Hayman Park Case Study – The tallest playground in NZ
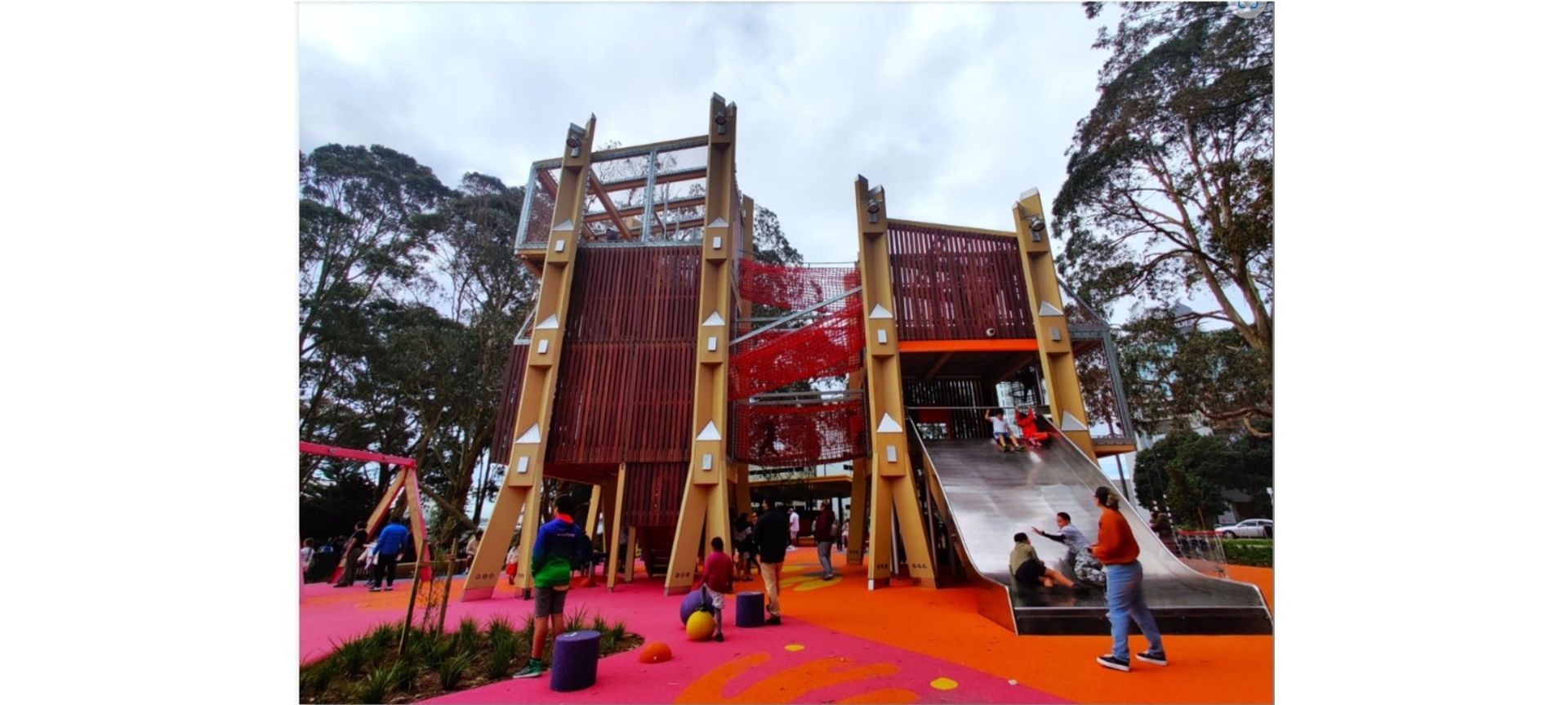
PROJECT CREDITS:
Client: Auckland Council; Eke Panuku | Project Manager: Bluewater Project Management | Architect: Athfield Architects and Wala Landscape + Architecture | Engineer: Enovate Consultants | Contractor: HEB Construction | Mass timber installer: Kobe Construction
The Tallest Playground in New Zealand
Red Stag TimberLab proudly participated in the new Hayman Park playground development in Manukau. The project involved two large Glulam towers: one 4 stories and the other 3 stories. Currently, the playground stands as the tallest children’s playground in New Zealand, reaching a height of 12.8m. The towers contain three climbing walls, two slides, two flying foxes, four climbing bridges, and multiple walkways between the structures.
Because the existing playground was still in operation throughout construction, Red Stag TimberLab proposed a full prefabrication option to ensure a rapid site assembly and minimal site disturbance. The Glulam frames were factory pre-fabricated and delivered to site as large H-frames. Dimensions were up to 5.6m wide, 13m long and 2.9 tonne. Tight access and Traffic Management Plans meant all frames were delivered in the early morning. The crane had to be demobilized by 6am for each load.
