9 different types of cladding in New Zealand: pros and cons
Written by
10 September 2019
•
10 min read
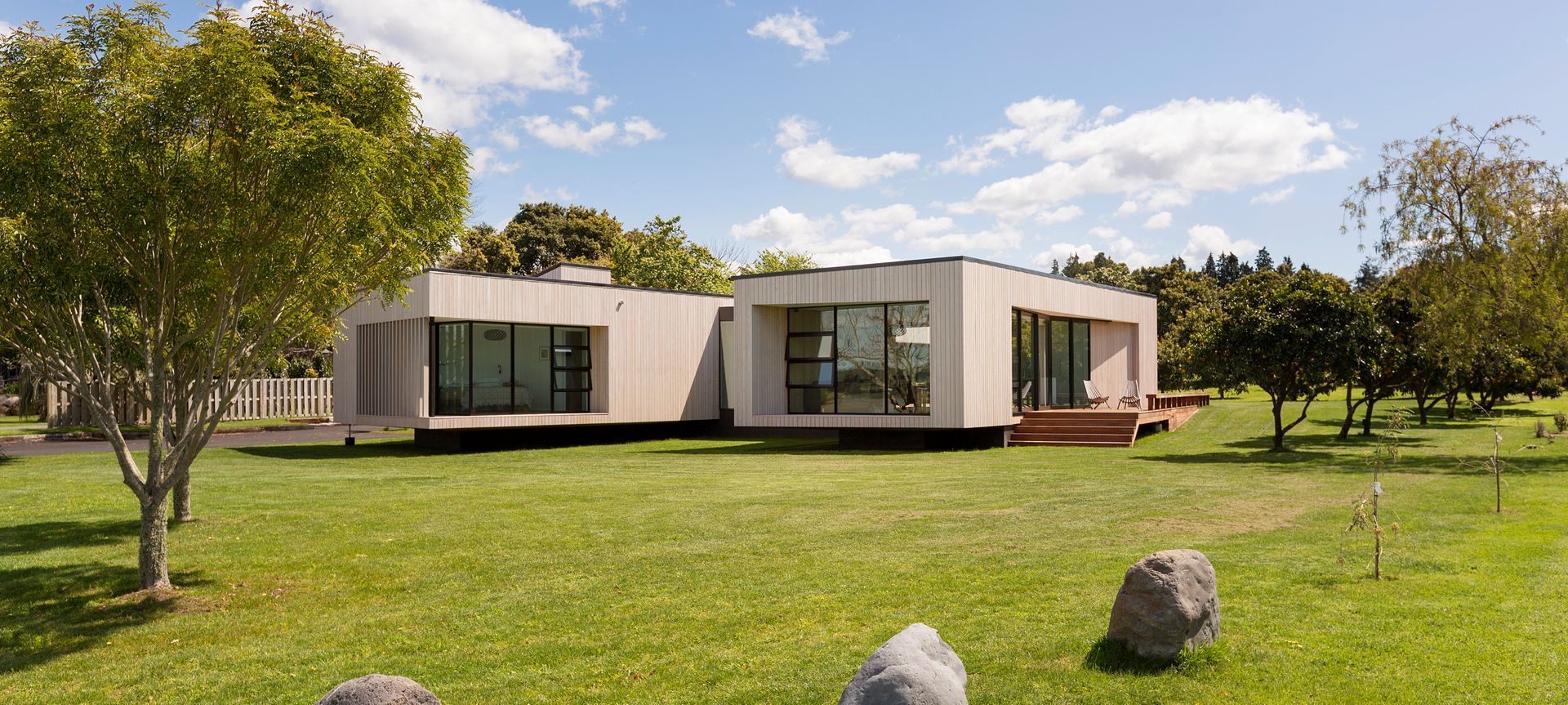
There are many different types of exterior cladding options in New Zealand making the job of choosing one all the more challenging. However, it's important to take the time to look at each on its own merits with care and consideration. To make this a little easier, we've included everything you need to know about all the different cladding materials so you can make a quick, informed decision that works for you.
Related article: What is cladding? A comprehensive guide
What types of cladding are available?
Cladding in New Zealand presents a true smorgasbord of options. Traditional timber cladding, rustic stone cladding, modern metal cladding — the list goes on.
The answer to which will be best for you depends on many things specific to your property like its location and local climate, while other factors like cost, expectations around lifespan and performance, aesthetics and more.
