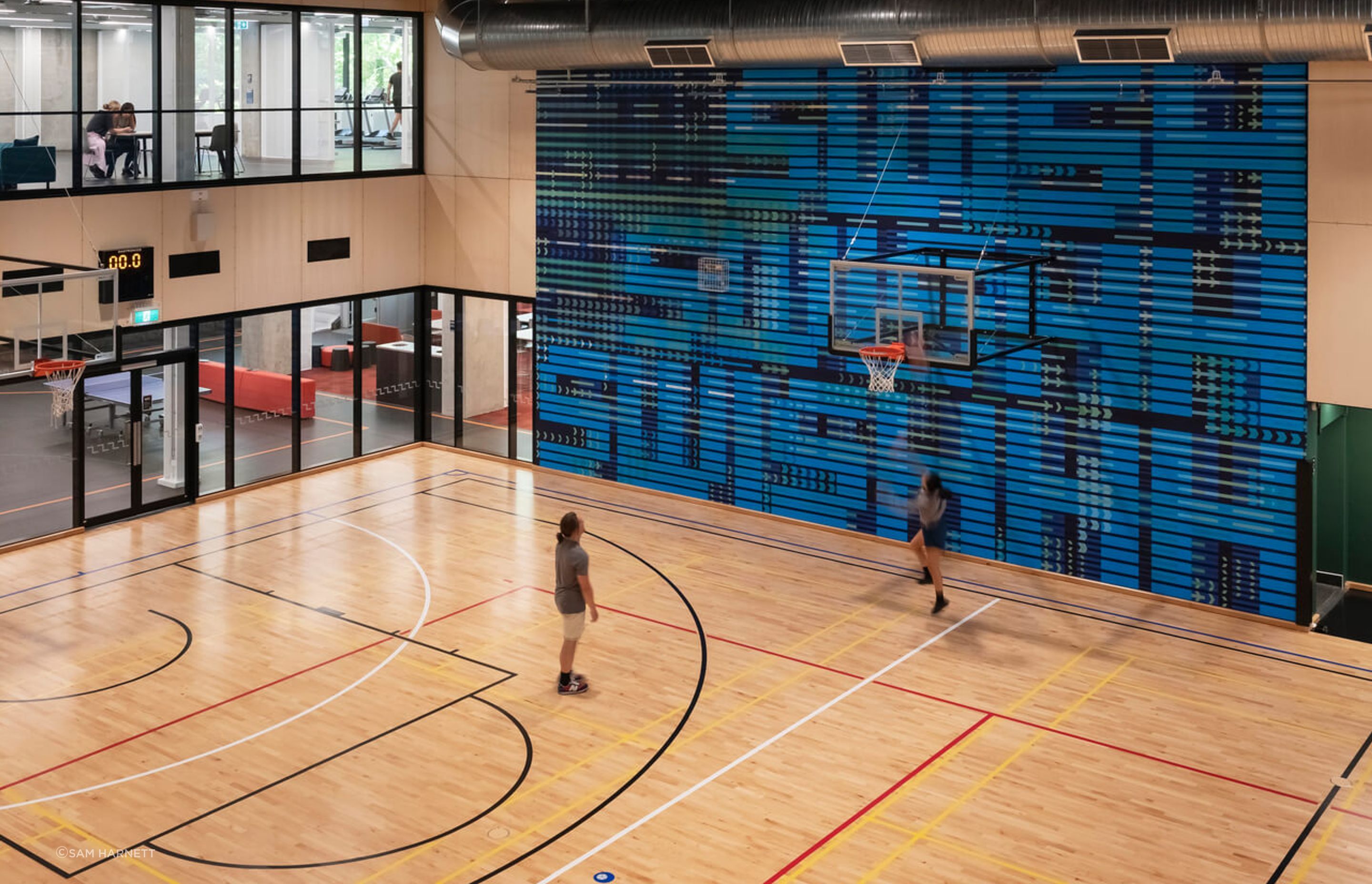
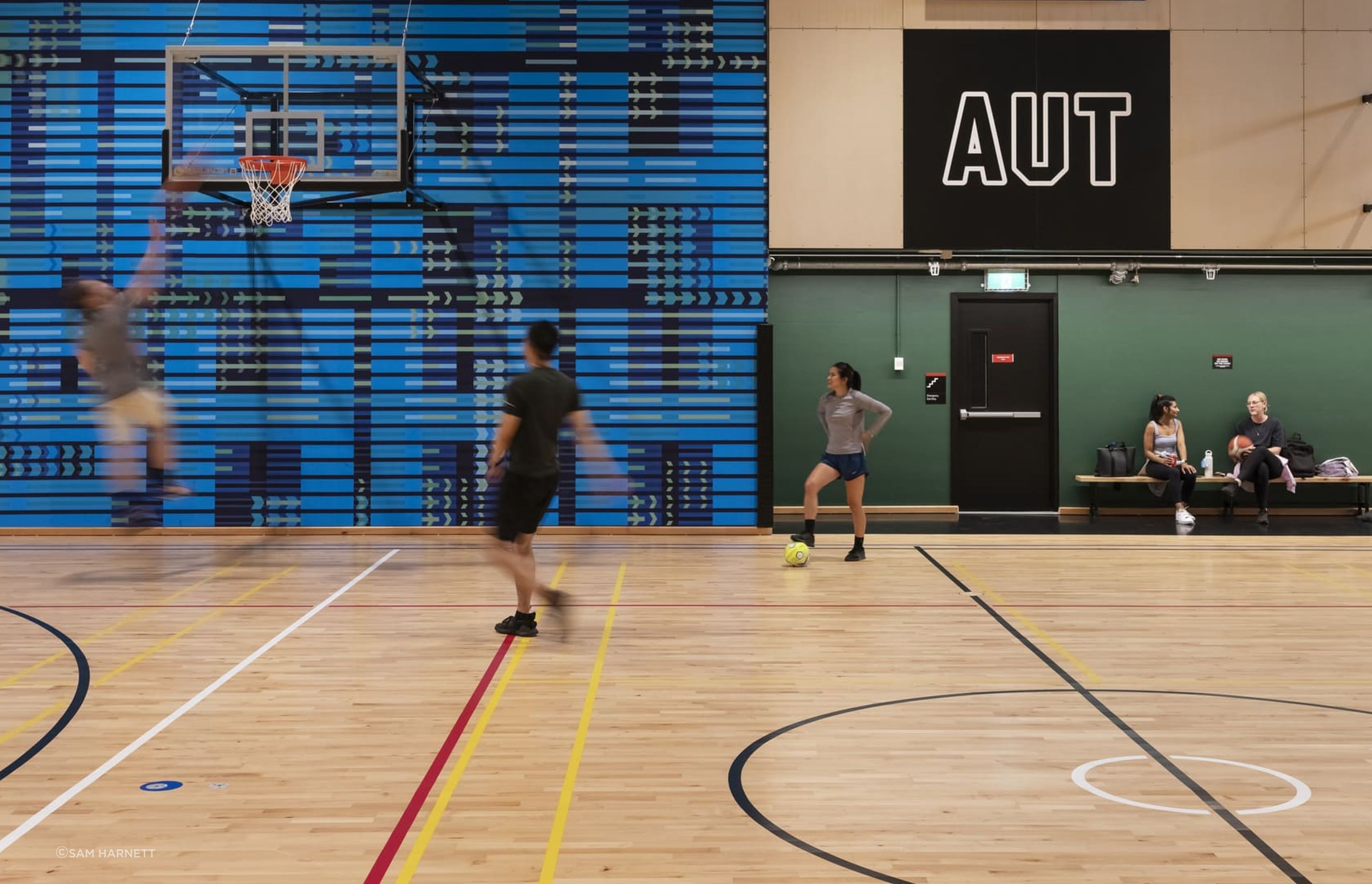
PROJECT CREDITS
- Service: CustomCoat
- Architect: Jasmax
- Manufacturer & Installer: Asona
- Photographer: Sam Harnett
- Writer: Folio
With little margin for error, custom UV-coating by Bates Surfaces was the process of choice for interior veneered panels sourced from a single Kahikatea log.
For the Sports Hall at AUT’s Te Āhuru Recreation Centre, architects Jasmax specified a series of solid and perforated timber panels that would meet acoustic and impact resistance criteria for the gym, as well as create the right aesthetic.
‘The Sports Hall is a large volume spanning three levels and providing a visual connection to a range of social spaces beyond,’ says Jasmax’s Sarah Kirk. ‘The timber lining articulates this large space with warmth and light, contrasting the more intimate social spaces.’
Track my Tree – protecting a precious resource.
Fabricated and installed by acoustics specialists Asona, the timber panels are finished with a kahikatea veneer cut from an ethically sourced windblown log with a unique ‘Track my Tree’ verification and fully documented chain of custody.
‘The kahikatea produced these beautiful veneer leaves, which we then bookmatched and fixed to a fire-rated MDF board with a black core,’ says Suzanne Pooley, National Sales Manager for Asona. ‘For the perforated panels, we developed a pattern to suit the design and specification requirements and practical fixing points.’
UV-cured clear coating for maximum durability.
To complete the panels, Bates developed a custom UV finish to physically protect the surface under the CustomCoat service. Sometimes referred to as ‘New Zealand oak’, kahikatea has an ashen tone, so Bates created various samples that maintained the original raw material colour for design approval.
