Carved into rock within a delicate mountainous landscape, this month’s Project of the Month needed great skill and experience to construct such an incredible home. ArchiPro spoke with the builder, Peter Campbell from Triplestar about the challenges his team faced at Hidden Island Retreat, a house designed by Mason & Wales Architects.
ArchiPro: What made Hidden Island Retreat such a complex build?
Peter: The internal environment is 800m², plus there are around 200m² of terraces and decks, so the house has about 1,000m² in total – it’s large! But, the complexities of the build are largely driven by the fact that it is very top-heavy, so there’s a lot of weight in the roof structure. The appearance of the roof is to look light but actually it’s quite heavy. We’ve had to engineer a ballast roof to accommodate tons and tons of gravel, which, when you fly over or if you’re up on the ski fields looking down, makes it quite hard to pick out.
There is also more than 500m³ of concrete in the building, including 30 cubic metres of concrete just suspended over the front entry, and pulling all of that together with an engineering solution that responds to the architecture was a challenge.
The excavation of the building was particularly complex, because we had to excavate into solid rock. We actually had to blast and cut the rock out and there was around 1,000 tons that came out of the build. While we haven’t used the rock in the actual building, we’ve utilised some of the rock in the landscape and to retain the front of the property.
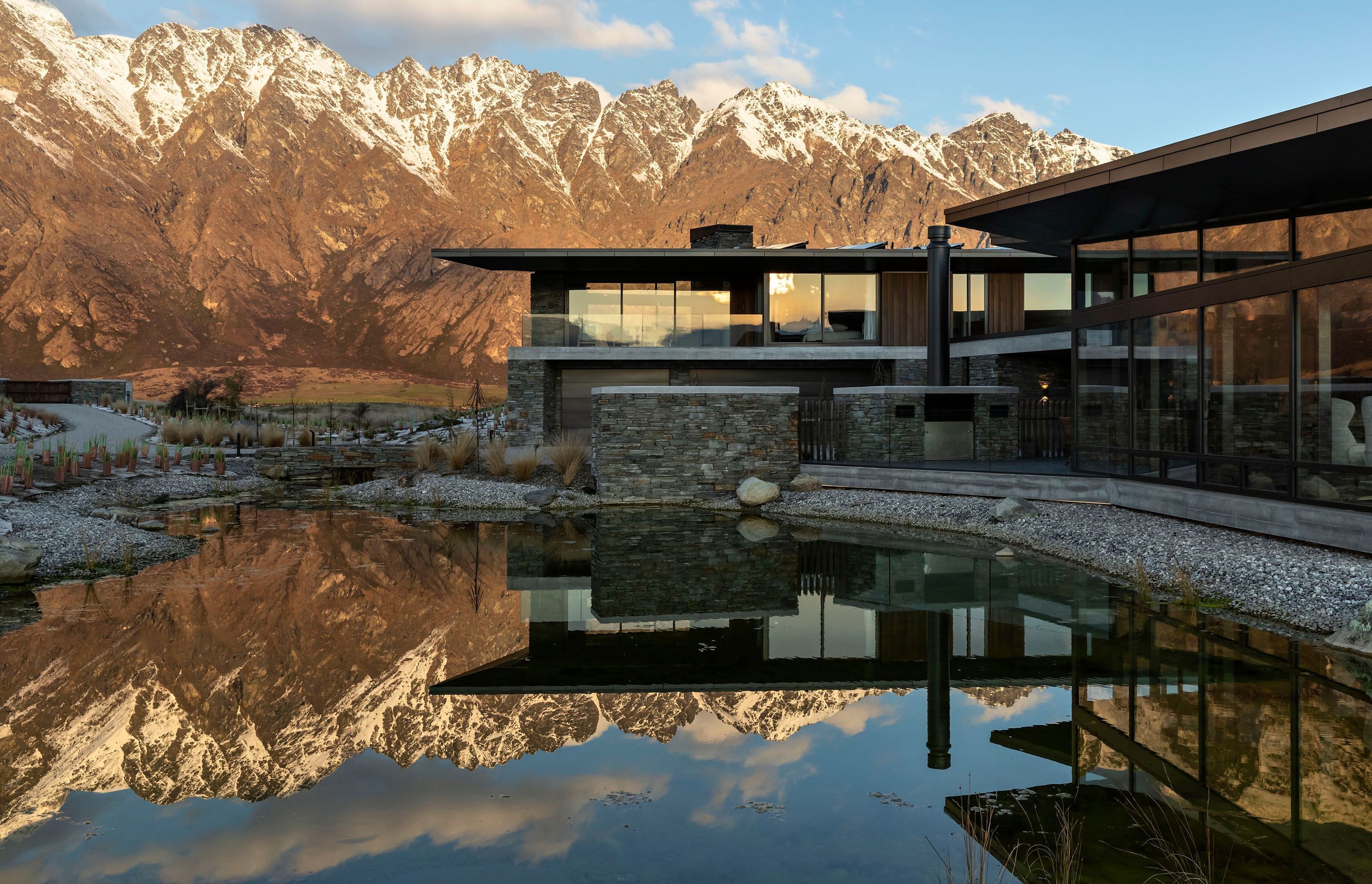
Was the installation of the services a big challenge, given the size of this project and the extreme climate in which it’s sited?