1. Timber cladding
Timber cladding is a trusted and reliable option, providing a warm and familiar appearance with the robustness of timber. Durable and able to withstand significant weather events, weatherboard homes have stood strong for decades in New Zealand with many Victorian and Edwardian-style villas and bungalows still popular today.
This makes timber weatherboards are solidly bankable option, given they will not only protect your home for many years to come but also have resale value when it is time for your next move. It does require a bit more ongoing maintenance compared to some other options, typically by way of painting or staining, but in doing so you'll ensure you get an excellent return on investment.
Pros of timber cladding
- Warm, familiar aesthetics
- Robust and durable
- Longevity when well maintained
- Popular in New Zealand
- Environmentally friendly when sourced responsibly
Cons of timber cladding
- Ongoing maintenance is required to keep it at its best
- If not cared for, is susceptible to rot
- A flammable material (treatments can mitigate this risk)
- Varying qualities and price points
Related article: 11 weatherboard houses in New Zealand worth celebrating
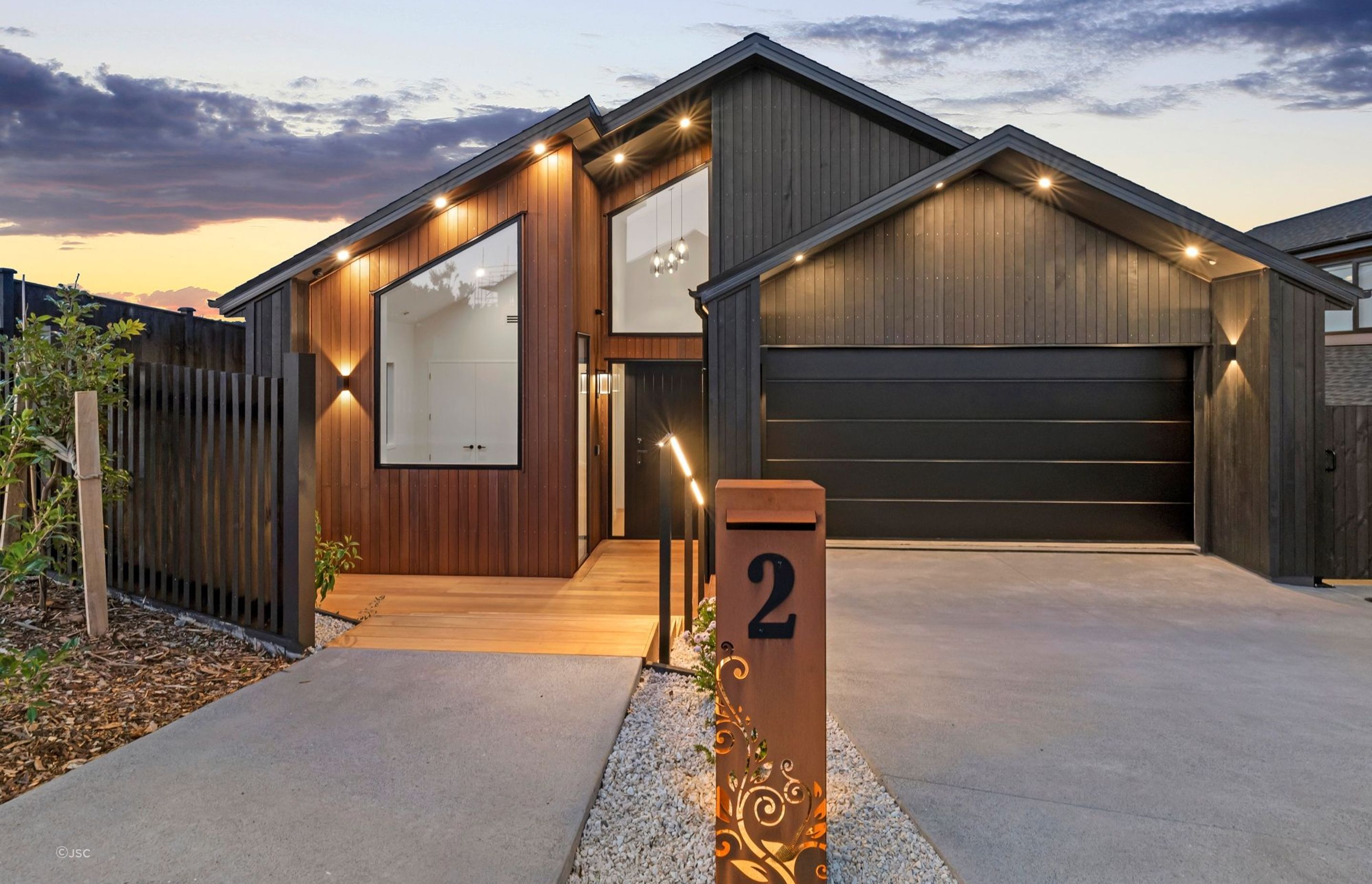
2. Natural stone cladding
Natural stone cladding is a premium rustic choice for exterior wall cladding in New Zealand. It is solid and formidable, especially against the elements and emanates a sense of permanence and timelessness when used as a facade.
