Adding value to surfaces with cutting edge UV technology
Written by
03 November 2022
•
4 min read
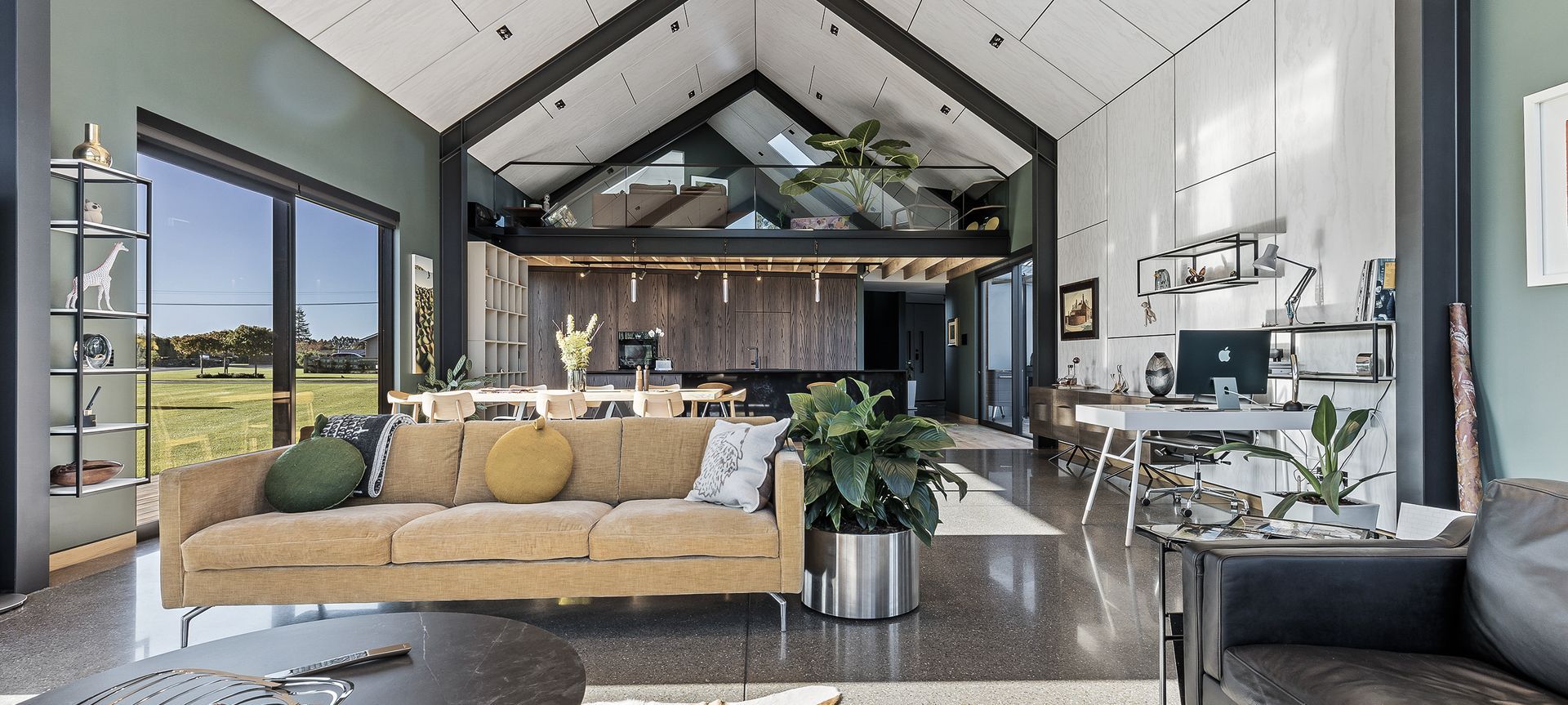
Prior to the Second World War, AJ Bates was one of the top car spray painters in New Zealand. He often did the work for the automobiles of the wealthiest people in the country, painting many high-end cars in his time.
