The bricklayers building the foundations for an ambitious affordable housing project
Written by
05 September 2023
•
4 min read
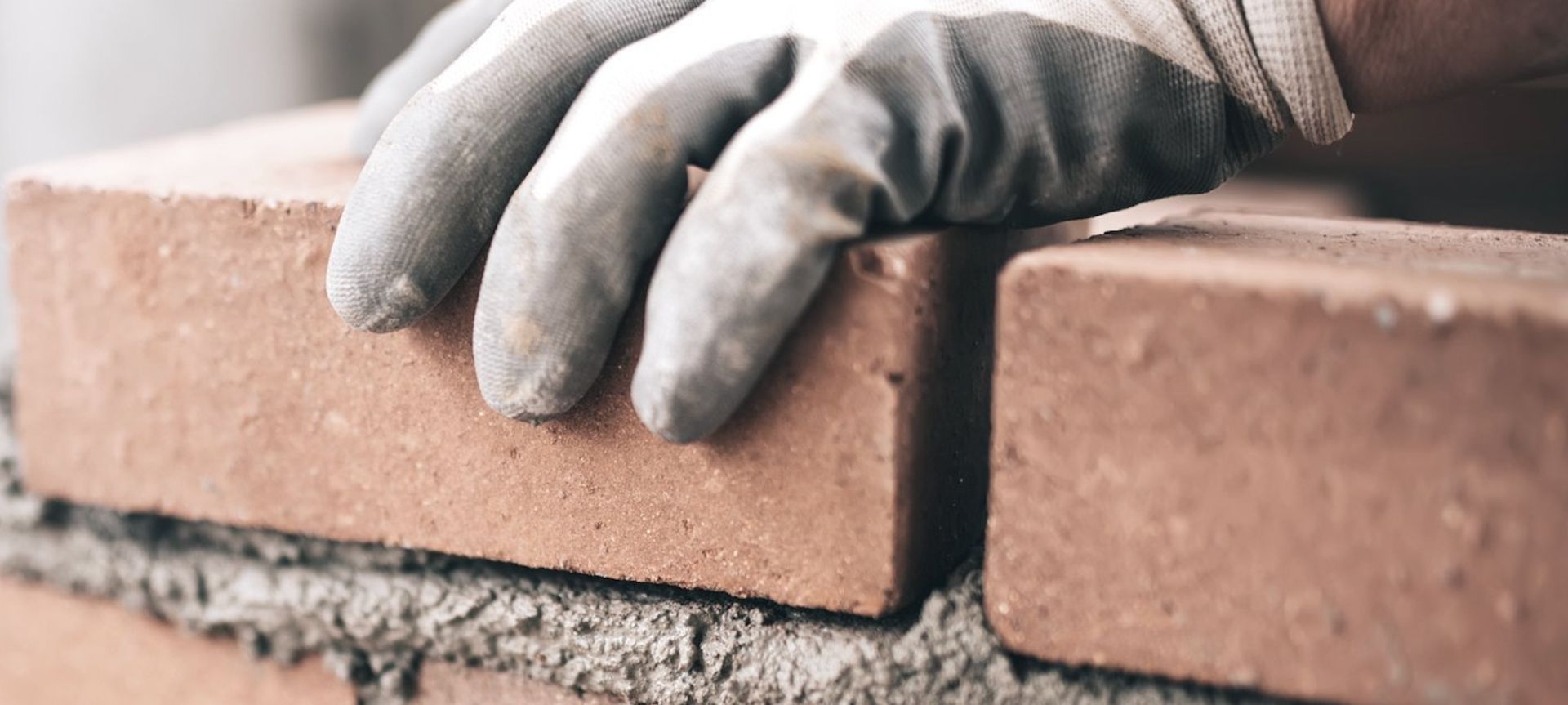
For Ben Roche and his team of bricklayers, the Hamlin Park project was an especially gratifying one.
In September 2021, Ben’s Bricklaying was brought on board at the preplanning stage for the sprawling Hamlin Park project – a $25 million housing development in Mt Wellington with the aim of providing 30 new apartments for Māori from iwi both in Tāmaki Makaurau and further afield.
They were tasked with providing the brickwork expertise for a large complex that comprises five three-bedroom triplex homes, nine one-bedroom, and 16 two-bedroom single-level homes – a particularly large undertaking for any trade. In the time from when the projected started in December 2022 until the final brick was laid in March the following year, a staggering 42,000 masonry blocks had been laid, and 336m3 of firth concrete block fill had been used.
Ben says the scope of the project, as well as the high degree of community involvement, made the whole process one to remember. “Being part of this project was really cool for me and my team for so many different reasons,” he says. “For us as a company, it was a really good opportunity to showcase the experience of everyone on my staff and our general ability to take on larger projects.”

But this was only a fraction of the satisfaction that the Ben’s Bricklaying team got from their work on Hamlin Park, and it was an especially sentimental undertaking for Ben.
“It always feels good when you’re helping create affordable housing,” says Ben. “As a young Kiwi myself, I know how difficult it can be to live in a good quality home that doesn’t cost a fortune. Knowing that these homes will be going to young people like that makes it all the more gratifying to work on this kind of site.
“We all deserve a nice, warm home to call our own.”
Achieving these goals – to create community housing that is warm, dry and healthy while also remaining affordable – calls for certain products and services that are conducive to this. Masonry, and the bricklayers that work with it, can absolutely be counted as being in the intersection of this Venn diagram, Ben says.