Multiple suppliers were involved in prefabricating different components for the project. Careful 3D BIM co-ordination was required between all parties to ensure accurate detailing and seamless integration. All Glulam components were modelled in 3D and fabricated on large CNC processing machines to ensure millimetre accuracy. The efficiency of digital fabrication becomes apparent in projects like this, where several components need to be prefabricated and communicated through a centralised BIM digital model.
CAD 3D Modelling

Prefabrication
By prefabricating the frames, the Glulam elements were able to be rapidly site installed with minimal disturbance. Prefabrication also provided a high level of quality assurance for the project delivery. Taking time off the building site and putting this into a controlled factory setting de-risks the project by having more certainty around cost, quality and timeframe at a very early stage. Site inspections were also a lot faster with consulting teams visiting our factory to provide sign-off on critical connection details when the frames were lying horizontal rather than 13m in the air.
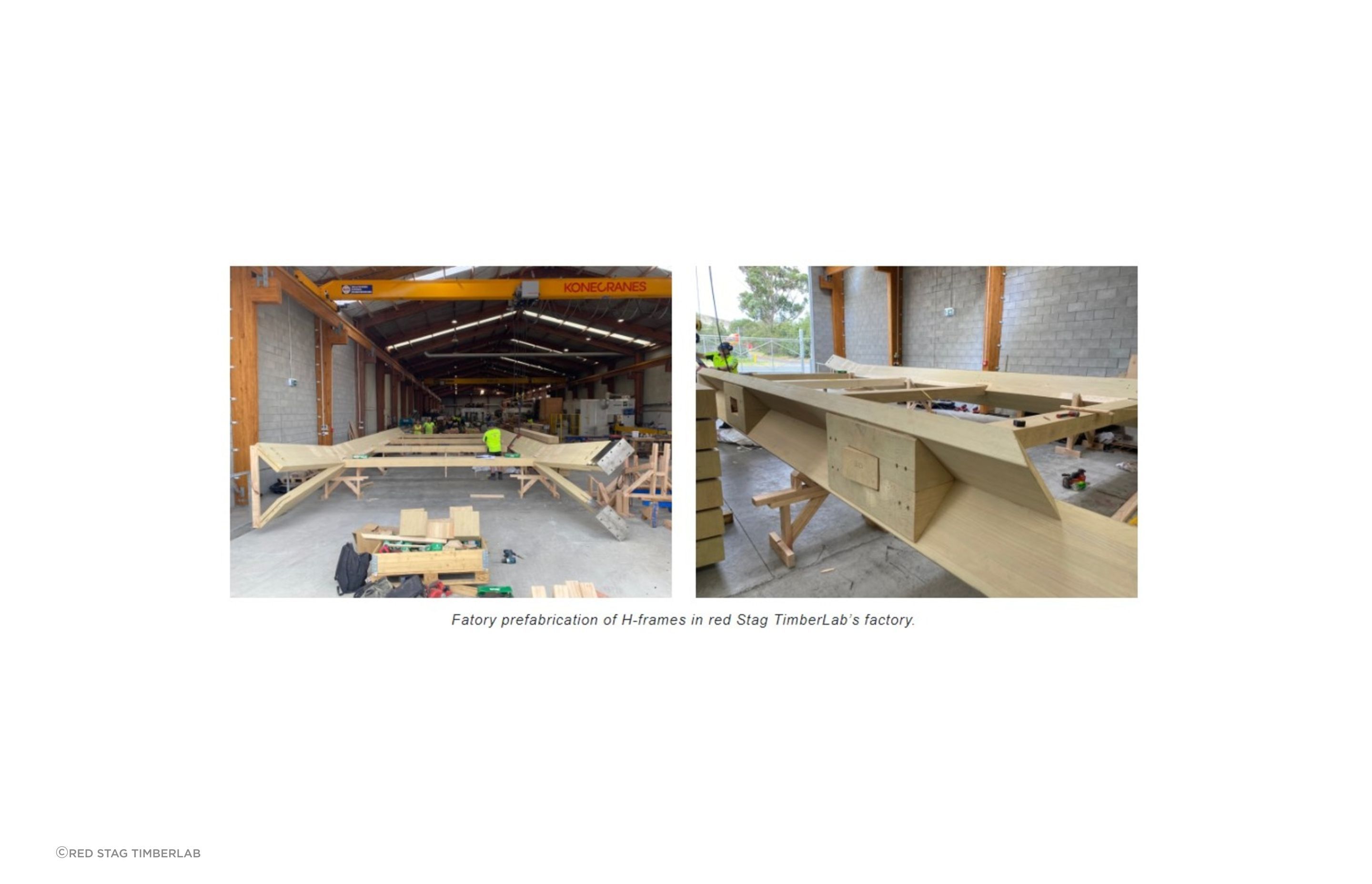
Due to the high level of prefabrication adopted in the project, all frames were installed onsite within hours. Saving time onsite offers significant commercial advantages. These include: lower financial holding costs, lower market risk, and lower preliminary and general overhead expenses. Considering these advantages, prefabricated timber solutions have been proven to be more cost effective than equivalent steel or concrete structures.