While creating bespoke automotive finishes for luxury cars and their very discerning owners, A.J Bates knew his knowledge and skills were transferable.
He began experimenting with paint technology to achieve glossy, durable finishes for building materials. Initially embraced by mid-century architects looking for innovative materials to help them make a design statement, a whole suite of high-performance durable wall and ceiling linings also began to evolve.
By the 1970s, his company, Bates Surfaces, was the coating power behind iconic products like Seratone ( then New Zealand Forest Products) and Hardie Glaze by James Hardie NZ. A.J had been joined by his son Robert Bates, and working together they delighted in constantly developing products to meet the needs of the New Zealand building market.
Newly trending colours, contemporary gloss levels and unique pattern ranges have featured in Hardie Glaze and Seratone products as they are developed, tested, and released by Bates Surfaces. The products are used in residential applications like bathrooms and kitchens, as well as commercial and industrial applications like manufacturing plants and healthcare.
As newly emerging paint technology offers resistance to mould, microbial activity and yellowing by the sun, Bates Surfaces makes these features part of its coatings range.
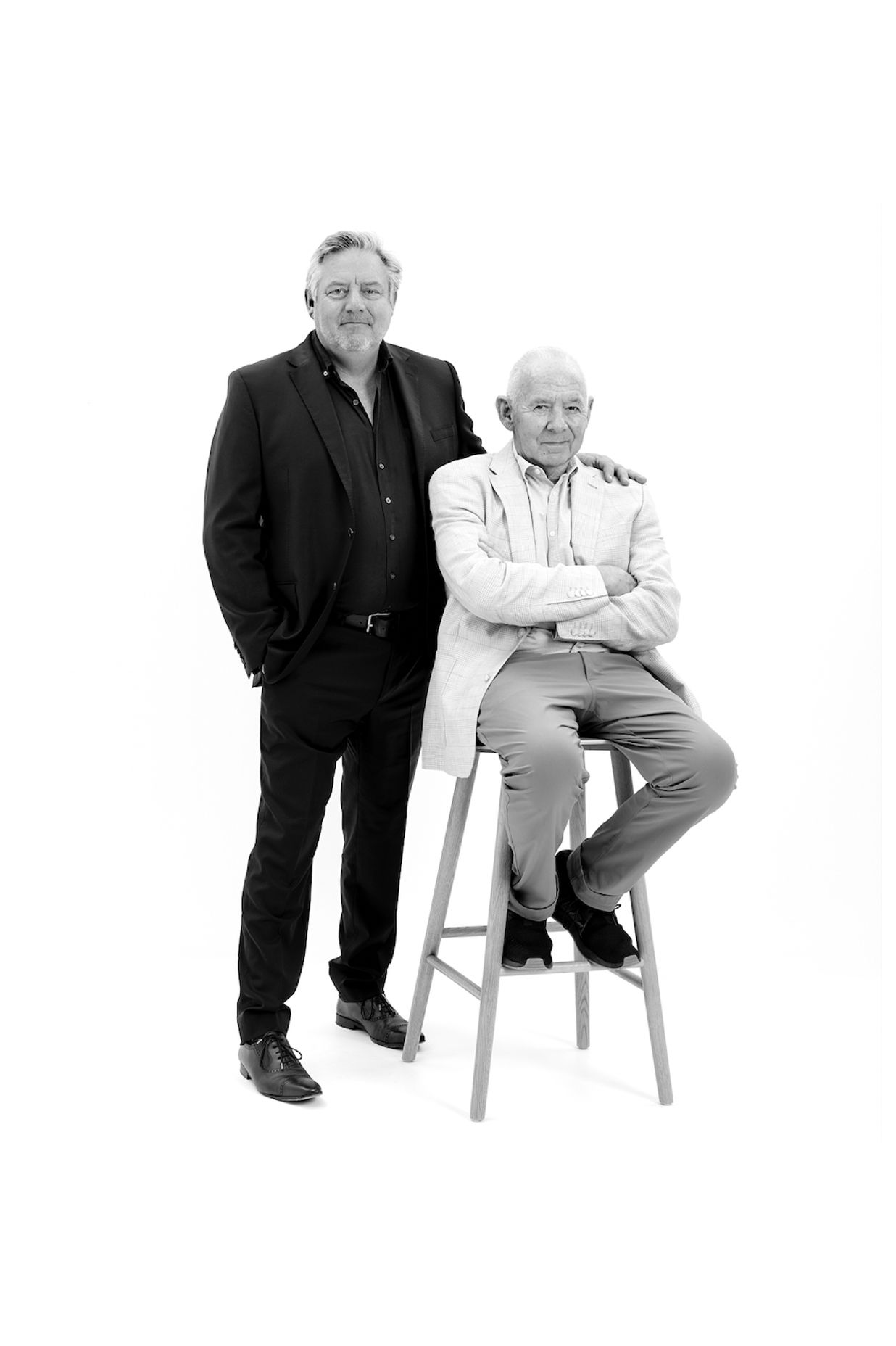
A versatile approach to technology