“Firstly, brick is a low-maintenance material, so the people moving into these houses don’t need to worry about costly upkeep,” says Ben. “It’s a one-time installation – there’s no expiry date on brick cladding. It doesn’t burn or rot, and it is an excellent insulator too – keeping your home warm in winter and cool in summer.”
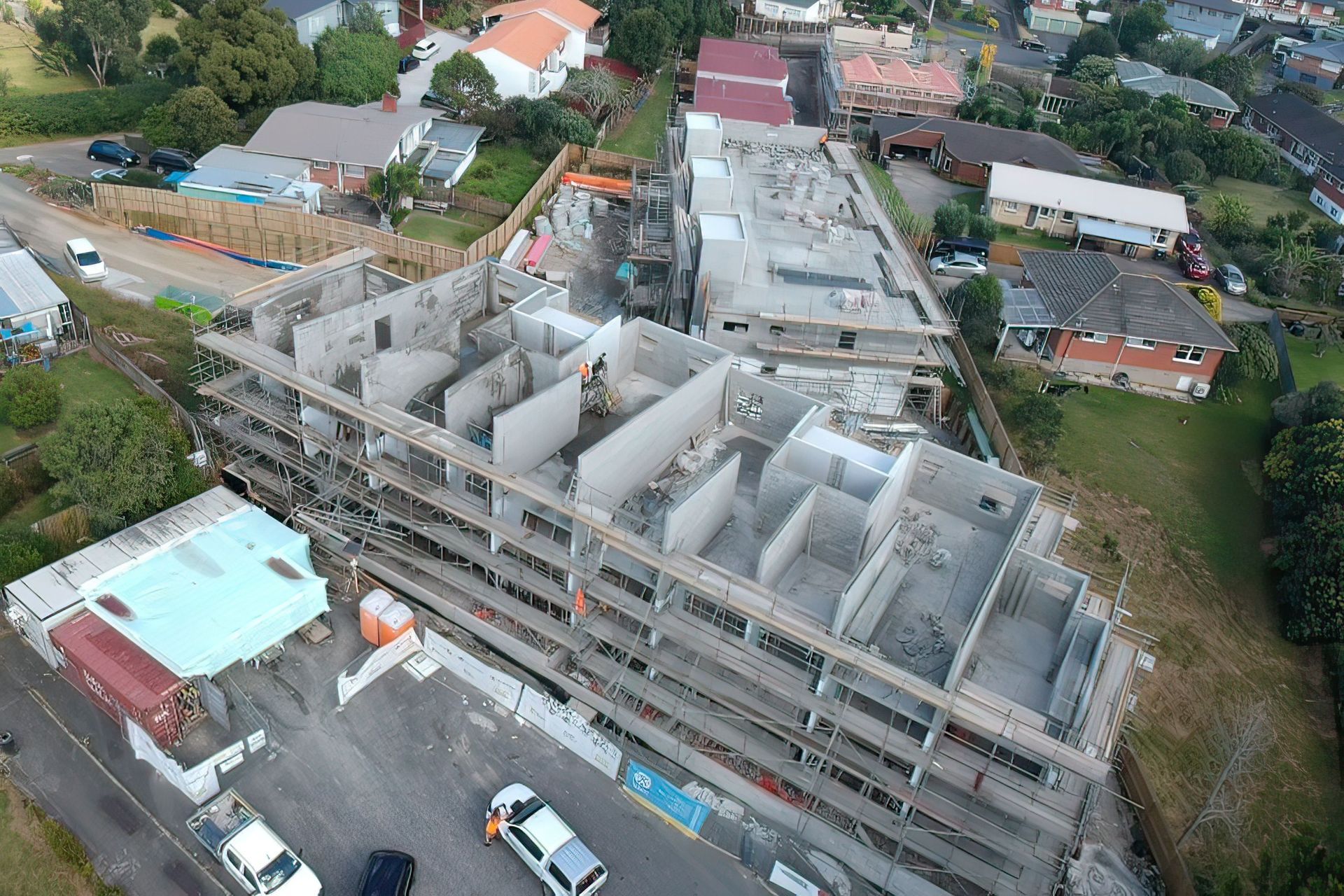
It’s also versatile when it comes to aesthetics, too – owners can choose to paint it or plaster it to introduce new looks or help it blend into potential future home extensions.
“There’s a reason masonry is one of the oldest continually practised professions in the world,” Ben says. “It’s such a versatile material – and for this project in particular, it fit like a glove.”
Ben and his team used Firth 20 Series blocks and Firth concrete throughout their work on Hamlin Park. With such a large volume of concrete to work with, there were a couple of snags that the team ran into – but nothing they couldn’t handle.
“Sometimes it felt like there was something new to organise every day,” says Ben. “At one point, there were two buildings going up at the same time, so there were multiple trucks and trailer loads of blocks going in every second day, concrete pumps, block fill and trucks every other day. Nothing we’re not used to – but still, a very busy construction site.”
This is the kind of challenge that Ben relishes, though. “The bigger projects seem to keep you honest,” he says. “There is so much going on each day, you really have to be on your toes at all times – and this makes it really exciting. No two days are the same.”
But at the end of the day, there was always a single highlight that stood out from the rest.
“Knowing that Ben’s Bricklaying is playing a vital part in creating affordable housing for fellow Kiwis,” he says. “That was the driving force behind us.”
Learn more about Ben’s Bricklaying and its services.