While it's rare to find an entire house clad in natural stone, you will see it used as the main cladding option on the most visible and prominent sections of a home. The most common types of natural stone used tend to be sandstone, limestone and schist to name a few.
Stone provides exceptional insulation and is non-porous and non-absorbent, offering moisture protection and weather resistance. Its size and weight make it typically more costly and time-consuming to transport and install.
Pros of natural stone cladding
- Formidable and solid
- Natural, rustic appearance
- Long-lasting with little maintenance required
- Unique choice that will stand out
- Weather resistance
Cons of natural stone cladding
- Premium products, are often more expensive than alternatives
- Requires a specialised stonemason for installation
- Size and weight make it slower to work with and install
- Less variety in aesthetic options
Related article: Stone cladding — pros and cons, types, costs and more
3. Fibre cement cladding
Fibre cement is a stable, reliable and durable cladding solution that can be trusted to do its job – stand the test of time with very little need for maintenance.
Fibre cement consists of sand, cement and cellulose fibres and is most commonly applied in sheets or horizontal boards. It has strong energy efficiency and has high levels of fire resistance and resistance to rot and termites.
While it may offer less character than timber or stone cladding, it is usually more budget-friendly and is available in an endless variety of colours and finishes, allowing room for individual flair and design.
Pros of fibre cement cladding
- Resistant to rot, termites and fire
- Low maintenance with no seasonal treatments required
- Huge variety of colours and finishes
- Can be one of the more cost-effective cladding materials
Cons of fibre cement cladding
- Lacks the character of natural alternatives according to some
- Isn't as popular as some other cladding materials
- Professional installation from a cladding installer is recommended to ensure proper fitting
4. Brick cladding
Bricks are considered a highly effective exterior cladding option, aesthetically pleasing, known for its longevity and incredibly robust in our environment. They are an undeniable favourite among homeowners and developers in New Zealand, seen as a tried and tested cladding material that has very low associated risk.
Bricklaying is a little more time-consuming than installing weatherboards (as an example) which can add to costs in the early stages. Understandably, the more complex the design, the more labour hours you'll need to pay to get the job done. It is also one of the heavier exterior cladding materials which can add to freight costs, depending where you are in the country.
Once installed, however, bricks are almost maintenance-free with great durability to give you decades of use with total peace of mind.
Pros of brick cladding
- Superb durability and longevity
- Almost no maintenance required
- Aesthetics that appeal to many
- Fire-resistance, thermal efficiency and sound insulation
Cons of brick cladding
- Can be time-consuming to install
- A heavier cladding material to handle and transport
- May be more appropriate alternatives for complex architectural designs
Related article: The art of brick selection — a definitive guide for Kiwi homes
5. Brick veneer cladding
Brick veneer mimics the appearance of natural brick (these days often indistinguishable), but is much lighter making it easier to transport and quicker to install. It's a versatile cladding option which is also often used internally for fireplaces, backsplashes, walls and sidings.
Being so lightweight, brick veneer can be installed on most residential walls and is much easier to manipulate during installation than its natural counterparts. Durable and fireproof, brick veneer looks appealing without any need for paint — and therefore should be considered a highly effective cladding option.
That being said, like fibre cement cladding discussed previously, it doesn't quite have the same allure as real brick cladding, nor does it have quite the same level of robustness. Consulting a cladding professional is highly recommended to avoid moisture issues between the veneer and the structural wall.