Bates Surfaces CEO Andre Bates says it's this innovation and continuous interest in developing new products that has ensured Bates Surfaces’ longevity. “Our most exciting project to date has been redesigning our whole process by embracing the latest Ultraviolet (UV) technology – which allows us to remove solvents and excess Volatile Organic Compounds (VOCs) from our manufacturing.
“During the 1990s, my father Robert championed this change and travelled overseas to research the best practices currently being used around the globe,” says Andre. “Robert then began to bring his research back to New Zealand shores – and this journey has formed the backbone of our offering ever since.”
Andre says the technology also bolstered the durability of the company's coatings, while also enhancing their aesthetic appeal.
“Having a better product with more effective quality control, that's much faster than more conventional ways of coating is increasing the capacity of our production lines,” he says. “We are proud to be much more sustainable with near zero VOCs, no solvents, and greater energy efficiency in our manufacturing.”
By 2010 Bates surfaces was ready to use UV coated systems and since 2016 this application has been used across all product ranges being manufactured at their factory in Penrose.
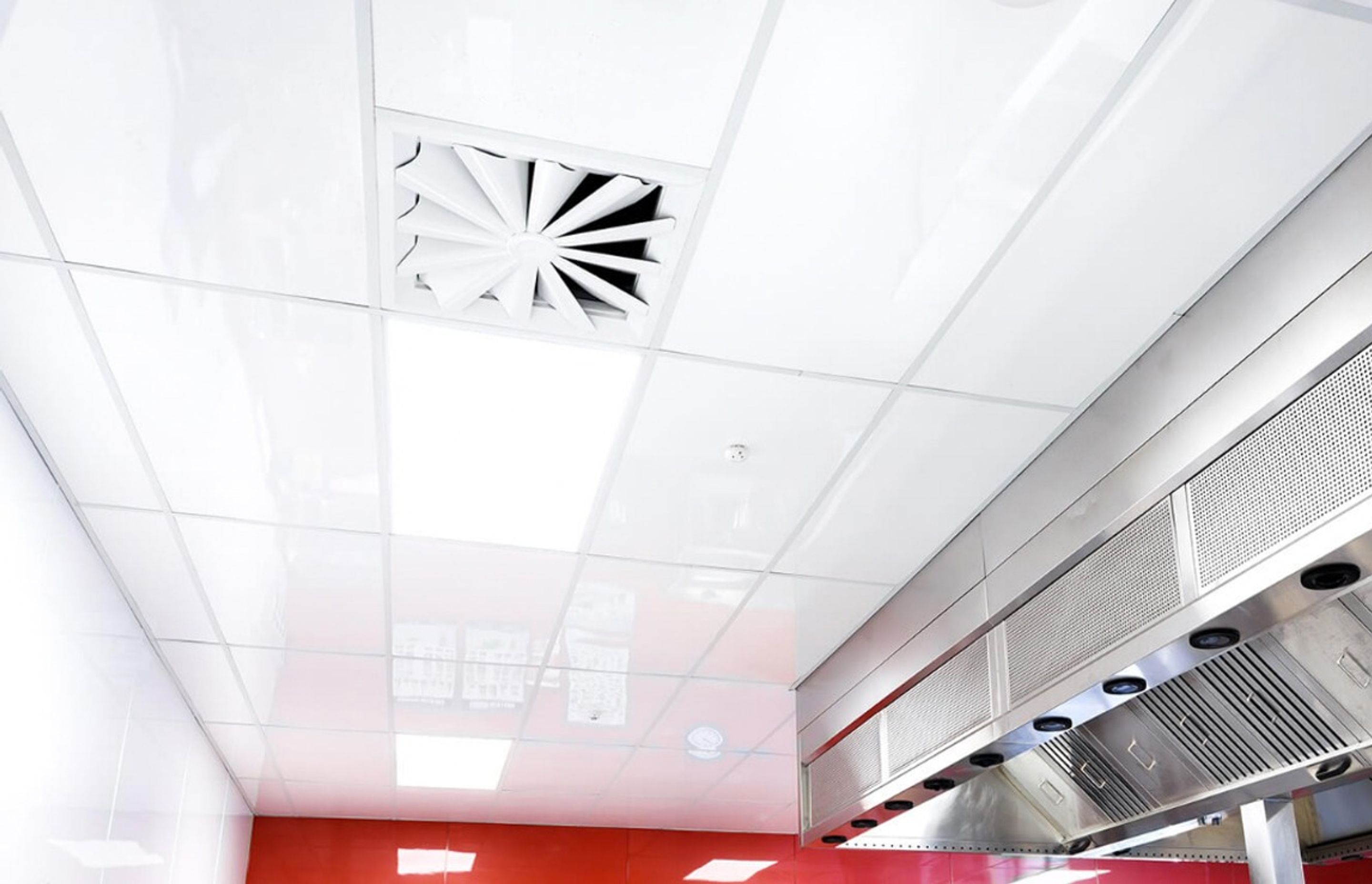
A diverse product line
Bates Surfaces takes both established and newly developed products and adds value for their manufacturers by offering UV coatings. The company works to transform the likes of raw fibre cement panels into pre-finished material products – working with manufacturers as they take these pre-finished products and make them part of their product ranges and systems.
FENTA
The new Bates product Fenta is a commercial ceiling tile product. It's a hard-wearing, pre-finished, washable ceiling tile with a high gloss or satin UV coated urethane based antimicrobial non-yellowing coating. It's ideal for healthcare, aged care or hospitality projects.
PLY PLAY
This prefinished UV-coated plywood is made from sustainably grown plantation pine, and is ideal for residential interiors. It can be installed straight to stud by one trade, and gives a natural timber finish but still has high resistance to sun-fading or yellowing.
PURE COAT
This high-end paint finish joinery panel is ideal for vertical applications such as drawers, cabinet doors, wall linings, and large feature panels. New colours and finishes will be released in early 2023.
The updates don't just stop at the products, though. Bates Surfaces has introduced new personnel with an aim to bring the company to the next level: Ben Hutter has come on board as the company's new business development manager. Ben has a history of collaborating with architects and designers on commercial and residential projects throughout New Zealand.
This multitude of benefits is emblematic of Bates Surfaces as a whole – embracing new shifts in technology and adapting them to ensure their products are the best they can be. It's this mindset that has created success as a company through the decades, Andre says.
“We're a third-generation family company and we're proud of it, and our intention is to continue far into the future.”
Learn more about Bates Surfaces and its products.