Treatment
All the Glulam components are exposed to the weather in the finished structure. Secondly, being a children’s playground, it is vital to avoid toxic treatment chemicals in the timber. To achieve durability requirements, all Glulam raw material was pressure treated with Micronized Copper Azole (MCA) to H3.2. This avoided the need for harmful chemicals such as arsenic. MCA is an environmental alternative to CCA and has benefits associated with visual grade Glulam. Additionally, an oil-based topcoat system was used to provide a colour tint to the timber and offer long-term resistance against moisture ingress.
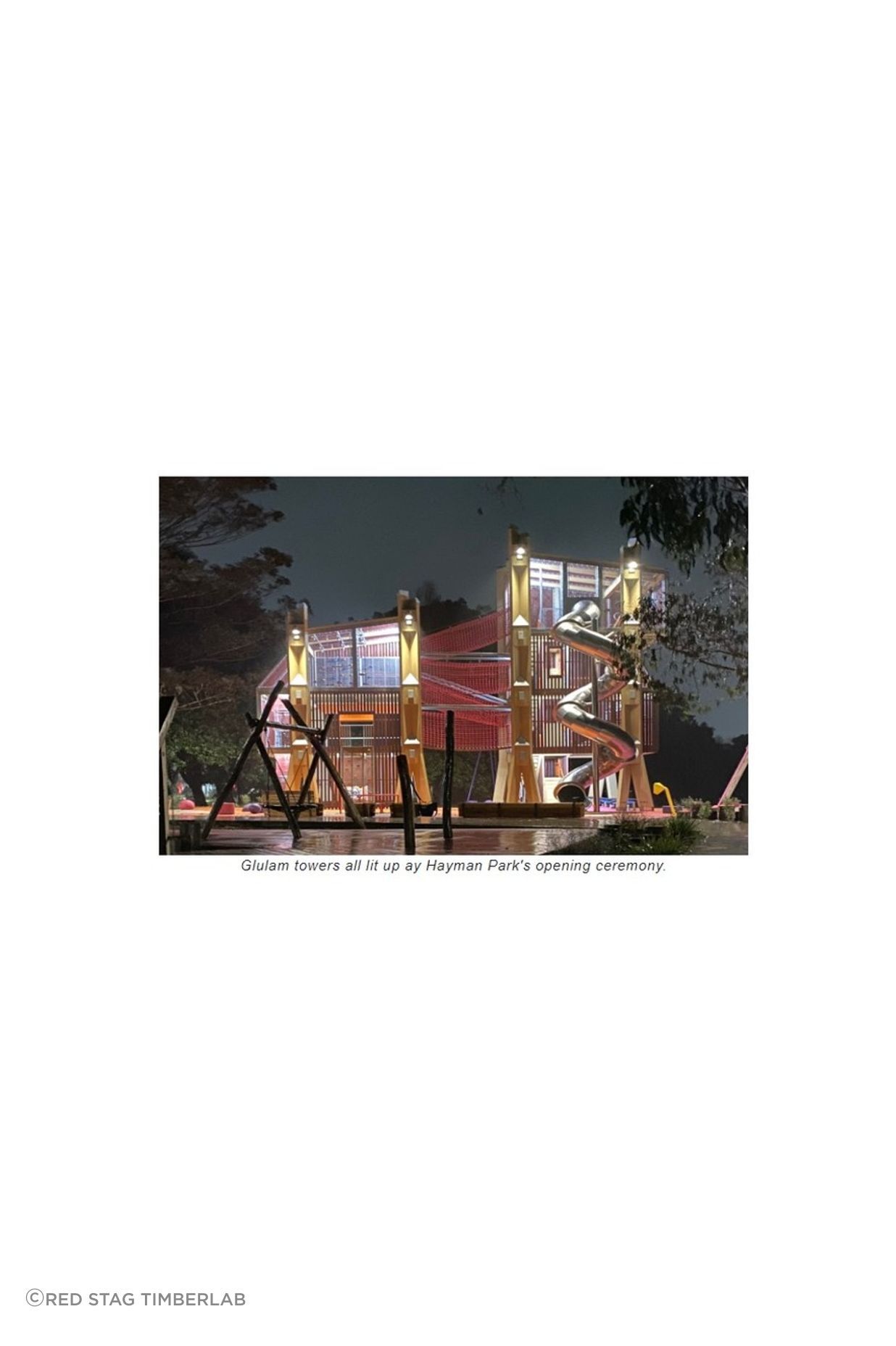
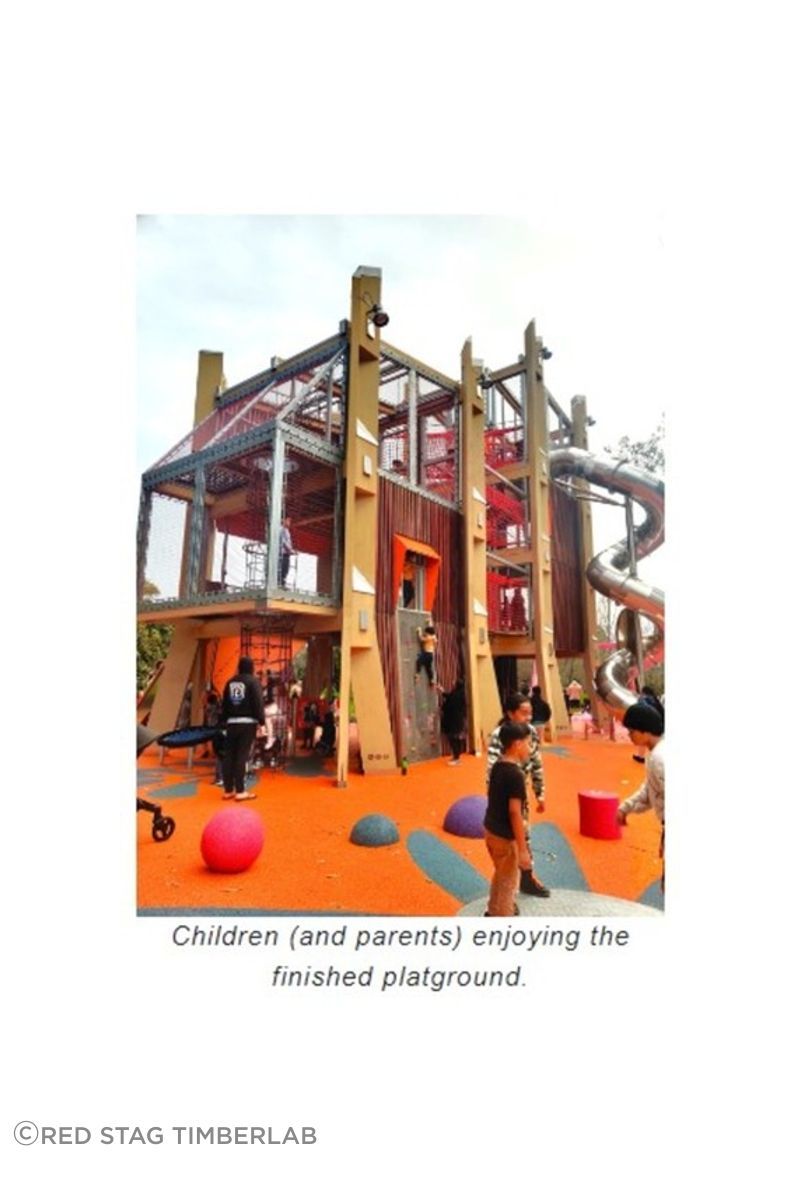
Our commitment
Community projects such as this are always rewarding for us to be involved with and seeing the playground being used by hundreds of cheerful children really highlights the benefit mass timber has for biophilic design.
Our commitment to being leaders in delivering these types of projects means we make use of every project to refine our systems and explore new technologies to help make the construction process better for our customers and project collaborators alike.
With every new high-profile project completed, the public and design communities become more aware of mass timber’s limitless design options. Working with mass timber helps us achieve a sustainable, carbon-neutral future. A future Red Stag TimberLab is proud to be a part of.
Testimonial from Blair Tipler – Director, Kobe Construction: “Working with the team at RSTL on the Hayman Park project allowed us to utilise the use of their factory to pre-assemble the massive Glulam H-Frames. Due to the size of these frames, they could only be transported to site overnight and with TMP restrictions we needed to have these installed and the crane had to be demobilized by 6am for each load. These types of projects require considerable co-ordination, and it was a pleasure to work with RSTL to deliver Hayman Park. It surely is spectacular.”