LVL Prefabrication – Clearwater Apartments, Christchurch, New Zealand
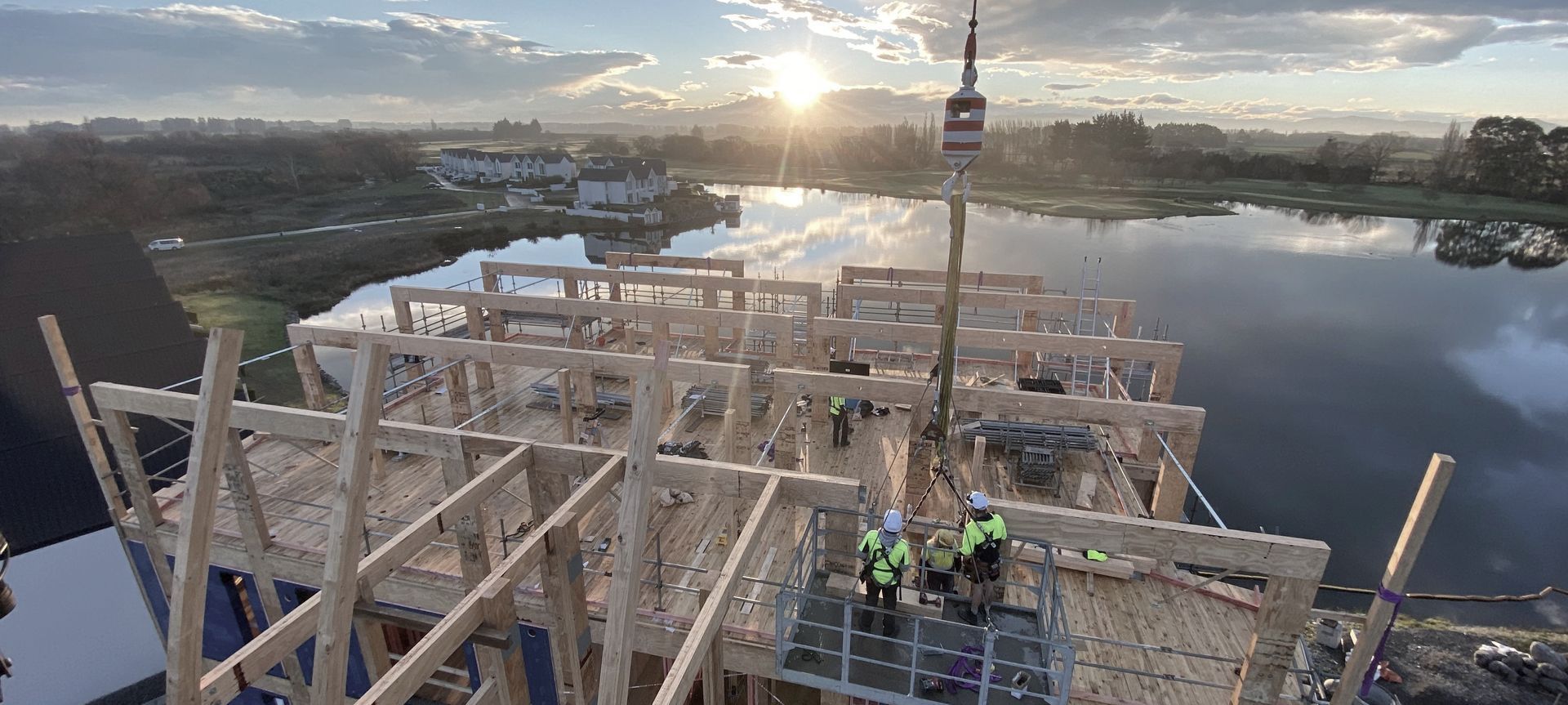
Click here to view the full article: LVL Prefabrication | TimberLab | Clearwater Apartments, New Zealand (redstagtimberlab.co.nz)
Project team: Enovate Consultants, Pacific Environments, Logic Group, Kobe Construction
Client: Red Stag Investments
The Clearwater Apartments (The Gap) is a 5-levelled high-end residential apartment building with a total floor area of 2,130 m2 (including garages). The building has 2-apartments per level with an open plan design looking over the lakefront of the prestigious Clearwater development.