Yes, our client had a pretty specific brief regarding the services, which created a bit of the challenge for us as the design and construction team. The client wanted a house that’s able to maintain 28 to 29 degrees Celsius in the winter, because he spends a lot of time in Asia and wanted a warm environment but, with 800m² of internal space that includes large voids, big spans and wide open areas, as well as lots of glazing and cold winters, we needed some pretty modern, state-of-the-art heating systems.
We decided to heat the house using a ground-source heating system. Effectively, how it works is that for every square metre of floor space, you drill a lineal metre into the ground so, to cater for the 800 m² floor area, we’ve drilled eight bores 100m deep into solid rock. So, we’re taking the heat from the ground and boosting it with a heat pump to heat the environment through the bores.
The simple principle behind it is that the ground temperature you go down to has an inherent heat of about 12 or 13 degrees so, if you want your internal temperature to be 22 degrees, you’re heating from 12 to 22 degrees, which requires only 10 degrees of heating. Whereas, if you’re drawing heat from the outside and putting it through heat pumps, and it’s minus-five degrees outside and you want 22 inside, then you need to heat the house by 27 degrees. So, a ground-source heating system uses a lot less energy and while it has a higher capital costs, the ongoing operational costs are way lower.
The other challenge with the services on this particular build is that there are a lot of different structures; thus, we had to reticulate the services around very tight ceiling voids – so, a lot of thought went into that.
Can you please describe how you've incorporated solar panels and rain water harvesting into the build?
We’ve installed photo-voltaic solar panels on the building, kept them quite low from a visibility perspective but, obviously, sat them at a position where we could maximise the sunlight. Their purpose is to provide electricity, not to make the building completely off-grid as we were never going to be able to achieve that with a building of this scale, but we have achieved a considerable level of self-sufficiency within the energy requirements for the building. And, large buildings like this cost a lot of money if you’re running them off diesel or with straight off-the-grid electricity.
There are sustainably driven environmental considerations by the client in the building. For example, there is a natural tarn, a little waterway, at the top of the property, which is intended to filter down to a man-made reflection pond that’s been created for the building. The tarn dries up during the summer months, but we didn’t want the pond to be drying up and looking arid, so we decided to use the pond for the stormwater collection. Rainwater comes from the roof and is discharged directly into the pond and, then, through evaporation, we top the water up from one of the water bores.