Pros of brick veneer cladding
- Closely mimics the appearance of bricks
- Lightweight and quick to install
- Durable with little ongoing maintenance required
Cons of brick veneer cladding
- Not quite the same allure as natural brick
- Isn't quite as robust
- Professional installation highly recommended
6. Metal cladding
Profiled metal cladding is widely considered a reliable cladding option. Offering a modern and creative feel, aluminium and steel are the most popular metal cladding materials. They are available in a range of profiles, most commonly corrugated or trapezoidal.
While steel is usually more expensive, it is also more durable, with aluminium composite panels (ACP) often cheaper to build with but less robust. Both offer architects and builders all sorts of opportunities when it comes to design and construction which is why you'll see a lot of modern builds using these cladding materials.
With metal, you don't have to worry about rot or insect damage, though corrosion can be an issue for some types of metal cladding (treatments are usually available). Noise from the rain against metal cladding can also be a little more pronounced as well as denting and scratching, which doesn't impact brick by comparison.
Pros of metal cladding
- Modern aesthetics
- Presents architectural design opportunities
- Low maintenance with no threat from rot or insects
- Durable and relatively lightweight
Cons of metal cladding
- Anti-corrosion treatments for some types of metal cladding
- Pricing can vary widely between different options
- Prone to denting and scratching
- Noisier during rainfall them some other cladding materials
Related article: The pros and cons of metal cladding for New Zealand homes
7. Concrete cladding
Concrete cladding has a relatively long lifespan and can last for several decades with proper installation and maintenance. The exact lifespan of concrete cladding depends on several factors such as the quality of materials used, environmental conditions, and exposure to elements. In general, concrete cladding can last for up to 50 years or more before needing significant repairs or replacement. Regular cleaning and maintenance can help extend the lifespan of concrete cladding.
Modern concrete cladding comes in a variety of textures, colours and finishes making it a viable option for many architectural styles. It is a heavy substance to transport and work with, requiring the hands of experienced professionals. The production of concrete also requires a lot of energy so there is usually a larger carbon footprint when using this cladding type.
Pros of concrete cladding
- A strong, durable cladding option
- Offers decades of use with proper installation
- Minimal maintenance required with no threat of corrosion or warping over time
- Excellent fire resistance and sound insulation
Cons of concrete cladding
- A heavy material with professional tools and expertise required
- Can be more costly than some other options
- Often draws a higher carbon footprint
- Robust and reliable
Find the concrete cladding solution your project needs on ArchiPro
8. Stucco
Stucco is a form of plaster cladding that was used in about 15% of New Zealand homes in the 1940s - 1960s meaning it still has a presence to this day. Its textured appearance is unique and has a certain degree of charm that appeals strongly to some.
When properly applied and installed, stucco is durable which is why many of these homes still exist to this day. It's a non-combustible material giving it fire resistance and has good sound insulation properties too.
It does require a bit of maintenance over its lifespan to prevent cracks and water ingress as moisture can cause significant damage over the long term if it gets into the underlying structure. The installation of stucco requires the expertise of an experienced professional.
Pros of stucco
- Unique, distinctive appearance
- Durability when installed properly
- Non-combustible material with strong fire resistance
- Good sound insulation
Cons of stucco
- An older style of cladding
- Requires care and ongoing maintenance
- Professional expertise usually required to install and upkeep
- Water ingress can severely compromise stucco
9. uPVC cladding
uPVC cladding, sometimes called vinyl cladding, is a cost-effective, low-maintenance solution that offers great convenience for those with busy lives. Often taking the form of weatherboards, they can look strikingly similar to their natural timber counterparts.
The upkeep is very simple with no regular painting or staining required. Soap and warm water are usually more than enough to keep the surfaces of uPVC cladding clean. They are also typically very lightweight, making them easy to work with and less labour-intensive to install.
Many modern uPVC cladding options are made from recycled materials though might not be recyclable themselves. They also suffer from the same stigma that other non-natural products on this list do, with some put off by the perception of them.
Pros of uPVC cladding
- Cost-effective, low-maintenance solution
- A variety of convincing aesthetics available
- Lightweight and easy to work with
- Many made from 100% recycled materials
Cons of uPVC cladding
- uPVC material doesn't appeal to all
- Disposal of products can have negative environmental impacts
- Small repairs can be tricky without replacing an entire panel
Related article: What is the most cost-effective cladding in New Zealand?