The structure consists of prefabricated LVL moment resisting frames, prefabricated light timber framed (LTF) walls, curved glulam columns and cross-laminated timber (CLT) floors. TimberLab were proud to be the supply partner for the LVL moment resisting frames and curved glulam columns. Other supply partners included XLam CLT floor panels and Concision LTF walls, utilising Red Stag timber.
Because multiple suppliers were involved in delivering the project, careful 3D BIM co-ordination was required between all parties at an early stage to ensure accurate detailing.
Each supplier worked from the same modelling software which enabled accurate sharing of 3D models for drafting and co-ordination.
Working from our 3D digital model, we transferred files to our CNC machining centres to accurately complete all the cutting, drilling and shaping to suit connections and interfaces with other products. The efficiency of digital fabrication becomes apparent in projects such as this where several suppliers are needing to work from the same centralised BIM model.
The building structure relies on the LVL moment frames to provide the full lateral load resisting system across the building. Given the high seismic requirements of Christchurch, the frames needed to be designed with ductility in mind which resulted in complex connections at the beam/column joints. To save time onsite, LVL prefabrication was undertaken by TimberLab to fabricate all the complex connections in a controlled and efficient environment. The frames were supplied to site as ‘H-frames’ with a simple connection splice required onsite at each mid-height column joint. H-frames were delivered to site in sizes up to 11.8m long x 4.1m wide.
Because this is a show case timber building, the visual quality of the structural timber components was an important aspect in the design consideration.
All bolts were counter-sunk in the factory, plugged with timber to create the required fire char resistance and then sanded to a high aesthetic finish.
All TimberLab elements were CNC processed to millimetre accuracy, packed in specific order and carefully coordinated with other suppliers before being freighted from our Auckland factory.
Due to the size of the prefabricated H-frames, careful attention to detail was required with the crating protection and packing order.
The stairwell structure was designed to visually expose all timber elements and to emphasise the natural beauty of mass timber architecture. Curved glulam columns were detailed to the back of the stairwell to provide an elegant entrance façade to the building. The columns had to be carefully detailed to ensure ease of construction and to accurately interface with connections.
After pressing the curved columns, TimberLab CNC machined the profile to ensure they were perfectly dimensioned.
Incorporating factory prefabrication meant that significant time was saved onsite. Each floor (LVL frames, CLT floors and LTF walls) were installed in less than 2 weeks per floor. Saving time onsite has significant commercial advantages, lower financial holding costs, lower market risk, and lower preliminary and general overheads. When considering these advantages, the Clearwater mass timber solution was proven to be more cost effective than an equivalent steel or concrete structure.
Carbon sequestration also resulted in significant environmental benefits when compared to equivalent concrete and steel solutions. Trees remove and store around 1.8kg CO2 / kg wood from the atmosphere during growth. Each m3 of solid Pinus Radiata therefore stores approximately 900kg of CO2. Analysis of the Clearwater Apartments showed the embodied carbon of the mass timber building was -82 tonne of CO2-eq while the steel and concrete equivalent solutions would have been +792 tonne and +831 tonne of CO2-eq respectively.
Sustainability is now established as a fundamental requirement for modern construction and our regulatory framework is rapidly adapting to meet this requirement. Wood is, by far, the world’s most sustainable building material. Sustainable forestry practices and certification in New Zealand means that vast quantities of timber can be used in construction materials to create long-term carbon sinks, which continue to grow day by day. Mass timber projects such as the Clearwater Apartments are an important solution in helping to achieve the Government’s Building for Climate Change targets.