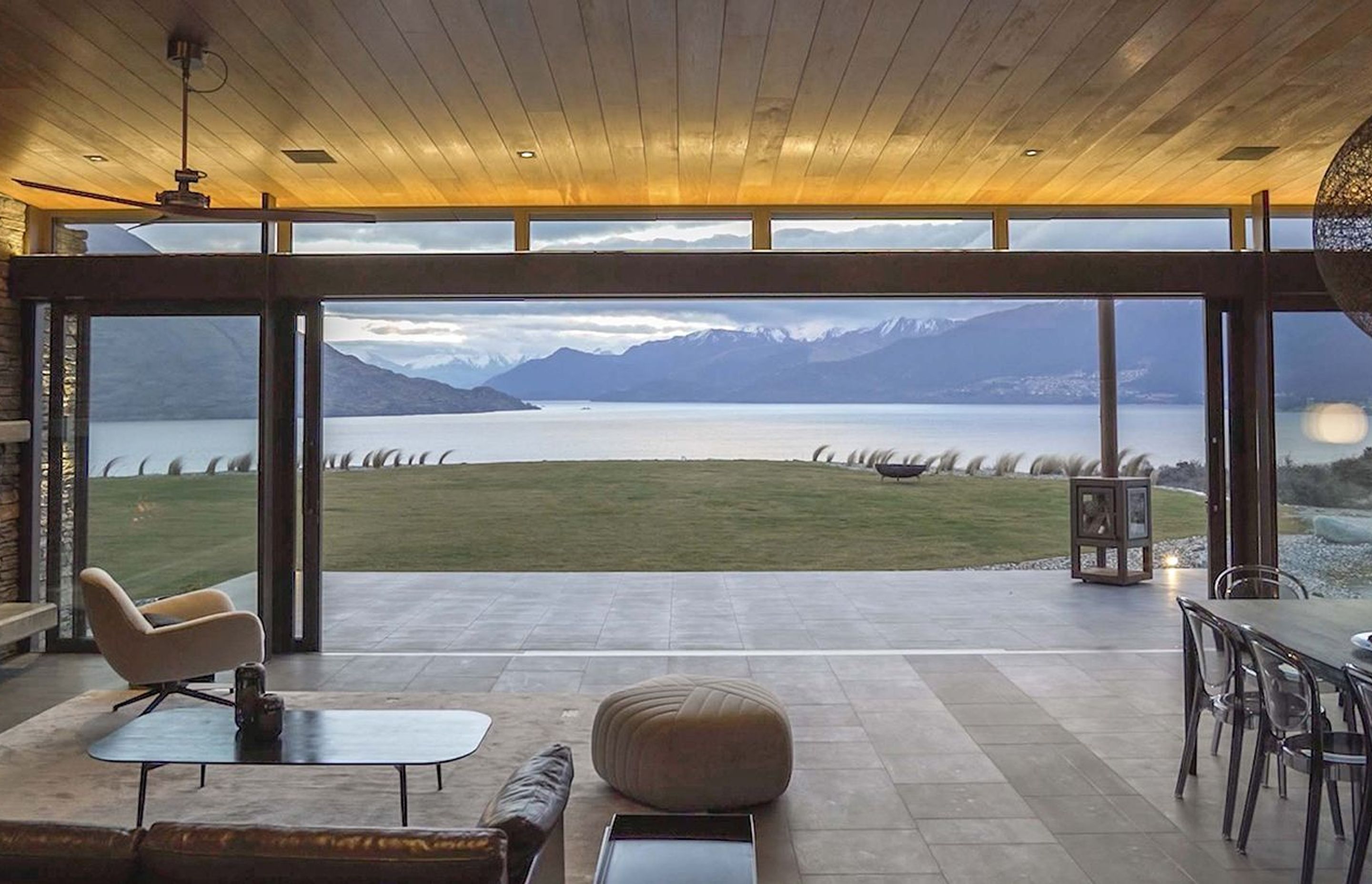
How does the building perform within this climate of hot and cold temperatures and glacial winds?
The climate in Queenstown is quite extreme, from very hot and very dry with a lack of humidity to extreme cold and this site in particular is very exposed to the wind. So, we have a high-performing thermal envelope with a warm roof that’s heavily insulated, and it’s also an airtight building. This means that the building is easy to warm but it also creates a cooling environment in the summer.
One of the tricks of this house is maintaining a high level of thermal efficiency, while maximising the views. There is a serious amount of glazing, which, typically, results in high heat loss so we’ve installed high-performance, thermally broken, double-glazed units and large eaves to stop the heat build-up over the summer months, along with automated windows that power open when a thermostat tells them to, allowing ventilation through the building.
How did the team work together?
We had a great crew of sub-contractors on this build, which was integral to creating such a refined finish and to achieve what the architect was setting out to achieve.
One of the things I’ve noticed is that with bespoke high-end architectural houses, there are a lot more beautiful natural materials being used now. When they’re finished and executed well, they look very simple on the eye, but the actual effort that goes in to make that happen requires a lot of coordination of skilled tradesmen, not just the builders but the guys laying the floors, the stone masons – everyone.”
Interview by Justine Harvey.
Photography by ArchiPro and Simon Devitt.