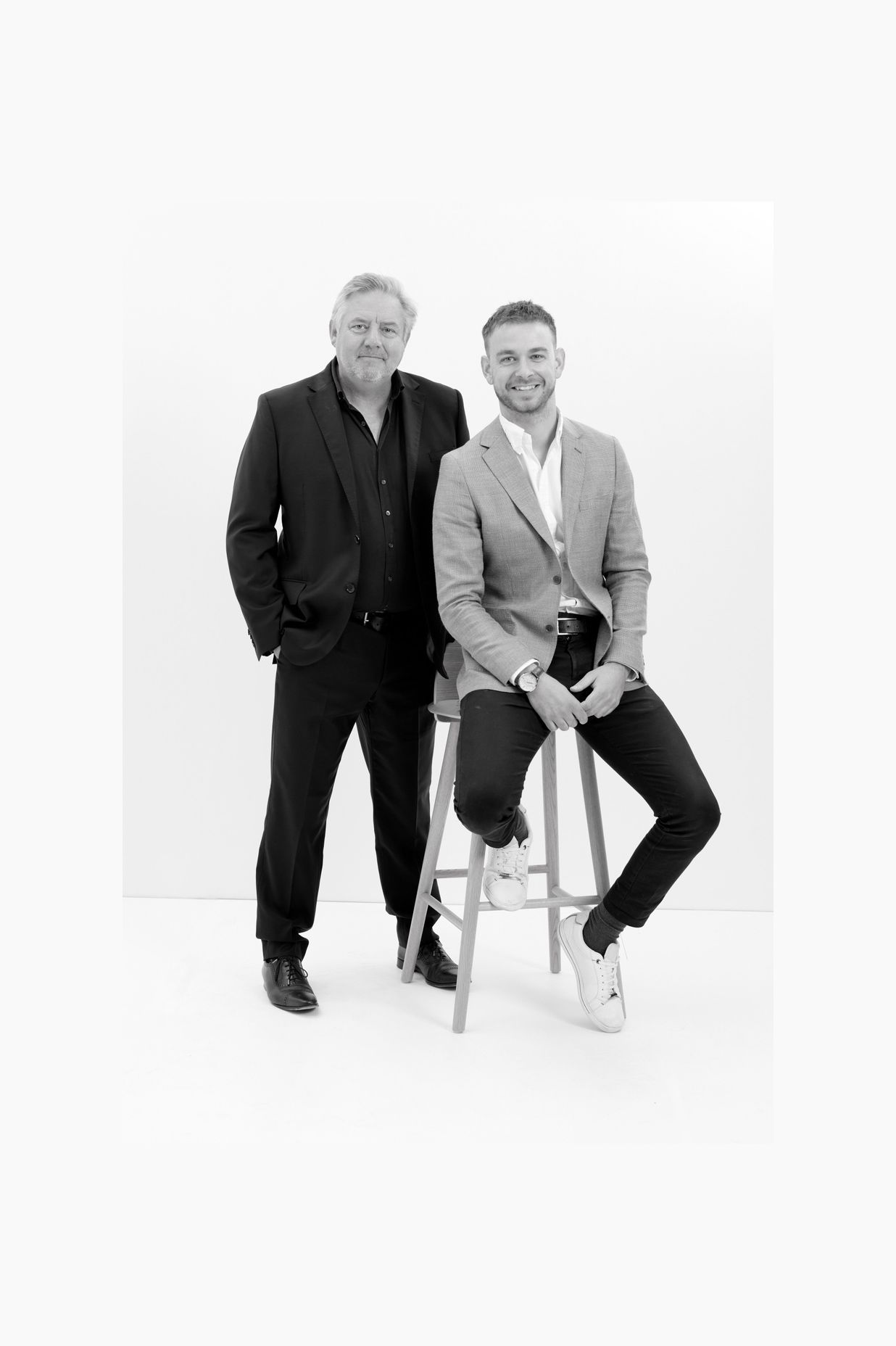