‘Because the entire project batch had to be produced from that single log, there was no room for error when coating the panels,’ says Andre Bates, CEO at Bates Surfaces.
UV technology makes the surface cured instantly, allowing the panels to be quality-checked as soon as they come off the line instead of waiting to dry. ‘That way, we ensure a factory-consistent finish,’ says Andre. ‘If there are any imperfections, we can spot them immediately and adjust the line, which keeps waste to an absolute minimum.’
UV-cured clear coating for zero VOCs
Along with quality control, the UV process used for CustomCoat is more sustainable than traditional solvent surfaces, with zero VOCs, no solvents, and greater energy efficiency in manufacturing.
In the end, the Sports Hall interior was completed with just two panels left over. ‘With such a valuable and rare veneer, anything we could do to minimise wastage was important,’ says
PROJECT CREDITS
Bates Surfaces has been a leader in surface-coating building products since 1953, utilising the best UV-coatings technology in the world.
As New Zealand’s largest applicator of UV coatings, we have been a trusted supply partner to the local industry for over 25 years.
We transform products, such as raw fibre cement panels, into pre-finished, factory-coated products – working with manufacturers as they make them part of their product catalogue.
In addition to fulfilling OSM orders for customers such as James Hardie and Laminex, we market our own brands – PureCoat™ kitchen and bathroom panels, PlyPlay™ pre-finished plywood wall and ceiling panels, and hygienic Fenta™ Ceiling Tiles.
Start you project with a free account to unlock features designed to help you simplify your building project.
Learn MoreShowcase your business on ArchiPro and join industry leading brands showcasing their products and expertise.
Learn More