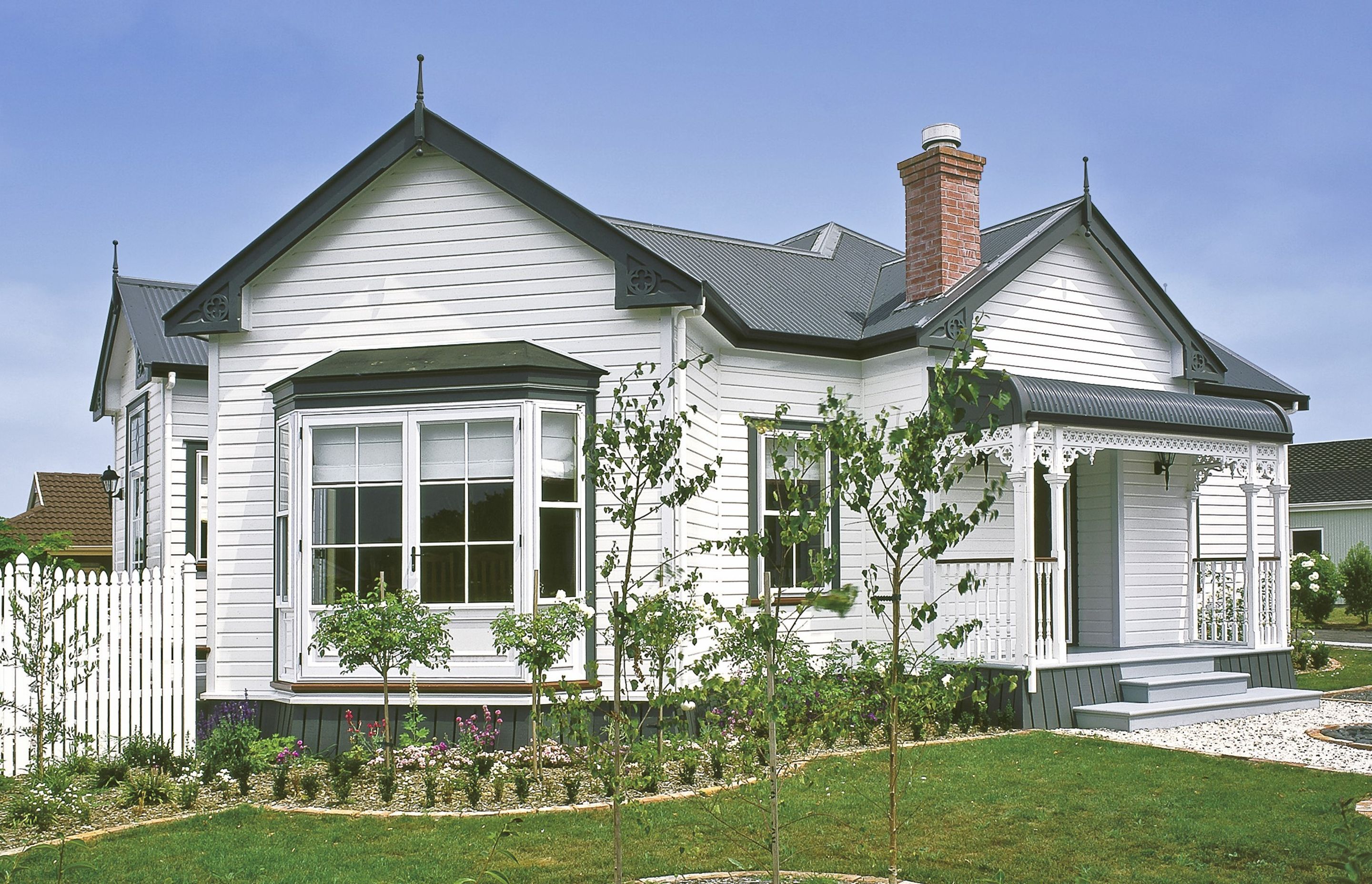
Getting you started with the main types of cladding options in New Zealand
So there you have it. The main types of cladding materials you'll come across in New Zealand and how each appears and performs in different ways. Having covered the bases, you're in a great position to dig deeper into those that make your shortlist in your journey to find the perfect cladding solution for your home.
(This article was updated on 26th February 2024)
Discover an extensive range of high-quality cladding solutions on ArchiPro
Top banner image credit: European Larch Cladding from Rosenfeld Kidson & Co.