A timber company’s bold move to a sprawling two hectare site
Written by
28 June 2022
•
4 min read
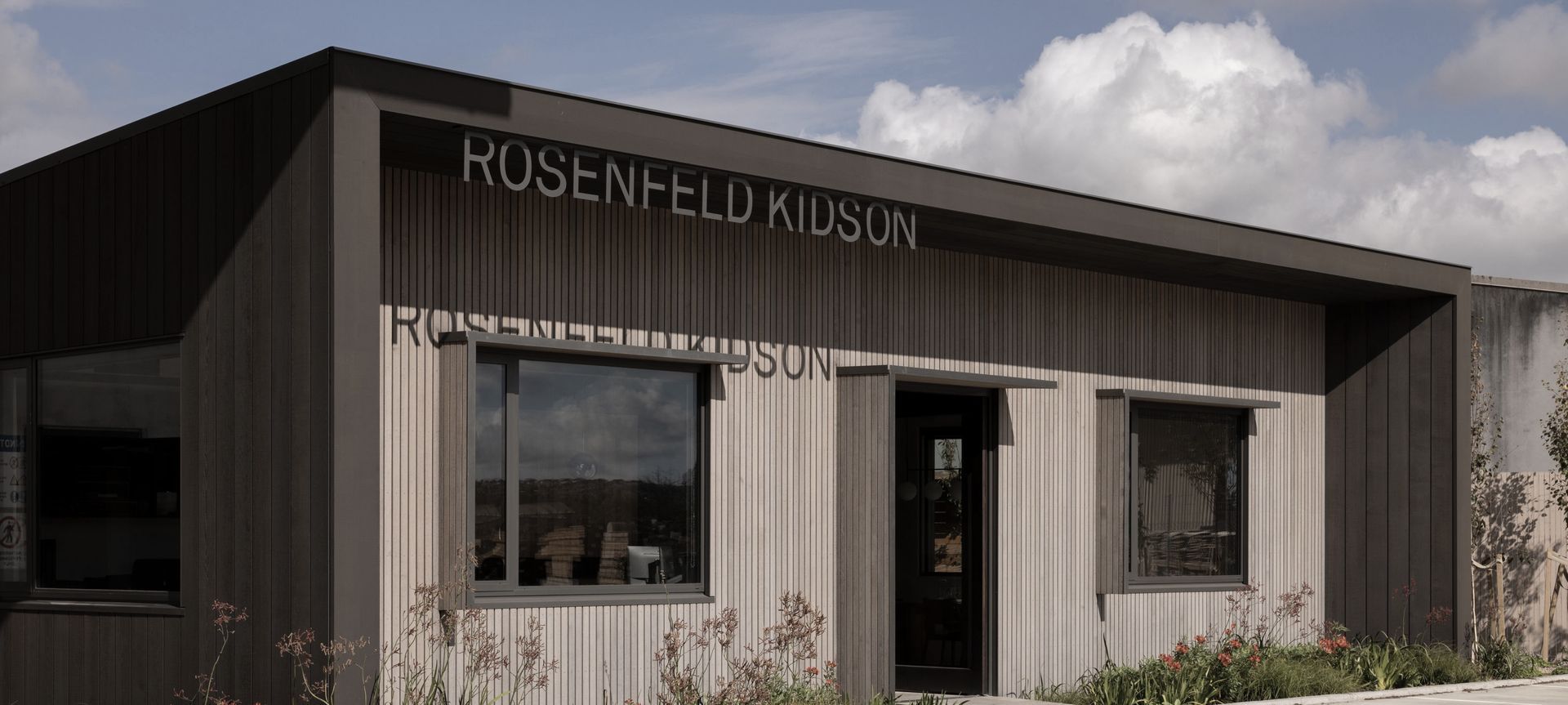
For companies that have been around for a long time, moving around is a common occurrence.
Celebrating the 90th anniversary of its incorporation three years ago, specialist timber company Rosenfeld Kidson is no exception: it’s continually evolved throughout the decades as the industry and country around it changed — including a general expansion of its business, and the opening of multiple new locations and warehouses.
From the 1930s until the mid 1990s, the company operated from the Strand in Parnell. Then, in 1996, it moved to a purpose-built premises in Mt Wellington, complete with a drive-through warehouse and 3000sqm of covered storage.
Last year, the company made its second big move: it commissioned a brand new manufacturing site in Papakura, where it imports timber, houses its state-of-the-art processing equipment, and hosts its dispatch operation — shifting most of these operations from Mt Wellington to Papakura.
The sprawling 2.2 hectare site also includes a small office, which doubles as a showroom to feature Rosenfeld Kidson’s products in a variety of end uses.
Mark Liggins, the managing director of Rosenfeld Kidson, says the move is symptomatic of the company’s trajectory in the last few years, and resulted from it outgrowing the Mt Wellington facility.
“It’s allowed us to have a lot more space,” says Mark. “We now have an additional 4000sqm shed and 7000sqm of concrete. What this means is that we can have all our operations on a single site.”
