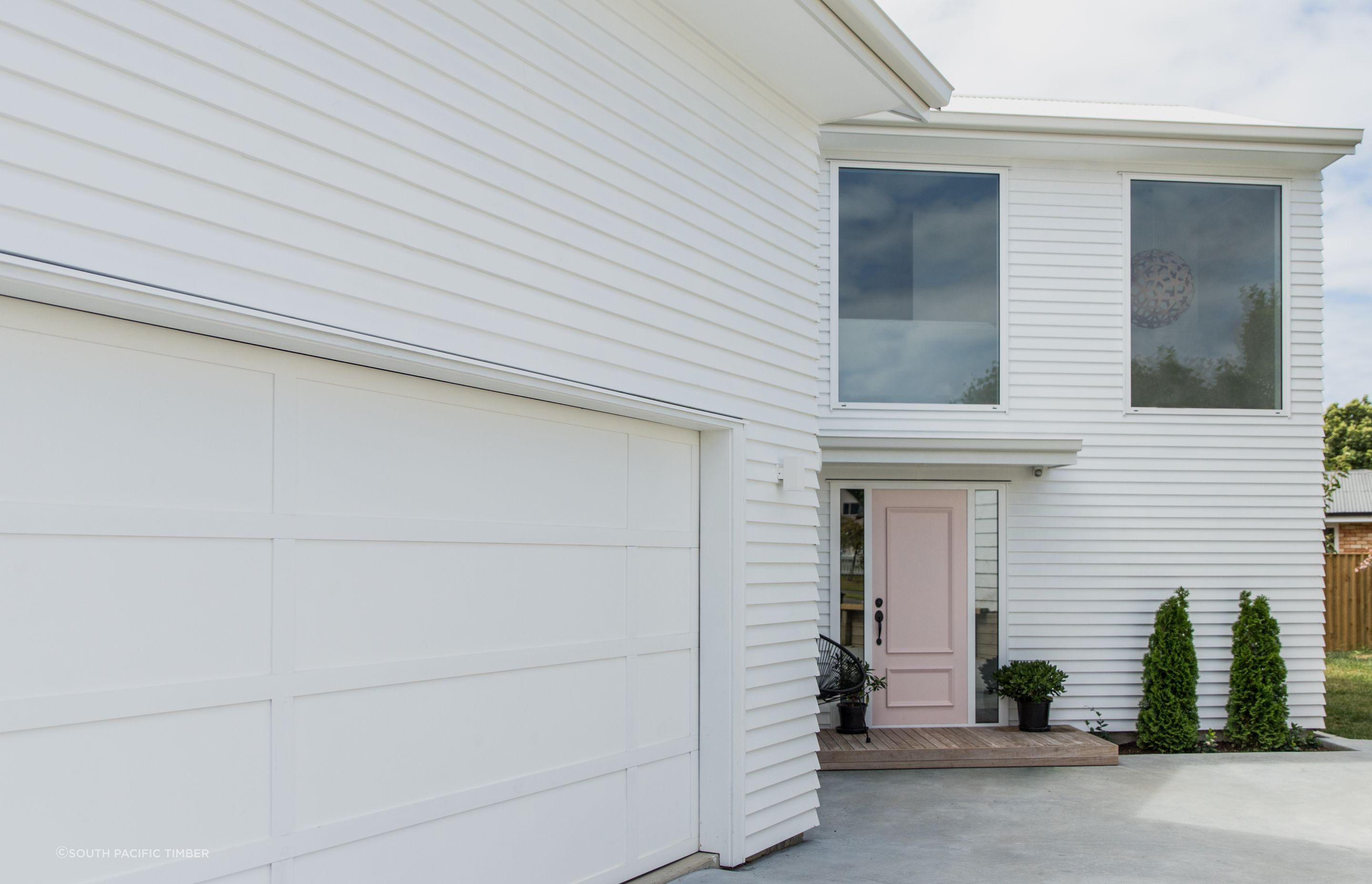
The essential differentiation: H3.1 vs H3.2 treated timber
Currently, H3.1 treated timber is the minimum acceptable standard for weatherboard applications in New Zealand. It has a significantly lower expected minimum service life of 15 years compared to a weatherboard treated to H3.2.
"Their application is the same, exterior cladding. But with H3.2, you've got the assurance that the substrate has been treated with a timber treatment that will last 50 years," says Trevor.
H3.1 is treated after the timber is machined by flooding a chamber with a solvent-based preservative under low pressures. By contrast, H3.2 is treated at high pressure with a water-based MCA preservative in a rough-sawn state, re-dried, and machined. While both systems meet the treatment standards, the H3.2 product does not rely on maintaining a paint coating to achieve lasting durability.
"In New Zealand, we have so much rain, we've got to have timber that has treatment right through the wood. Otherwise, it rots," Andrew adds. "Unless it is carefully installed and maintained, H3.1 product can actually rot from the inside out, which can lead to horrific failures. The outside can seem quite solid, but then you poke a little hole in, and it's all rotten."
"We've come to find that the H3.2 process would be used more if the New Zealand building industry had the resources to do it. Unfortunately, it takes years to make this change."
Assessing the economic viability of timber based on the treatment level
Any construction project should involve an assessment of its economic viability. This is informed by financial, environmental, and social analysis of the project's components.
In the context of materials, H3.2 treated timber has a higher upfront cost than lower-grade treated timber, such as H3.1. However, it benefits from an extended lifespan and is less demanding of maintenance, for instance, repainting or replacing. From a financial perspective, this results in long-term cost savings.
KLC supplies South Pacific Timber with Generation 2 H3.2 treated timber, which three separate environmental awarding bodies have recognised. The MicroPro treatment's micronised copper preservative presents fewer ecological risks, while the high-pressure process provides comprehensive protection to the timber's core. For areas with high moisture levels, frequent rain, or termite activity, the increased protection provided by H3.2 treated timber makes it an informed choice.
While H3.2 treated timber may have a higher initial cost, its extended lifespan, reduced maintenance requirements, and lower long-term replacement costs make it economically viable for many applications, especially in regions with harsh environmental conditions.
South Pacific Timber stands out as an independent business for its 'one-stop-shop' approach. Andrew always aims to have three months' supply to sell directly to builders and other merchants.
"We're an independent carrying huge amounts of stock to be able to support our small retail market and our wholesale market. We deal with people at all levels to support them and share these high-quality products," Andrew shares.
As many builders are becoming aware of the increasing risk and contingent liability they carry when undertaking a building project, the small premium an H3.2 treated weatherboard commands compared to an H3.1 weatherboard seems a highly justified investment.
Learn more about South Pacific Timber and their H3.2 cladding solutions