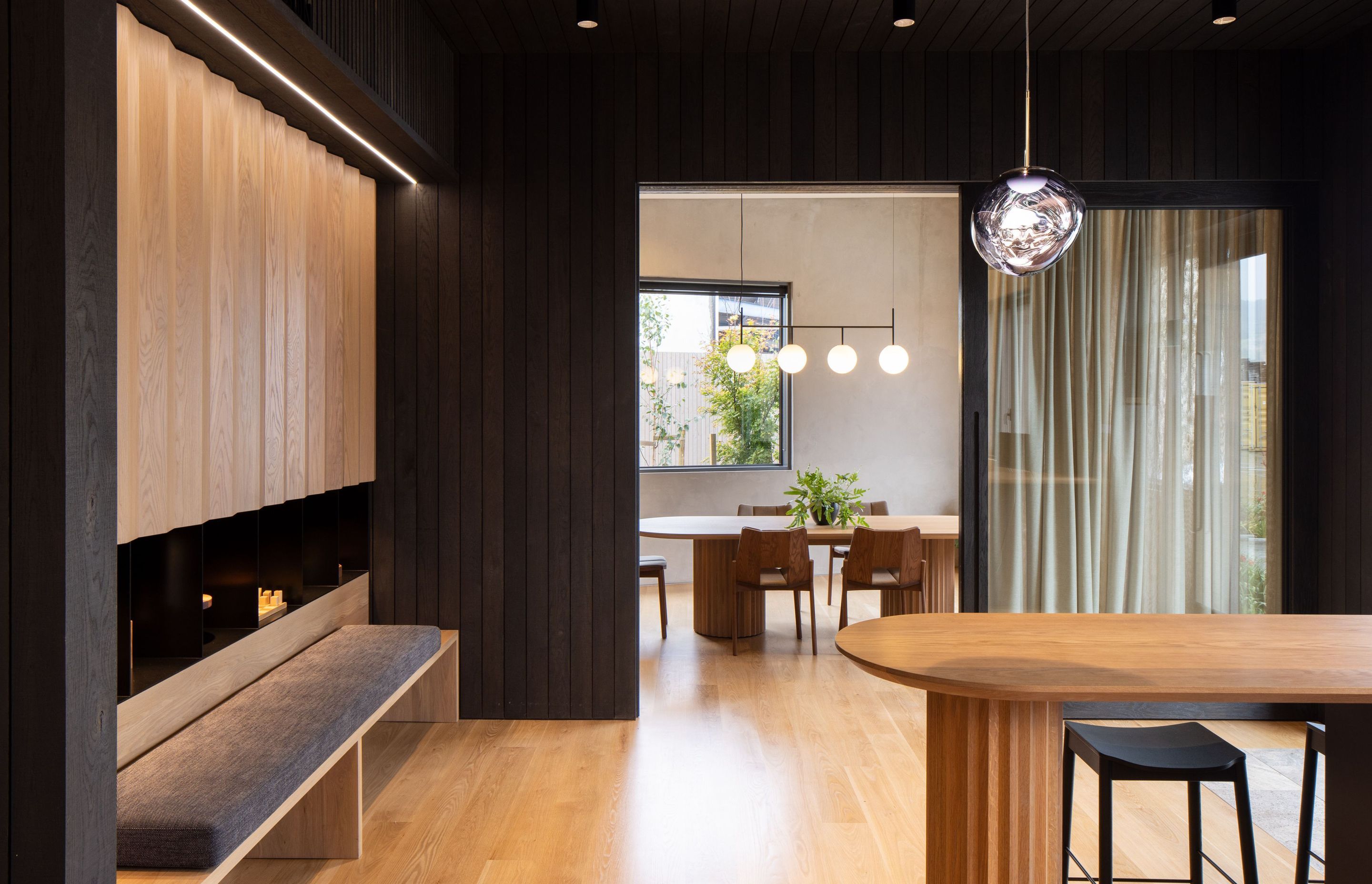
An opportunity for growth and elevated productivity
A significant factor in the decision to move to a larger space was the unpredictability and volatility of the global supply chain. Recently, Mark says, there has been reduced availability of timber and fewer ships coming here than usual — and when they do come, a lot of containers arrive simultaneously. This meant the company had to re-visit its logistical operations, procurement strategy and exposure to global supply chains.
“In Mt Wellington this presented a challenge — but on our new site, logistics are easier, and we can efficiently handle multiple containers at once,” he says. “An excess of space also means that we can have more stock and don’t have any problems accessing dry timber now, enabling the company to be more agile, supporting our innovative and creative business model.”
In addition to receipt of containers for de-vanning and inspection, it’s also enabled the company to enhance the efficiency of other integral processes – like timber grading and drying, order selection, timber profiling, coating and dispatch.
The entire timber operations and then production process can be done quickly and efficiently in the ‘machine shop’, which takes up half of the entire warehouse. This is where, once the orders have been selected, the timber is recut through a bandsaw, after which it goes through a planer to profile it. Following that, it gets pre-coated — after which it will be packaged and dispatched.
The premium timbers are then utilised in a variety of finishing timber applications — including exterior cladding, solid timber flooring, wall and ceiling panelling, exterior decking and joinery.
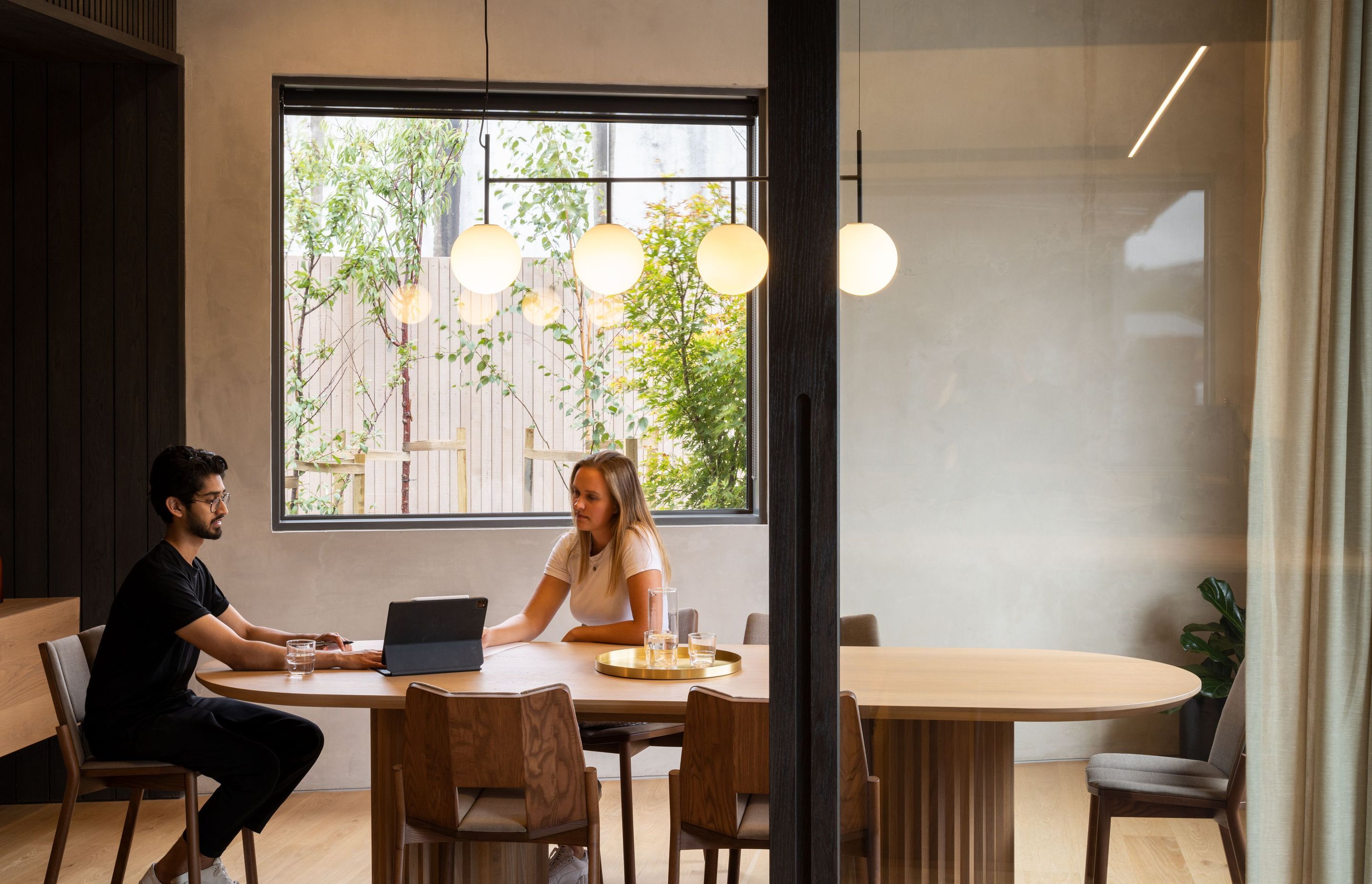
Showcasing the best in timber products
Part of this can be seen at the new showroom on the Papakura site. “The aim of this showroom is to give an impression of the essence of what we do,” says Mark. “We display our cedar cladding, in this case, as a 28mm thick weatherboard; there’s our recessed window flashing system, which allows traditional aluminium joinery to be set back from the façade; as well as custom fascia and panelling.
Rosenfeld Kidson enlisted the expertise of SGA Architects and Steve Joynes — a top residential architectural builder to create and execute some impressive junction details, again showcasing what the use of these timbers can achieve.
“For the interior, there’s multiple timber uses for interior joinery, solid timber flooring, wall panelling and furniture — all in American white oak, which is a very beautiful and great performing timber in these areas.”
There is also a ‘courtyard area’ connected to the showroom, which features some of Rosenfeld Kidson’s exterior hardwoods used for exterior furniture and decking.
And in addition to all the extra space and added efficiency the site offers, Mark says it also presents a great opportunity for specifiers, architects, builders and other professionals to visit and understand the entire process of imported timber handling, manufacturing and installation.
“It finished construction at the end of last year, and already it’s been a huge success,” says Mark.
Learn more about Rosenfeld Kidson, its new site and its products and offerings.